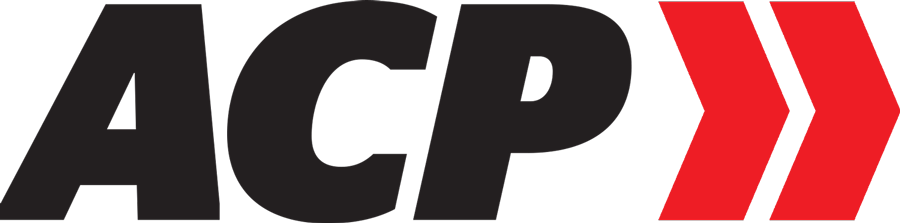
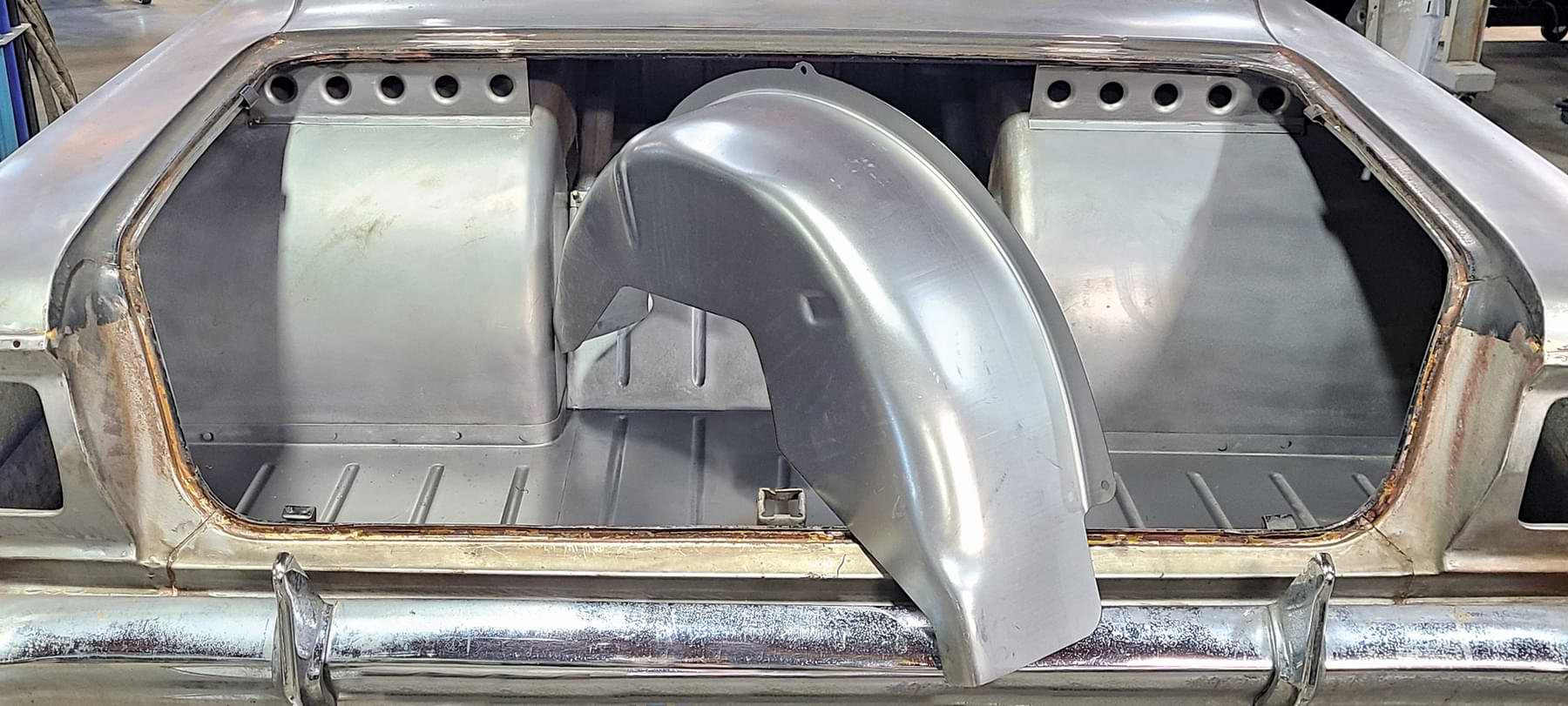

e’ve all seen the cars at the local cruise spots making a statement with the blowers sticking through the hoods and rear tires as wide as they are tall stuffed between the quarter-panels. But, if you think that look is overkill, there is another way to get performance from your ride without going overboard.
If you need up to a 12-inch tire out back but your ’69 Camaro still has its factory wheelwells for those extra-skinny ’60s-era tires, you’re in luck because installing a pair of mini-tubs will solve your problem. Detroit Speed manufactures several styles of mini-tubs for those owners who want to retain a near-stock appearance but add a little more tire out back.
Made in the USA using 18-gauge steel, the kit Detroit Speed offers includes two stamped tubs that are 2.75 inches wider than stock, look like the factory wheeltubs, come with a set of steel fill plates, a set of paper templates to help lay out the cut lines, and a 23-page(!) instruction booklet to explain how to do the work (they also have an installation video on their website).
This installation of Detroit Speed’s tubs (PN 040401DS) is expressly made for ’67-69 Camaros and Firebirds (there are extra instructions included for convertibles and certain text that’s unique to the ’67 models), and this particular subject car is a well-preserved ’69 that has been with one family for decades before becoming the subject of a Roadster Shop frame-swap and build that will happen over the course of three days during the 2024 Grand National Roadster Show in Pomona, California.
Performing that work will be a team from Orange County Hot Rods (Corona, California), which are the same folks who pre-prepped the body with these tubs to make the three-day swap schedule a little bit easier. Because the new tubs are wider than stock, you will also need to narrow the rear seat base and seatback, which is not covered in this story (this vehicle will get custom seating instead) but it is discussed in Detroit Speed’s instruction booklet.
Since the body will sit on a new Roadster Shop chassis with integrated upper shock mounts, relocating the original stock mounts is not shown here, but it’s in the Detroit Speed booklet. It always seems every builder does the same job a little different from the next shop, so follow along to see how Orange County Hot Rods completed this installation.

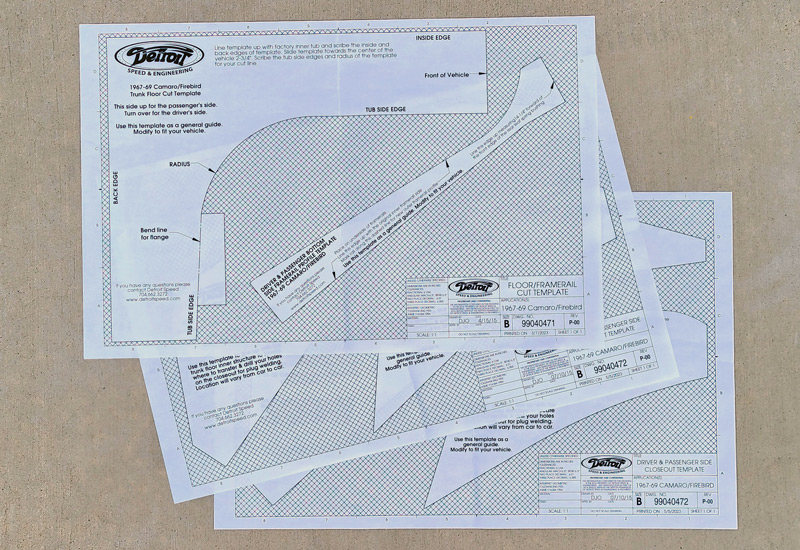

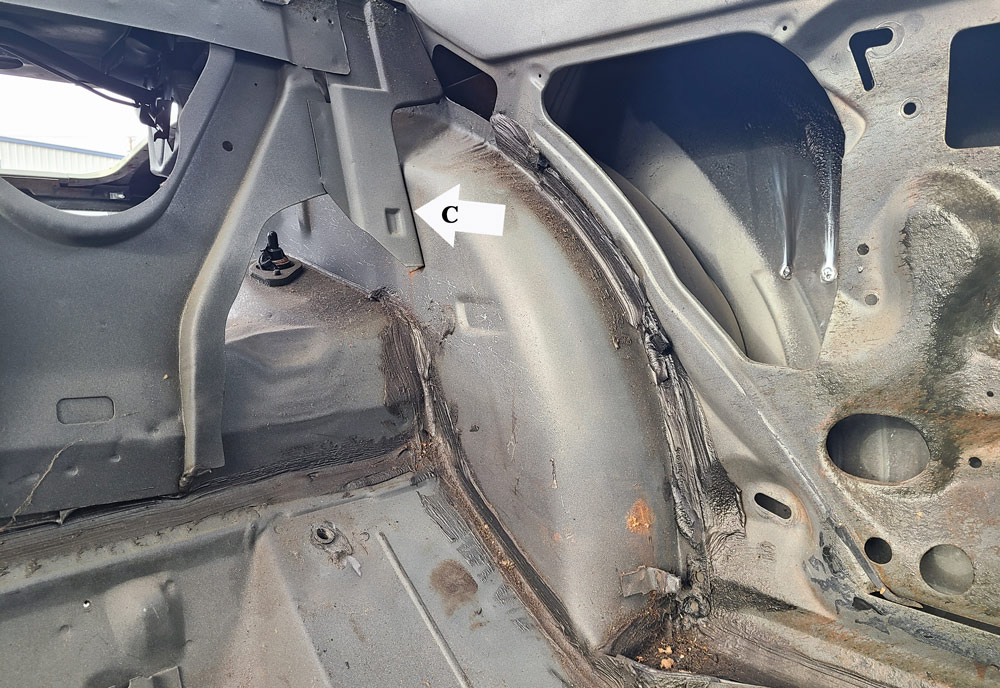
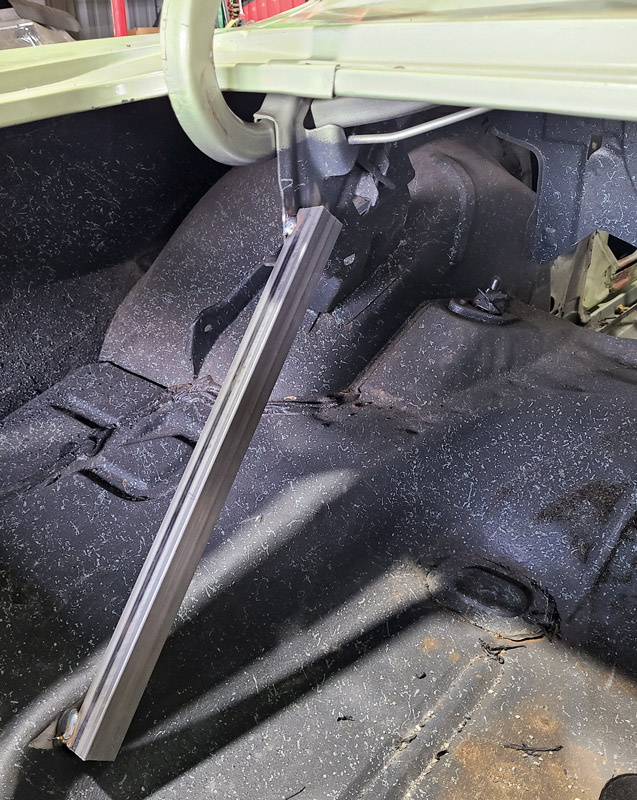
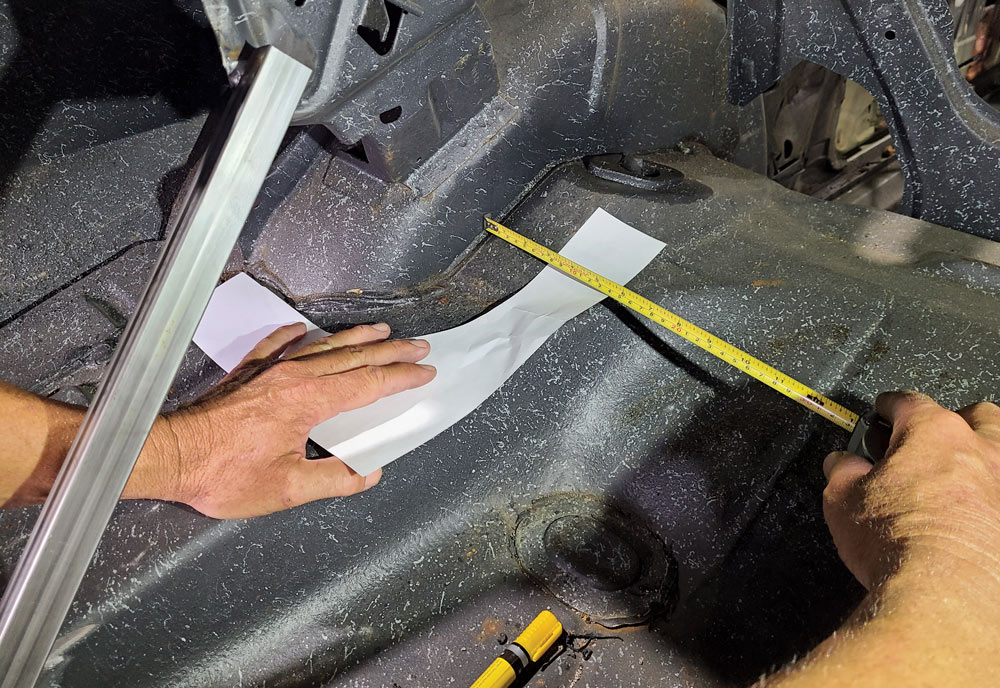
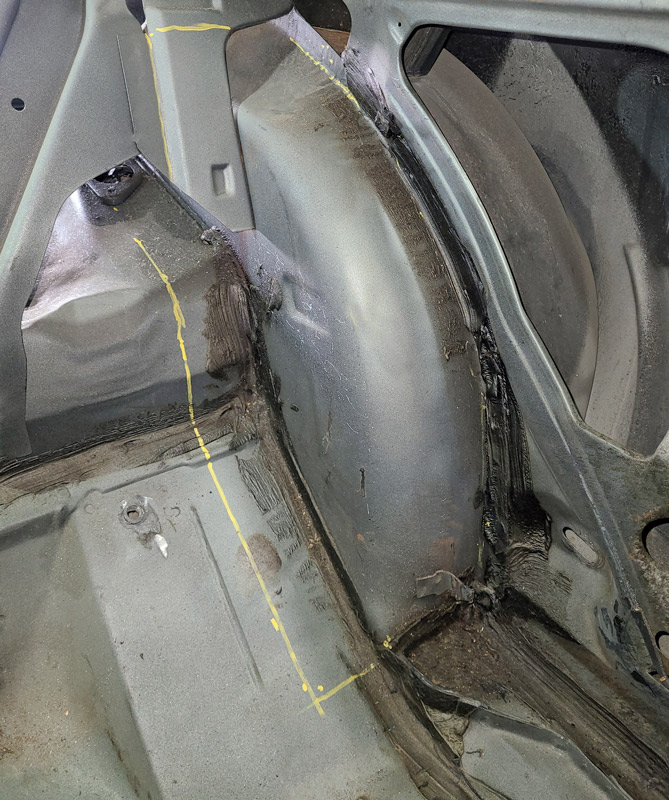
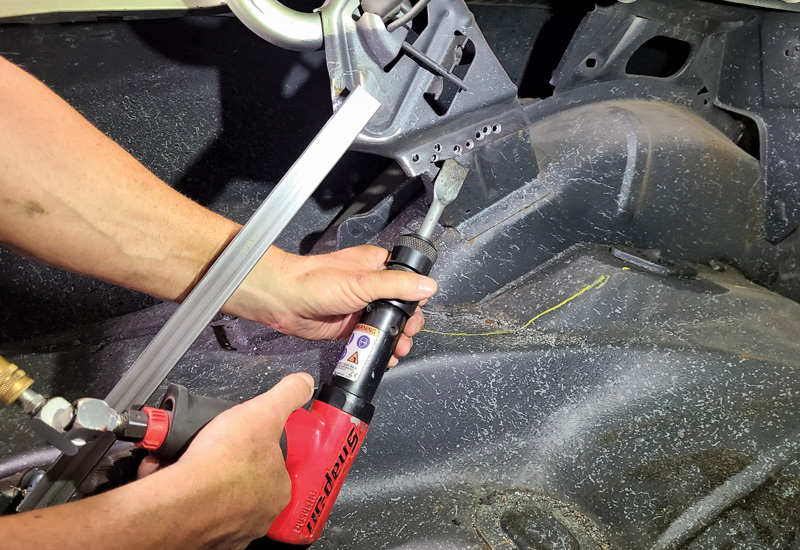
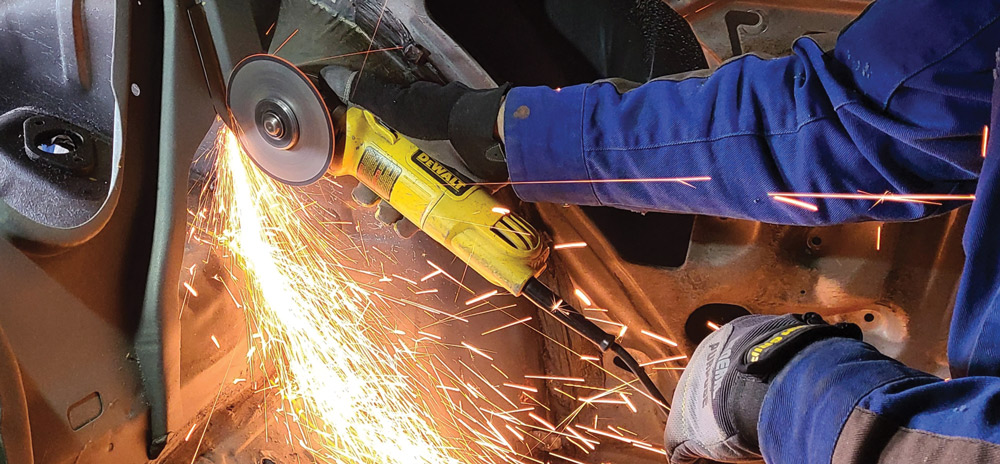

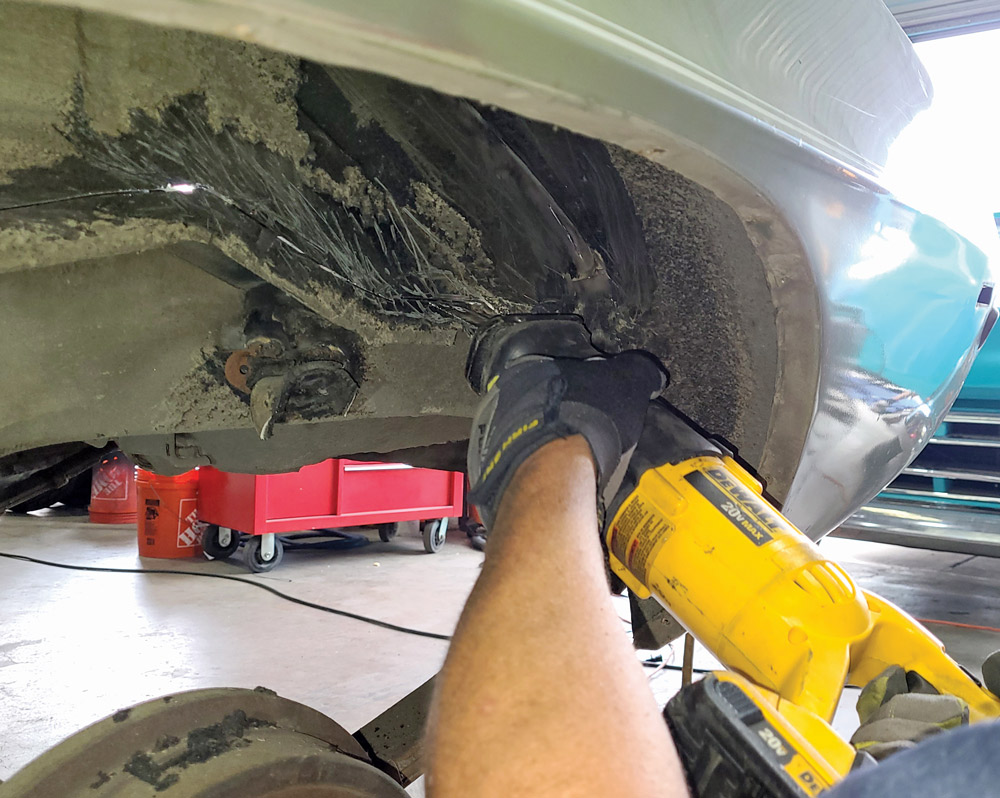
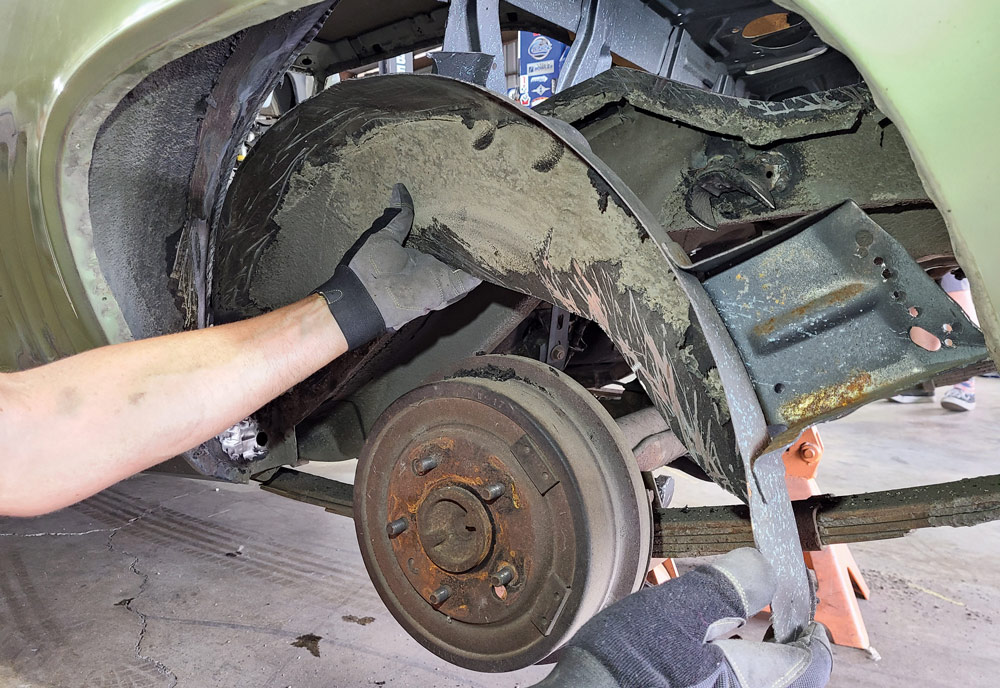
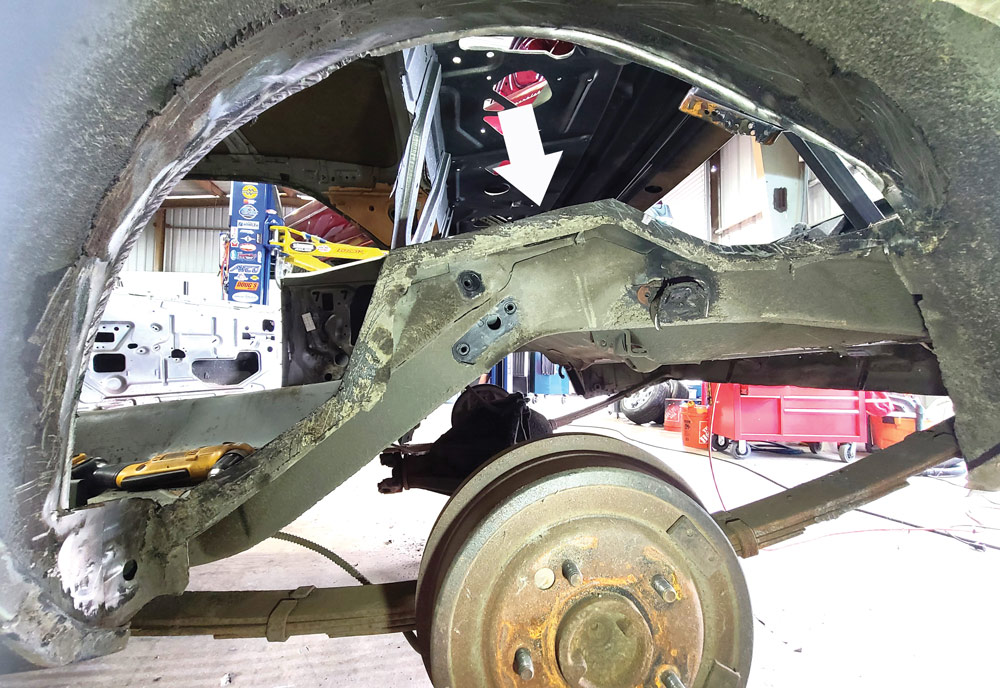

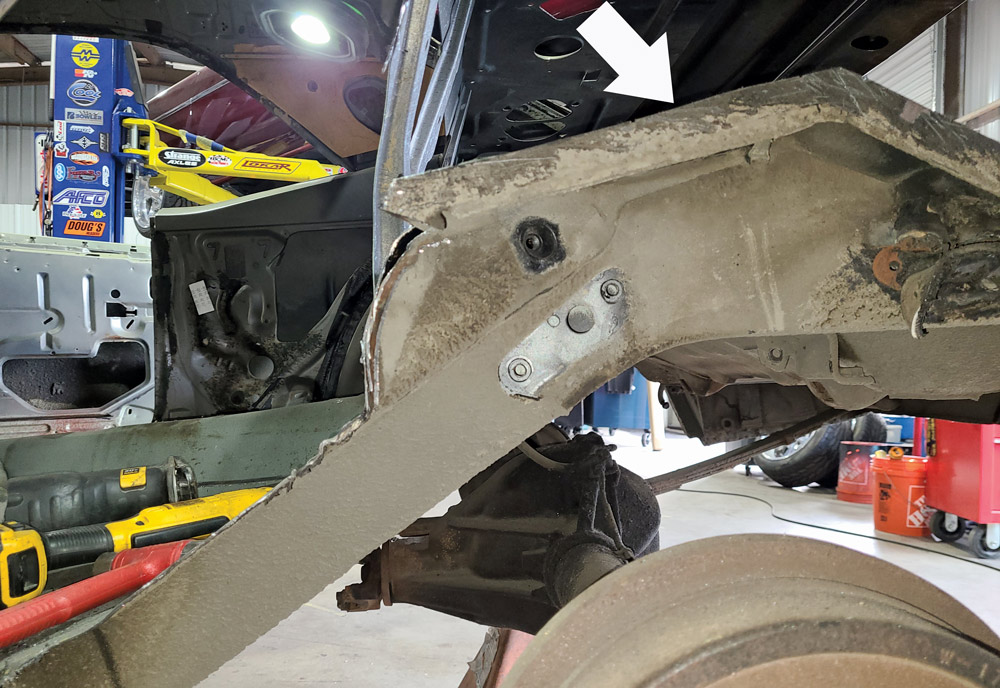
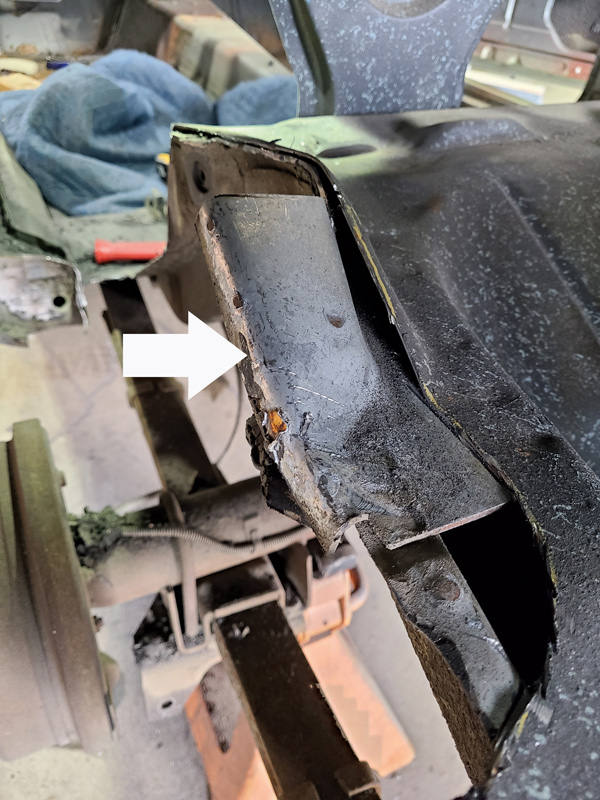
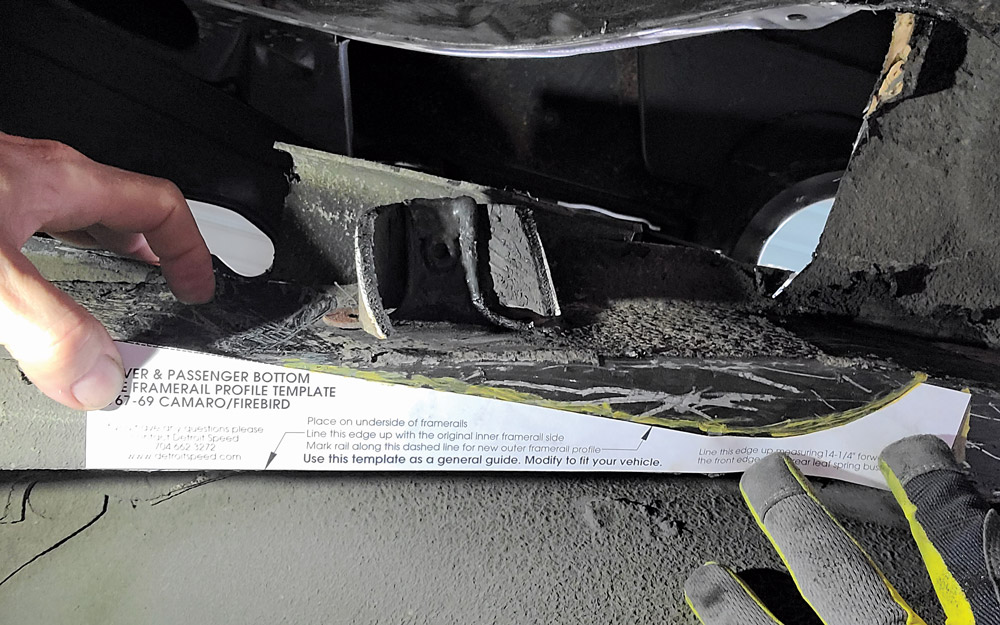



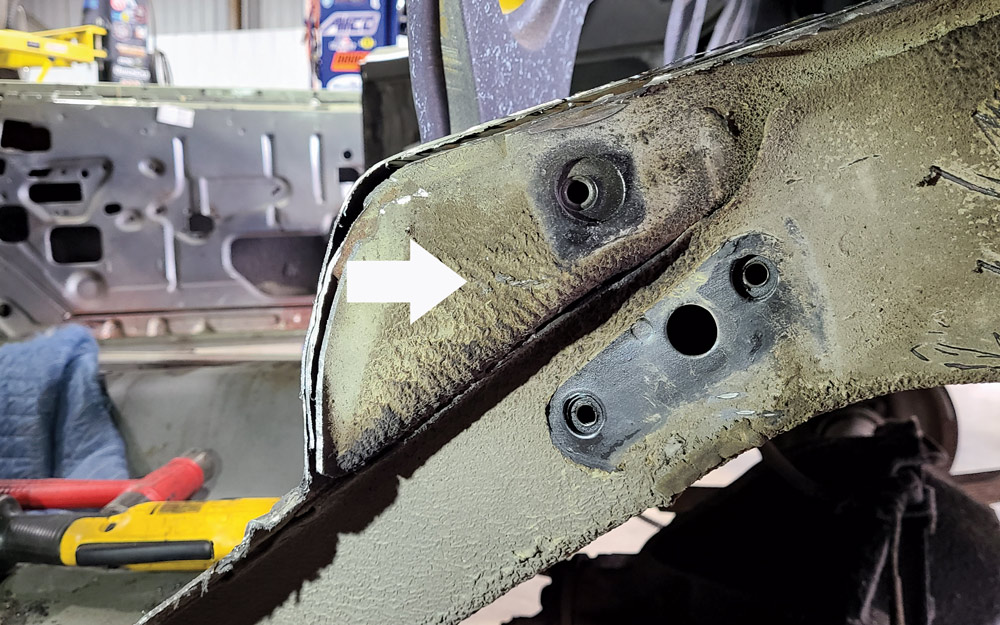
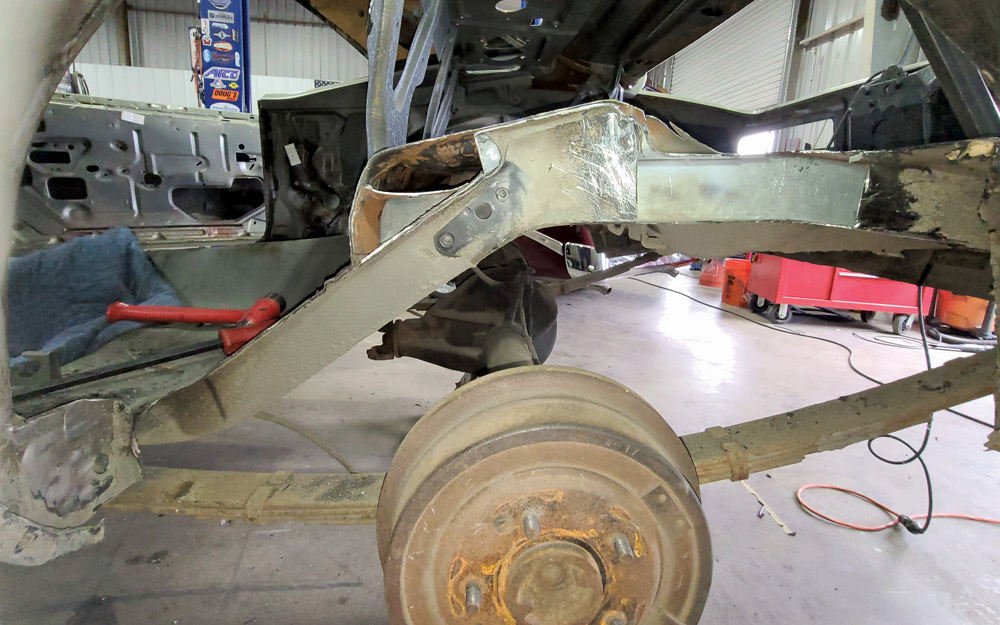



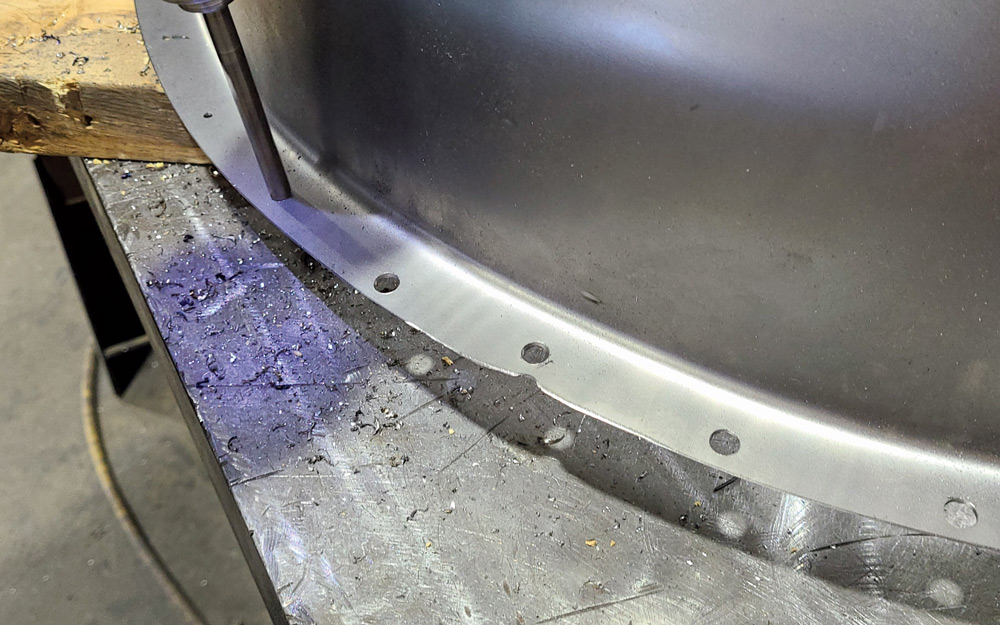


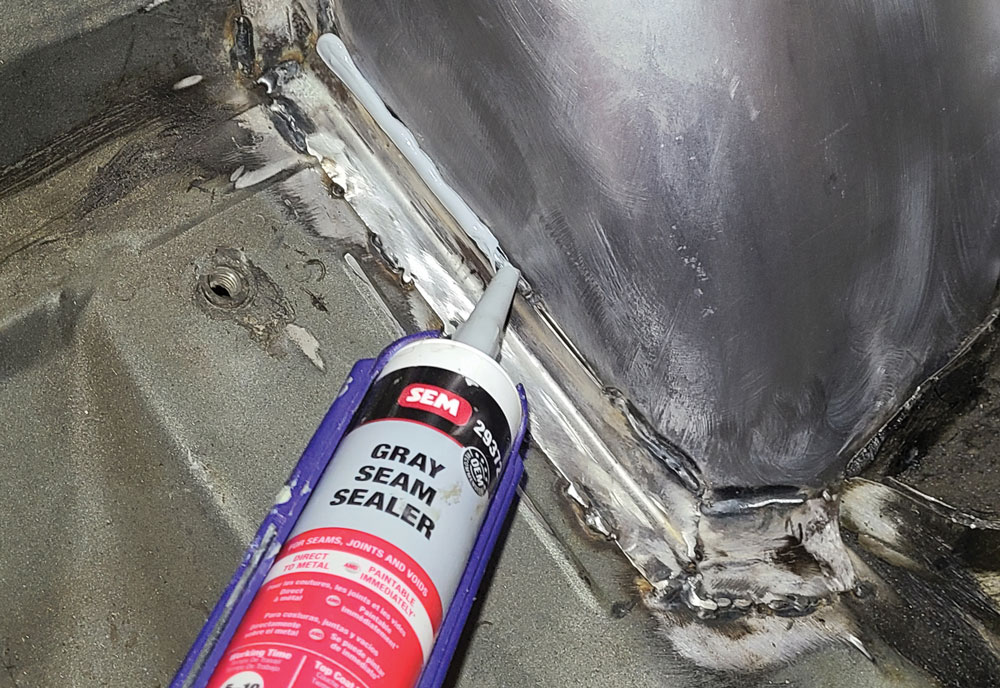
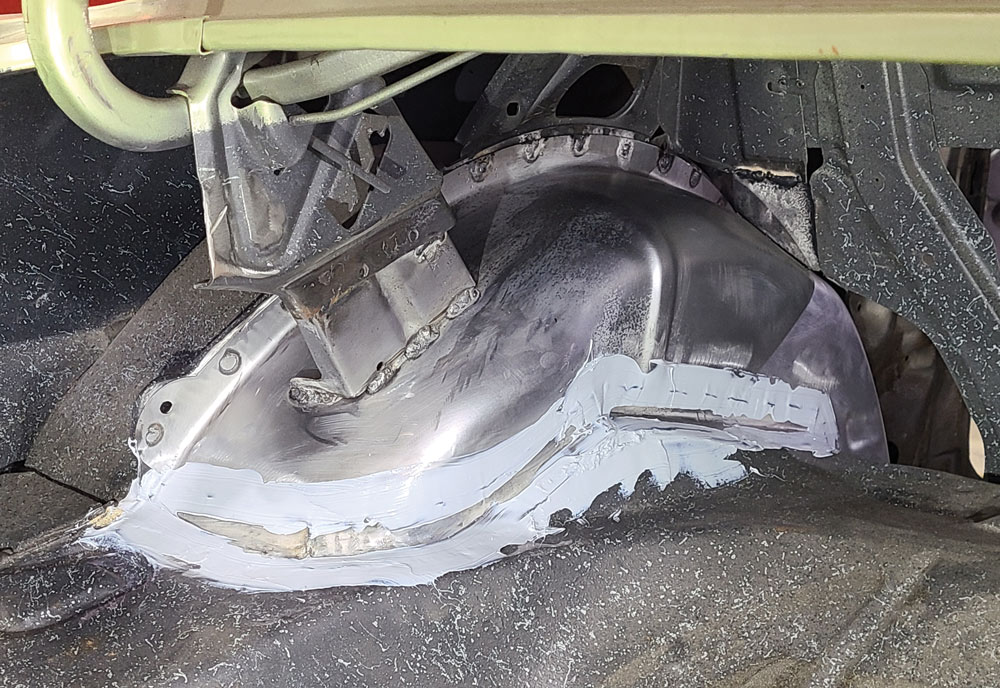

