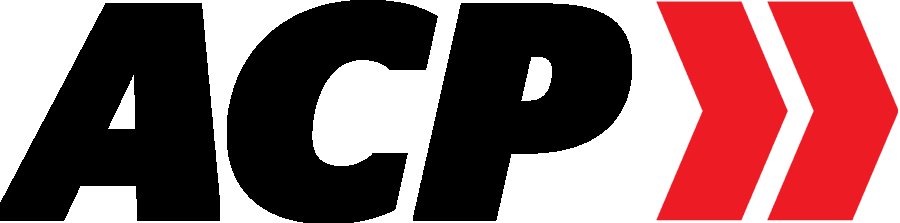
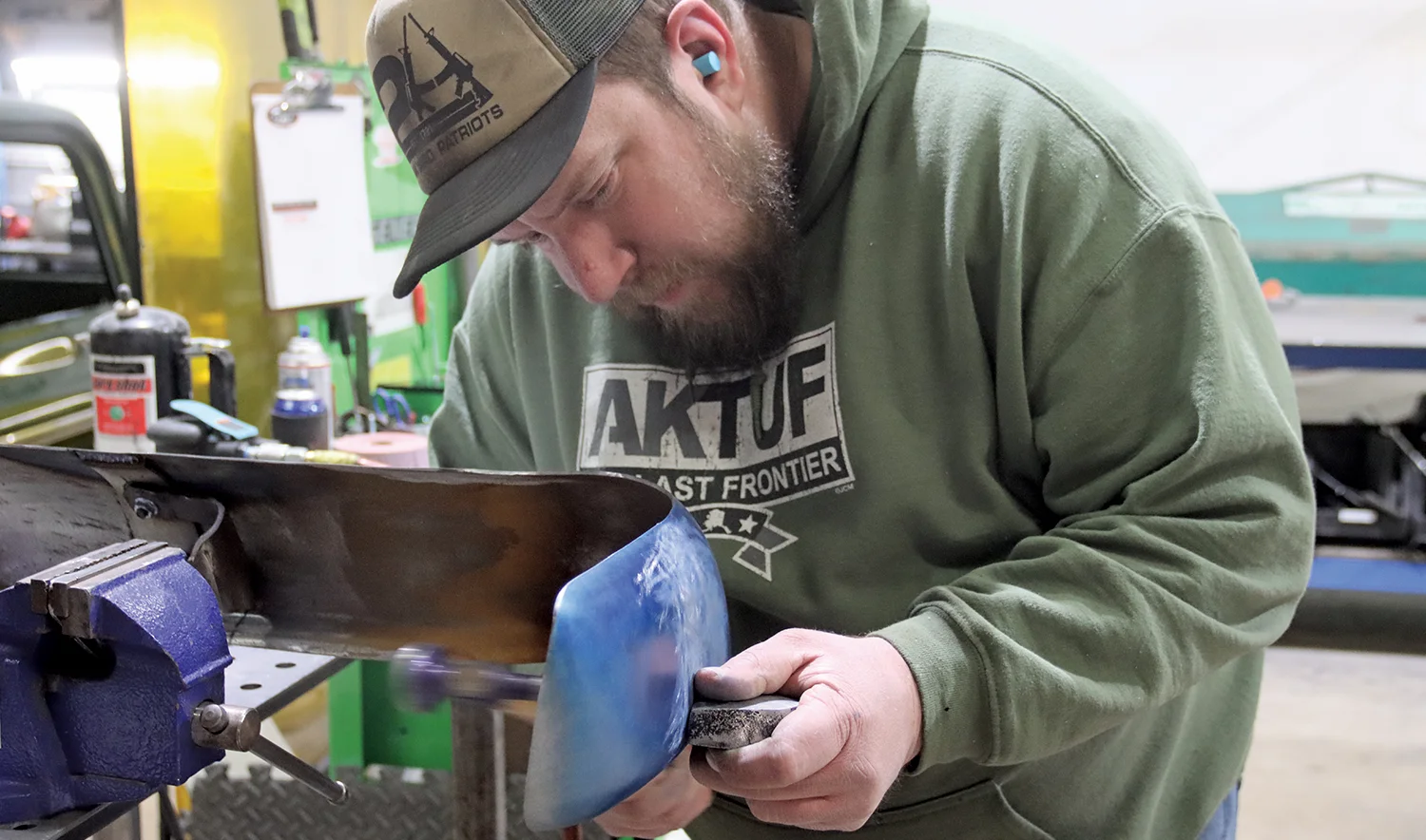

espite the fact that Chevrolet was the automotive sales leader in 1954, it was painfully obvious it was time to make some changes. Chevrolet was still using a version of the inline six-cylinder engine introduced in 1929. While it was vastly improved compared to the original design, Chevrolet’s chief competitor, Ford, had introduced an OHV V-8.
Another inescapable issue was Chevrolet’s styling had grown stale. The basic design introduced in 1949 had been repeatedly massaged, but by 1954 it was old news. In 1955 everything changed. The revolutionary small-block V-8 debuted, and some of the brand’s most iconic body styles would be produced over the next three years: the 1955, 1956, and 1957 Chevrolets, commonly referred to as Tri-Fives.
With the body mounted on an Art Morrison Enterprises chassis, MetalWorks’ Dave Williams turned his attention to making subtle but effective changes to the front and rear bumpers. The “California” front bumper was moved closer to the body with custom mounting brackets and the original boltholes were filled. The ends of the bumper that wrap around the front fenders were then cut and modified to precisely match the shape of the wheel opening. In the rear, the original three-piece bumper was smoothed by welding the seams and filling the boltholes. The bumper was moved closer to the body and the ends were recontoured to fit the quarter-panel indentations exactly.
While the changes made to both bumpers are simple in concept, in terms of the end results, they are dramatic—which is the perfect way to make a good thing better.
Over the years there have been a number of theories put forth to explain why GM went to the trouble of making two different styles for the same cars. Some said it was due to a difference in suppliers, others said it was because the multi-piece bumpers were cheaper to ship, while there were those who believed it had to do with rust forming where the sections bolted together. To find out the real reason we turned to an acknowledged expert on the subject, Christopher Sondles, founder and president of the American Tri-Five Association.
According to Sondles the reason for one-piece bumpers was simple enough—it was a state requirement. California mandated that front bumpers had to be made in one piece; multiple-piece construction wasn’t allowed. When you think about it, the “California” bumper requirement could be the only known example of a state law that automotive enthusiasts are thankful for.


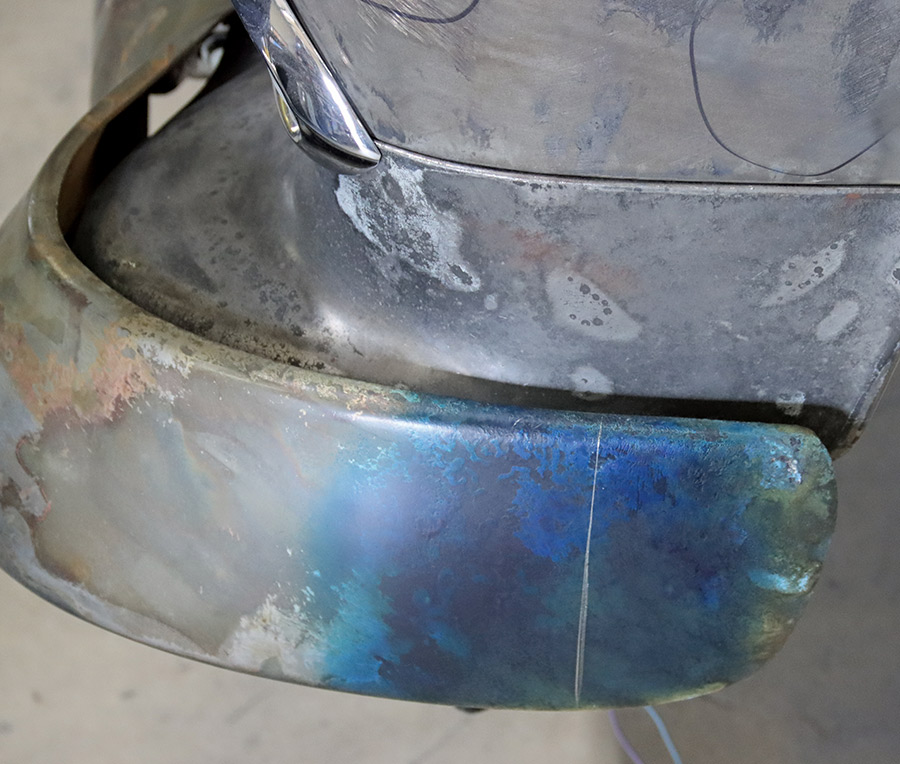




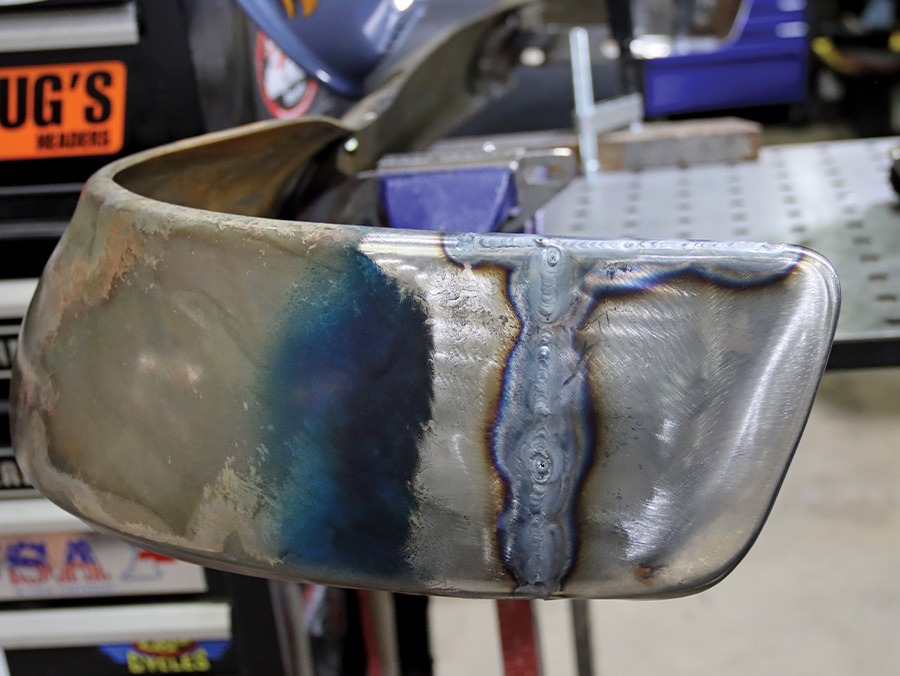




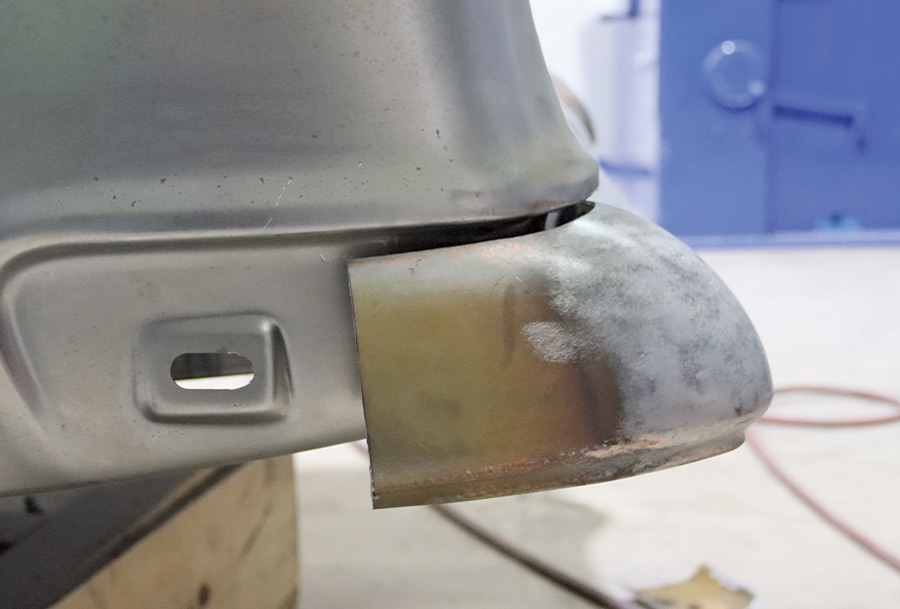


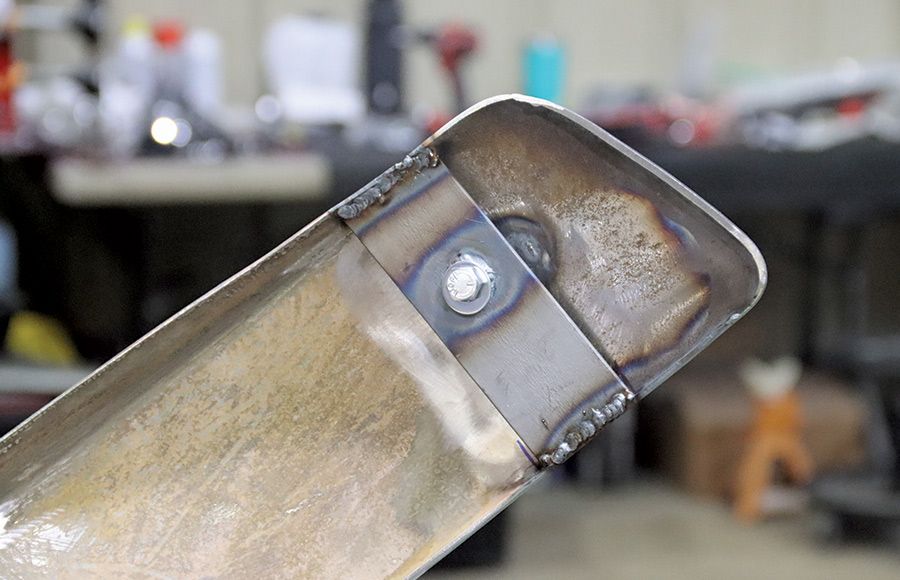


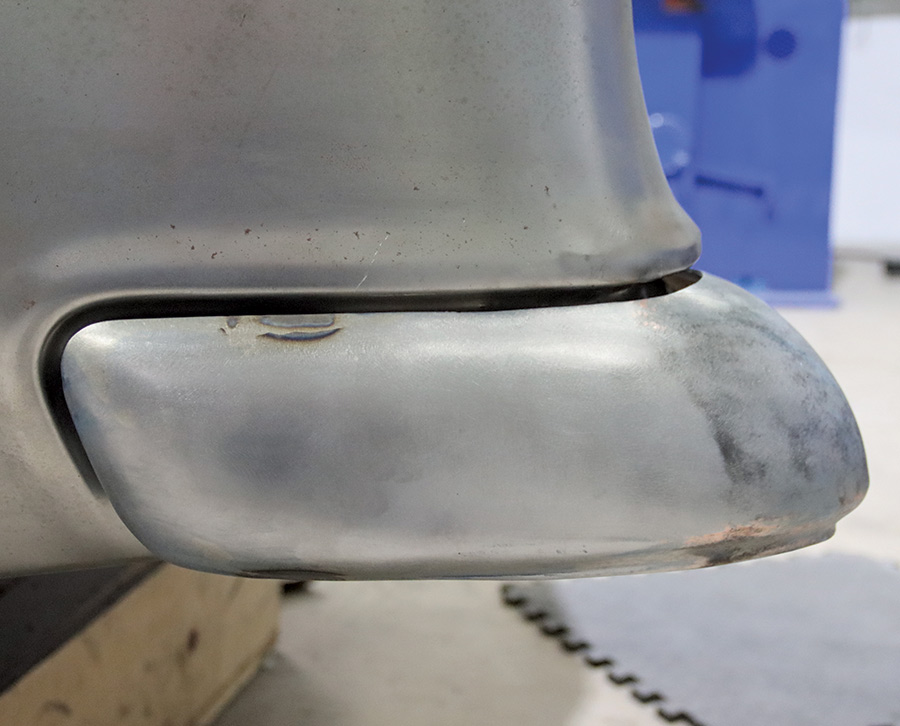
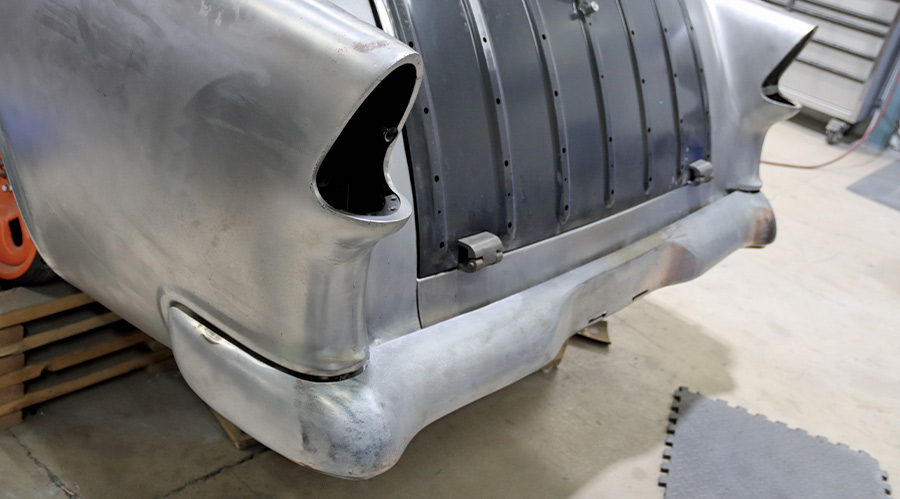

