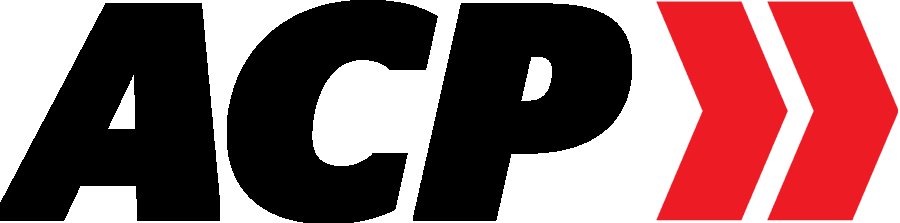
InTheGarageMedia.com


n America bigger is always better. A single cheeseburger is never as good as a double for lunch and most hot rodders believe the same goes for nitrous systems, carburetors, camshafts, and clutches …
But not always.
It’s a continuing battle. Street car horsepower and torque values have escalated in the last decade and now even domestic V-8 production cars are pumping out more than 700 hp and the latest Hellcat promises 1,000 hp from a production vehicle! This just exacerbates the boulevard horsepower boom and now everyone will assume they need four-digit horsepower. The truth is not everyone wants, needs, or can properly manage that much power. For every one guy who has the scratch to build a 1,000hp street car, there are hundreds of applications for the rest of the world in the 500- to 700hp range searching for a clutch.
Let’s take the stance that you have the chassis, brakes, suspension, drivetrain, and, yes, even the driving skill to handle all this power. This still demands a clutch system that can hold all that power. We’ll take a look at some of the variables that directly affect the decision around the kind of clutch and pressure plate you choose along with some areas to consider when facing the choice of moving to a twin-disc clutch assembly.
Before we dive too deeply into clutch details, it’s worth the time to outline how a dual-disc clutch operates. All dual-disc systems use what is called a floater plate, which is really just an additional friction surface in between the two clutch discs. As its name implies, this floater plate is released along with the discs when the clutch pedal is depressed. There are two basic methods of attaching the floater to the flywheel with either vertical stands or drive straps.
Because this friction surface must float when released, vertical stands can allow the plate to rattle as the plate responds to variations in engine speed. This is generally most noticeable at idle or low rpm. Many of the aftermarket companies now use a strap instead of stands that will eliminate this noise but other companies using stands have also essentially eliminated this annoying rattle through innovative design means. If you are concerned about this, ask your selected clutch company how they approach this issue.
There are multiple variables that affect how a clutch is able to grip and transmit the torque of an engine. In our previous “Clutch Basics” story we discussed clutch diameter (surface area) along with pressure plate clamp force, clutch material, and the operating temperature of the clutch material as variables that affect torque capacity.
The main reason for choosing a dual-disc clutch is to increase the surface area with four friction surfaces instead of just two on a single disc, which automatically improves the clutch’s ability to handle additional torque. Among the many variables that you will need to address is clutch disc diameter. This can range from 9 inches up to usually around 10.5 inches. Larger discs will offer more surface area but will also be heavier, which is a concern that we will address in a moment. Juggling disc diameter, clamp load, friction material, and cost are the major pieces of the puzzle you will need to address before making a decision.
At this point it’s important to first address how clutch systems are rated. To make things simple, most aftermarket clutch companies employ a horsepower rating. While this is simple and easy, horsepower is not the true factor. Instead, torque or the engine’s twisting motion is the actual input that affects a clutch’s holding ability. As engine torque increases, this will require a more aggressive clutch system to adequately transfer power to the transmission without slippage.
Generally, a clutch rated to withstand 500 hp likely can accommodate a similar torque rating. This is important in cases where a mild big-block might make 600 lb-ft of torque but only 500 hp because it doesn’t rev past 5,500 rpm. To emphasize this point, Chevrolet Performance’s 632ci 1,000hp big-block also makes 872 lb-ft of torque. That engine in a street car would most definitely demand a dual-disc clutch, especially in a heavy vehicle.
Conversely, a small-displacement 5.3L (325 ci) LS engine making 500 hp at 7,500 rpm may barely achieve a peak torque level of 400 lb-ft, and while it would not fit into the category of being “over-clutched” if fitted with a dual-disc clutch, this application might work well with a high-quality single-disc system. This is why clutch companies always ask for the displacement of the engine along with the car’s weight to help them recommend the correct clutch.
Regarding clutch diameter and therefore surface contact area, this is a fairly straightforward approach. The larger the diameter, the more surface area the clutch achieves, which improves its torque capacity. Clamp load is worthy of discussion because this directly affects pedal effort for street cars. The main reason that diaphragm pressure plates have become so popular for the street is because of the Bellville spring design. When the clutch pedal is depressed, at some point the fingers on the Bellville spring reach a center point. At that point, the effort required to hold the spring in place is reduced by virtue of its design. This takes far less effort to hold the clutch pedal in at a stoplight. The three-finger Long-style pressure plates are now more often used only in competition applications like drag racing.
The next factor in clutch design is the clutch facing material. We’ve included a chart that lists all the popular options. Organic facings are a blend of a several materials that are recognized as that dark, riveted facing on a clutch disc. These blends offer the advantage of a more gradual clutch engagement feel for street use. More aggressive materials like ceramic-metallic and sintered iron offer higher coefficients of friction that will hold more torque, but they also tend to be more aggressive during engagement, which can affect driveability on the street.
This is only one of several reasons why there are multiple variations on the dual-disc clutch approach. It would be near impossible for this story to list all the potential variations on this dual- versus single-disc theme but let’s start with a simple application. We have a 3,500-pound ’65 Chevelle with a professionally built, normally aspirated 420ci small-block that makes outstanding torque with 550 lb-ft of torque and 560 hp that shoves this power through a Richmond four-speed transmission and 3.55:1 rear gears. This car has seen hundreds of autocross passes along with a dozen hill climb runs, dragstrip passes, and other abuse that includes thousands of street miles.
This car also participated in the Optima Street Car Challenge several years ago. We submitted this application to a couple of clutch companies and the response was split, one company said it would be best served with a dual-disc system while another recommended a strong, single disc. The car has survived many years with a simple, Dual Friction single-disc clutch from Centerforce that is almost 15 years old. When we recently disassembled the car for maintenance, the clutch appeared used as you would expect but hardly abused and still capable of many more track days.
One part of this single disc’s success is that we thoroughly broke in the friction material and never abused the clutch, despite the fact that it was used almost exclusively in competition with thousands of careful up and down shifts. The point here is that advancements in friction material and clutch design now offer serious torque capacity from a single-disc clutch if the unit is treated properly.
Part of the choice for applications for a single- versus a dual-clutch assembly also has to do with rpm. Larger engines like big-block Chevys that can produce huge torque are great candidates for a dual-clutch assembly because of their capacity for big toque numbers at relatively low engine speeds. Conversely, a small-block with less displacement making high horsepower at much higher engine speeds presents a challenge for dual-disc clutches because of the higher rpm.
The most important factor around this point for dual-disc clutches is that the transmission must contend with the force created by a pair of clutch discs instead of just one. Modern dual-disc systems attempt to reduce disc mass to address this situation. For example, the Centerforce DYAD system uses one disc with a center hub with six springs but reduces the critical outer diameter mass with a paddle wheel configuration. By reducing the mass at the outer edge of the clutch disc, this reduces the inertia force created by the disc. The second disc also eliminates most of the center portion of the disc using a solid flange to mount the friction material.
Combined, these two discs reduce the inertial force created by a pair of fullsize plates at higher engine speeds. This is important because when the clutch is released during a shift, the force created by two discs can be greater than a single disc. The transmission’s synchronizers must contend with this greater force in order to match the gears for either an up- or downshift.
This does not mean that large-diameter, twin-clutch assemblies are bad. A twin-disc setup for a high-torque engine that will rarely see the high side of 6,000 rpm would work very well and not damage the transmission. This moves this discussion into the type of transmission used which is beyond the scope of this story. But it’s worth noting that modern manual transmissions offer synchronizers with far stronger capacity than the older, brass-style units used in ’60s and ’70s transmissions. Adding a second disc does make the synchronizer’s job more difficult but smaller diameter and lighter discs drastically reduce the total force generated at high rpm, but keep in mind that this force is doubled with the second disc.
Because there are so many variables between power, applications, and the vast number of clutch options between each of the many clutch companies makes the total number of choices vast. So, we’d suggest talking to several clutch companies to get their recommendation on your specific application. Armed with the information in this story, you can skip over many of the newbie questions and hone in on the best clutch that will make that connection between all that flywheel horsepower and putting the torque to those black spinney things out back.
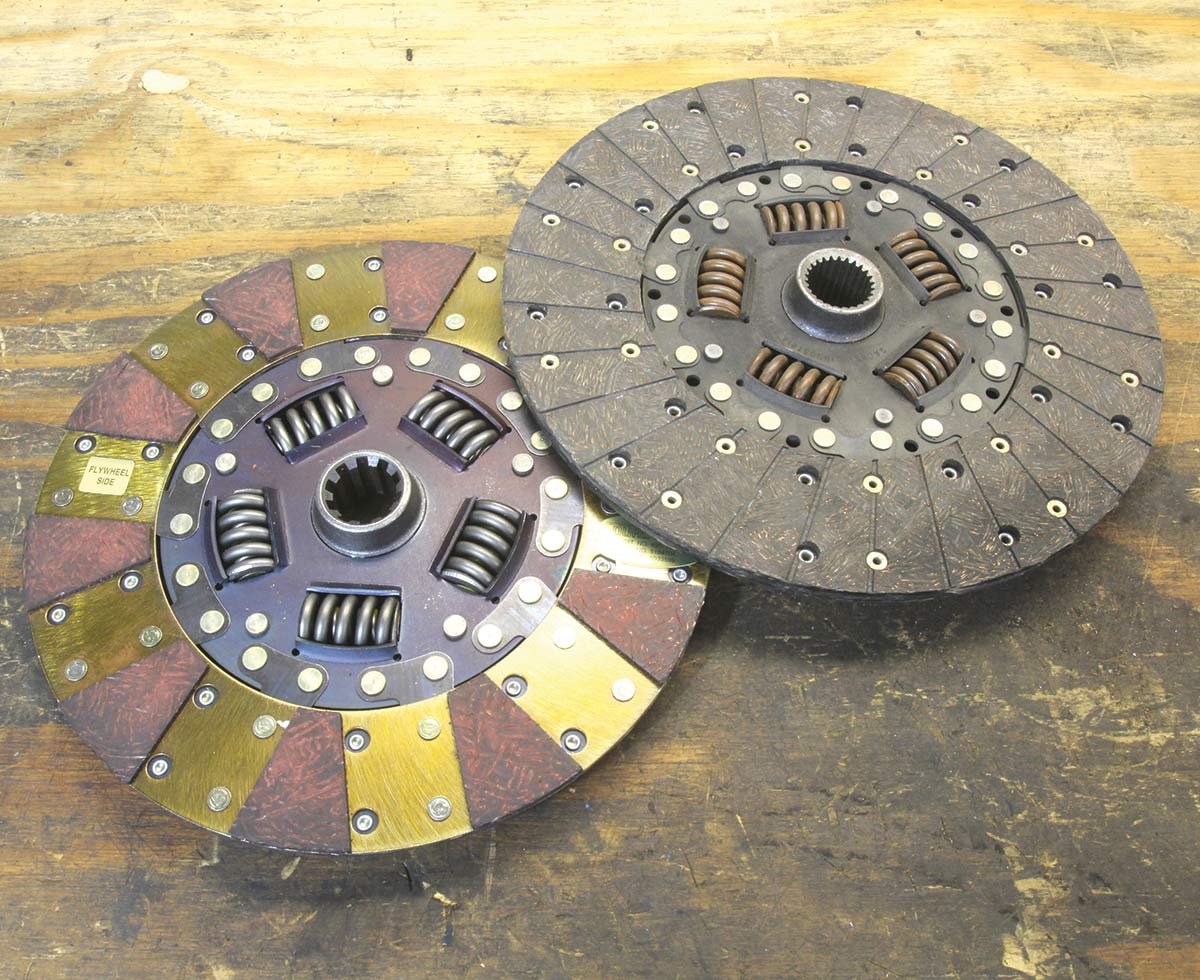
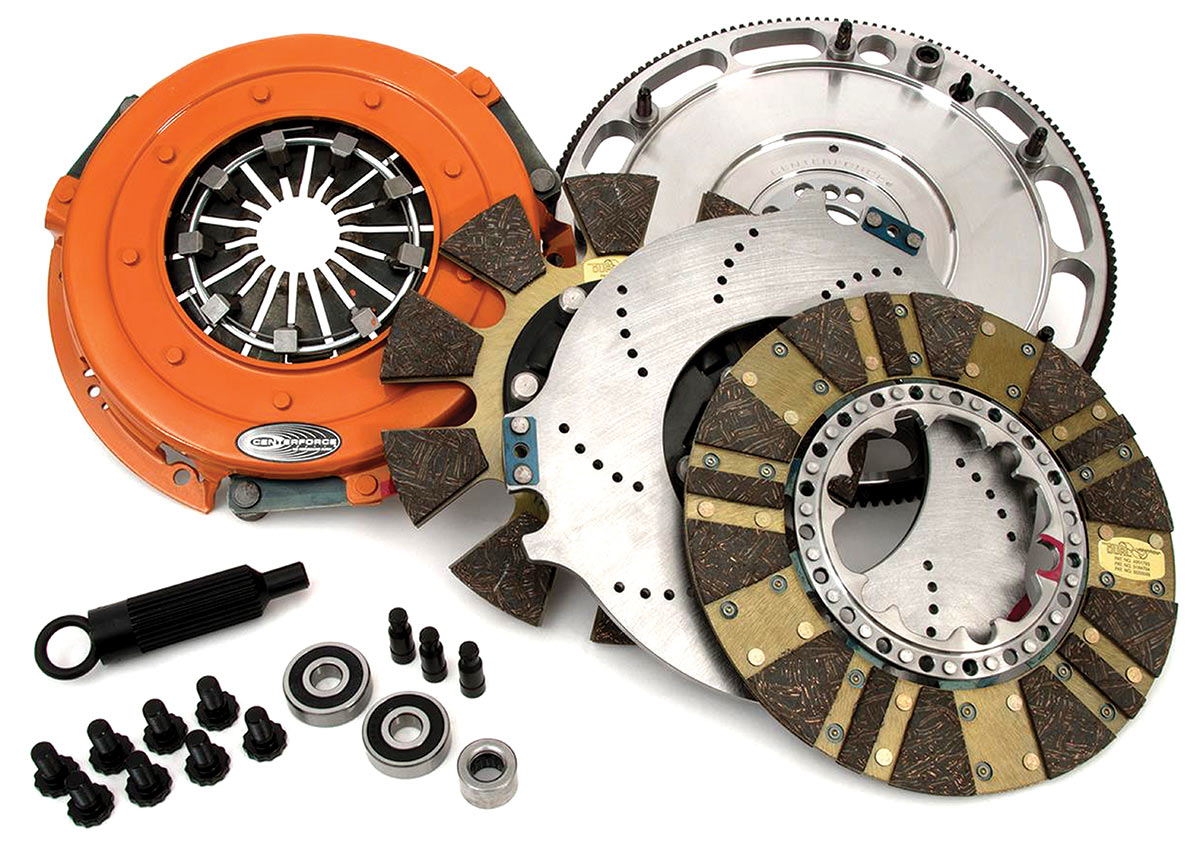
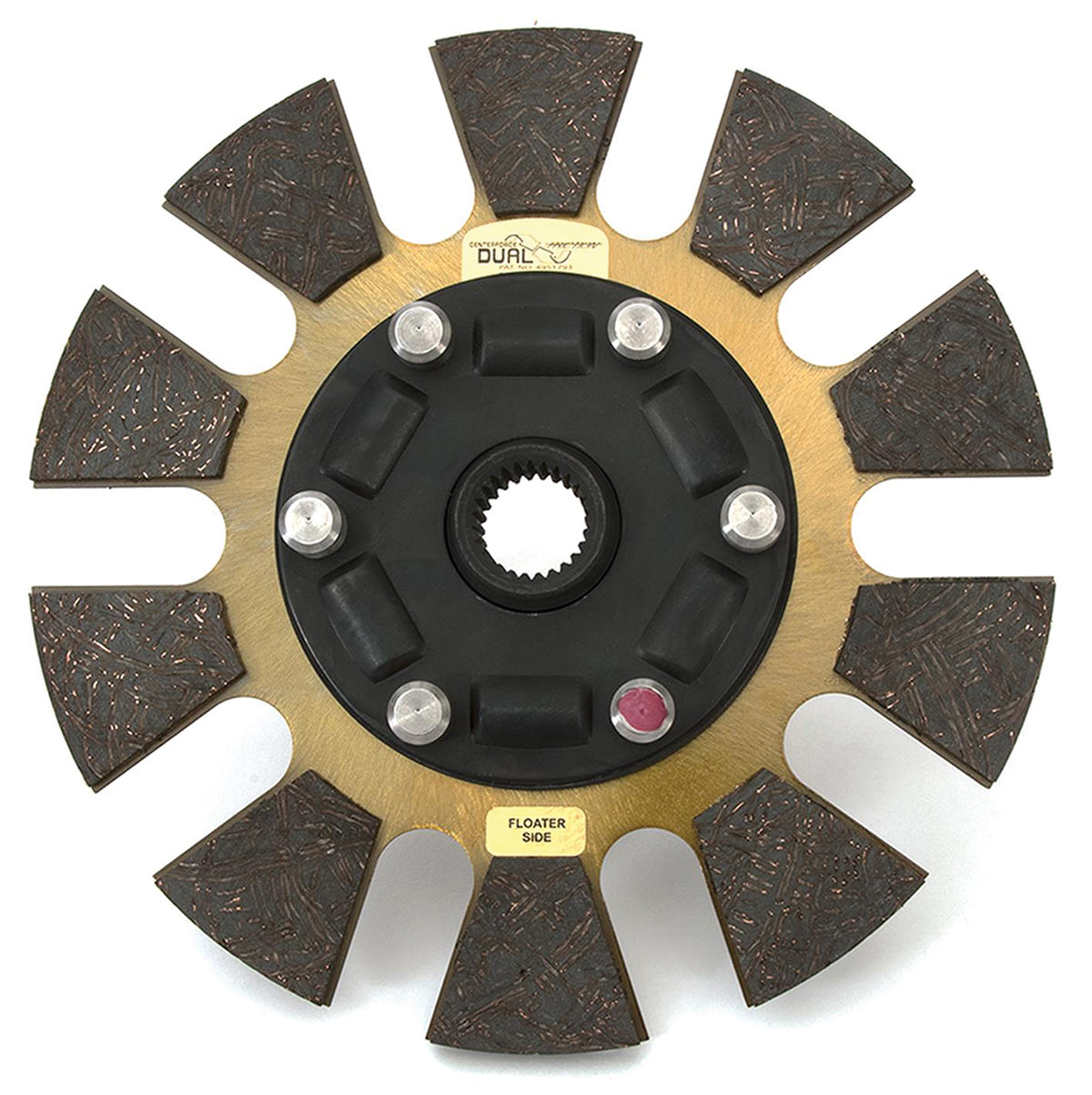
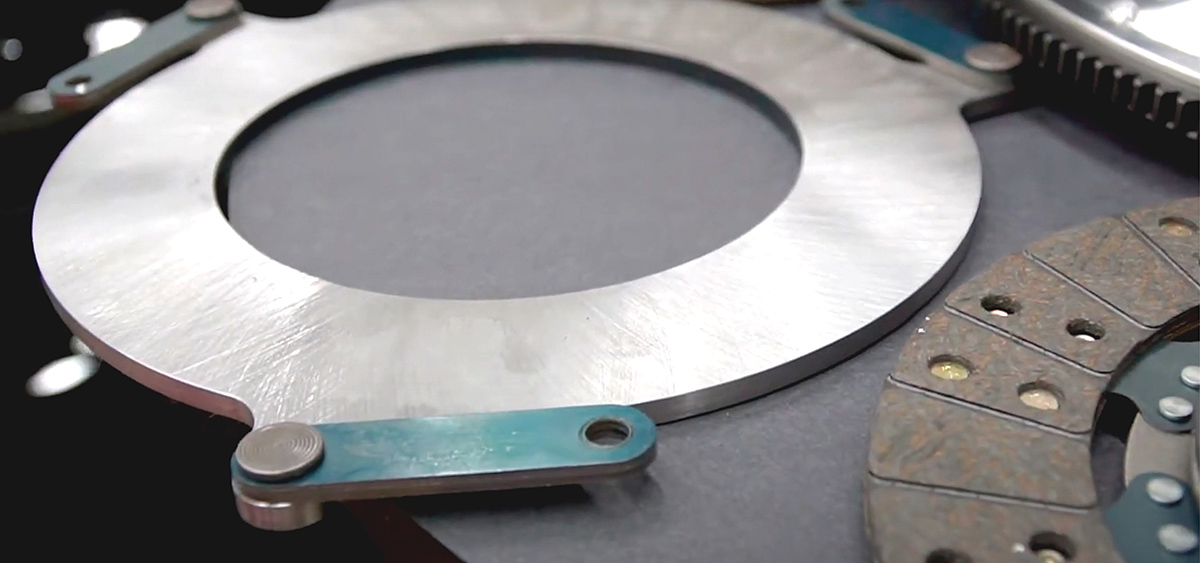
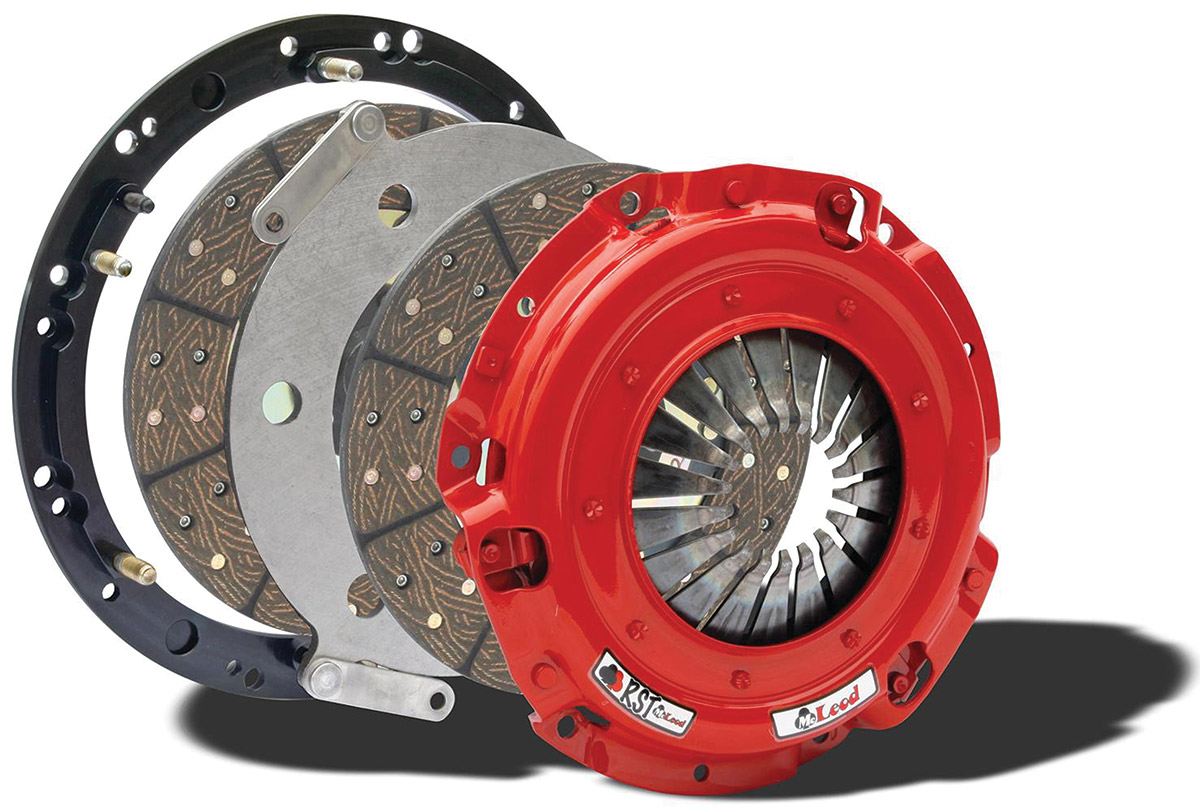
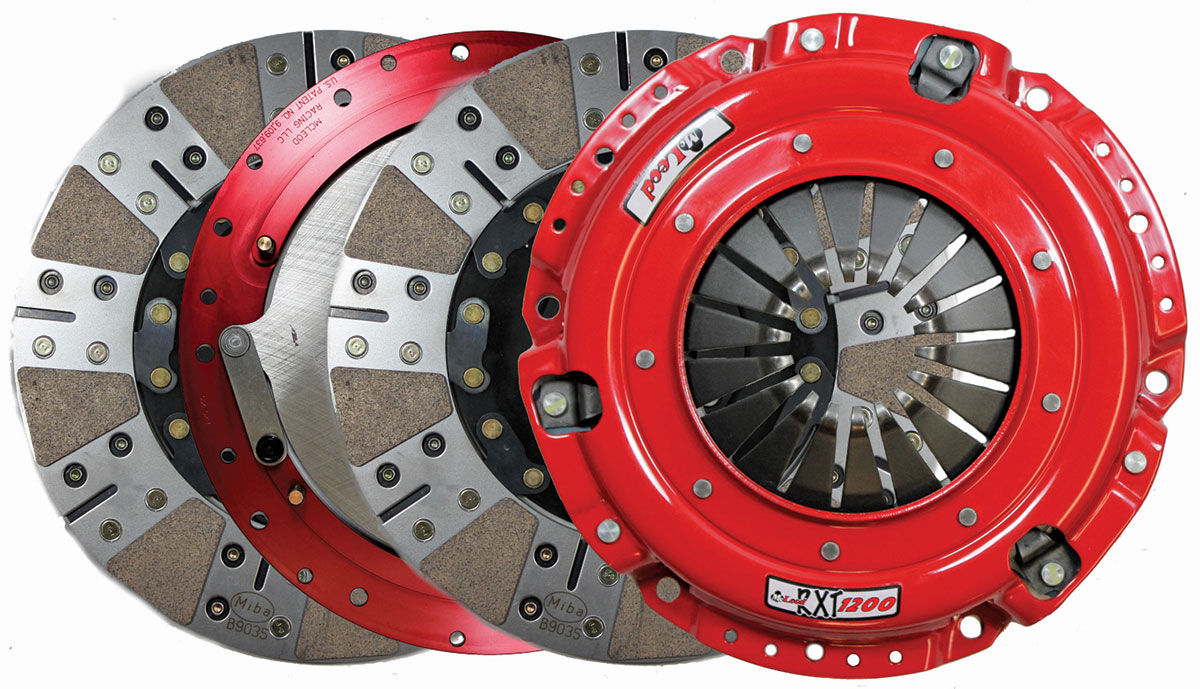
6. McLeod’s high-end system is the RTX 1200 with the number pointing directly at its torque capacity. This twin-disc setup is aimed at the big-end horsepower beasts who still drive on the street. Both discs feature ceramic linings yet still delivers a slightly higher-than-stock pedal effort. Within the McLeod lineup there are literally a dozen or more options from mild to wild for the twin-disc crowd.
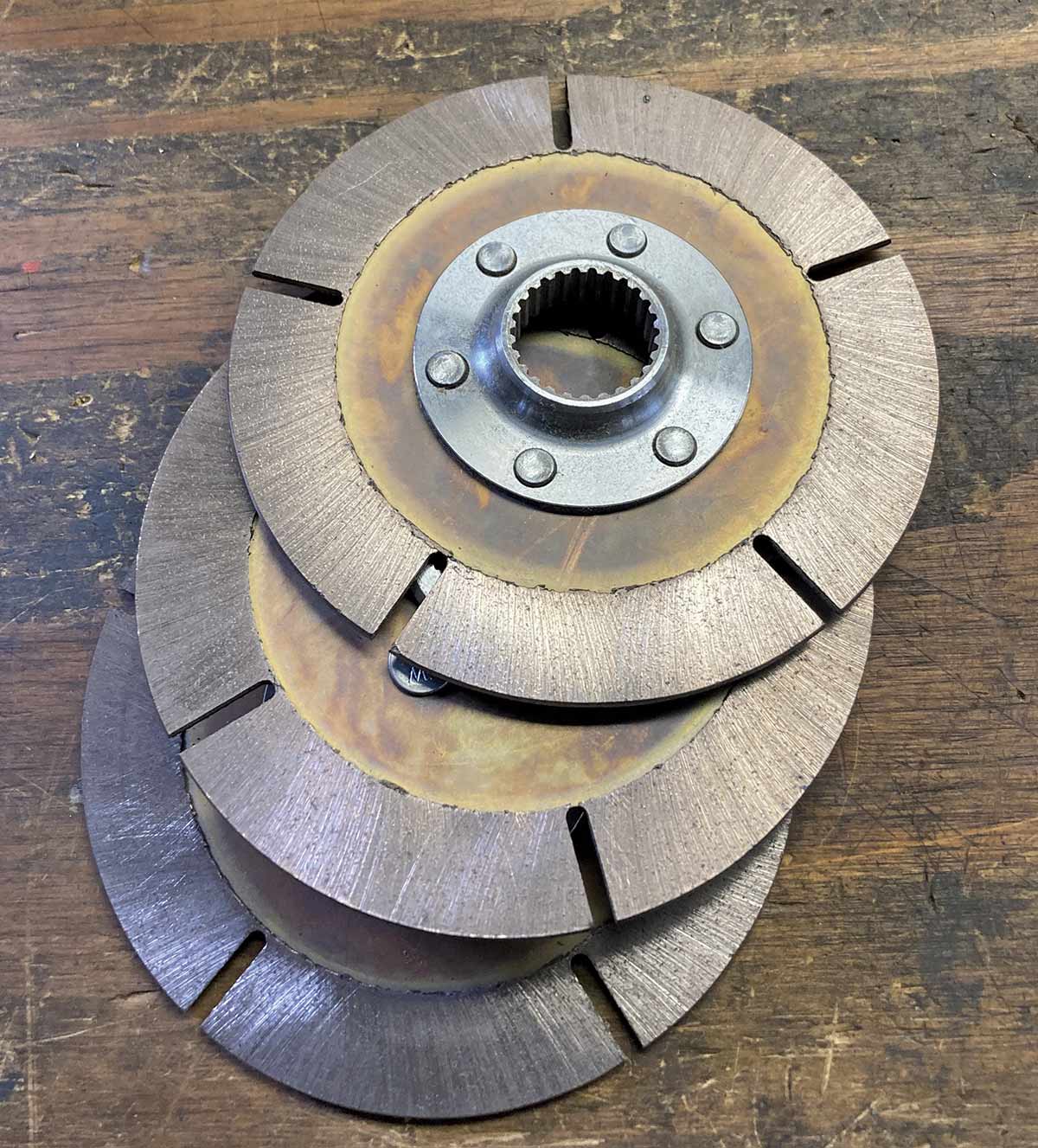
7. Full circle track racing clutches often use three or four small-diameter multi-discs clutches to reduce the rotating mass for better acceleration off the corners. These are 5.5-inch discs from Quartermaster just to illustrate their small size. This would be a horrible clutch for the street.
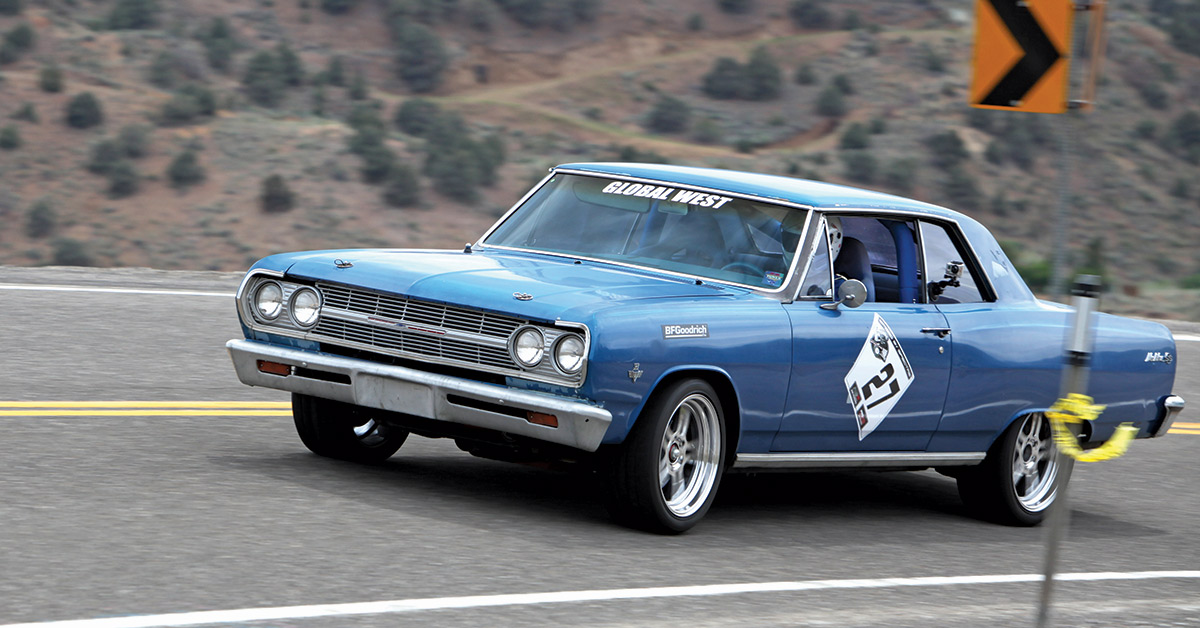
8. This is the Chevelle mentioned in the story halfway up the Silver State Hill Climb race up Highway 341 leading up to Virginia City, Nevada, several years ago.
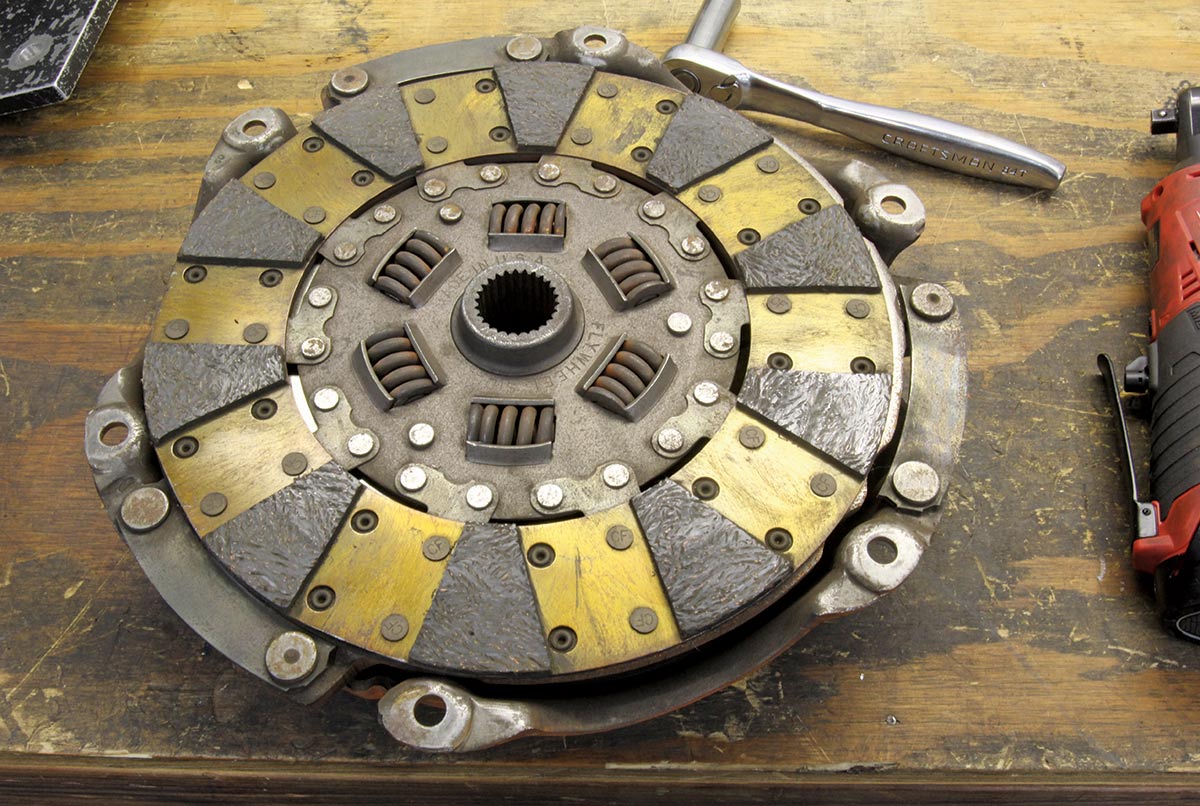
9. This is the single-disc Centerforce Dual Friction clutch disc that we removed from our 3,500-pound autocross and road race Chevelle after hundreds of competition passes. It still has plenty of life left in it despite the hours of competition abuse.
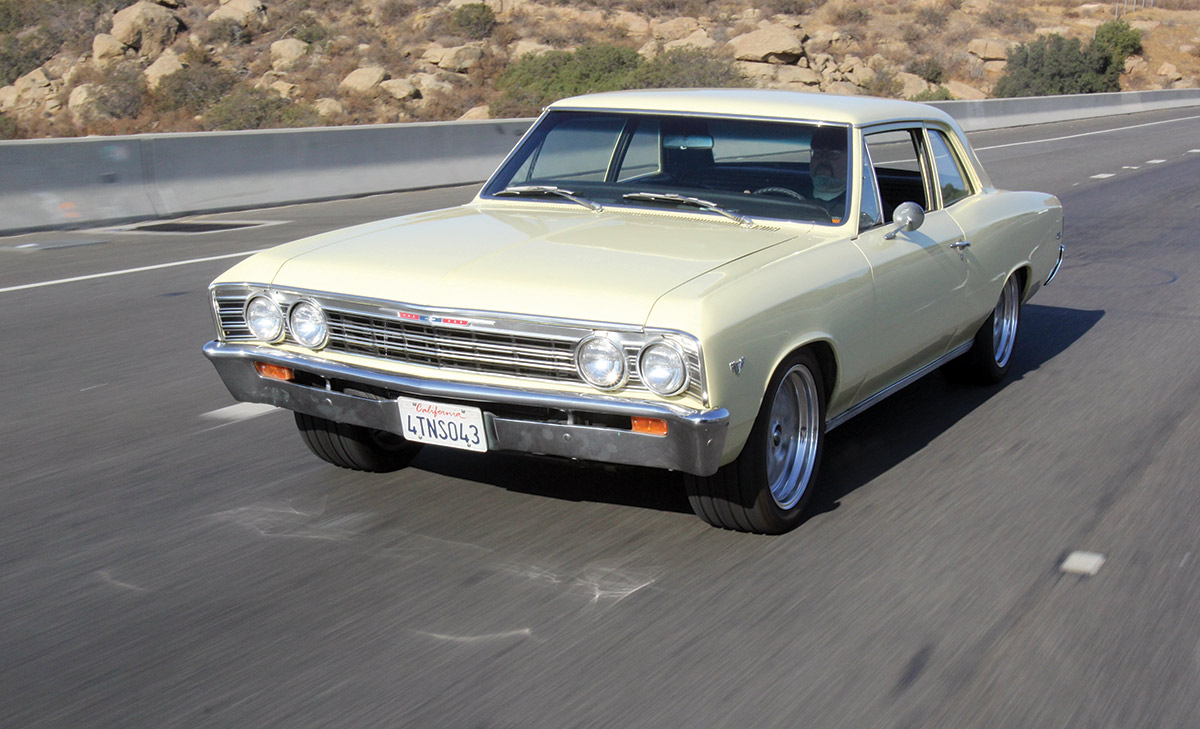
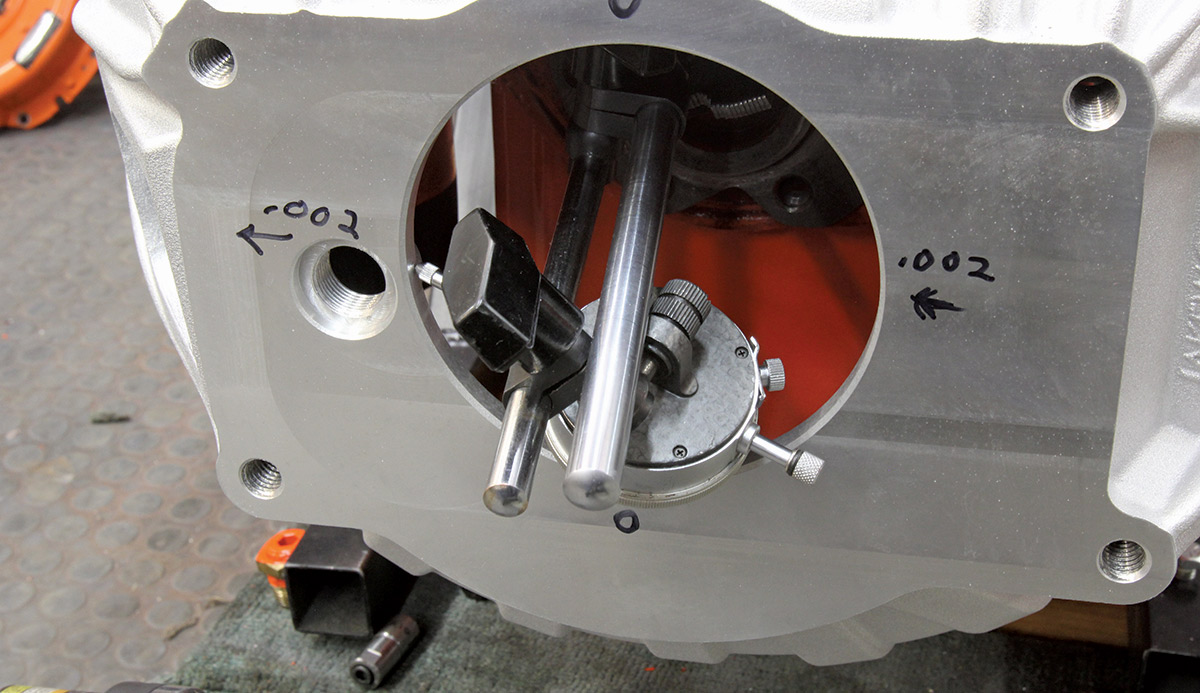
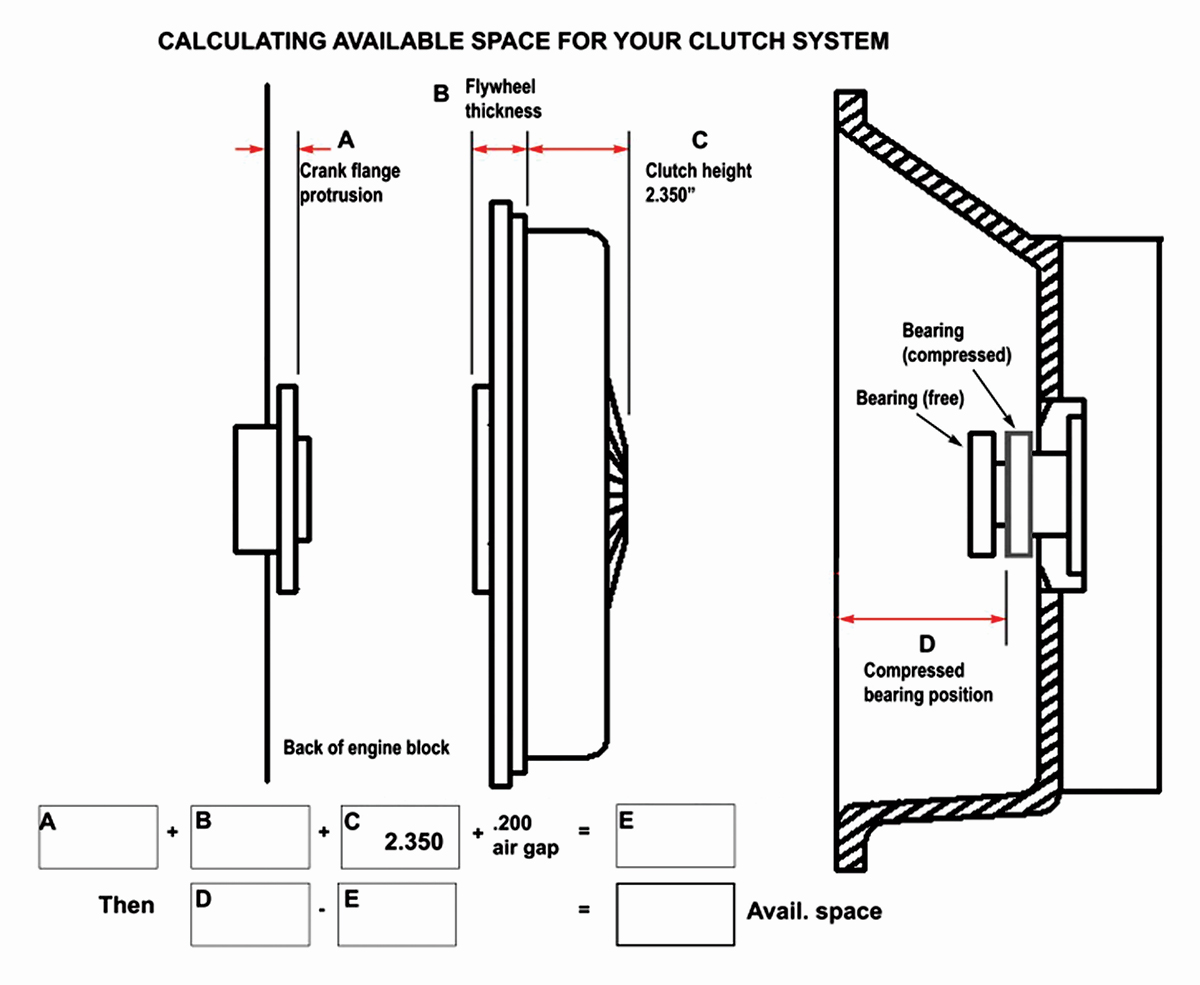
12. One important need-to-know detail is the overall depth of the dual-clutch pressure plate assembly. Adding another disc and floater will increase the overall height of the clutch assembly. A few simple measurements will determine if your existing bellhousing will accommodate the slight increase in height. This chart can be found on ramclutches.com.
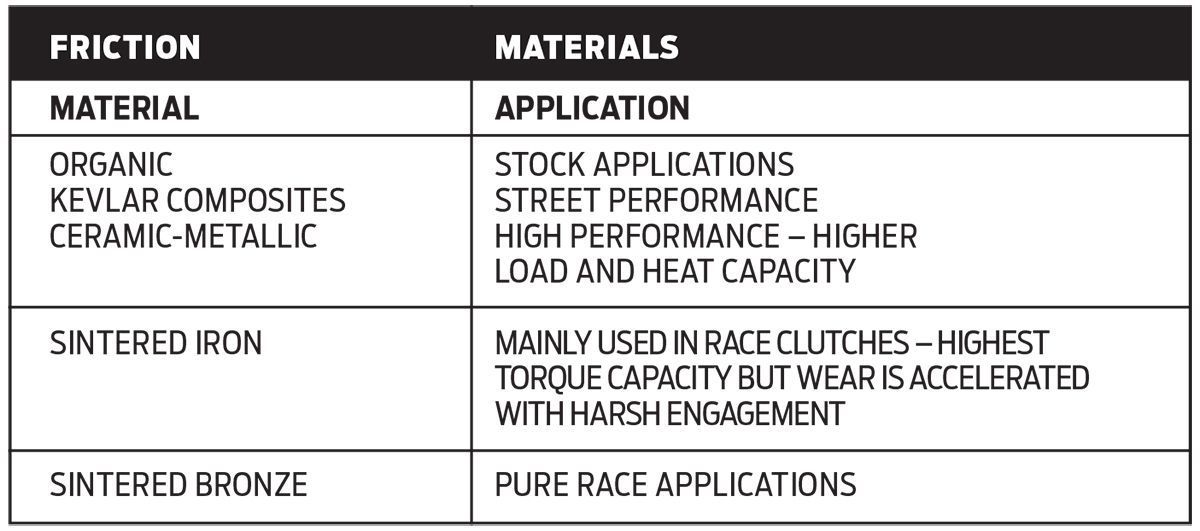
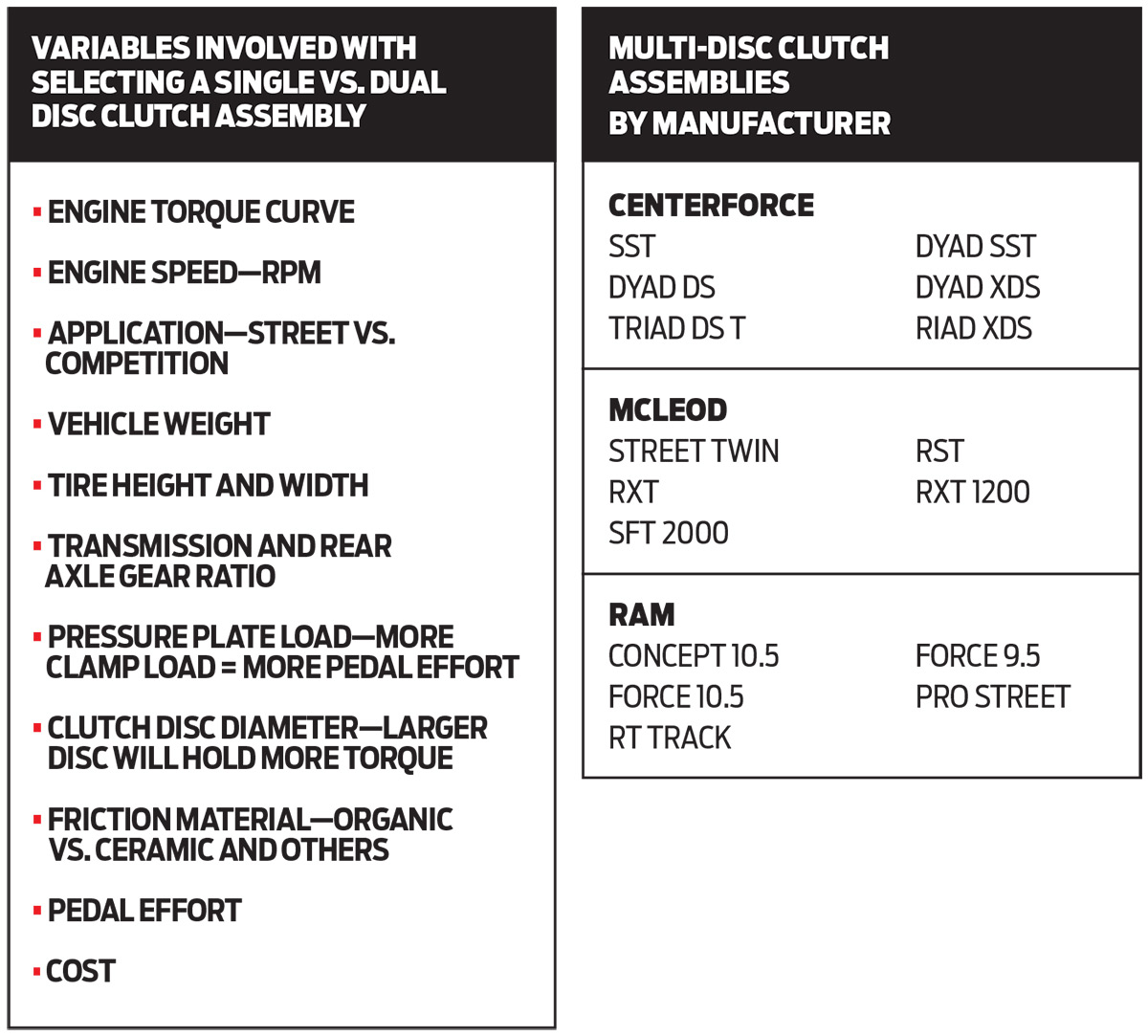
