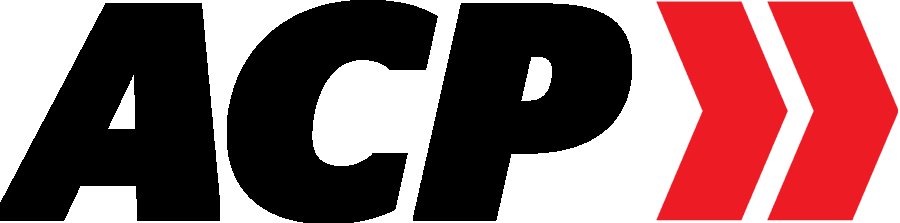
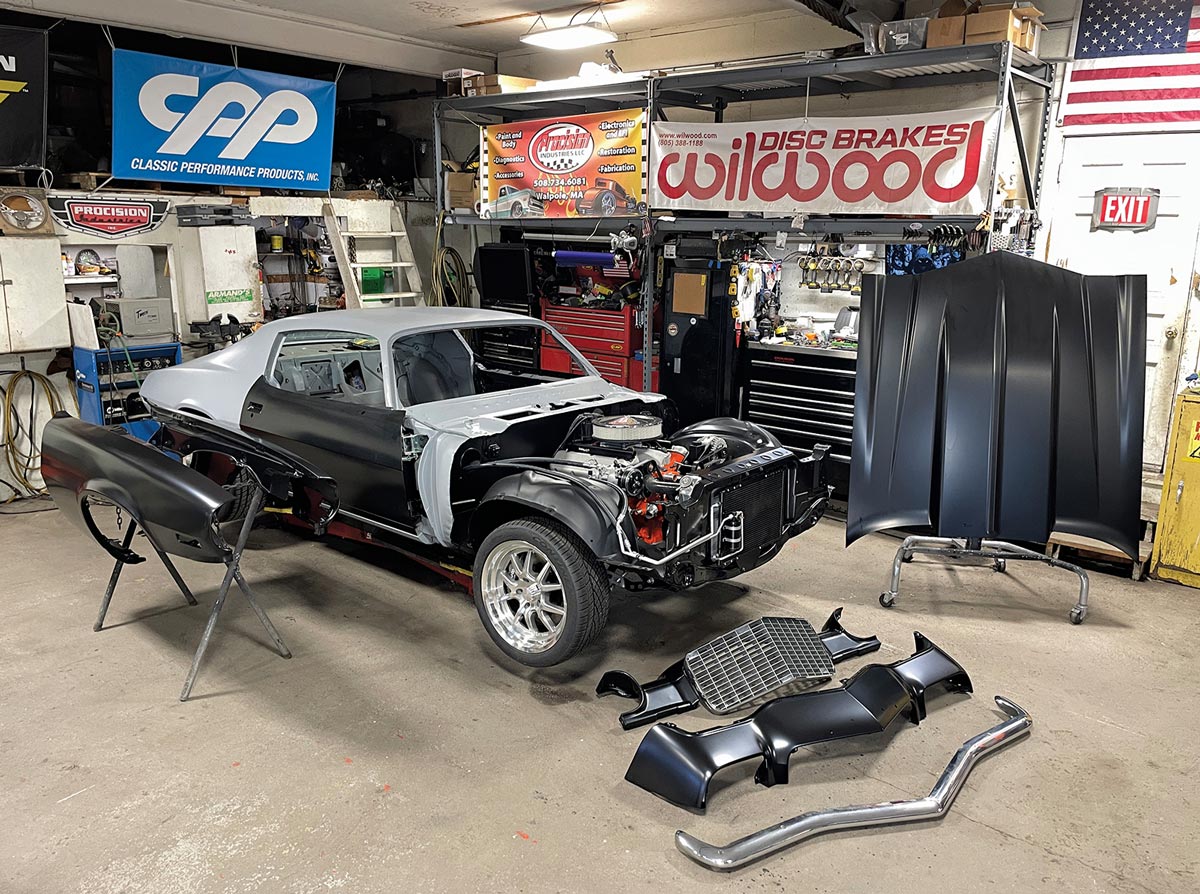



here comes a moment in every buildup where you need to address the status of the body. Many times it can be when all of the mechanical and chassis fabrication upgrades are finally completed. It’s always good to have a plan of action regardless of whether you’re going from ground-zero or taking it on in steps to reach your goals. Regular readers of All Chevy Performance will recognize the ’71 Camaro laid out across our pages as having started its journey as a picked-down shell that was totally bare bones and barely a roller. It’s certainly come a long way through past articles addressing the suspension, brakes, LS driveline, cooling, and exhaust.
We recently followed up at Procision Industries in Taunton, Massachusetts, where shop owner Pat O’Brien was preparing to move forward on the next step of addressing the body. Seeing that the car was void of any front sheetmetal, it was a perfect time to look into options and address ideas of how he would like the styling of the car to look. O’Brien contacted Auto Metal Direct (AMD) to check out their vast catalog of sheetmetal components as well as everything needed to complete the full assembly of the front end. Any particular needs for your restoration project, from body components to glass, electrical, trim, and everything else you could imagine, they’ve got it covered.
When it came to the front end, there were numerous choices available, from standard front sheetmetal, including the fenders, valance, header panel, and one-piece bumper with grille, to the Rally Sport version incorporating turn signals in the header panel as well as offering split bumpers and an Endura nose. Here, the decision was made to incorporate the standard front end sheetmetal accented by a 2-inch raised cowl hood. To complete the installation, AMD included a complete Master Body Hardware Kit (PN H-70FB-S, 368 pcs) as well as all related brackets, rubber components, shims, latches, plastic components, and filler panels. Taking on a job like this it’s important to have help, especially when it comes to panel fitment, alignment, and hood installation.
Bringing it to the next level regarding underhood components, a call to Eddie Motorsports raised the bar with a set of their CNC-machined billet hood hinges crafted in the USA from high-quality 6061-T6 billet aluminum. The stunning hinges feature stainless steel nitrogen-filled gas struts with sealed bearings for flawless hood operation and are available in varying strengths to accommodate all types of hoods, from standard steel to fiberglass and even carbon fiber. They’re available in a machined or polished finish as well as a myriad of custom Fusioncoat colors and arrive ready to install with all the needed stainless steel mounting hardware.
Finally, Rocket Racing proves that performance and stunning looks don’t have to break the bank with their flow-forged aluminum one-piece wheels, which are available in a number of different sizes and offset combinations for most popular applications. Here, the Attack-Series wheels feature a generous caliper clearance design along with a crisp machined face and rim with titanium color accents and a clearcoat for protection while a set of Continental ExtremeContact DWS06 Plus Series tires ensure excellent handling.
Seeing the car with its new front end sheetmetal and wicked rollers easily raises a pulse rate as the build moves closer to the street every day.
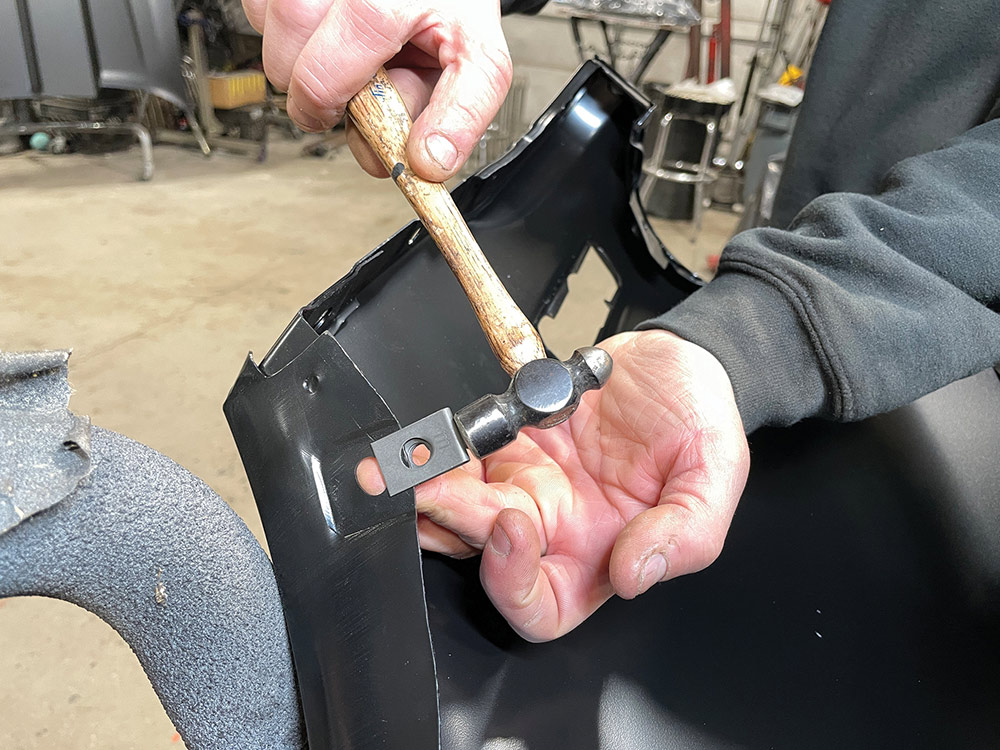
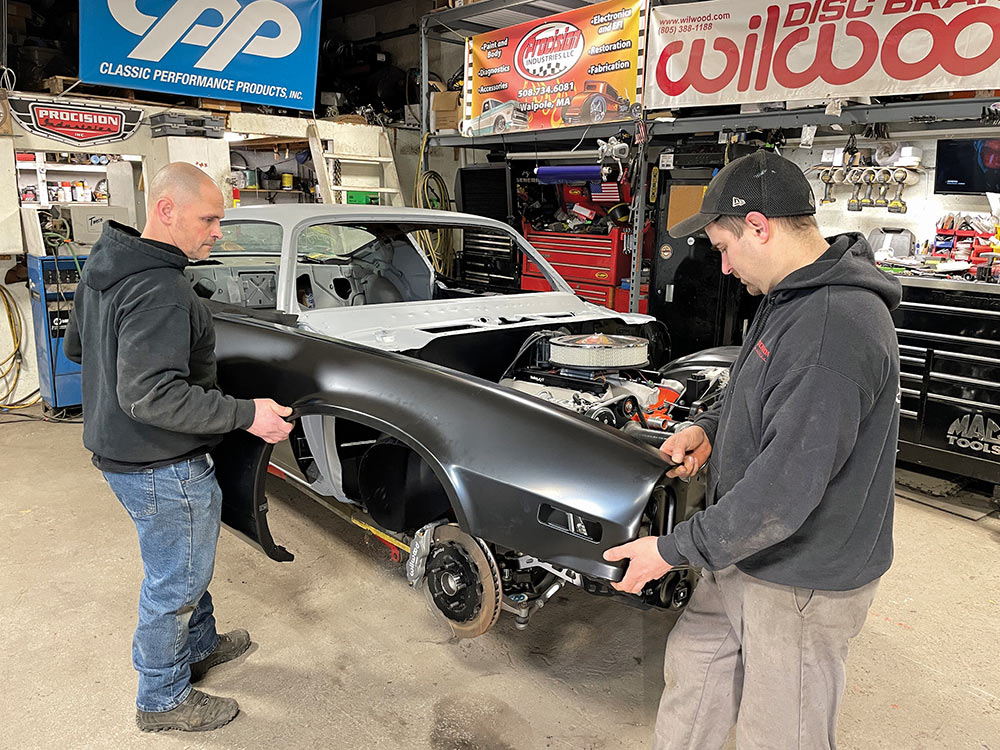
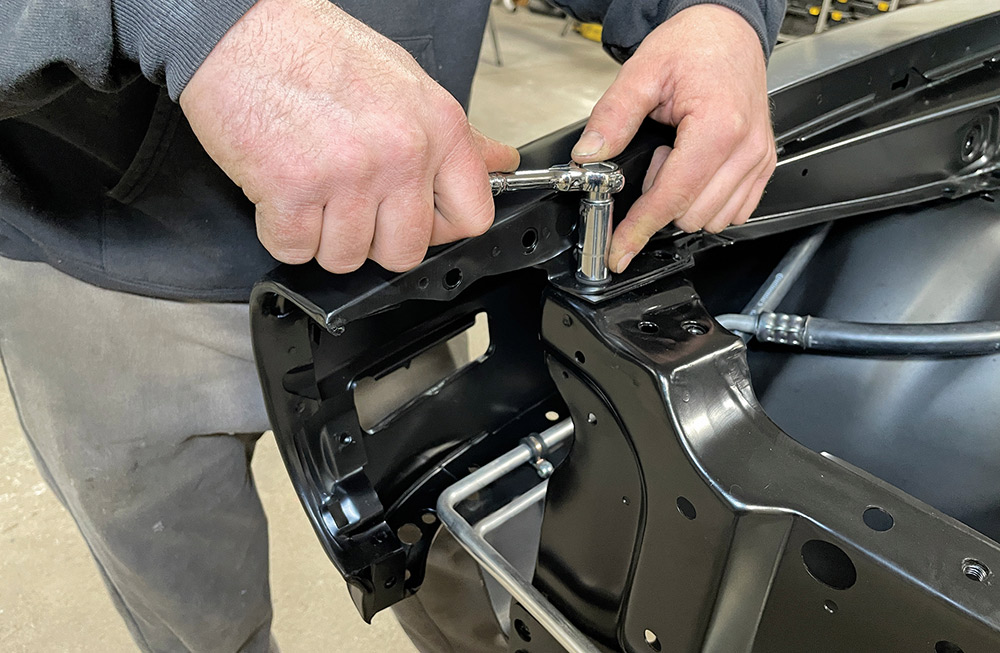

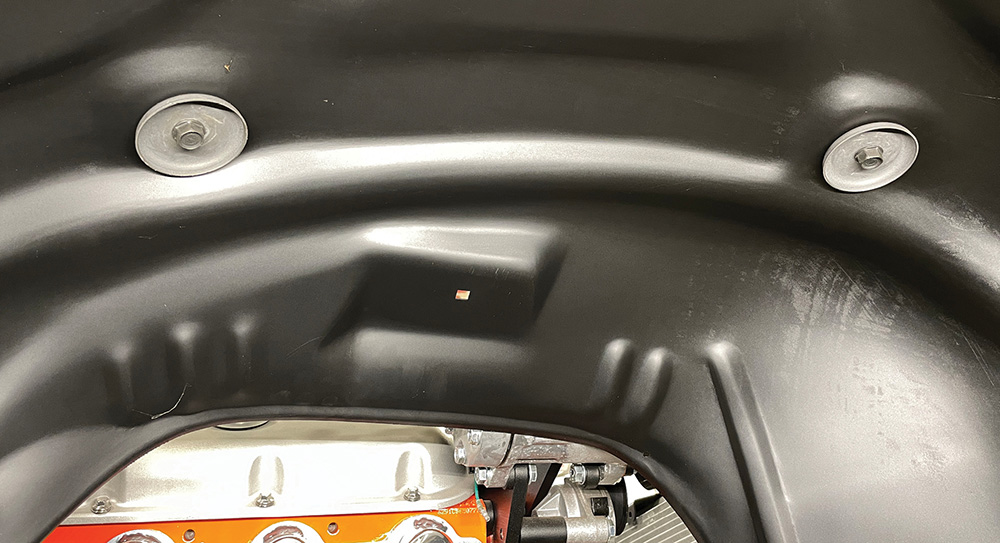
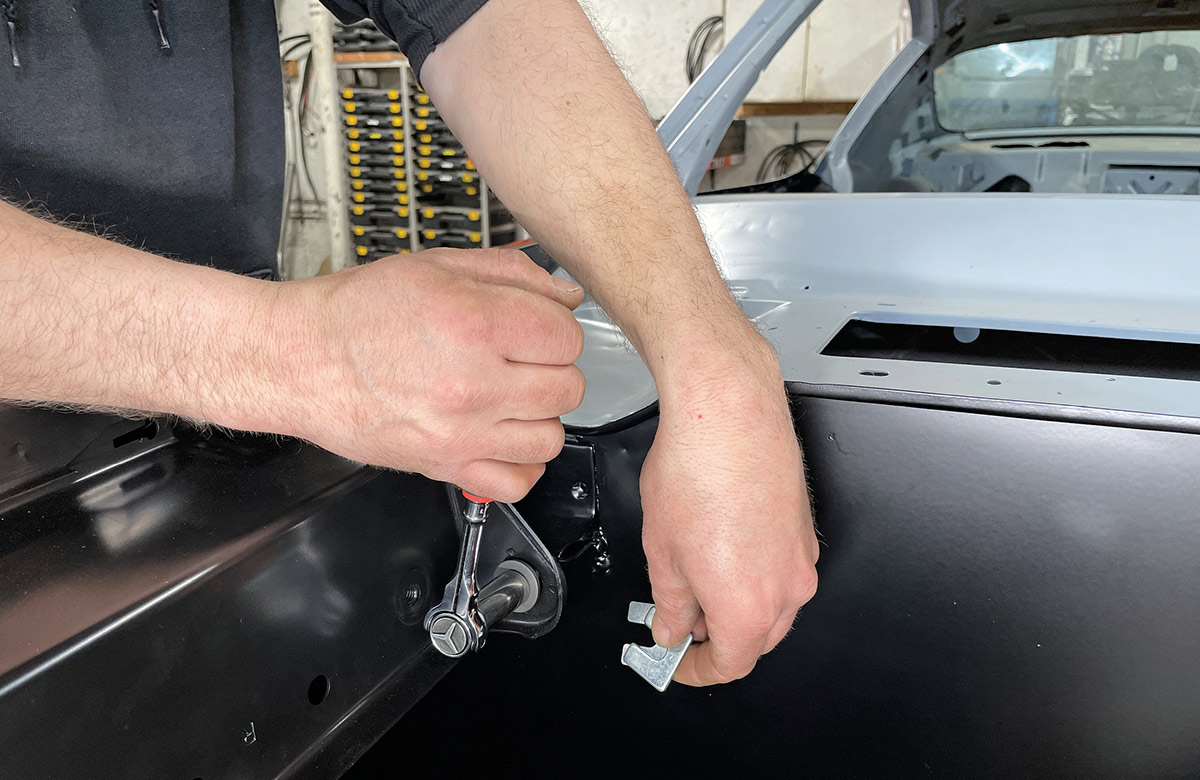
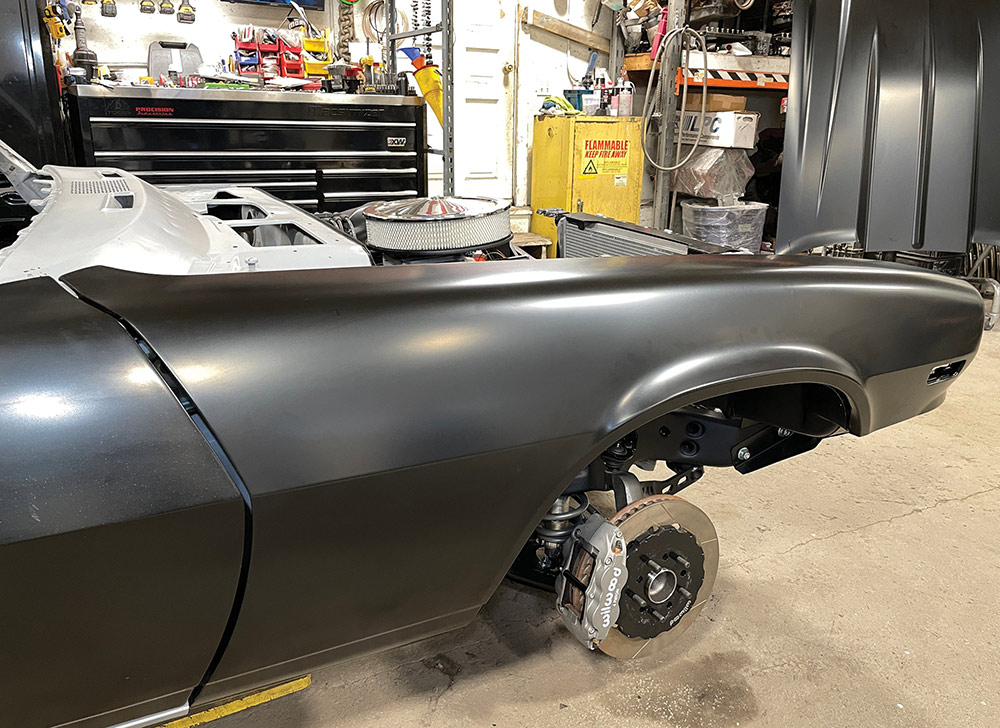
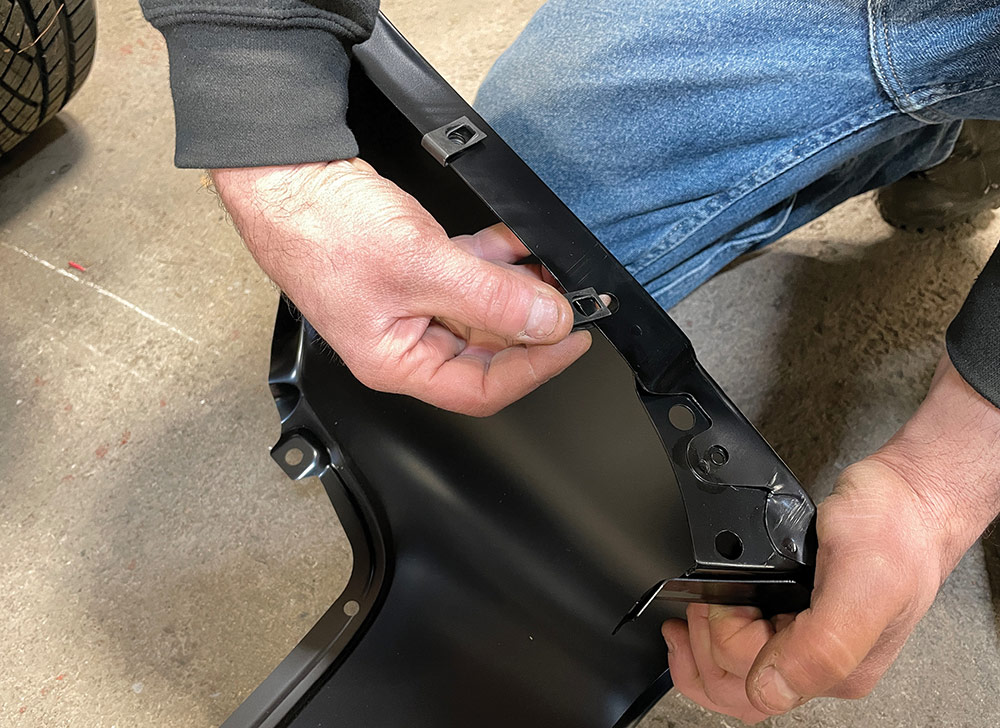
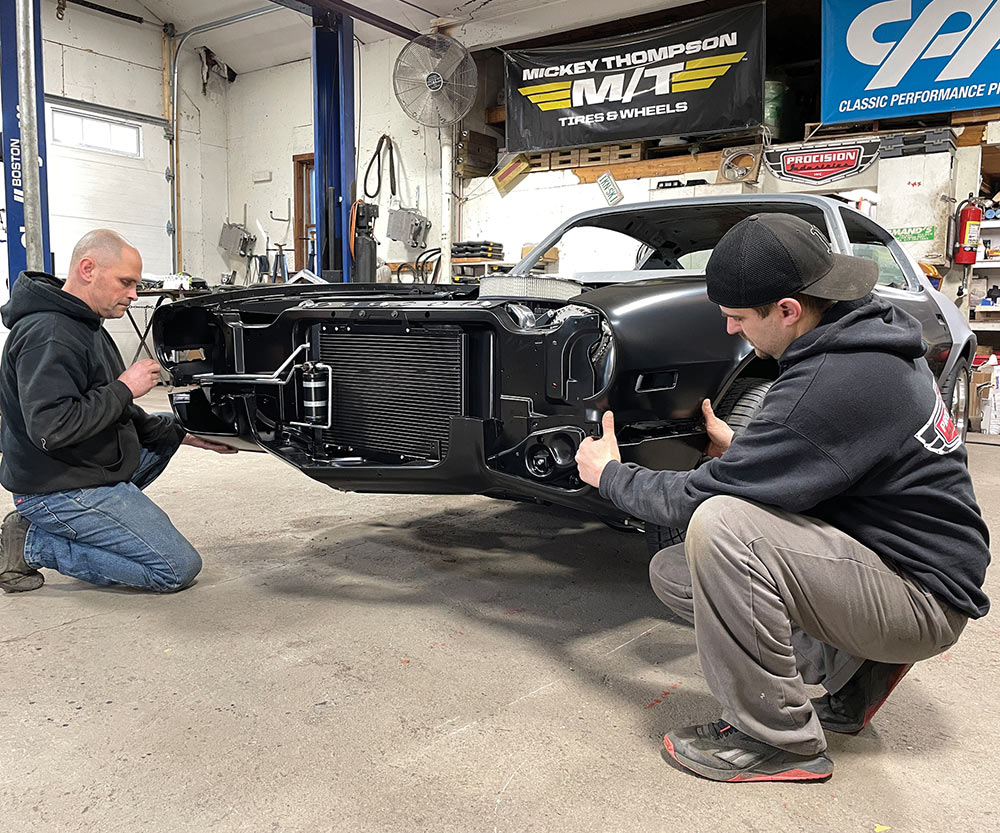
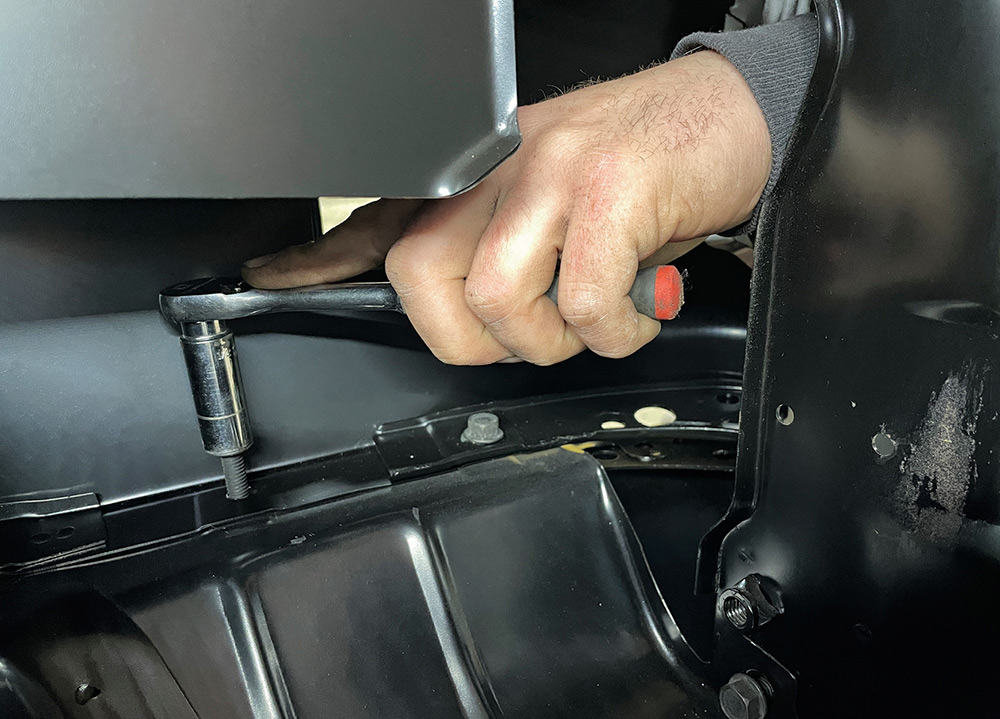
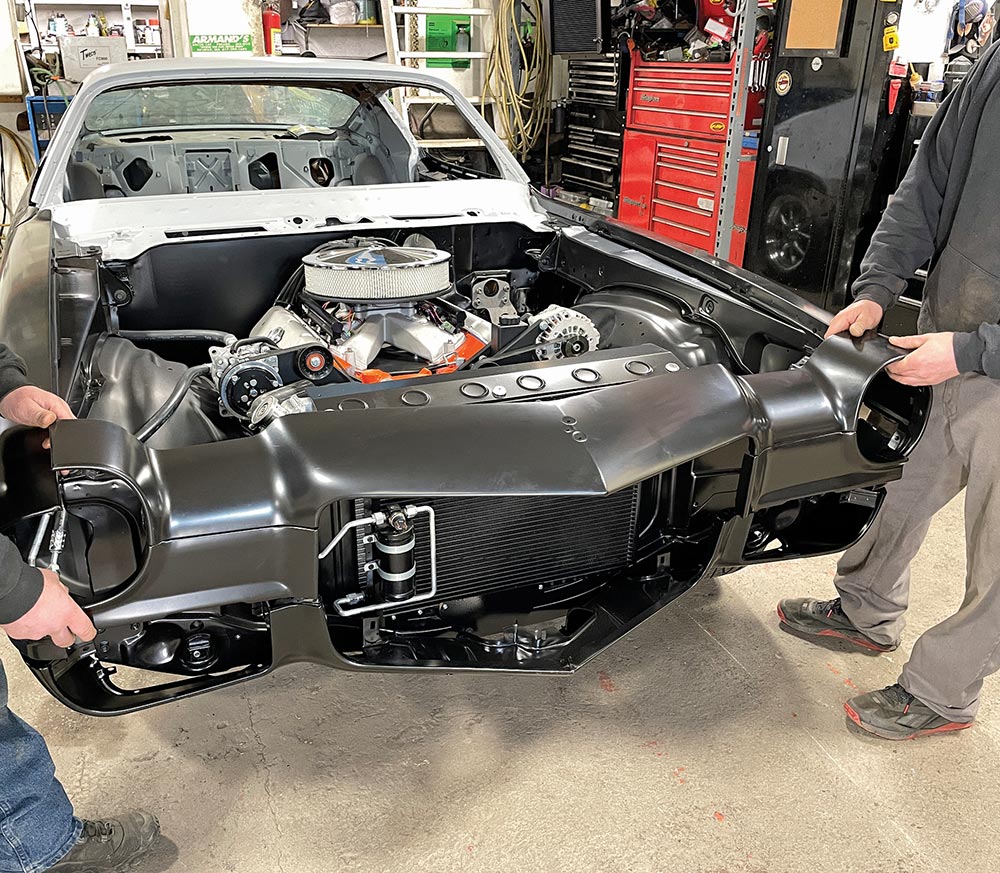

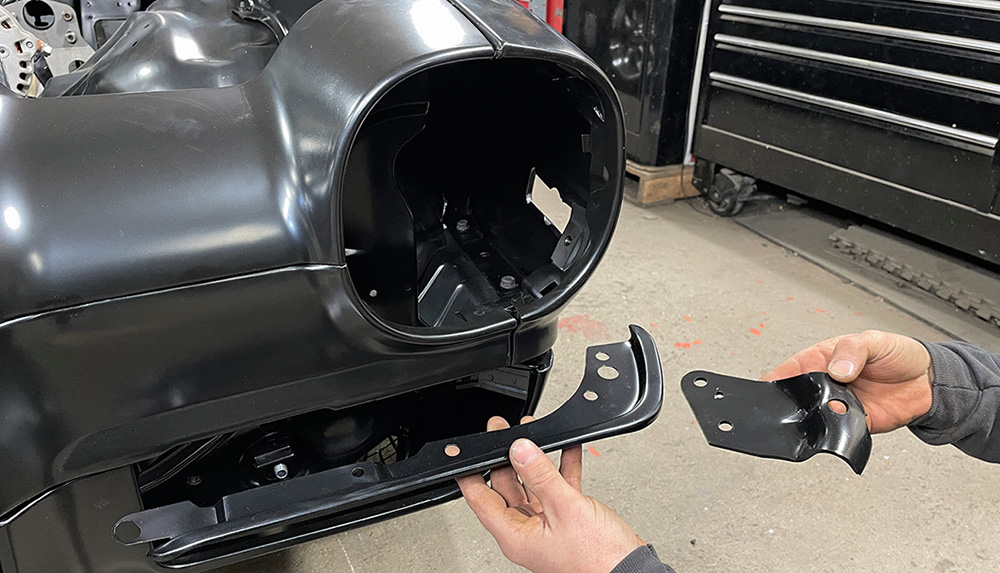
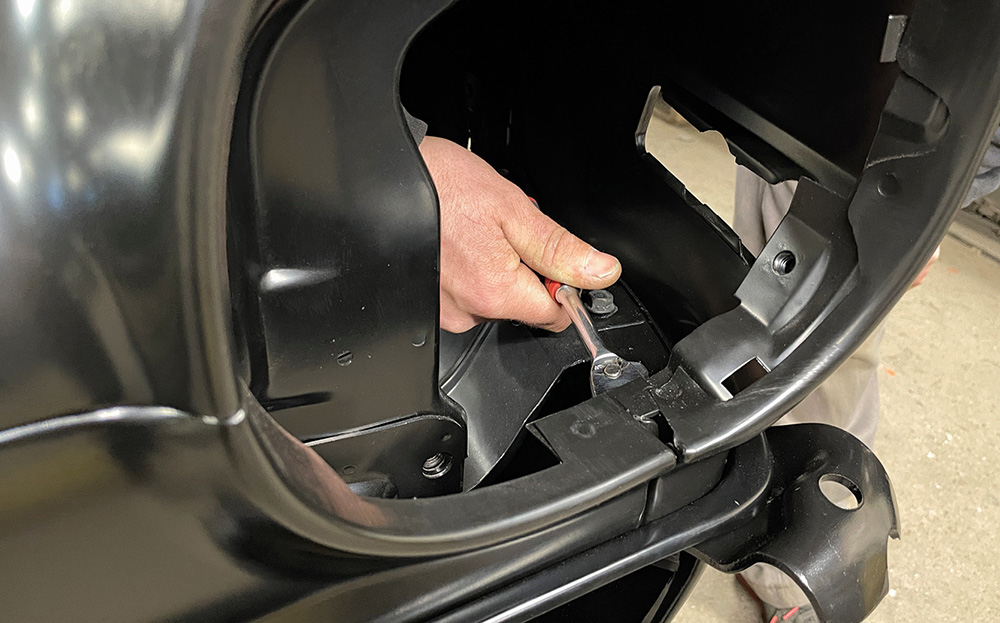
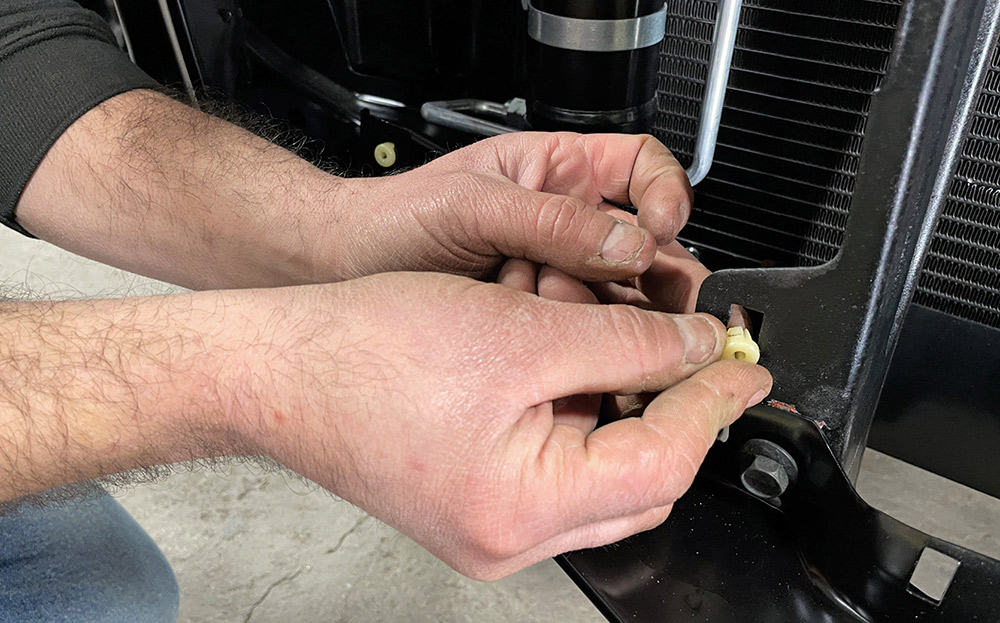
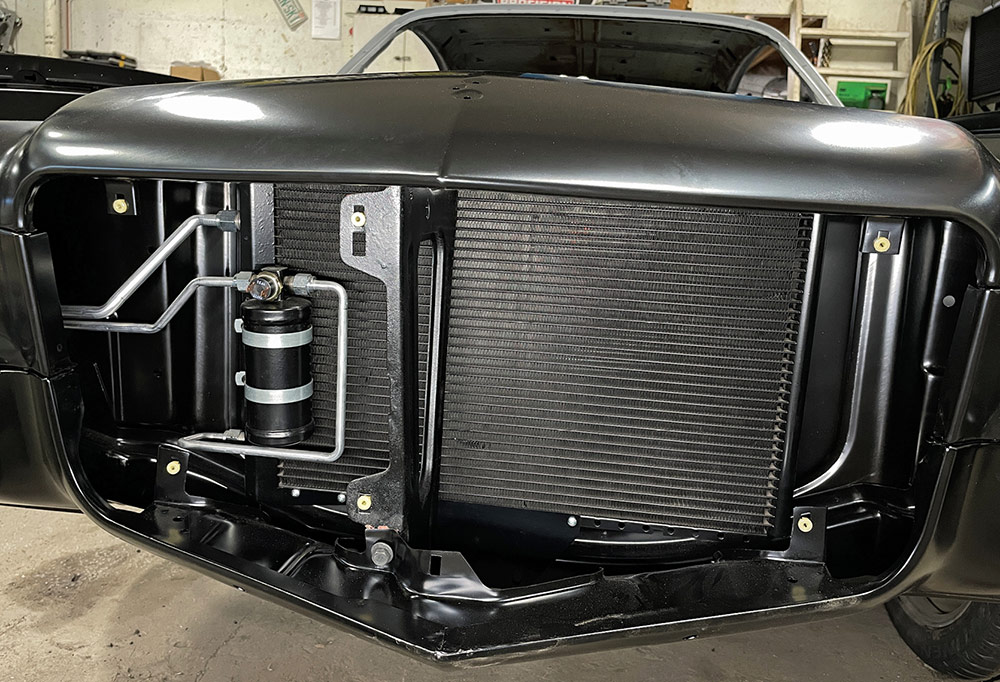
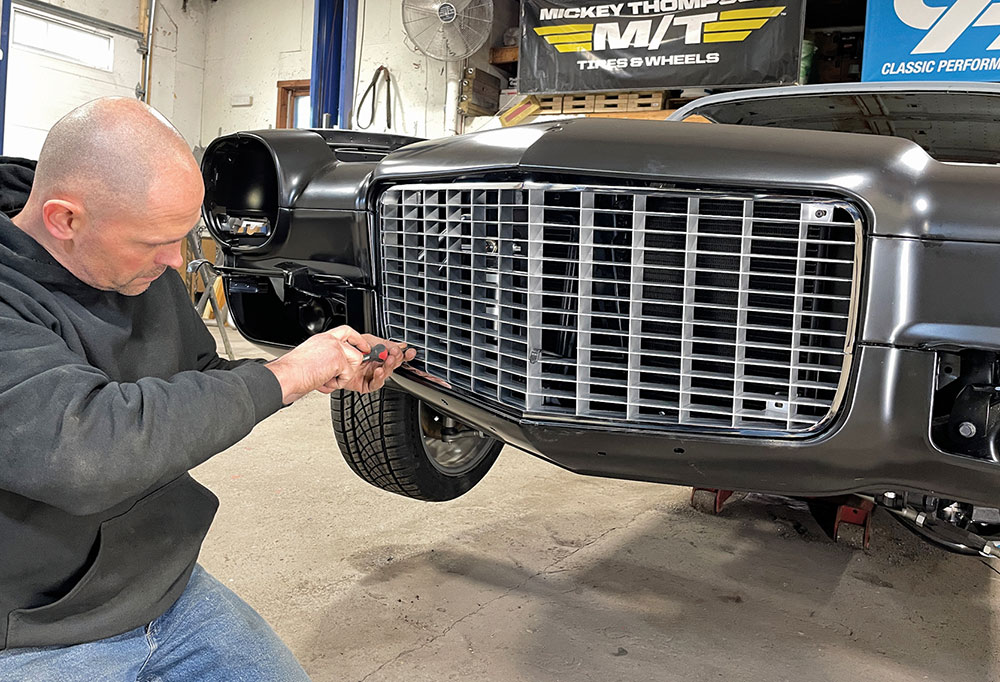
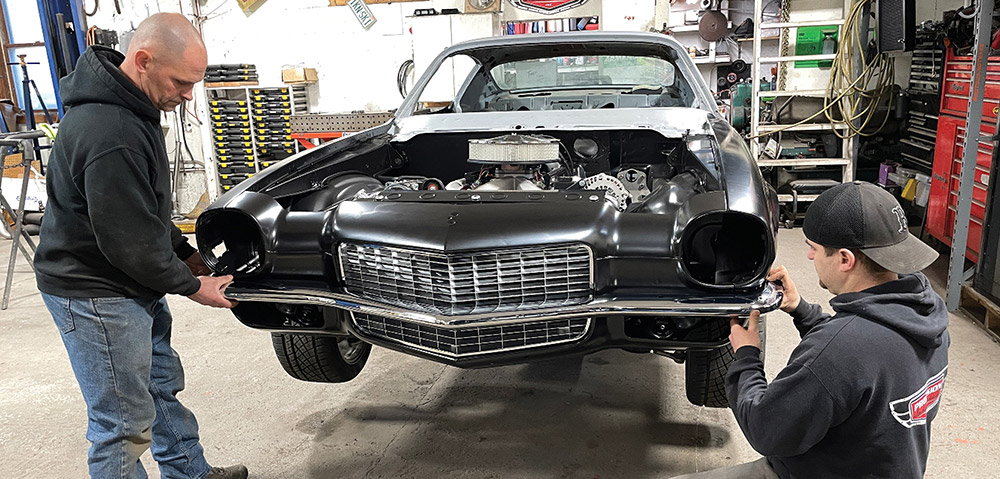
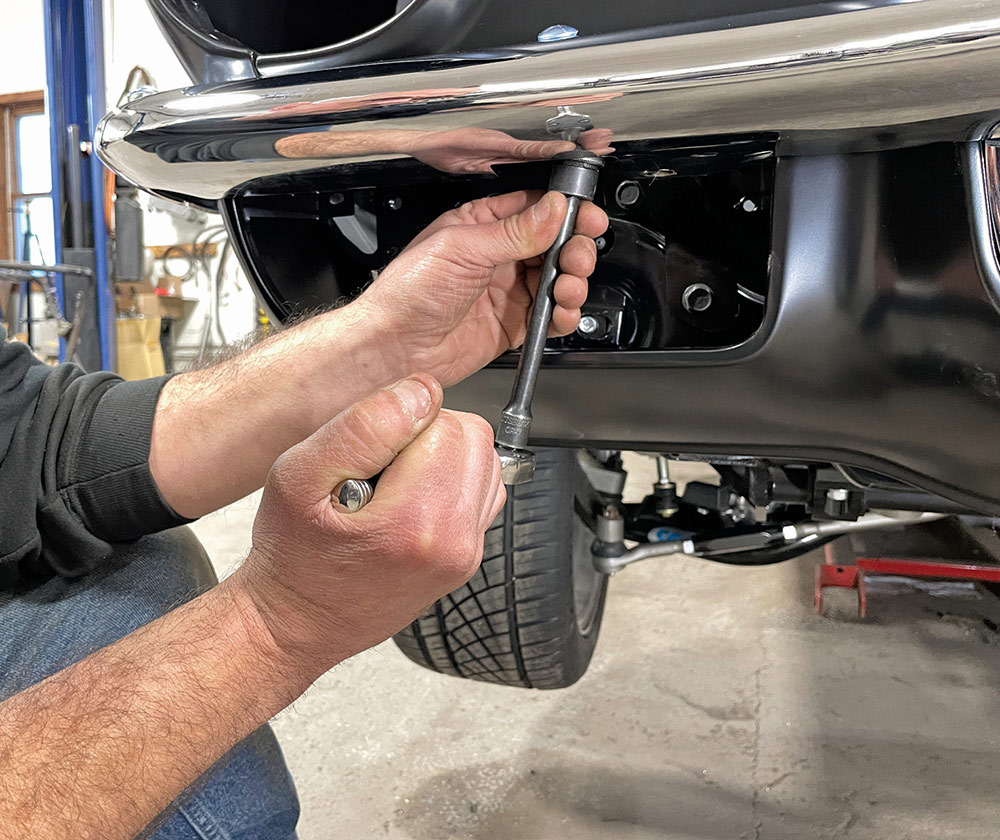
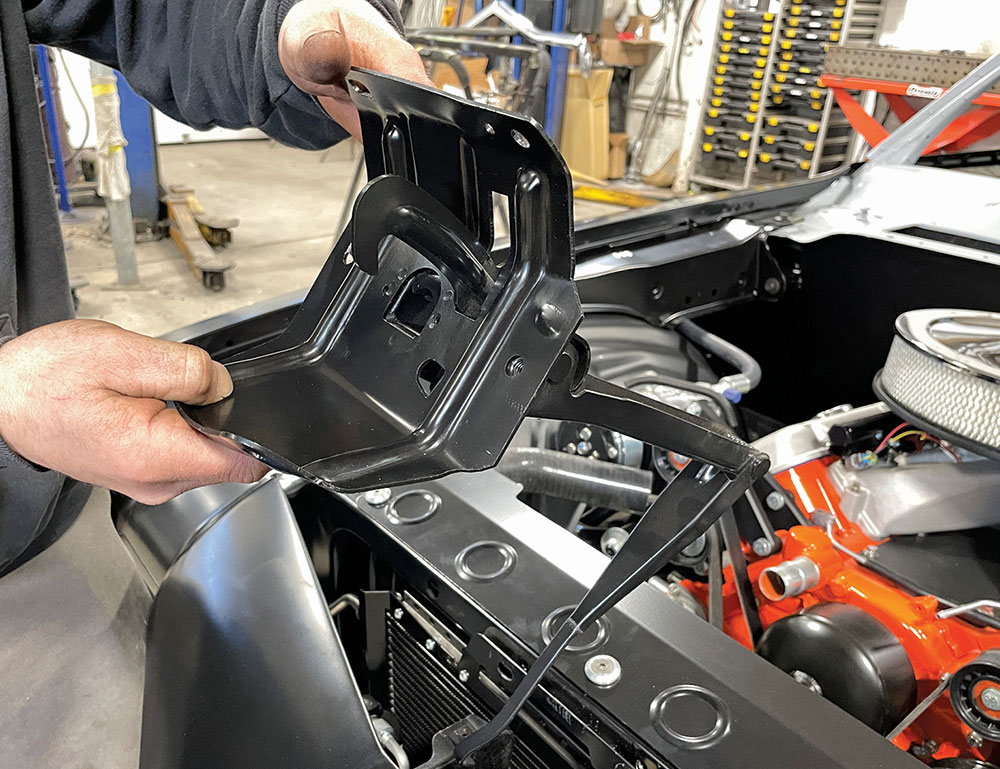
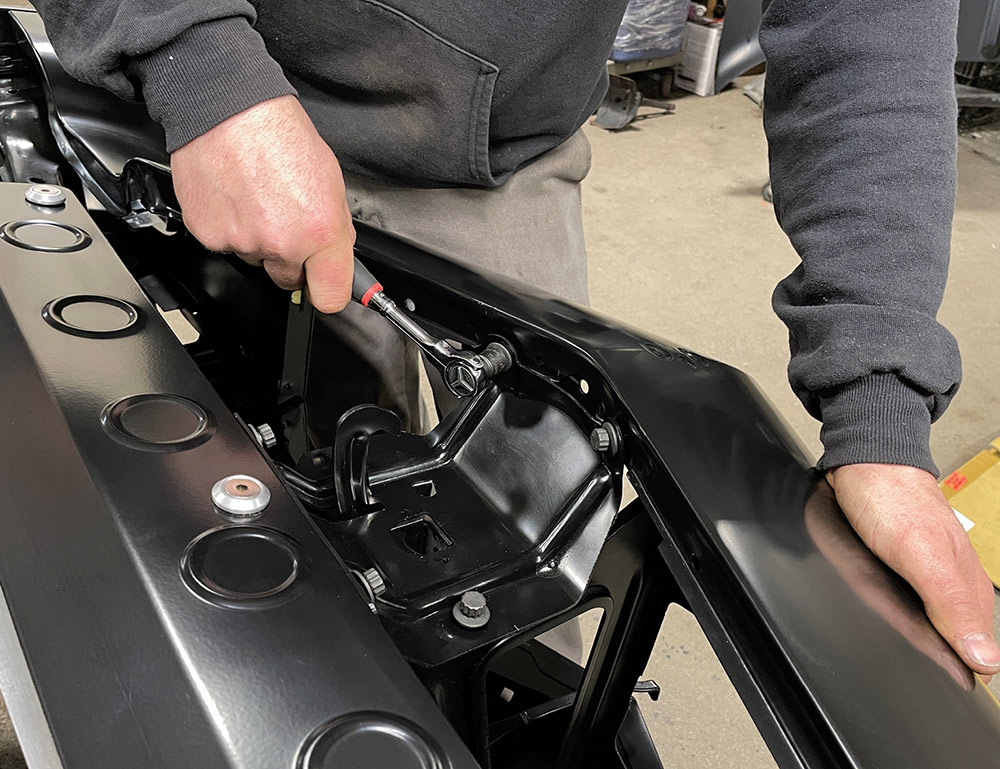
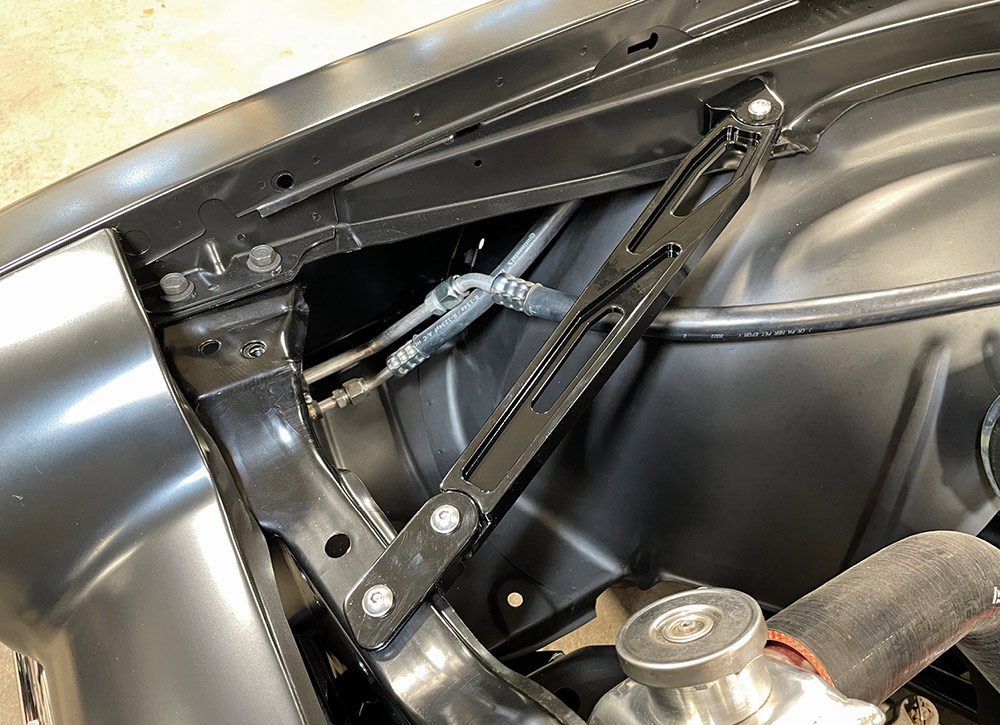
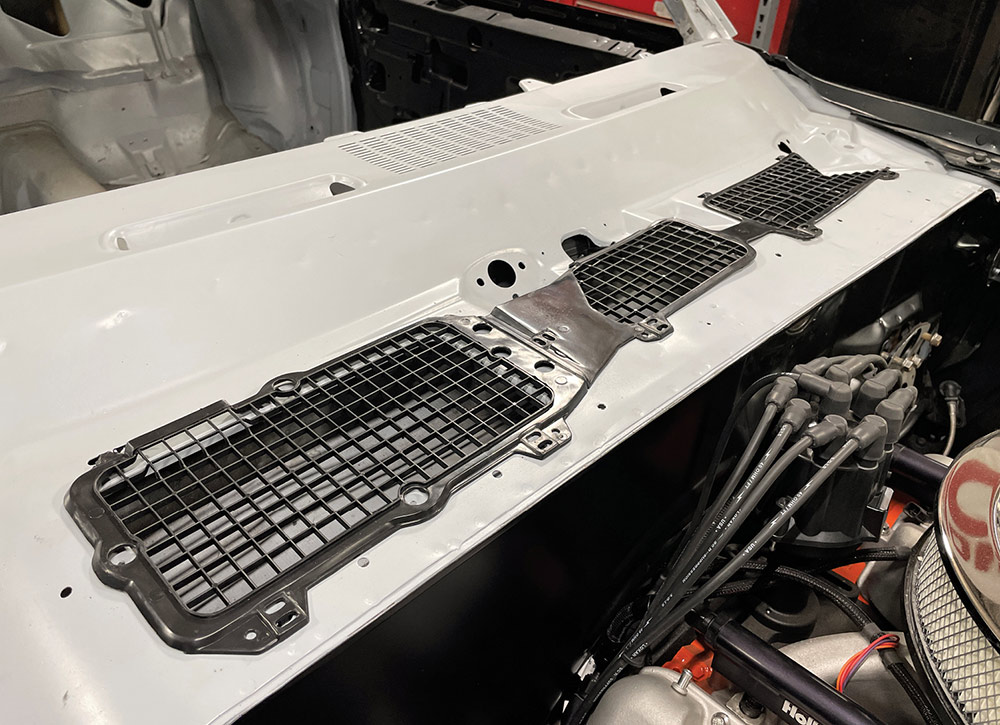
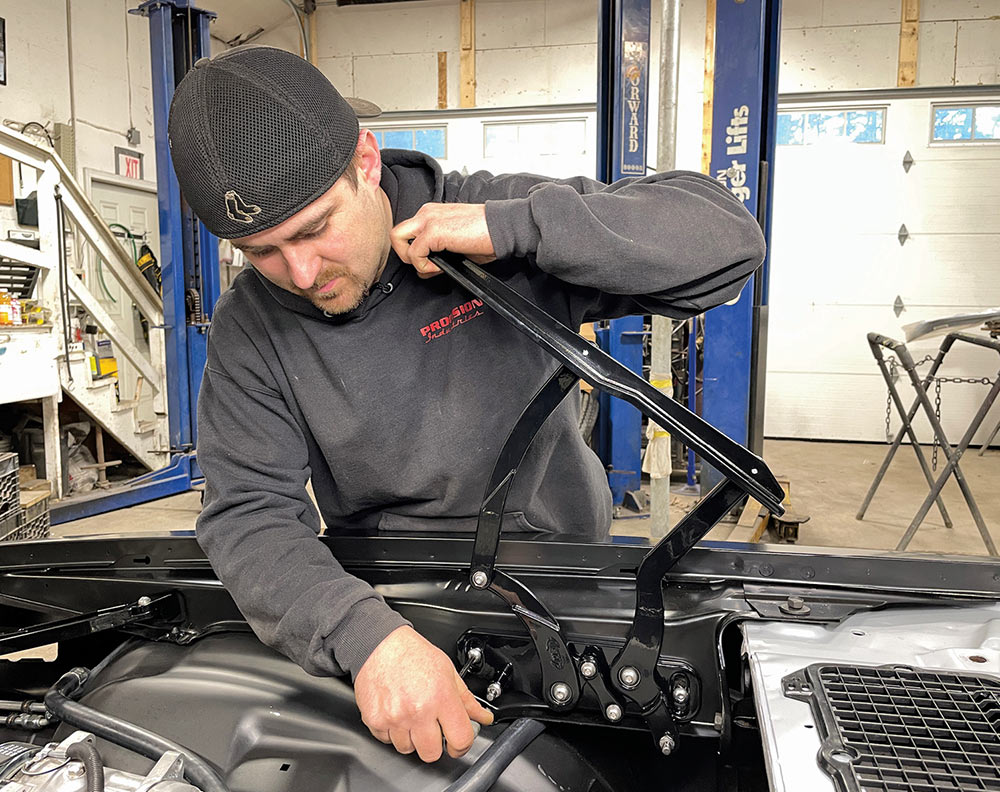
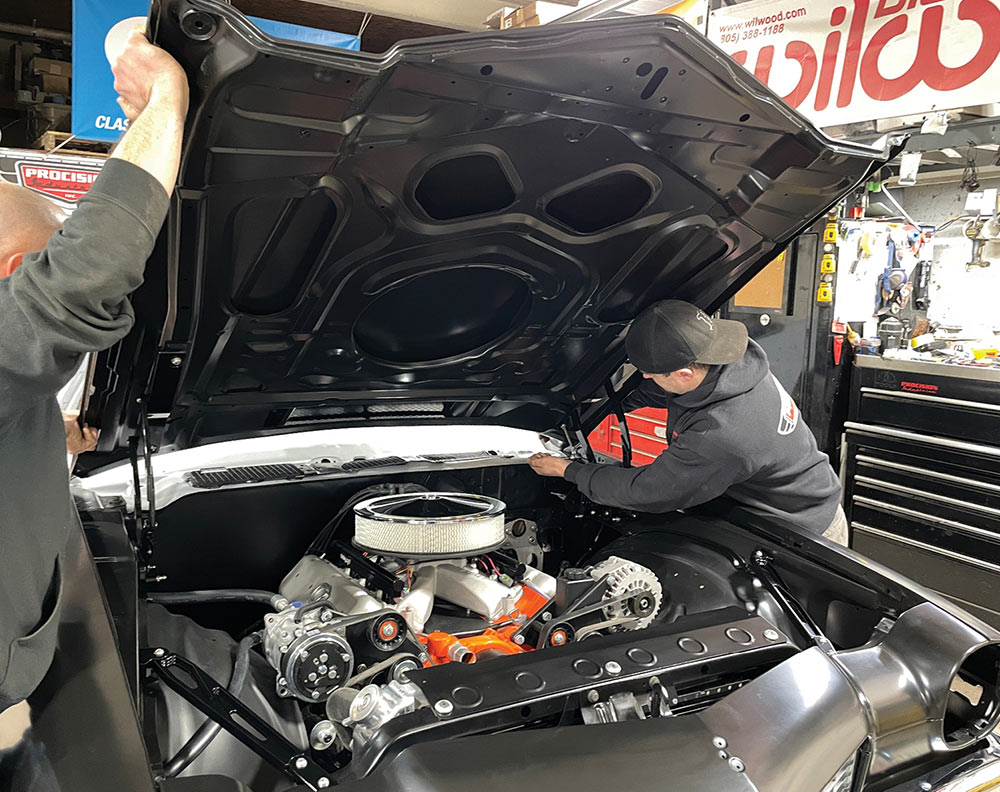

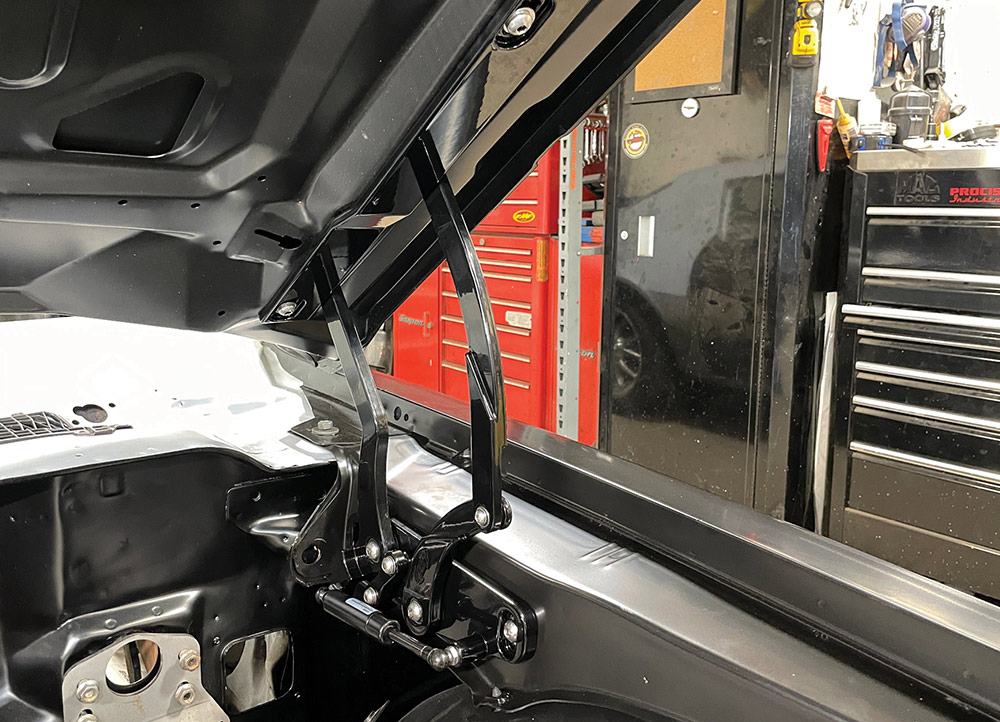
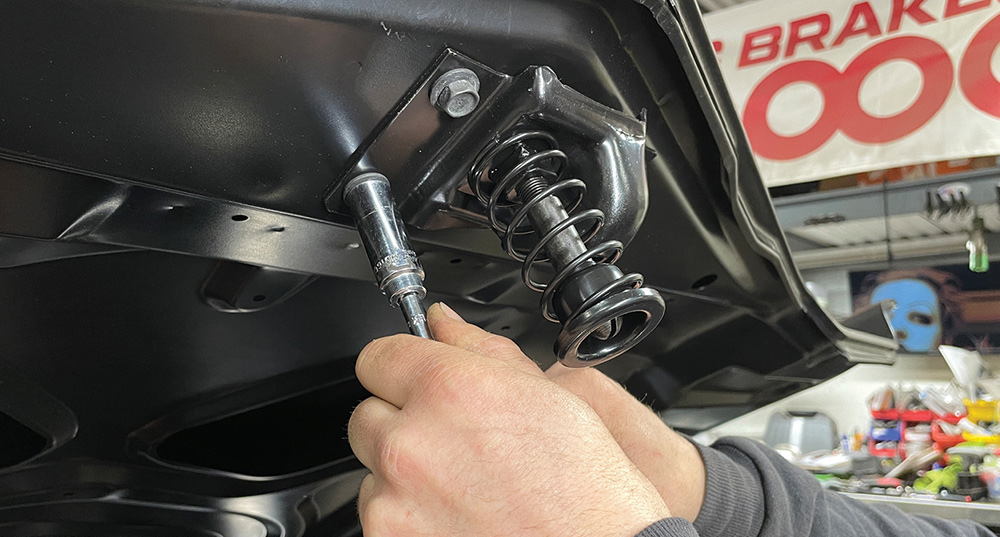
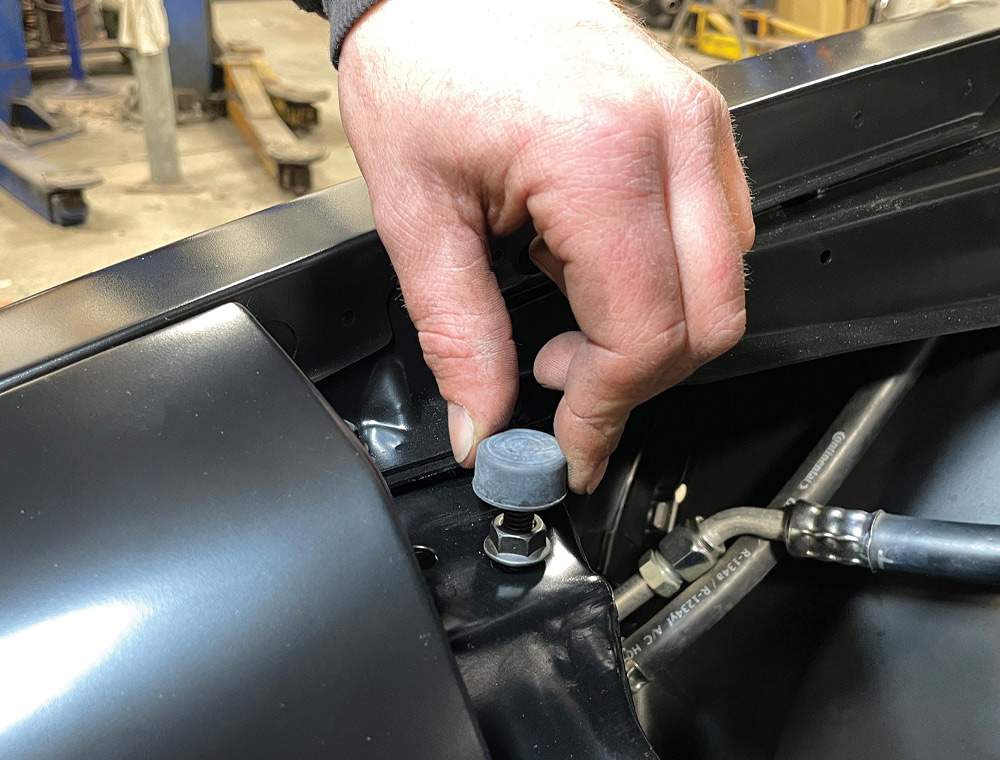

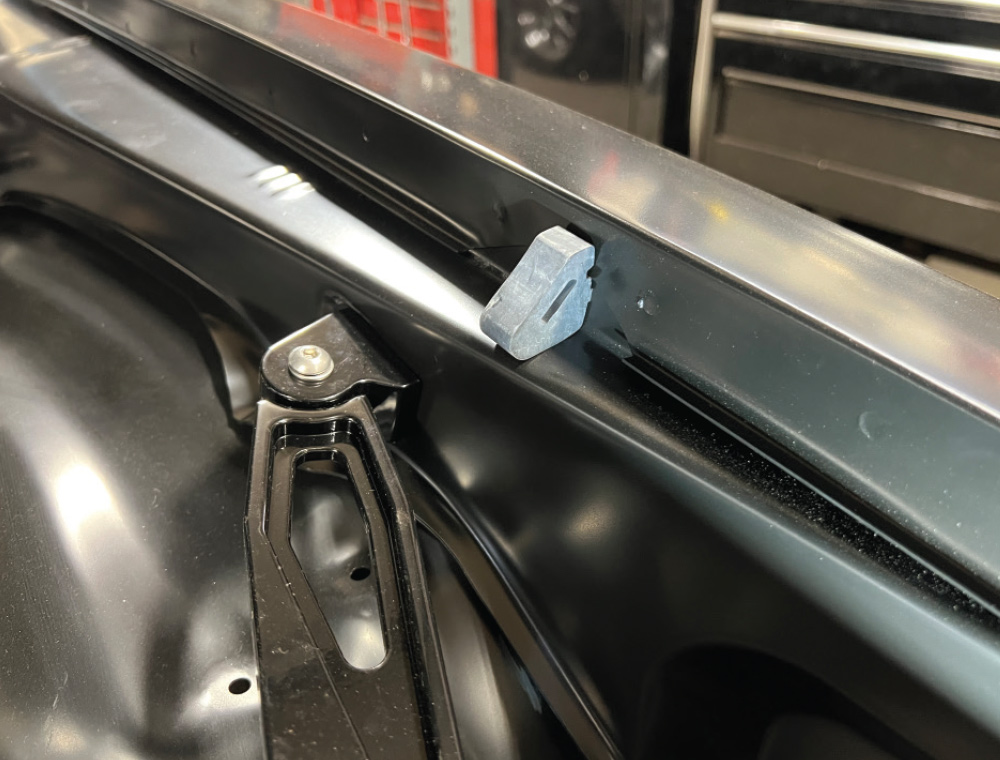
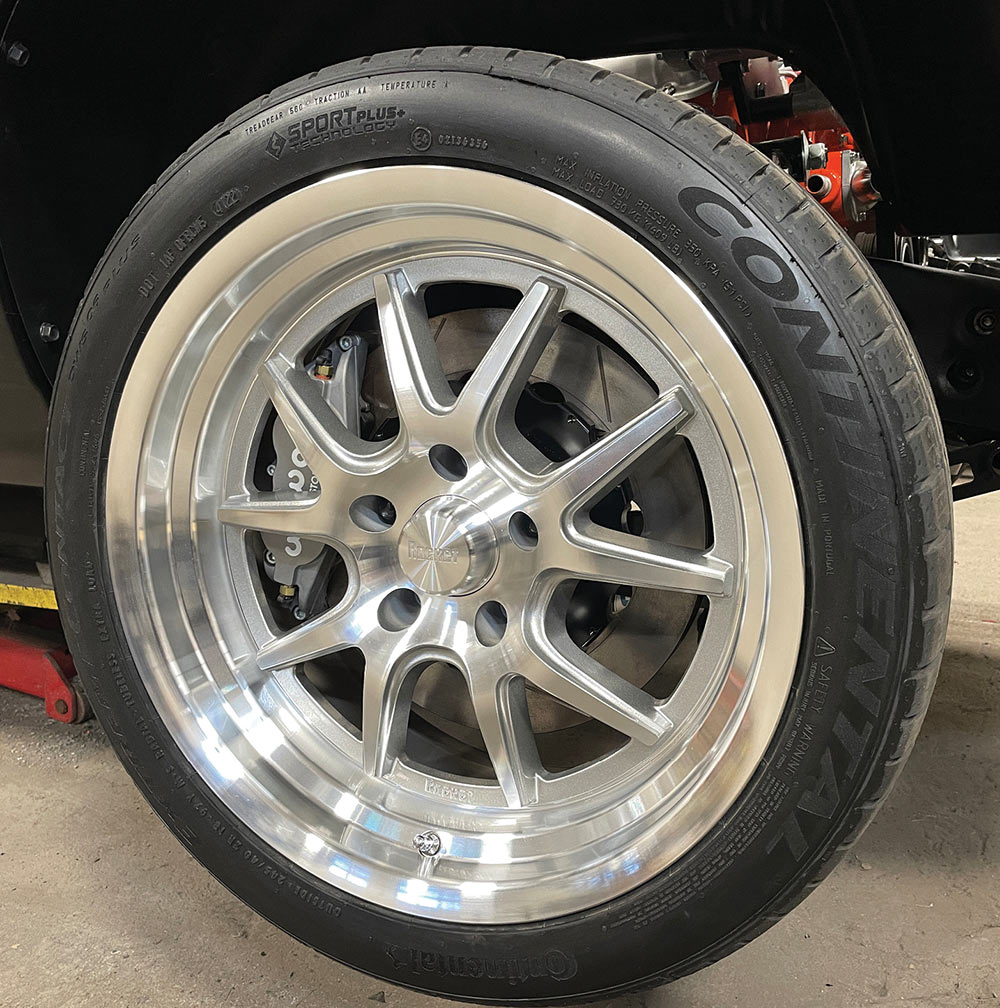
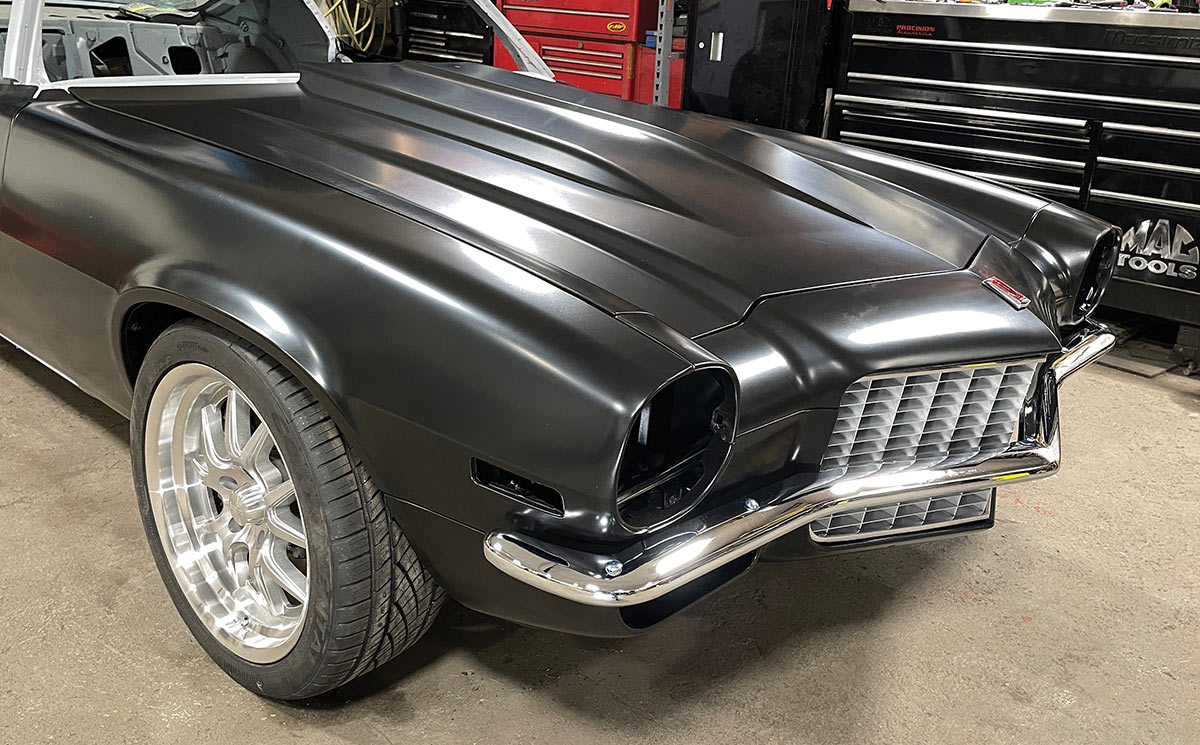
