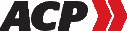
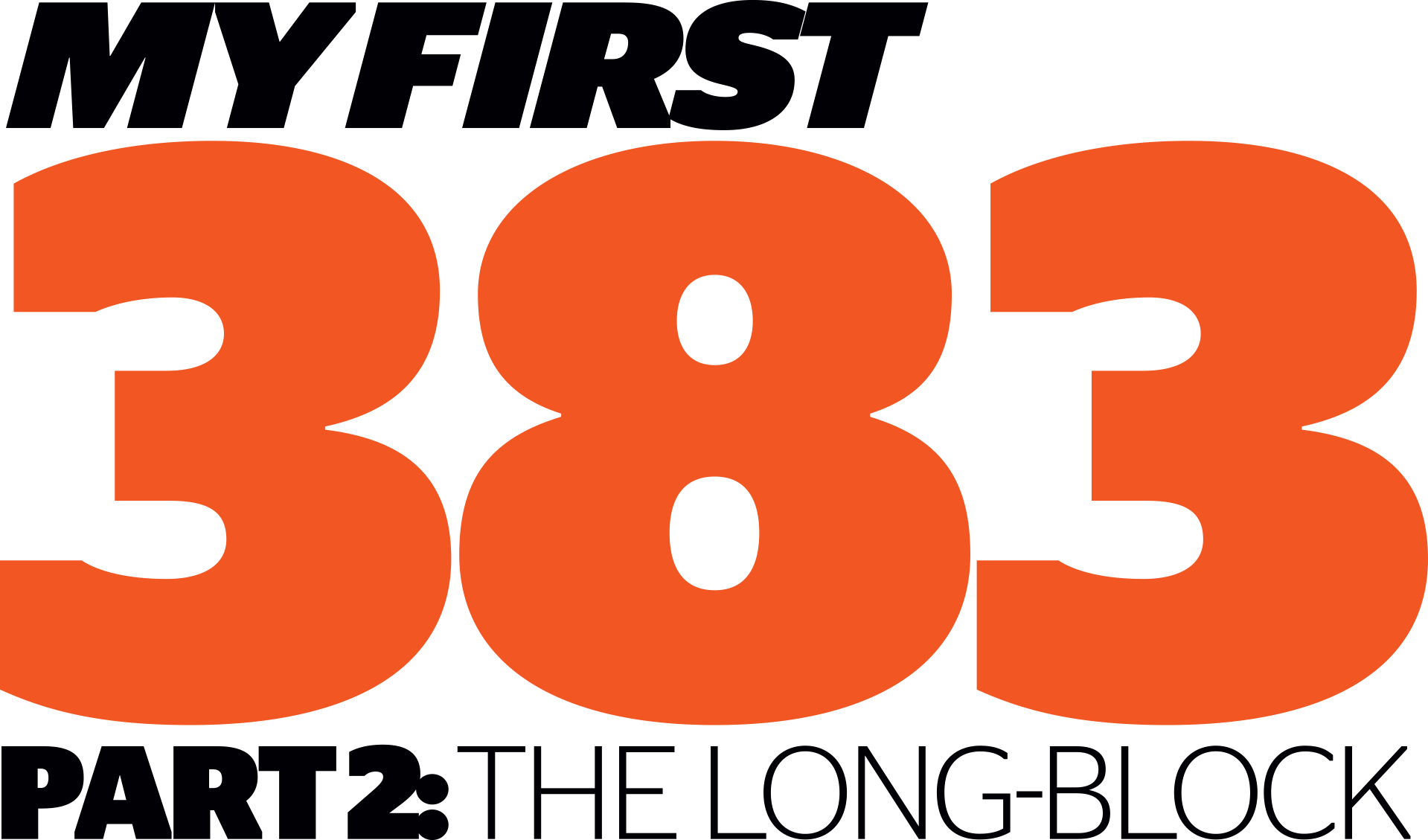

here’s nothing like building an engine yourself. If it works and works well, the feeling of accomplishment is huge. If it doesn’t work out so well, you’ve probably got no one but yourself to blame. As they say, failure is the greatest teacher, but if we’re honest it’s not a class we’d prefer to take. If you embark on a similar build as us, you’ll be well aware that this isn’t exactly a $1,000 budget build. So, learning a lesson the hard way might be more than you can afford—it’s certainly the case for us.
To hopefully avoid that form of education, we’re going to suggest reading this article instead. We’ll admit that this is no replacement for a factory service manual or the application-specific instruction sheets you get from each manufacturer. Hopefully, though, this tech story can at least serve as a road map describing one way to assemble a 383ci Chevy using off-the-shelf parts.
In part one of this build, we covered the process of having a block machined to handle a stroked rotating assembly. Then we installed said rotating assembly, piece by piece. In contrast, this half of the build is less heavy on the specialty tools and more about bolting on a combination of parts that will not only look good but perform well, too.
Our goal for this build is a simple small-block that has a classic—but not totally stock—look, makes good power, and actually sounds the part. We’d also like to drop it into our ’69 Nova without having to whip up an entirely new recipe when it comes to fitment, fuel delivery, and wiring. Maybe we’ll go EFI in the future, maybe we’ll put a hotter roller cam in it, or more hard-core cylinder heads, but for now we just want a solid all-rounder that we can swap in and have some fun with.
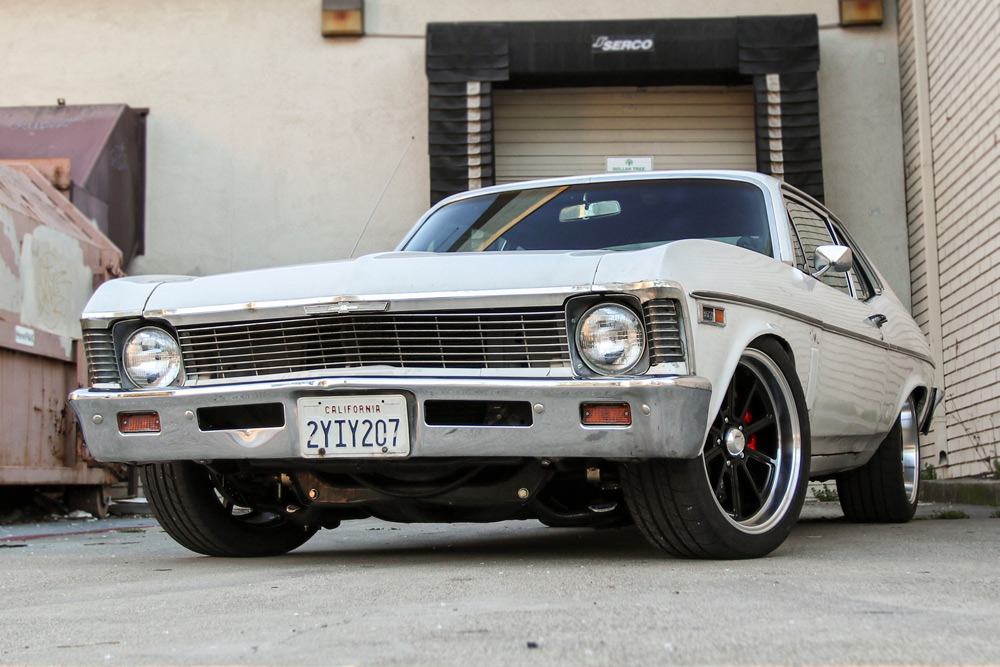
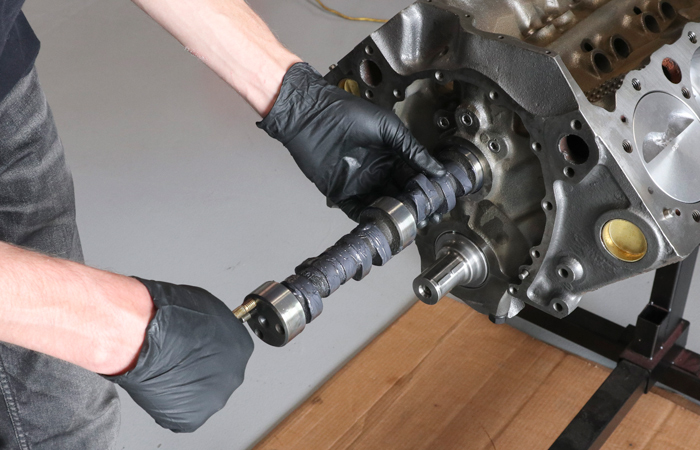
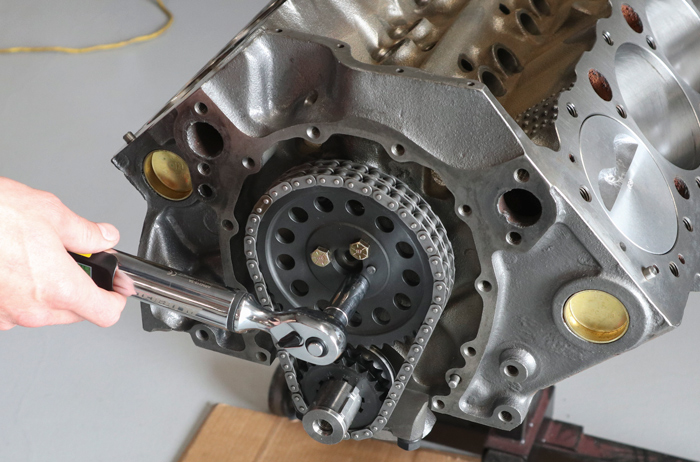
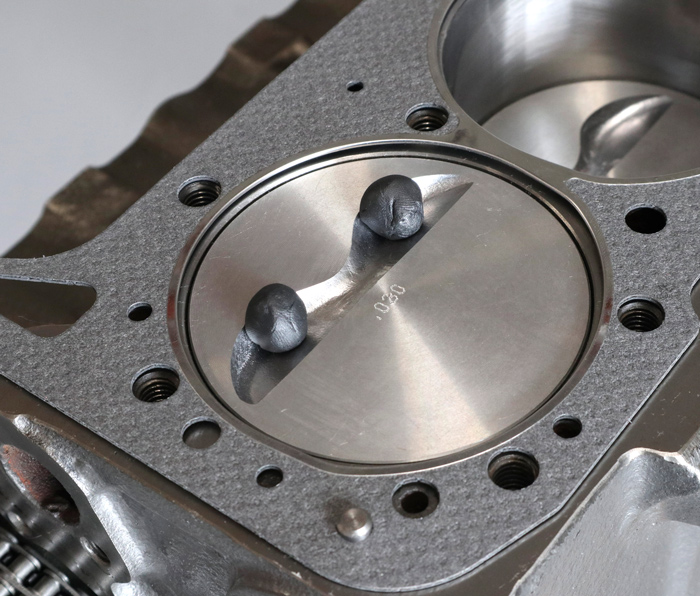
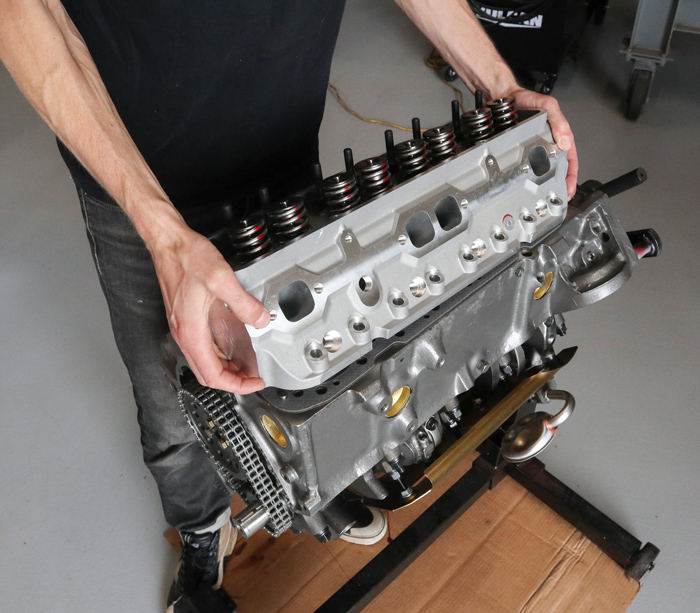
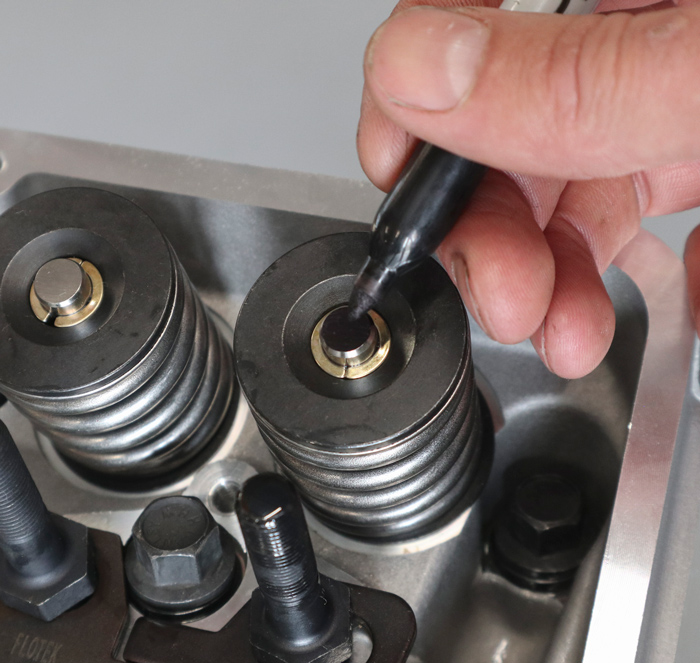
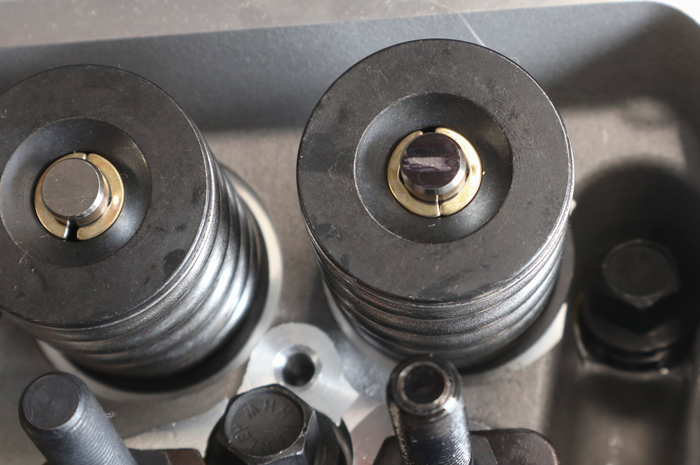
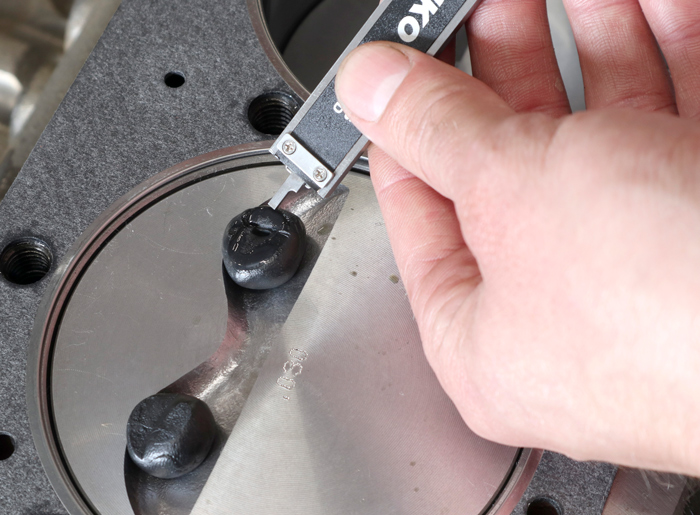
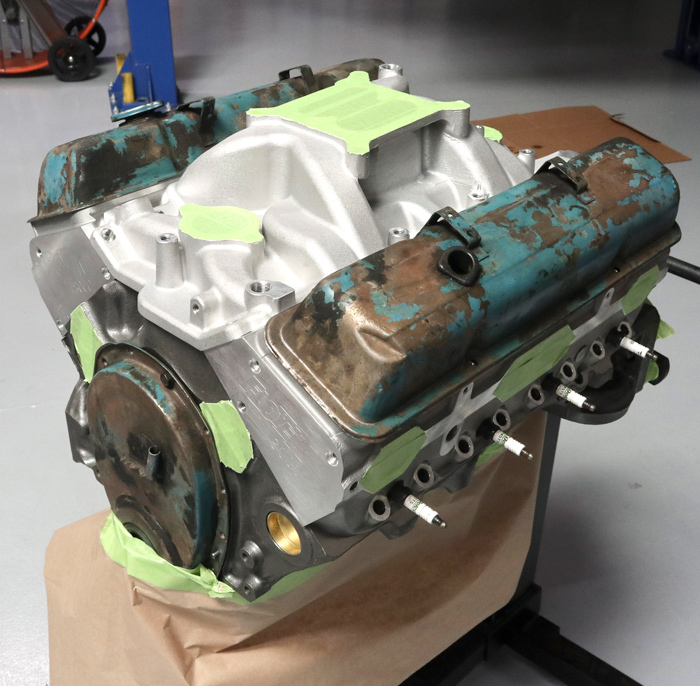
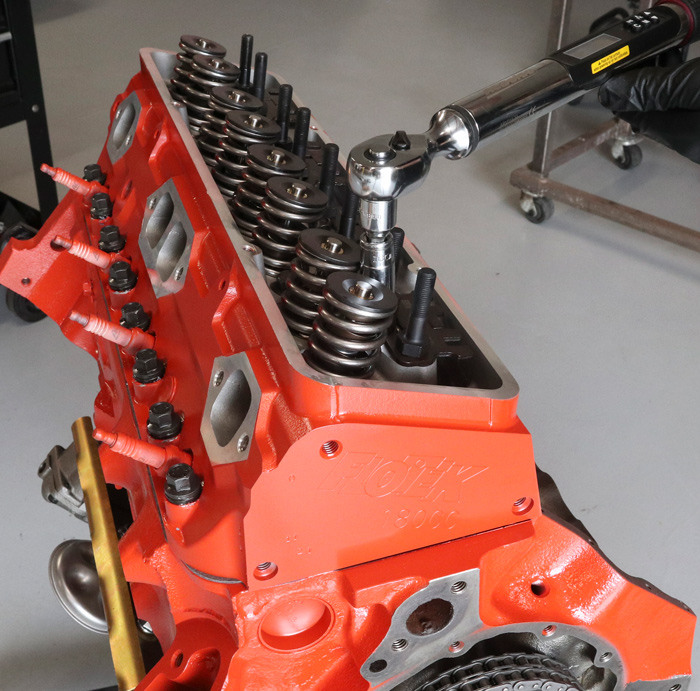
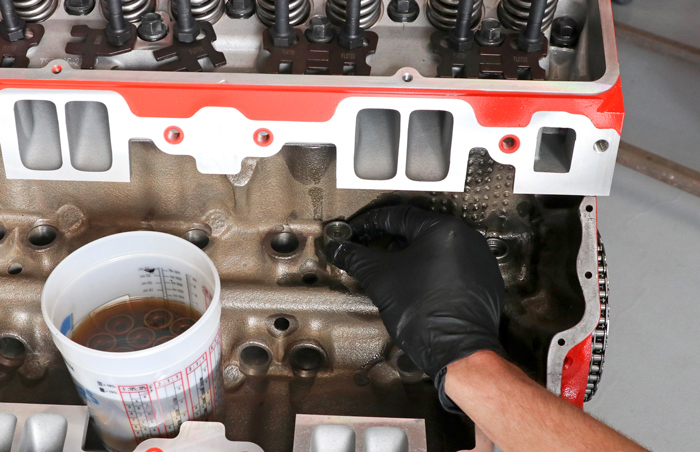
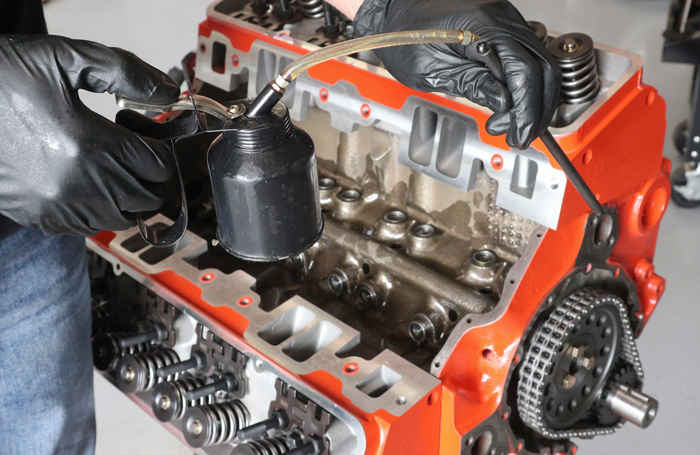
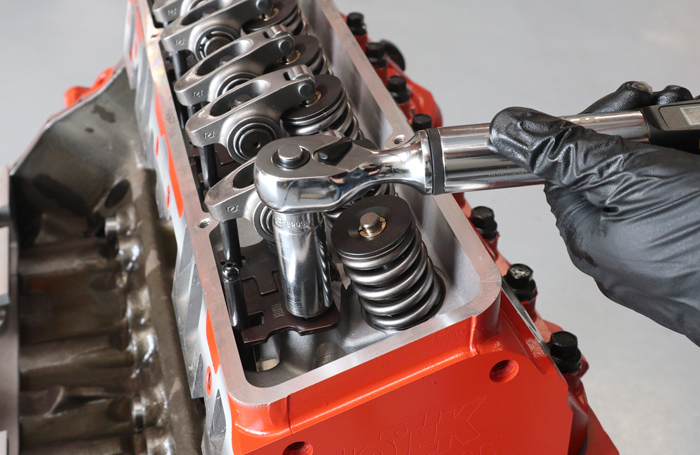
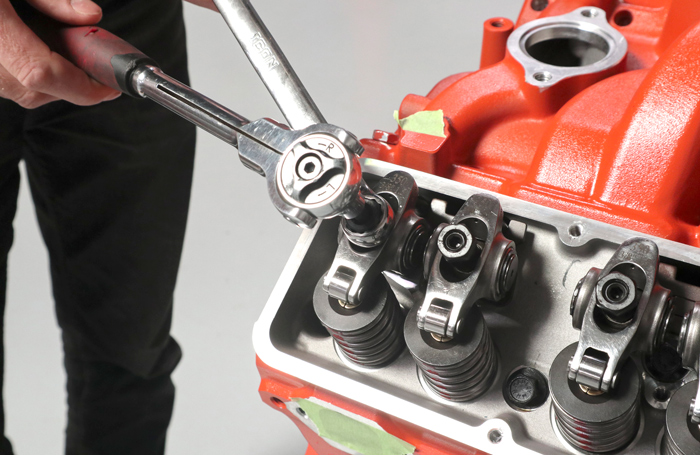
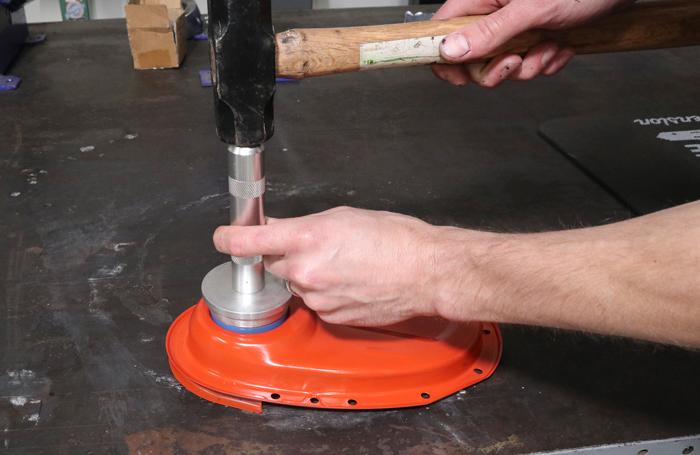
15. Next we used a seal installer (a large, properly sized socket can also do the job) to tap in the timing cover seal before bolting the cover to our block.
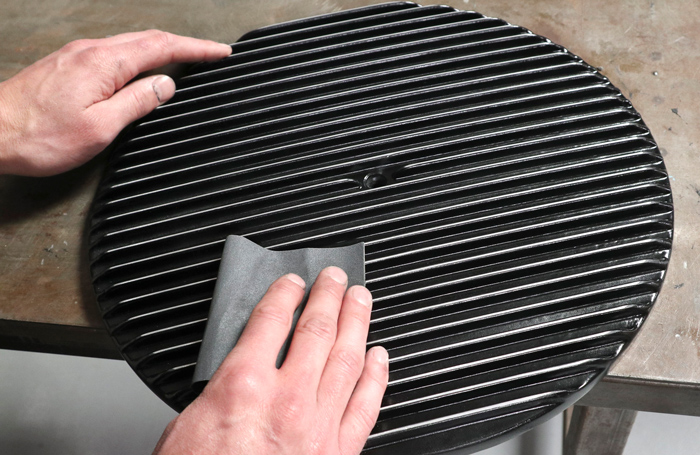
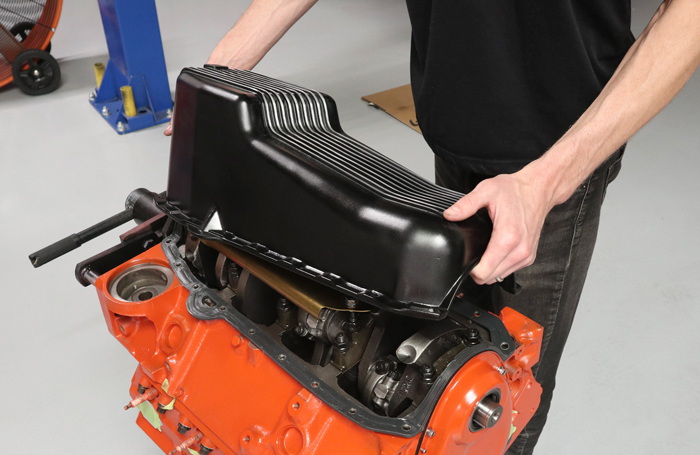
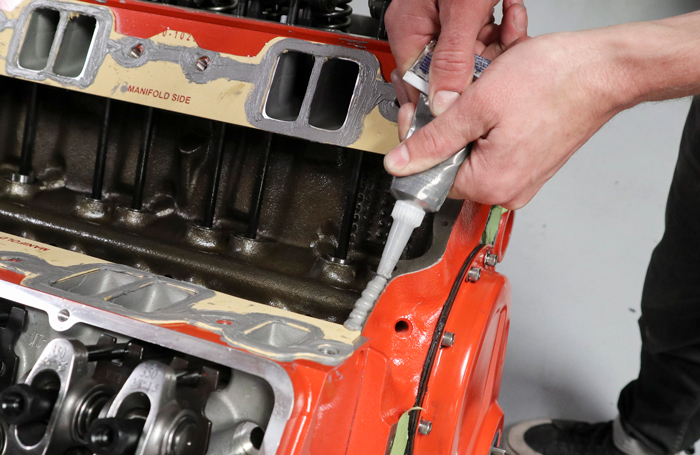
18. Next up, we flipped the engine back over and moved our attention to the intake manifold. The top-end kit comes with an oversized gasket that needs to be trimmed to match the ports of your intake manifold and cylinder heads. Once we tidied up the gasket, we gave each port a thin coat of gray RTV on each side followed by a thick bead along the front and rear edge of the lifter valley.
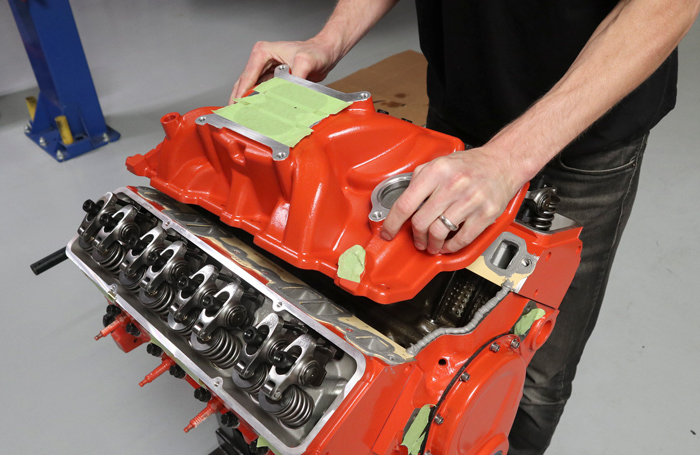
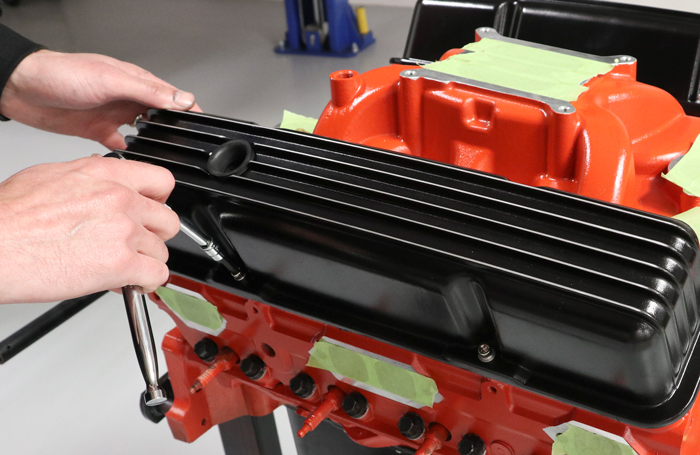
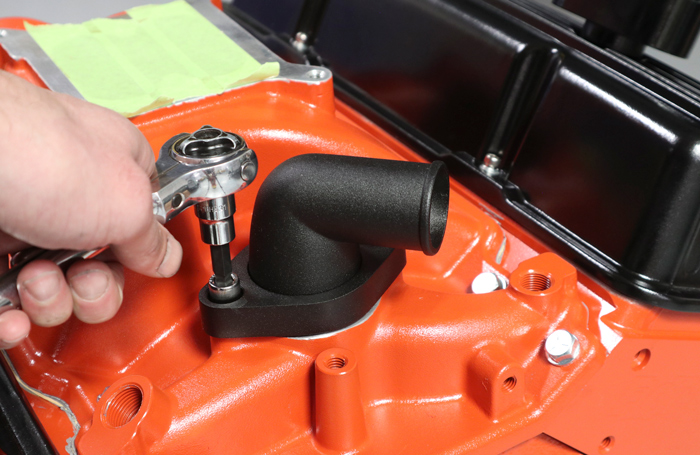
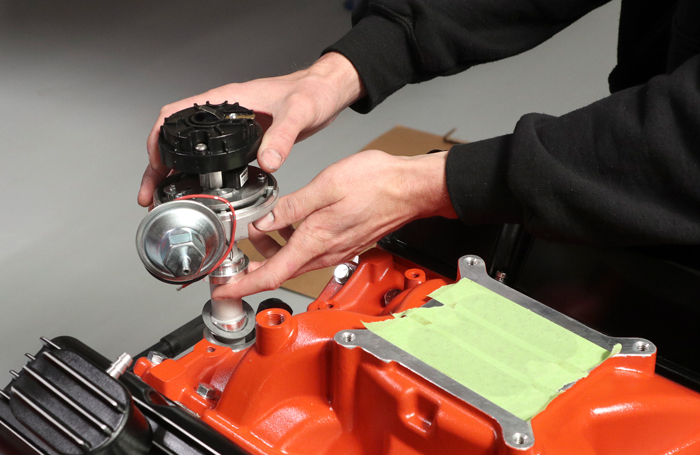
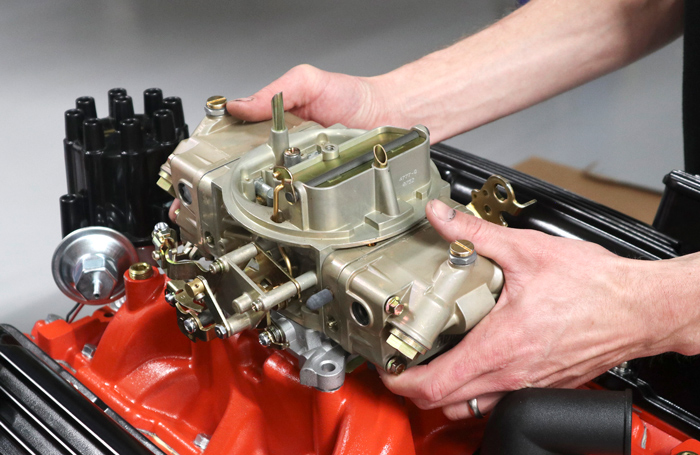
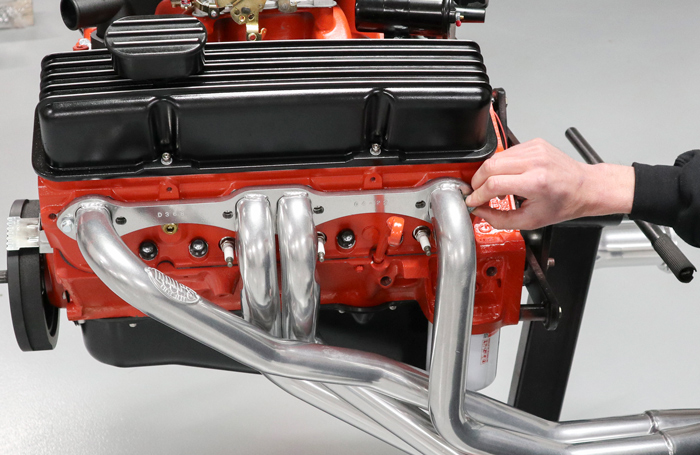
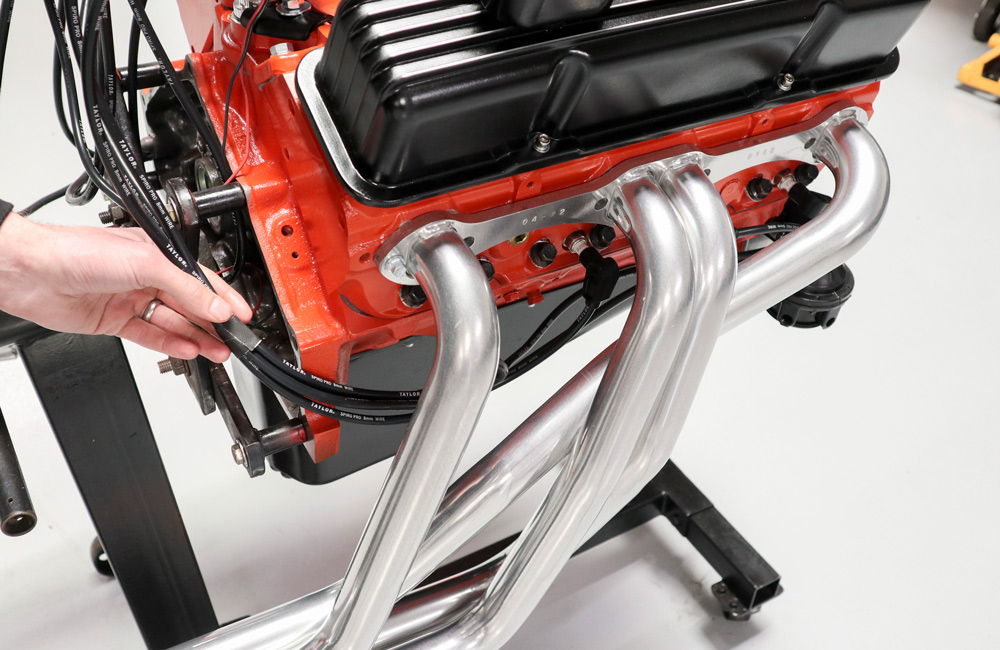
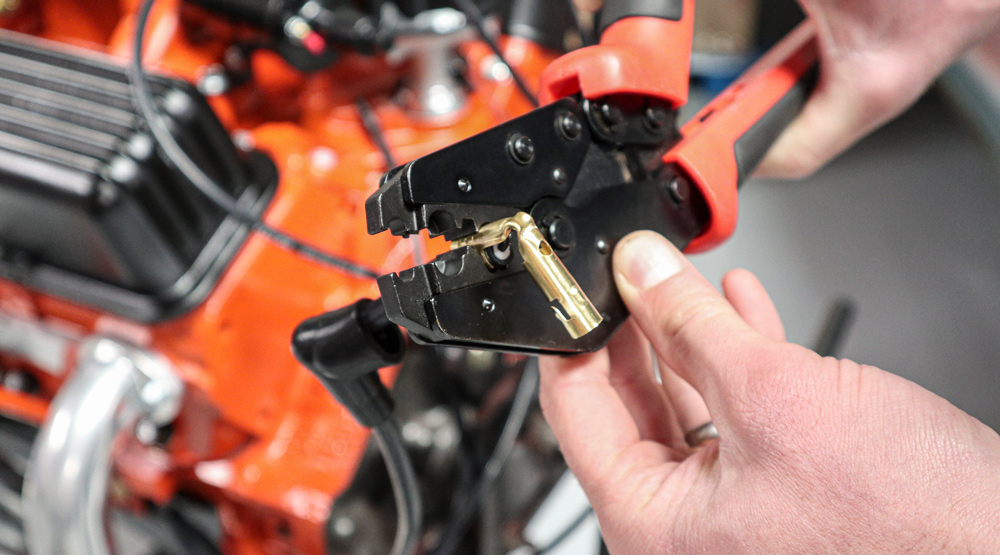
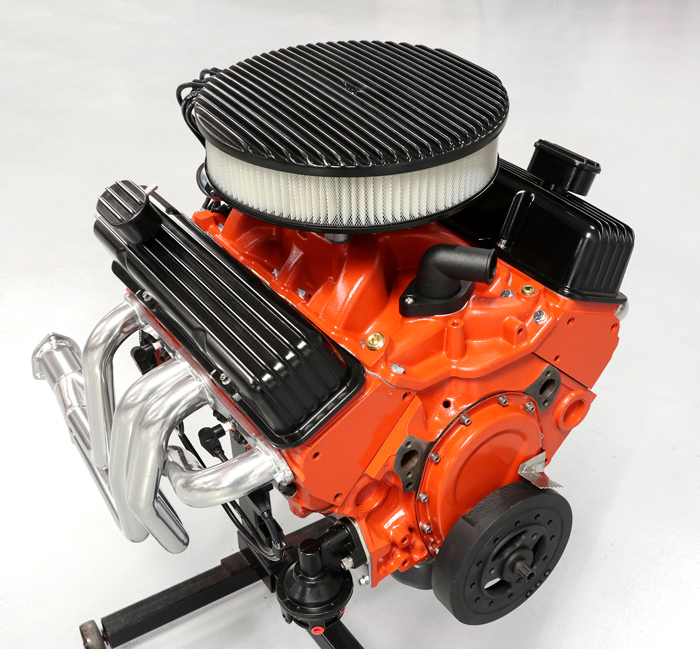
