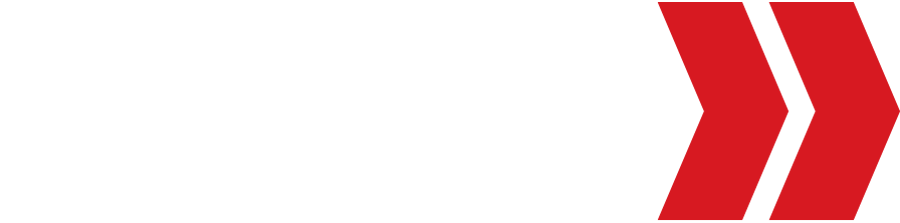
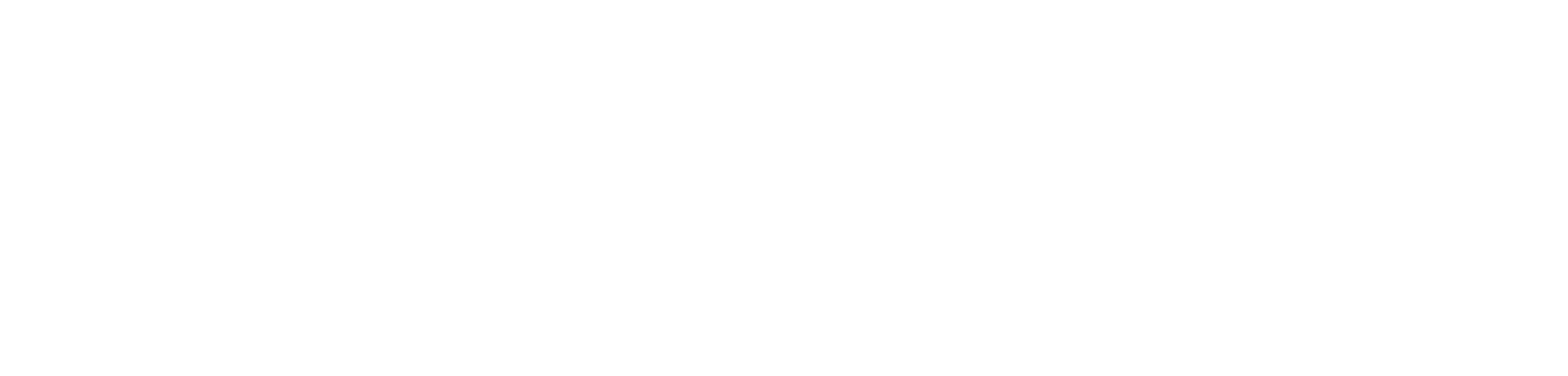
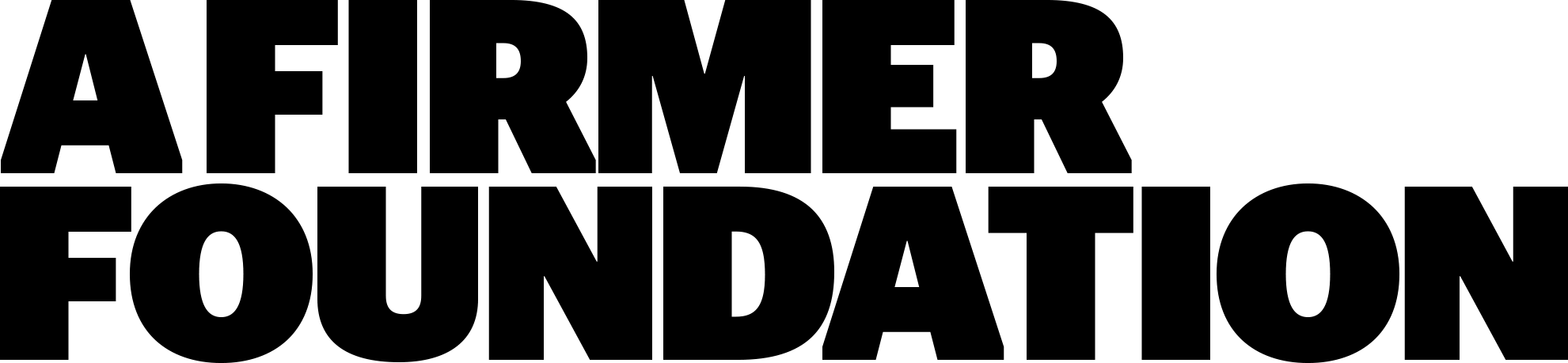
By Barry Kluczyk Photography by THE AUTHOR
tructural rigidity has long been the Achilles heel of unibody cars—particularly cars from the muscle car era, such as the first- and second-generation Camaro. The issue becomes more acute with a significant jump in performance when greater horsepower and handling capability expose the functional boundaries of the body structure.
A weaker structure is not only prone to metal fatigue and even ripping in some areas, but it makes it more difficult to put all the car’s power to the pavement, whether in a straight line or in corners. It’s simply impossible to optimize launches or handling with excessive chassis flex.
So, just as long as there have been flexible unibodies, subframe connectors and other structural enhancements have been the cure—but even they have had their compromises. Typically, they’ve necessarily followed the contours of a car’s floor, which often means less-than-optimal strength. Also: Following the underside of the floorpan often reduces ground clearance while also creating somewhat of an unsightly profile.
That’s where Detroit Speed’s (DSE) first-gen F-body subframe connectors differ. Rather than compromising strength and ground clearance, they literally cut through the floorpan to create a straighter, more rigid, lower-profile link between the front subframe and rear framerails.
Let’s be clear about that: Installing DSE’s subframe connectors requires cutting holes in the floor. Fortunately, they do not interfere with the rear seat mounts in coupe or convertible models, but in addition to the holes to be cut in the floor, the installation also requires notching the front seat risers on both body types as well as the reinforcement plates on convertibles.
We recently followed the installation at Sled Alley where the job was being performed on Mark Stielow’s latest ’69 Camaro project—the one in which we’ve already covered its complete floor replacement. It also just received a new, bolt-on DSE front subframe.
“Even though you’re cutting into the floor, it’s the most effective way to build strength into the body,” Sled Alley’s Matt Gurjack says. “The connectors’ rails don’t intrude much into the floor and the carpet fits right back over them.”
Notably, the rear of the connectors are welded to the rear framerails, while the frontends are bolted in place, allowing the front subframe to remain removable. The portions of the connectors that protrude into the interior are welded to the floorpan, further enhancing the overall strength of the upgrade.
If adding these connectors to an already running-and-driving car it’s going to require pulling out the interior for the job. The brake and fuel lines should also be removed because, you know, it all involves welding in their vicinity. The more practical approach, as seen on Stielow’s car, is to bake their installation into a project that already required stripping back the body to its bare shell.
Either way, it’s the smartest and most effective way to add crucial strength to the F-body’s body structure—strength that will absorb a more Pro Tourer or restomod’s horsepower, while also making sure those ponies stay in line around the bends. If you’re adding big power or handling capability to your early F-body, this upgrade is a must.
Follow along as we provide an overview of the installation procedures.

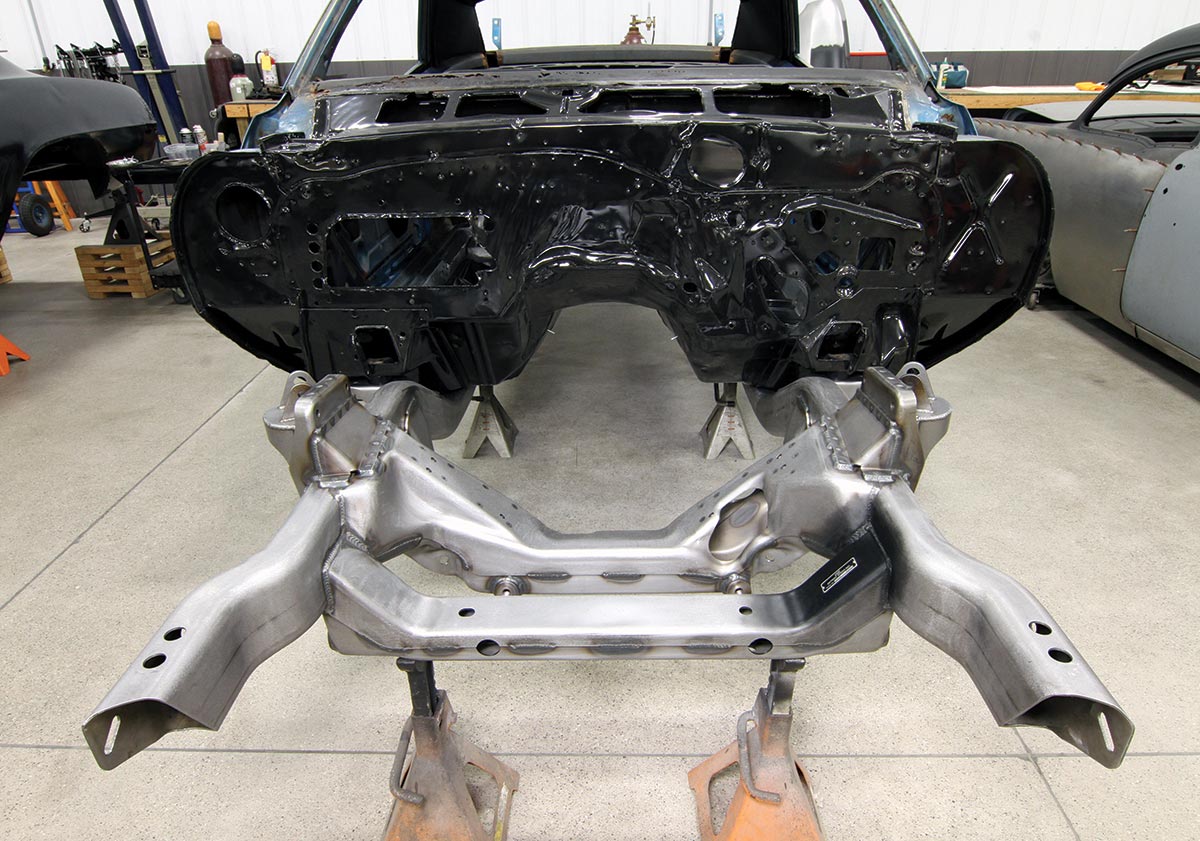
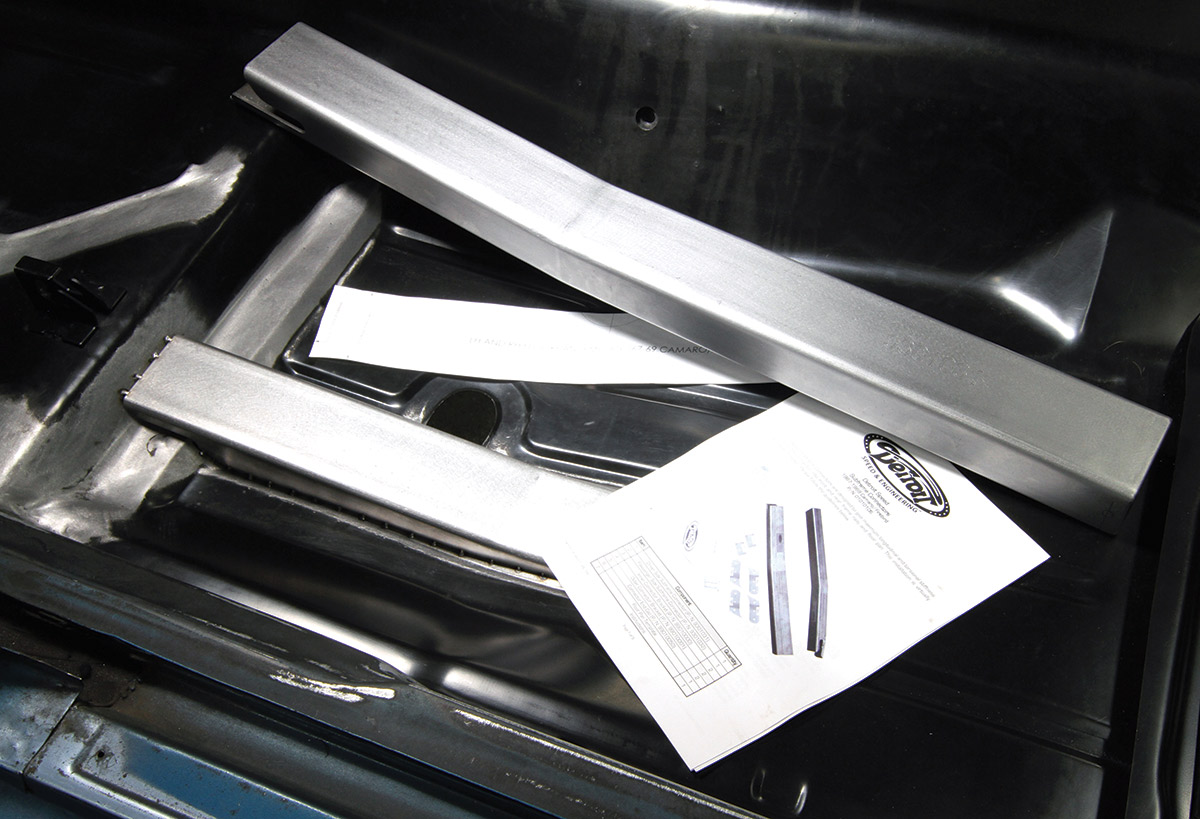
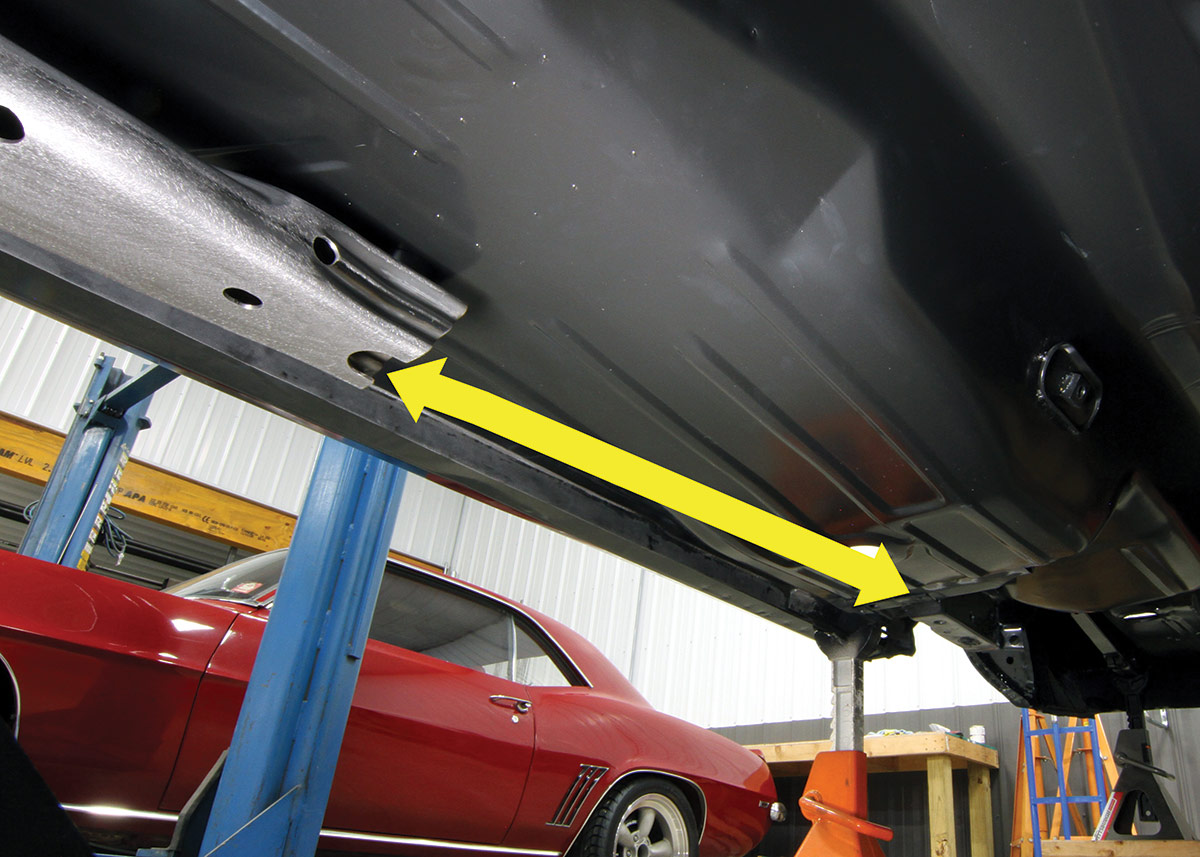
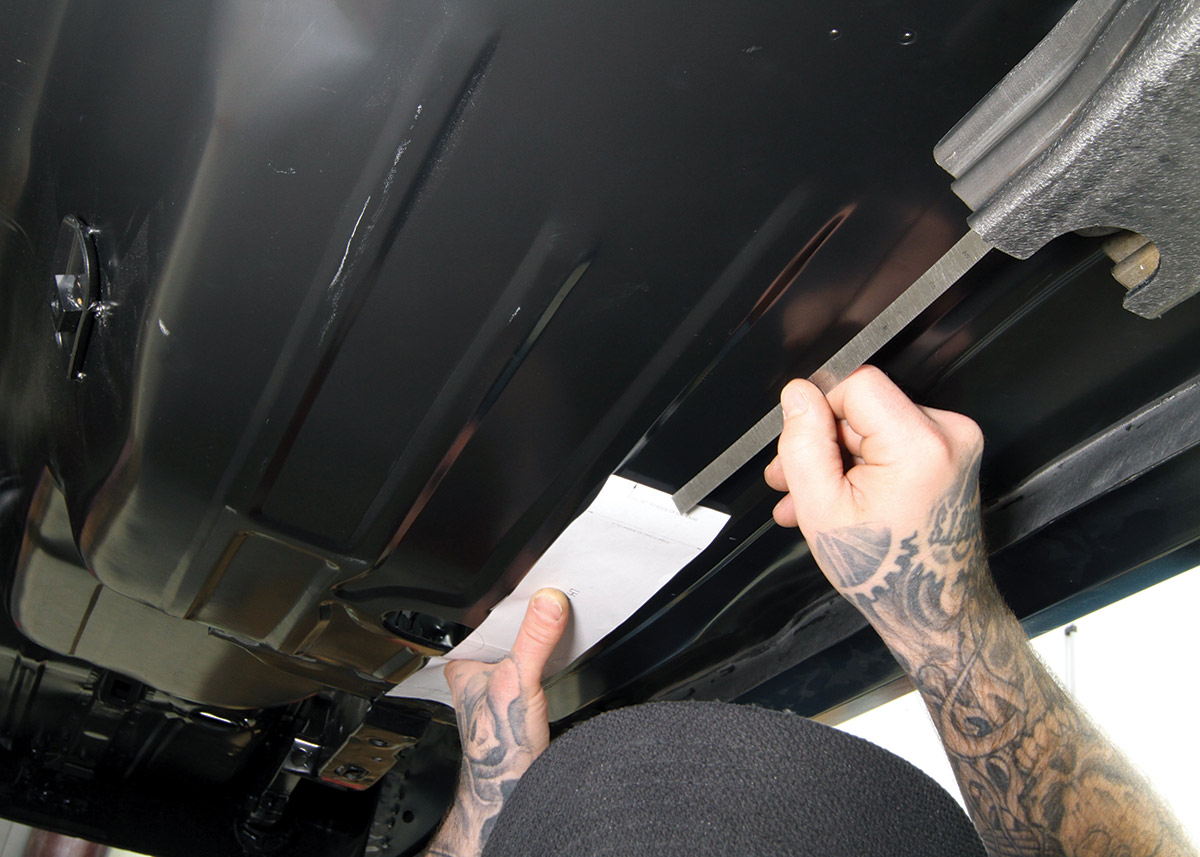
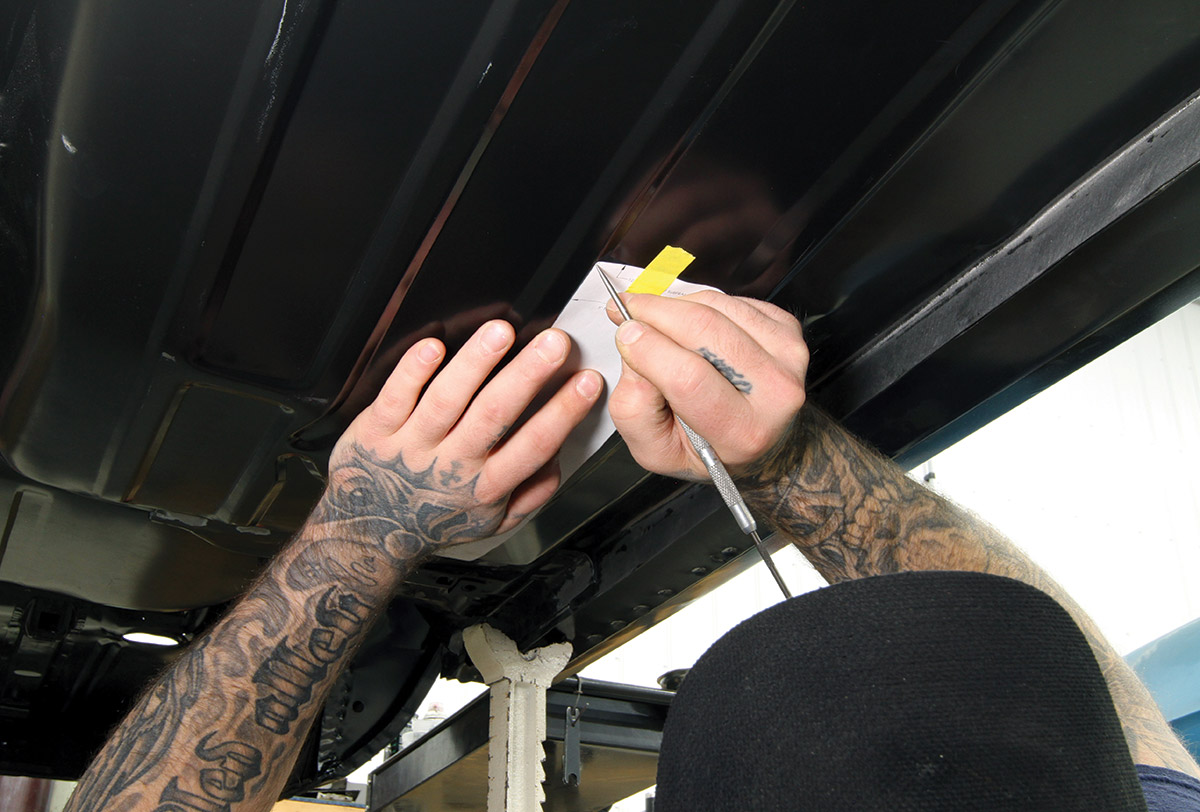
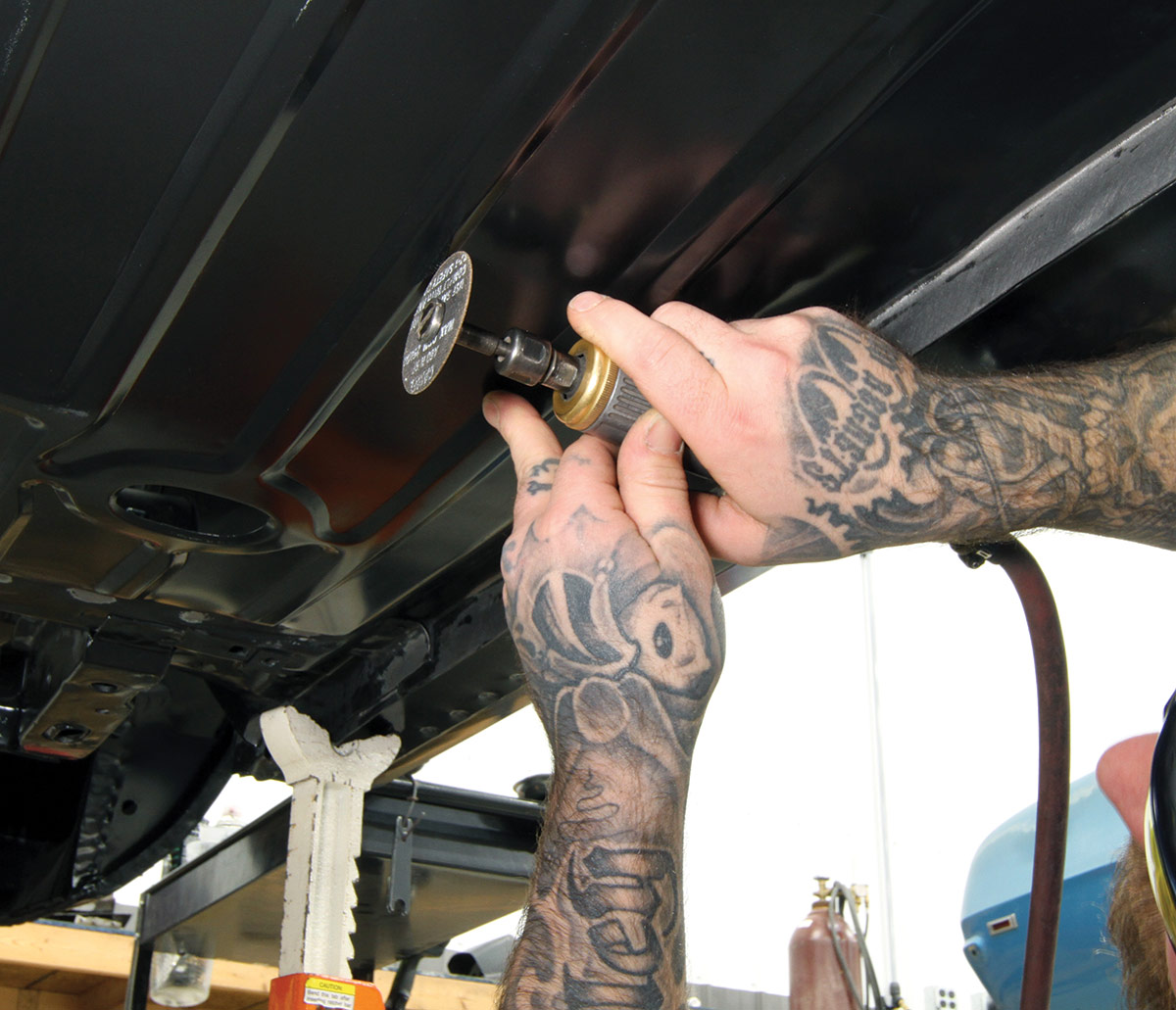


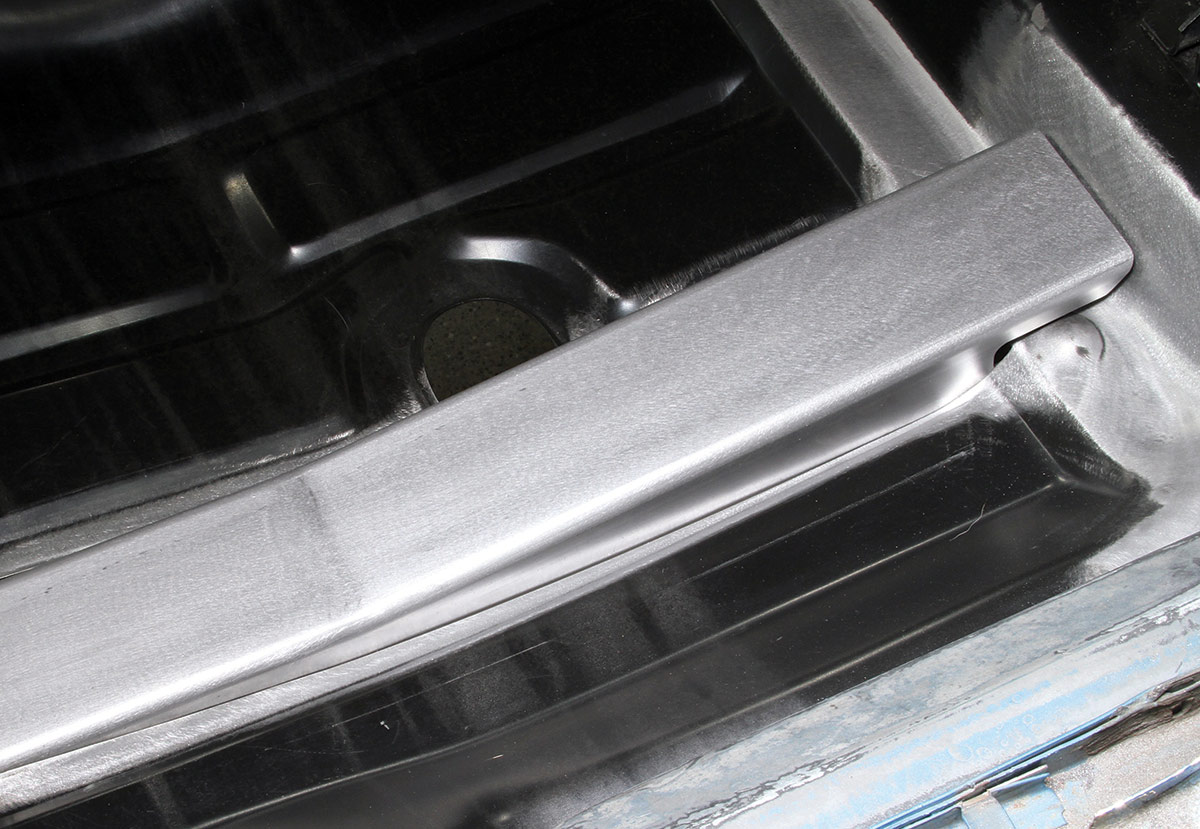
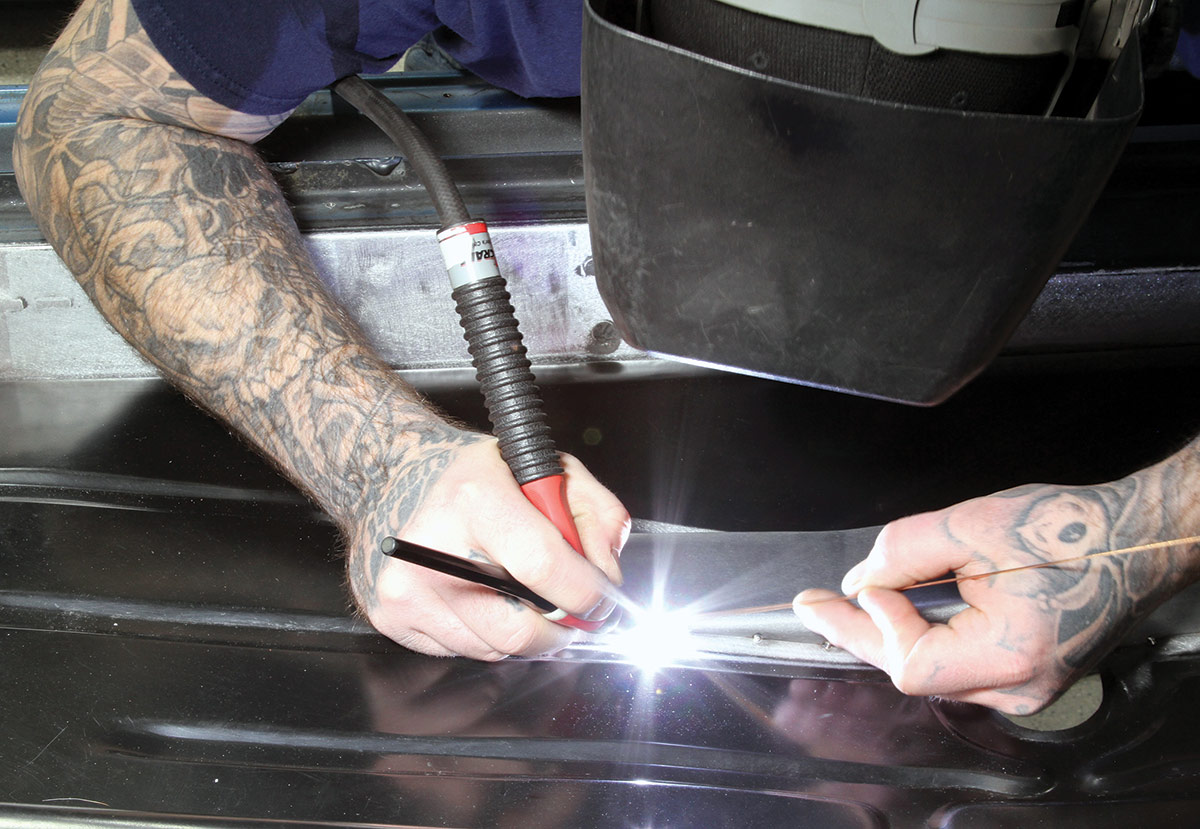
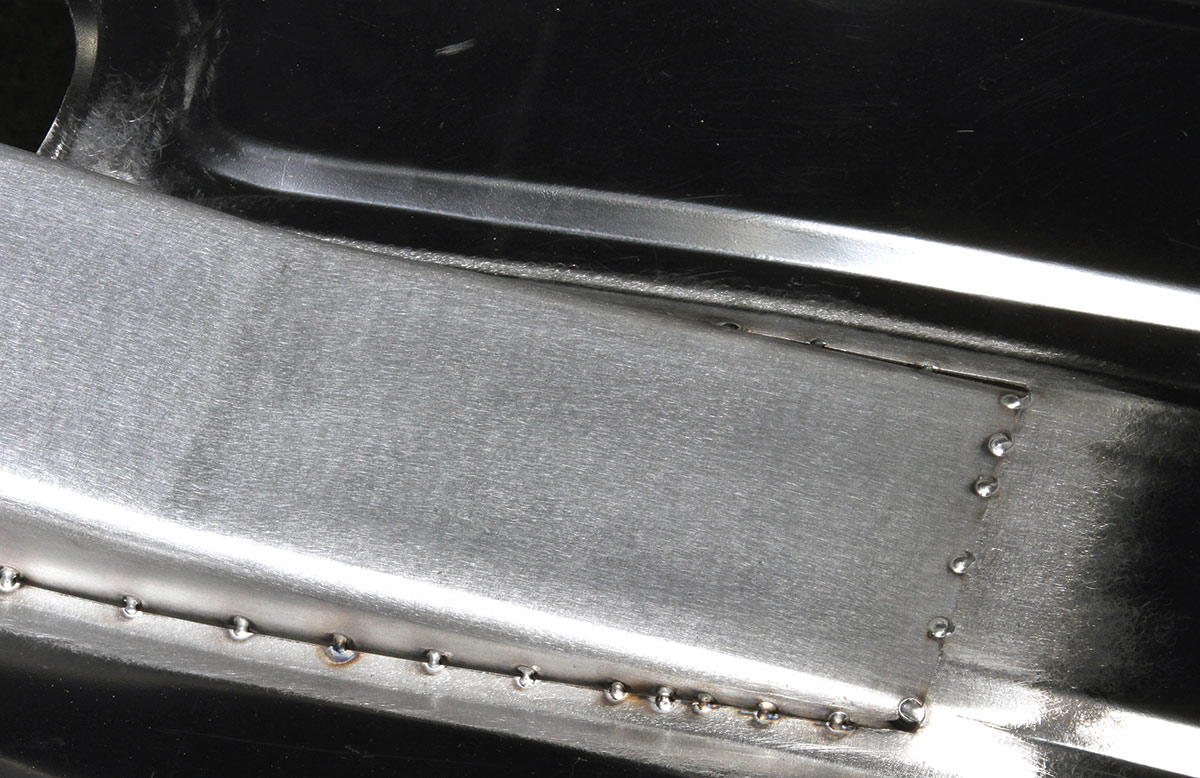

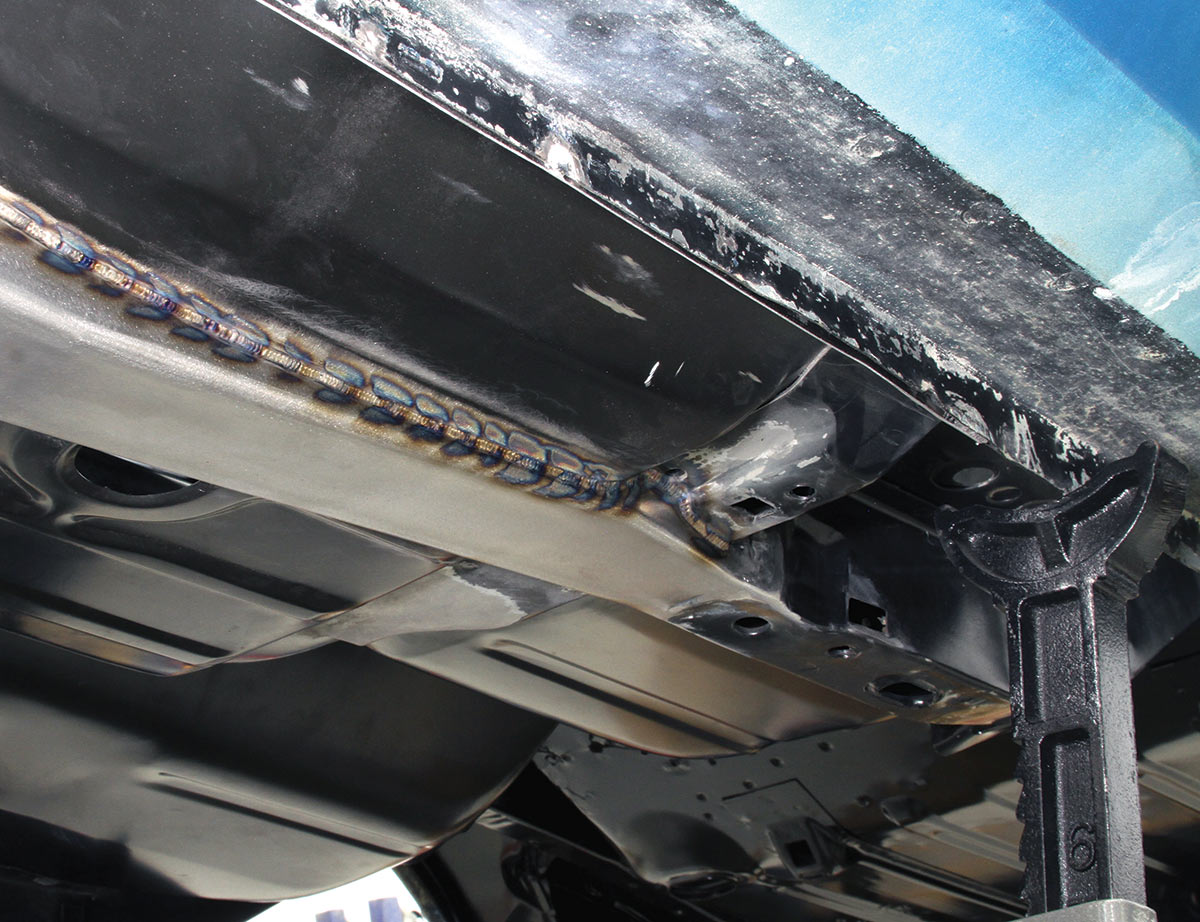


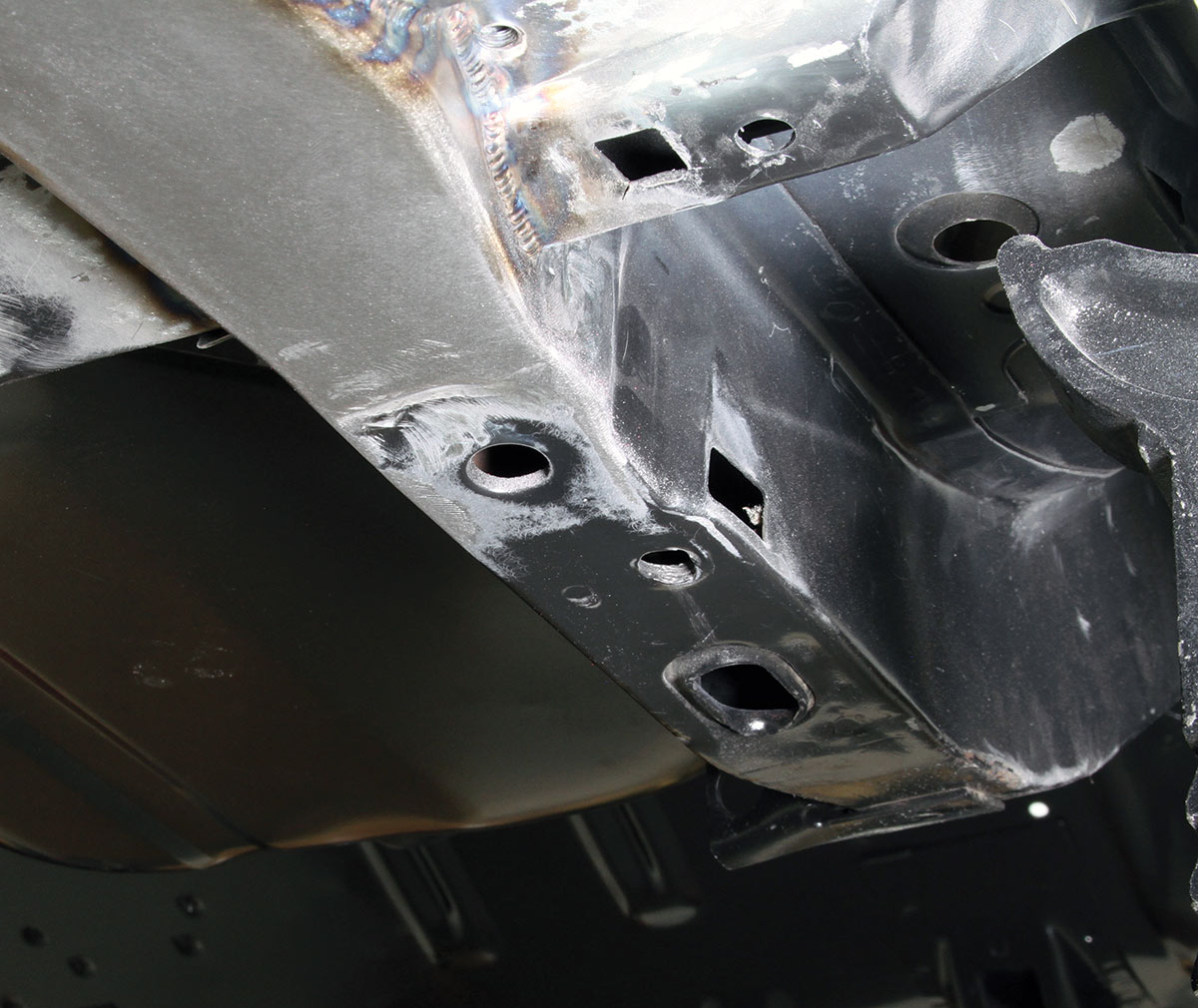
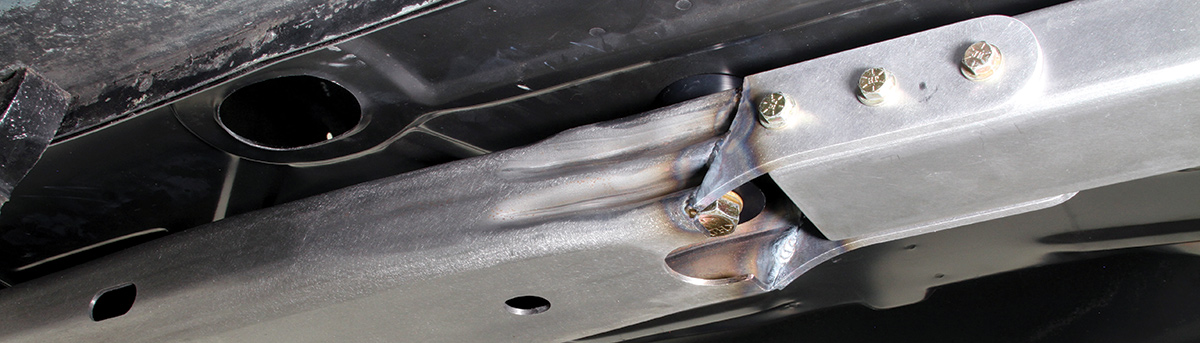

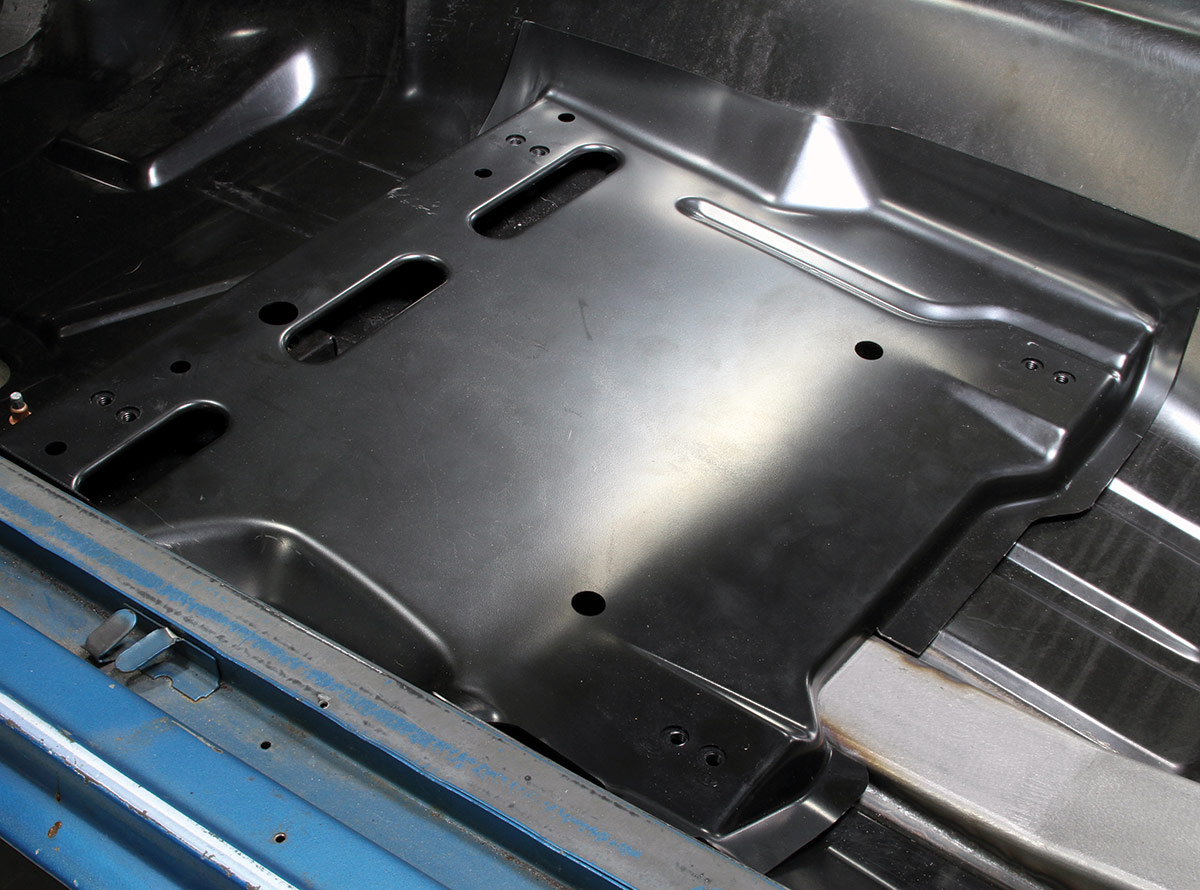


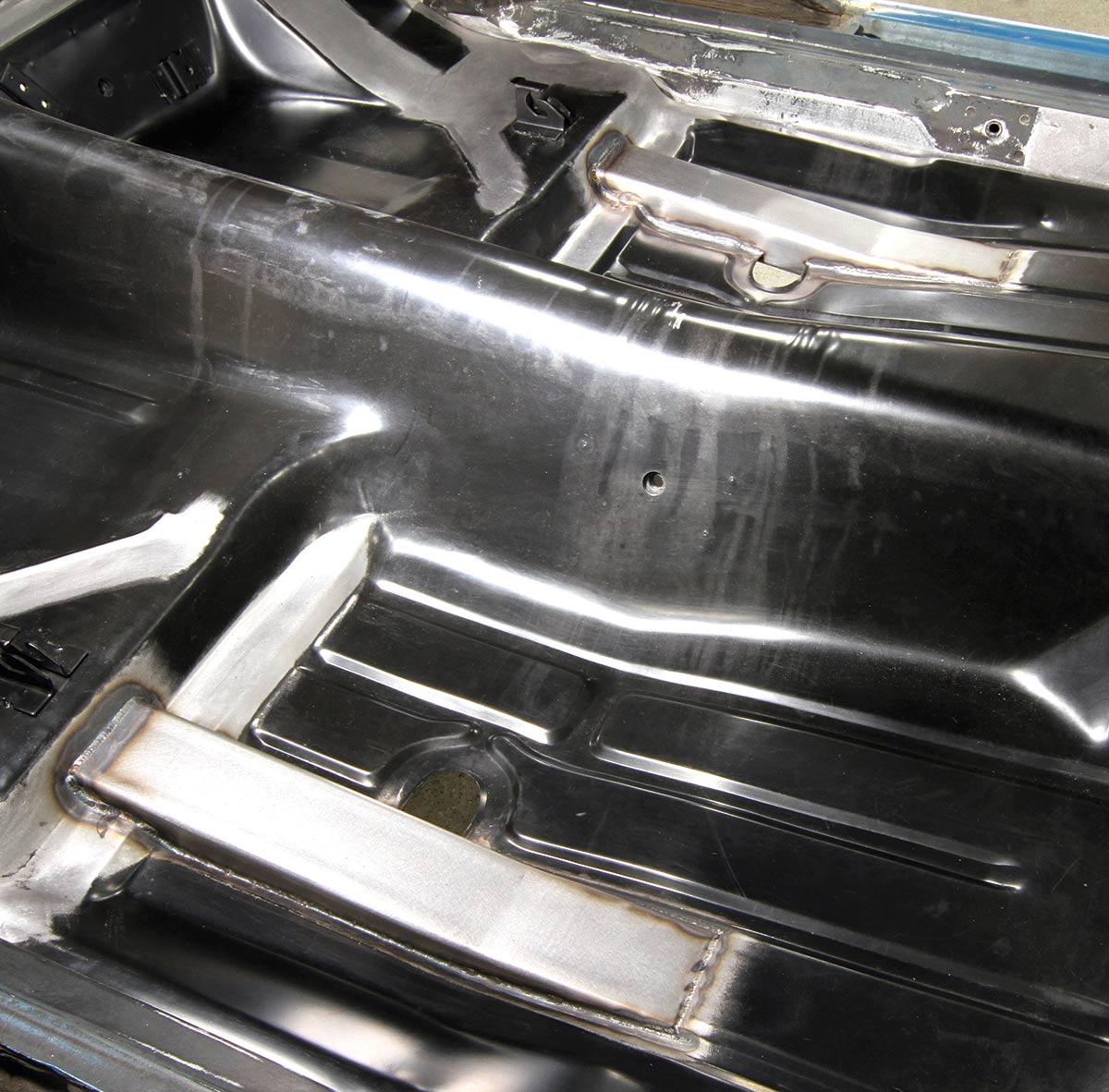
