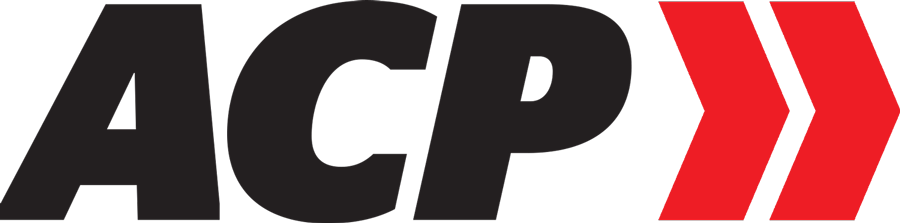
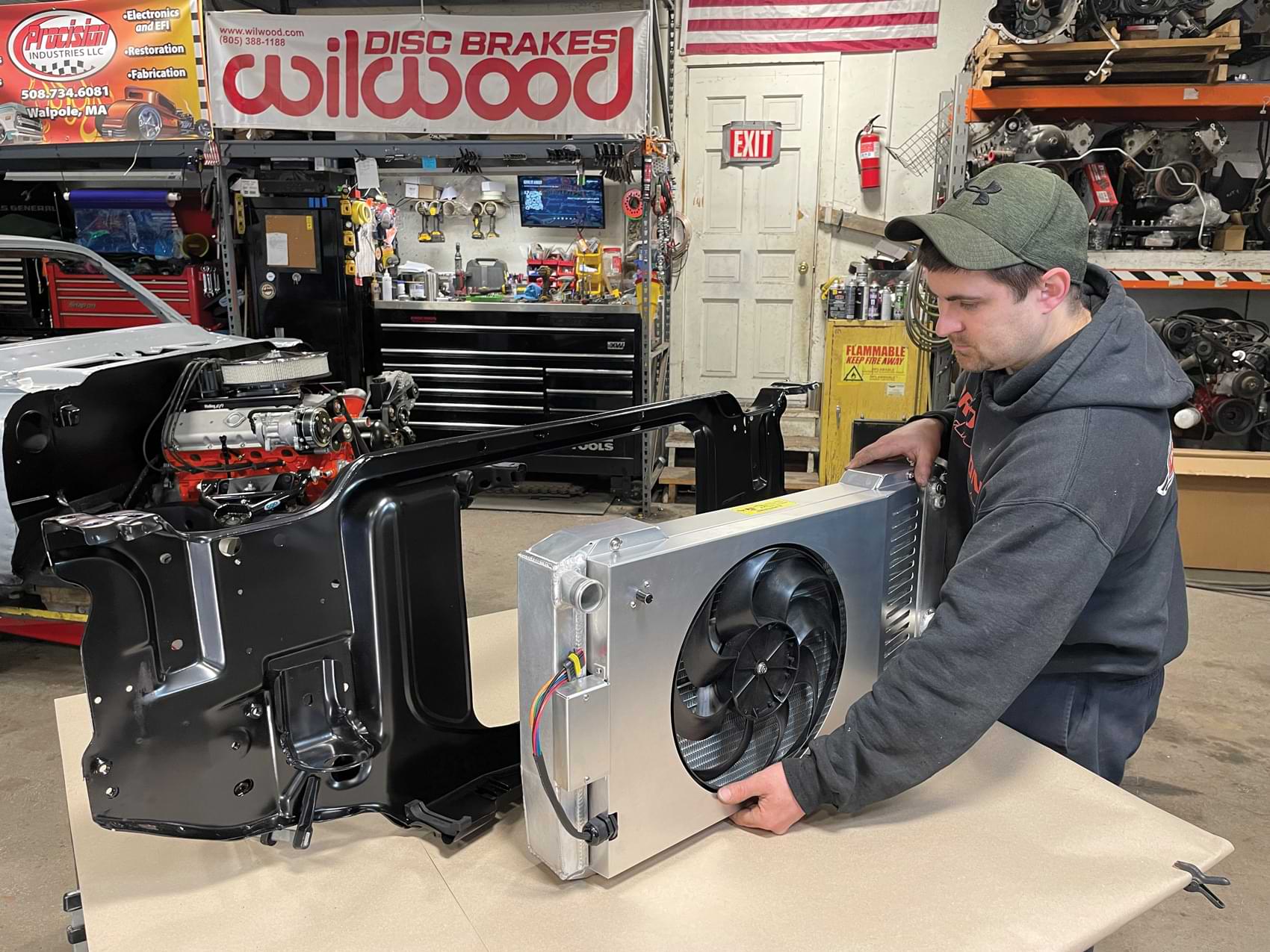

here’s nothing more revered in the performance world than adding horsepower to your ride, regardless of whether it’s naturally aspirated, supercharged, or turbocharged, however you’d better be able to chill the beast to make its time on the street a long-lasting experience. There’s nothing worse than having to constantly watch a temperature gauge with fears of overheating due to a tired or poorly set up cooling system. Add in the needs of an upgraded LS conversion and you’d better do your homework to incorporate a properly designed setup that can handle the demands of everyday life on the road.
On a recent visit to Procision Industries in Taunton, Massachusetts, we met with shop owner Pat O’Brien whose newly installed high-performance 5.3L LC9 in his personal ’71 Camaro project gave All Chevy Performance a perfect opportunity to follow along as he formulated a modern cooling system to take care of business. Seeing that he was starting bare from the firewall forward, it was time to select a proper foundation to support the new cooling system, beginning with fresh reproduction factory parts from Auto Metal Direct (AMD). Their radiator core support struck from heavy-gauge steel (supplied by X-Parts) combined with radiator support insulator pads, support bushing mount kit, radiator core to frame support brackets, and all related installation hardware made preparing the area a snap.
To handle the LS conversion’s specific cooling needs, a call was made to PROFORM for one of their Slim-Fit radiator systems packed with exclusive features. Their design showcases years of development in creating the industry’s first all-in-one integrated radiator system where the combined core/shroud/fan thickness is only 4 inches in depth (up to 40 percent thinner). Offered in direct-fit, LS conversion, and universal applications for up to a 600hp mill, it’s easy to see they’ve got your high-performance Chevy covered.
Here, we’ve spotlighted their prototype for the second-gen Camaro LS conversion system, which should be available sometime soon. As with their entire Slim-Fit line, it’s a complete unit straight out of the box, packing an impressive set of specs, including an all-aluminum construction, hybrid extruded tube core technology with proprietary engineered louvers, precision TIG-welded tanks, and an innovative core-mounted fan motor. Systems incorporate everything needed to complete the installation, including Slant-Edge radiator cap, adjustable thread-in thermostat, and weather-tight-equipped wiring harness.
It was also perfect timing to address all underhood plumbing to the air conditioning system utilizing Vintage Air’s Gen IV SureFit Condenser Kit with Dryer as well as their Beadlock 14-Fitting Extended Length Refrigerant Hose Kit (without drier), which provided everything needed to complete the system through the firewall. To link it all together, a set of AMD inner fender braces were installed to the firewall base followed by a pair of AMD (produced by X-Parts) reproduction inner fenders stamped from heavy-gauge steel.
Follow along as the updates are installed to this second-gen Camaro.
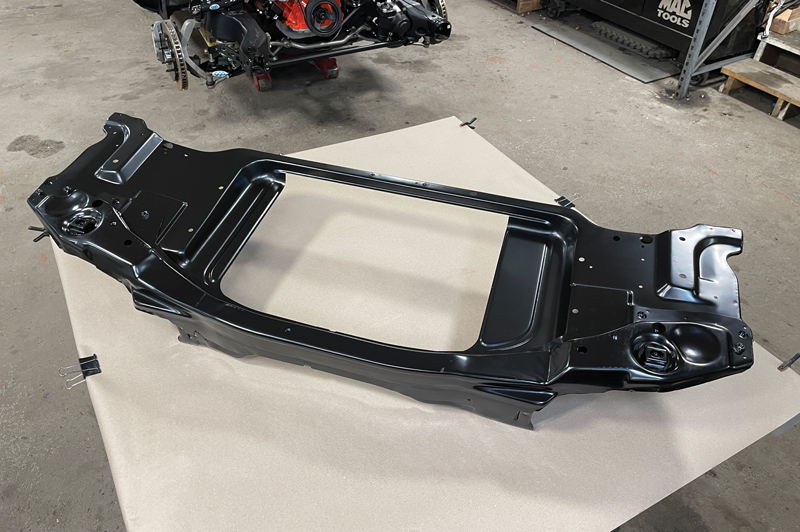
1. To properly anchor the cooling system, a call was placed to Auto Metal Direct (AMD) for a fresh factory reproduction radiator core support stamped from heavy-gauge steel produced by X-Parts.
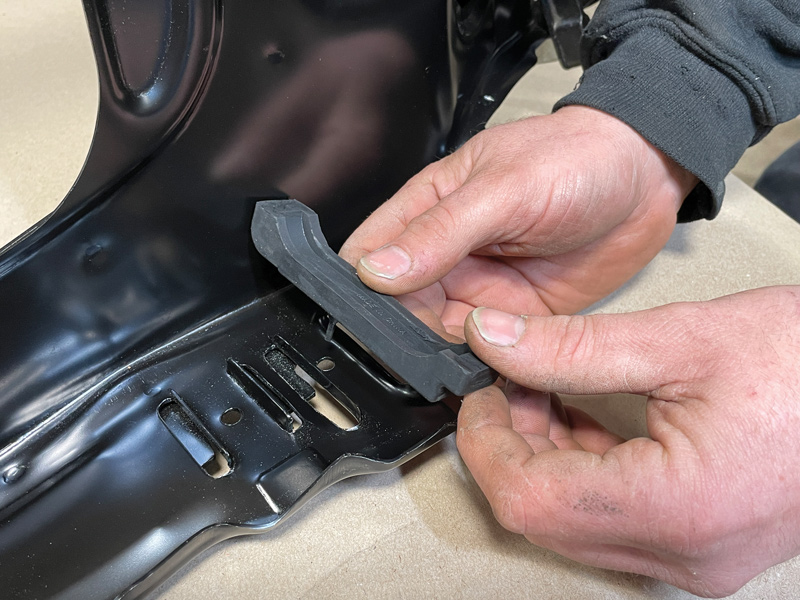
2. Getting started, Pat O’Brien of Procision Industries installed a new set of AMD radiator retainer insulator pads to the base of the core support. These will properly brace the radiator once in place, eliminating vibration.
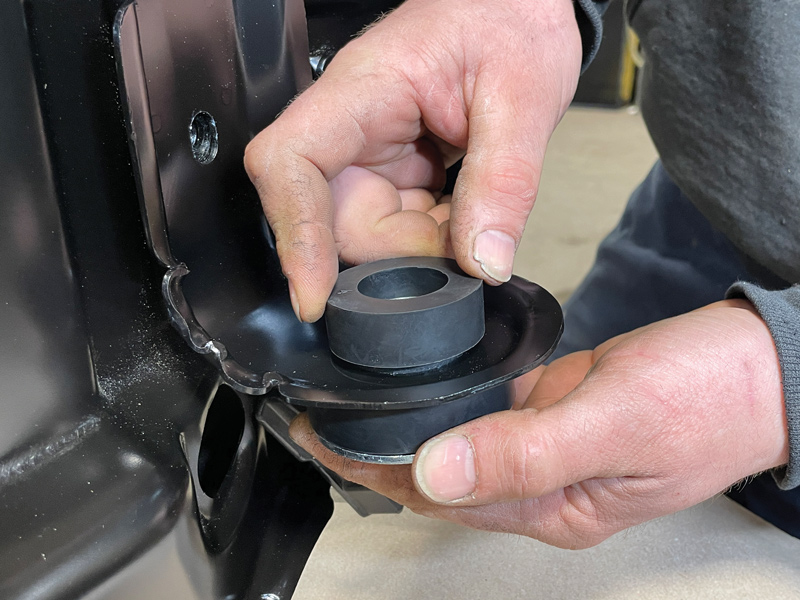
3. Next, a radiator support bushing mount kit from AMD was used; first place the bushings at the bottom of the core support and follow with the rubber cushions added to the top.
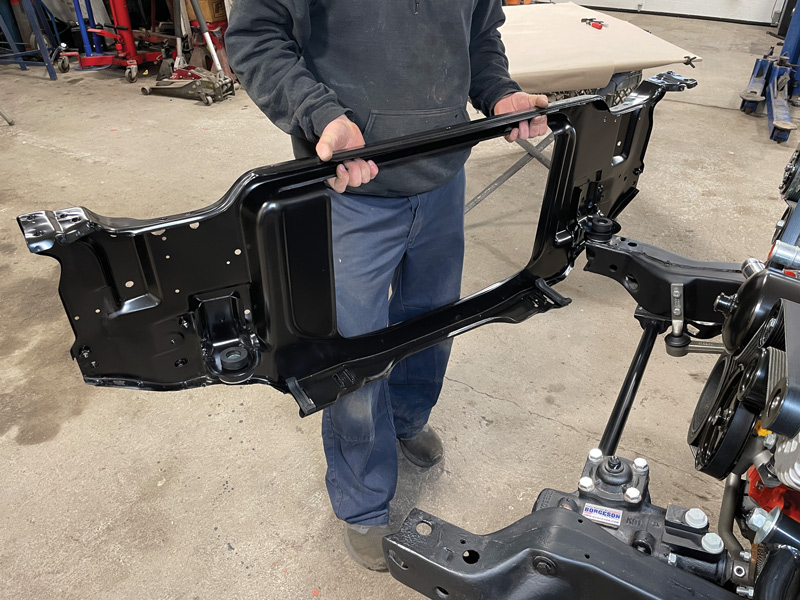
4. The core support was then set in place atop the framerails to prepare it for installation.
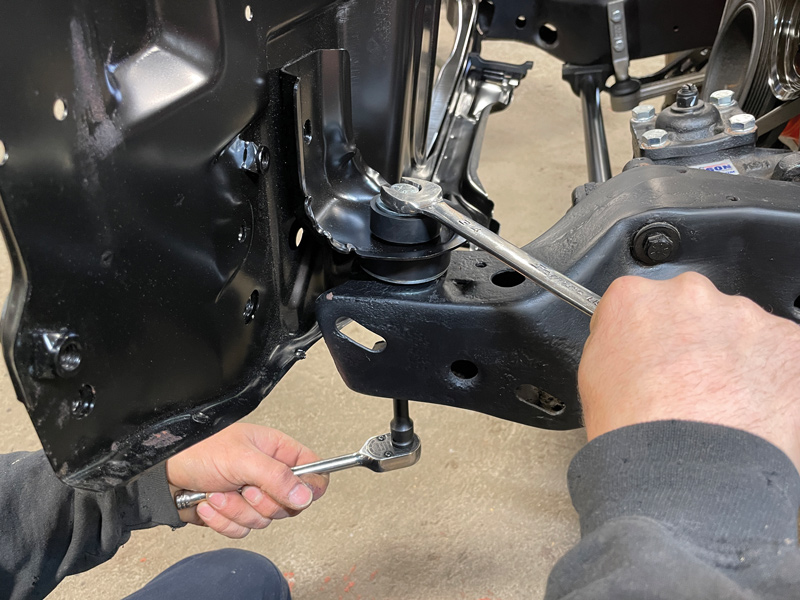
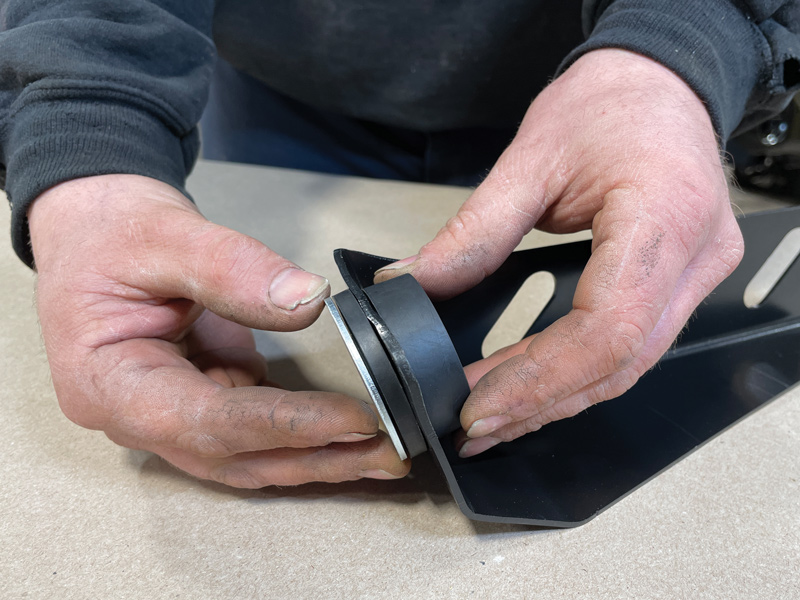
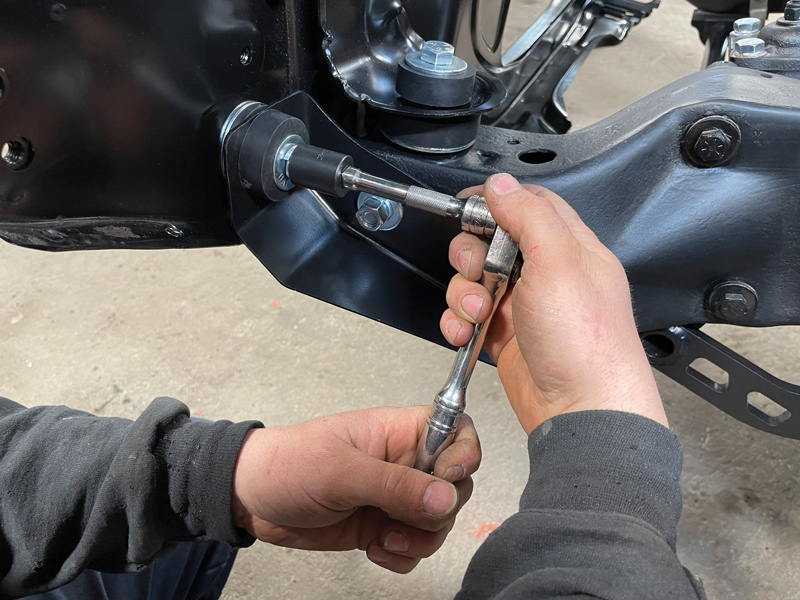
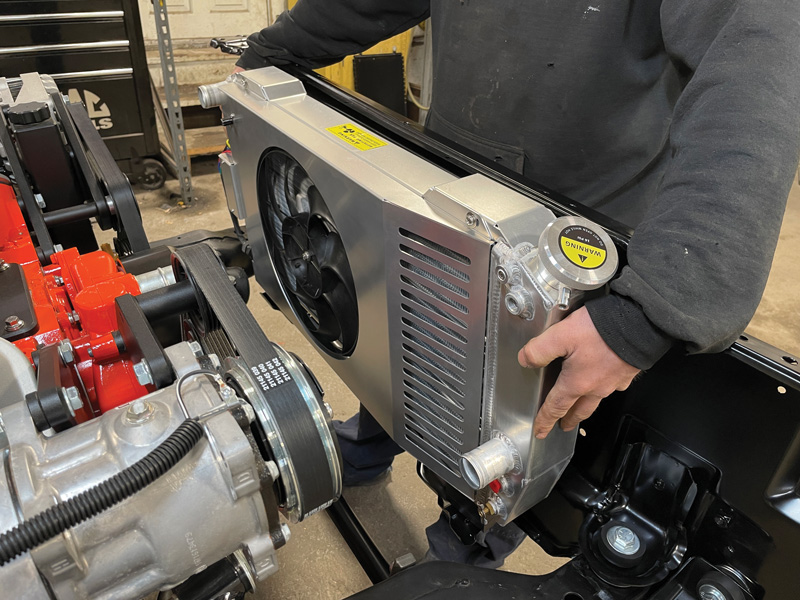
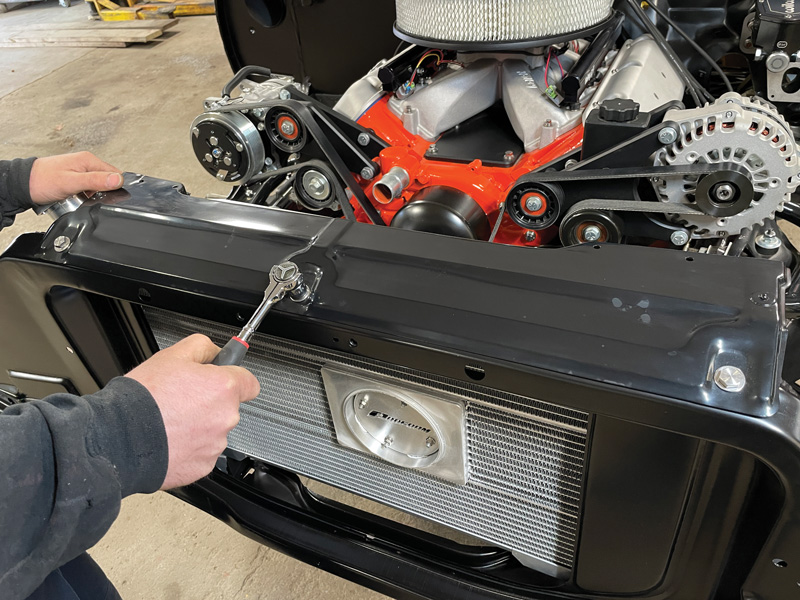
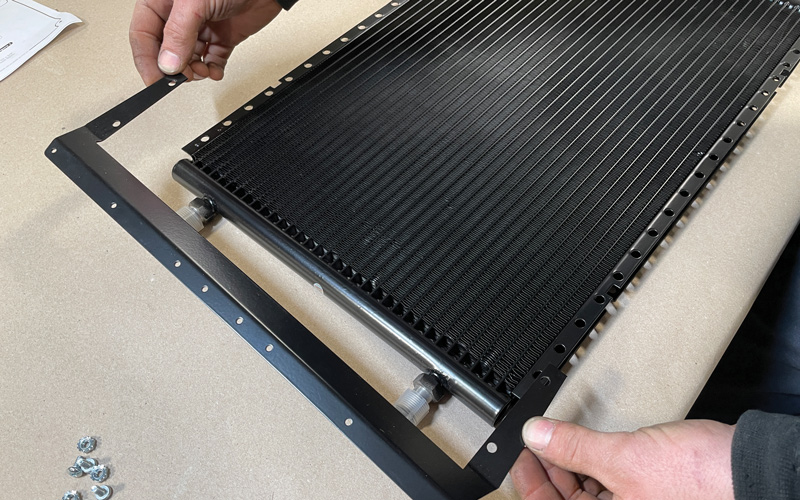
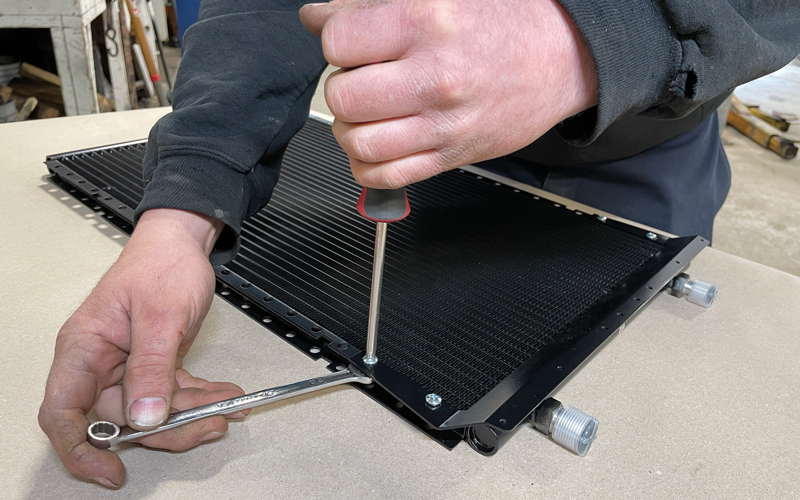
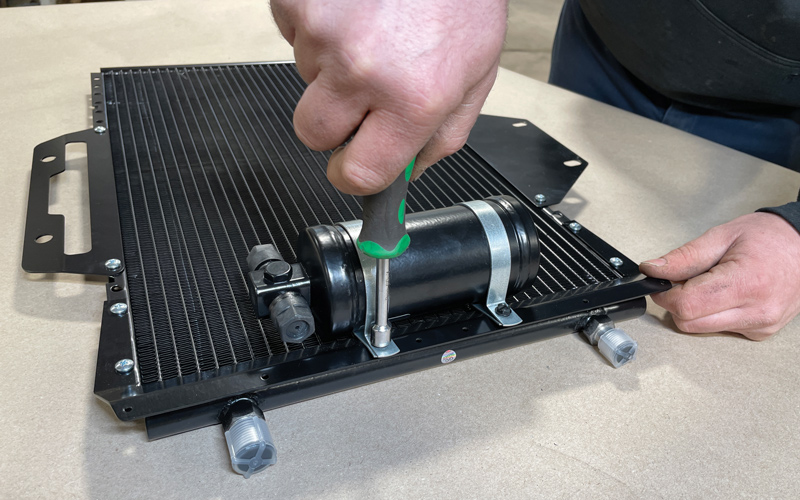
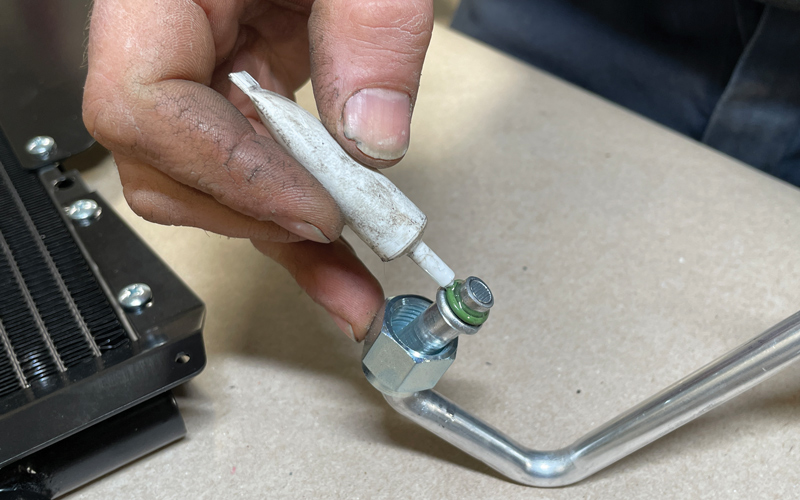
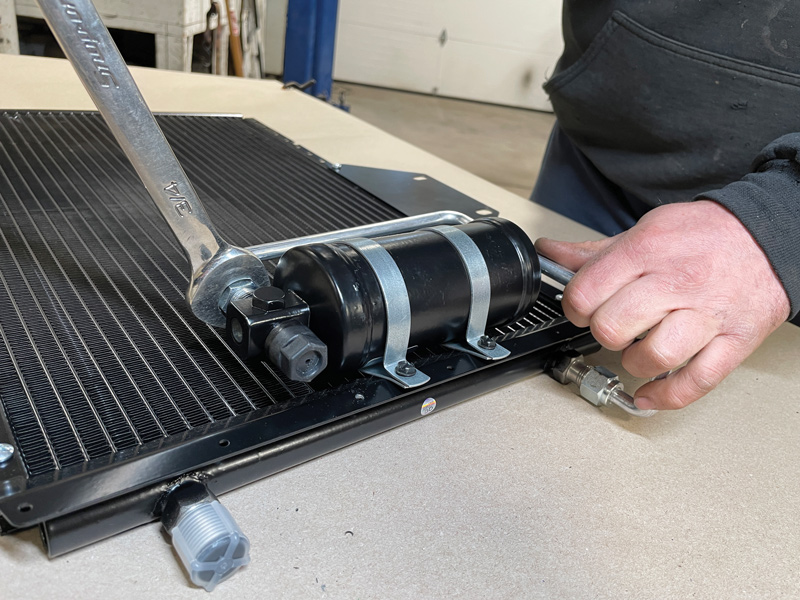
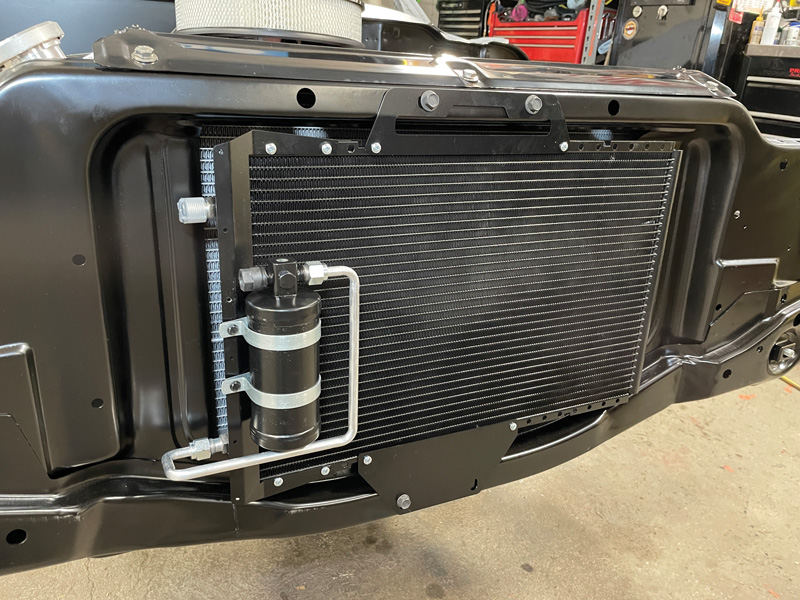
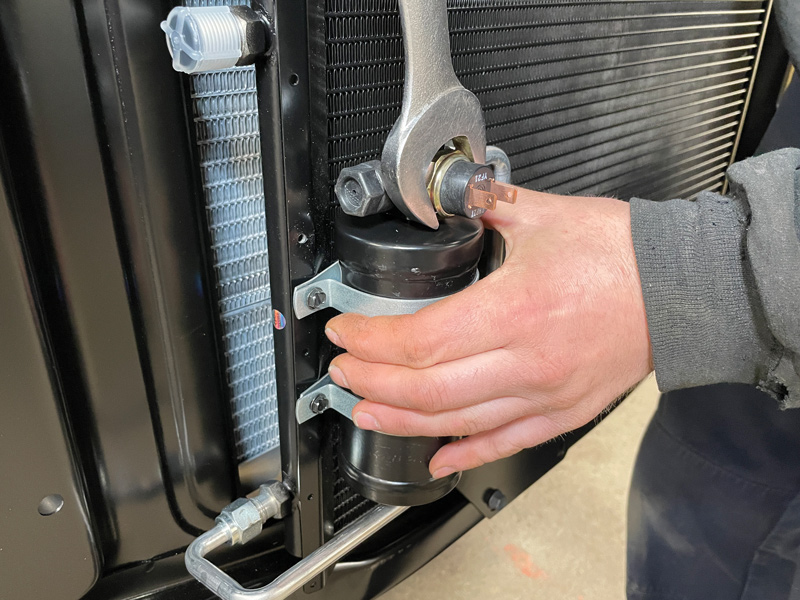
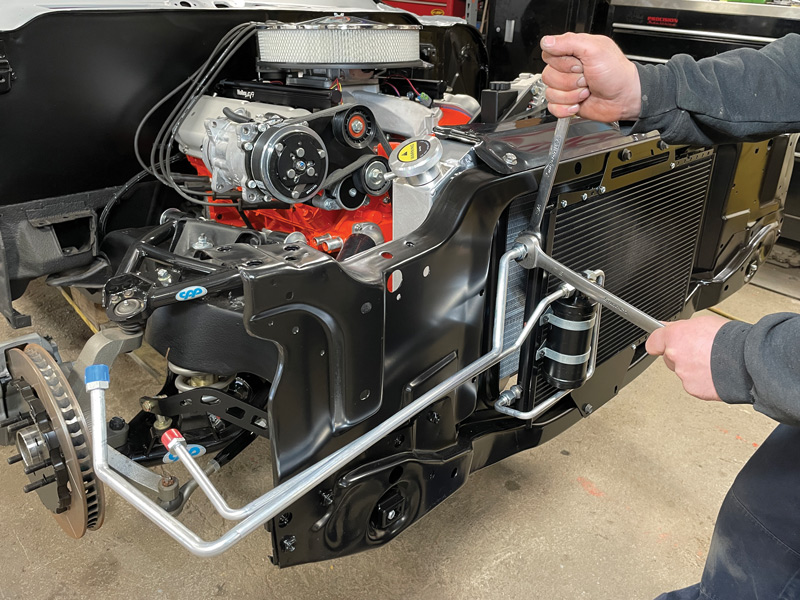
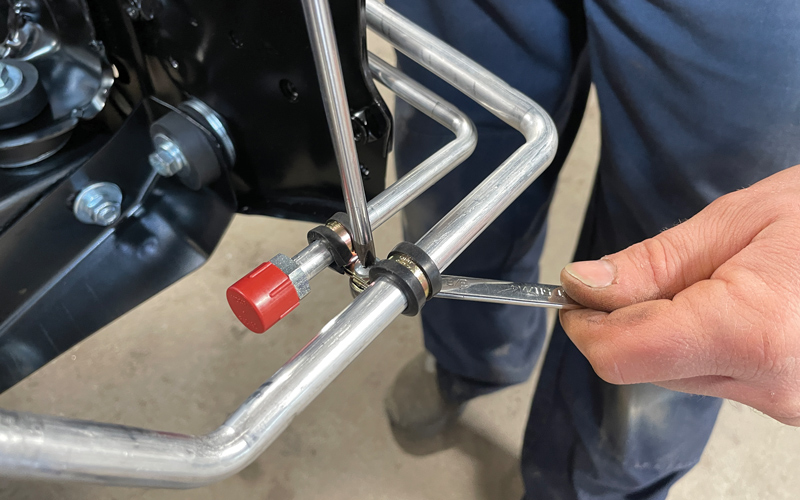
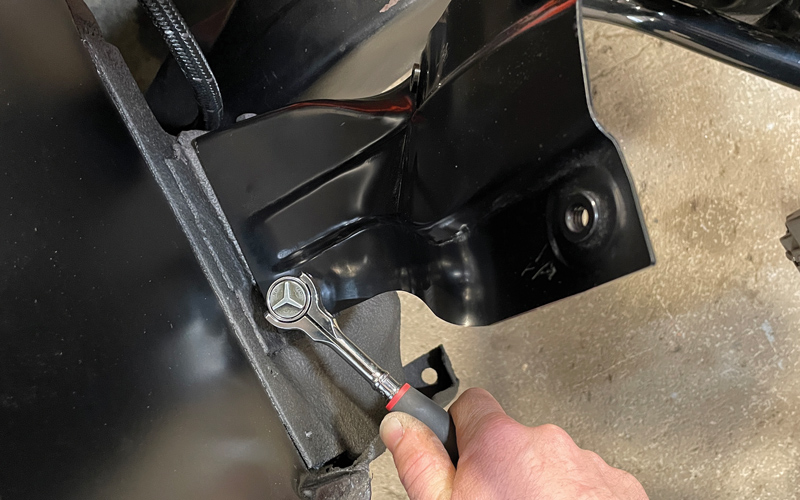
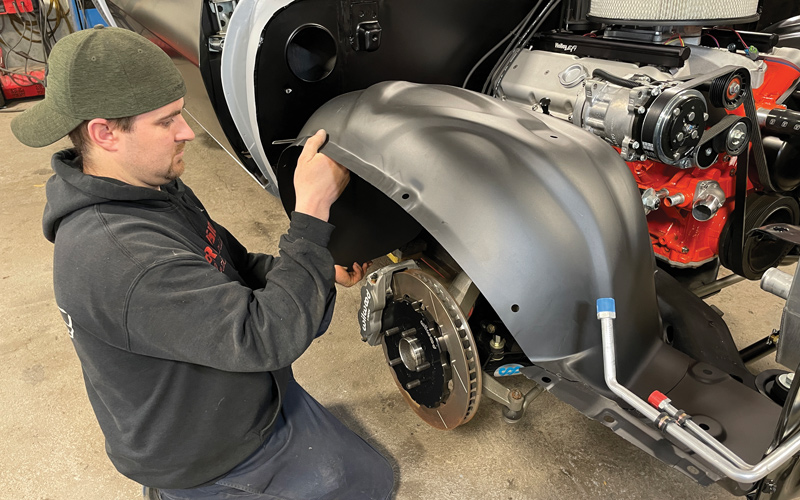
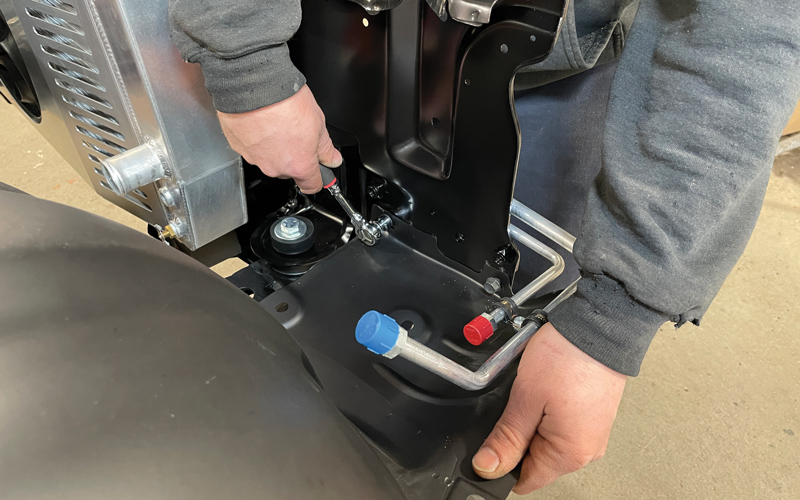
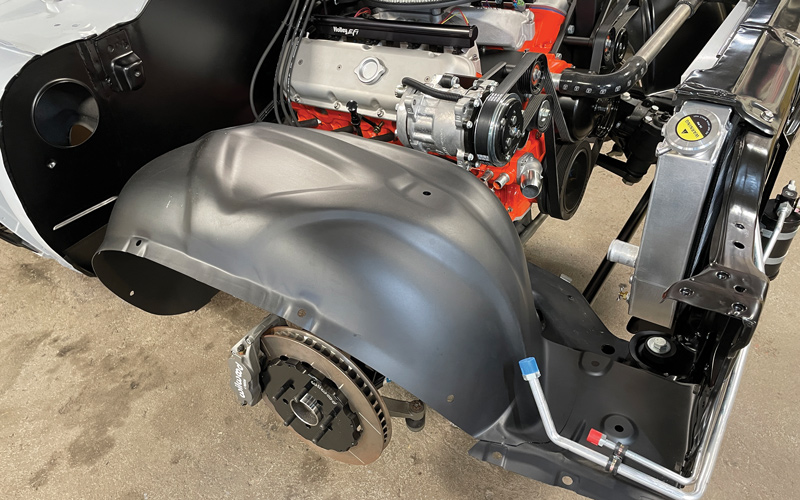
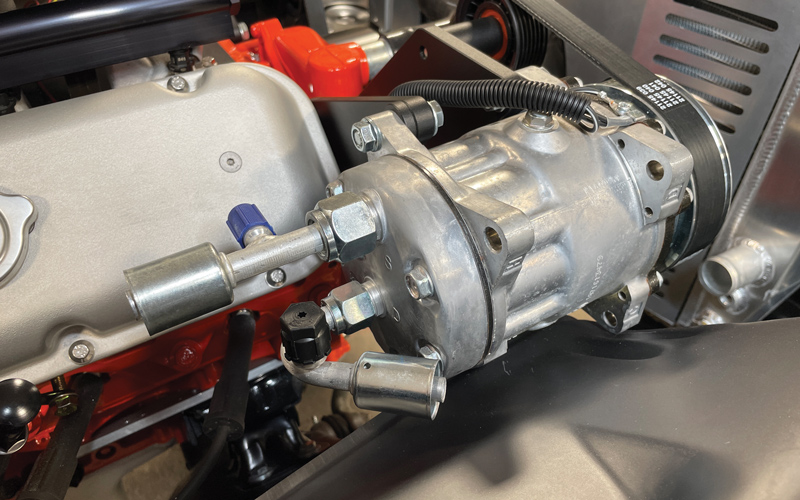
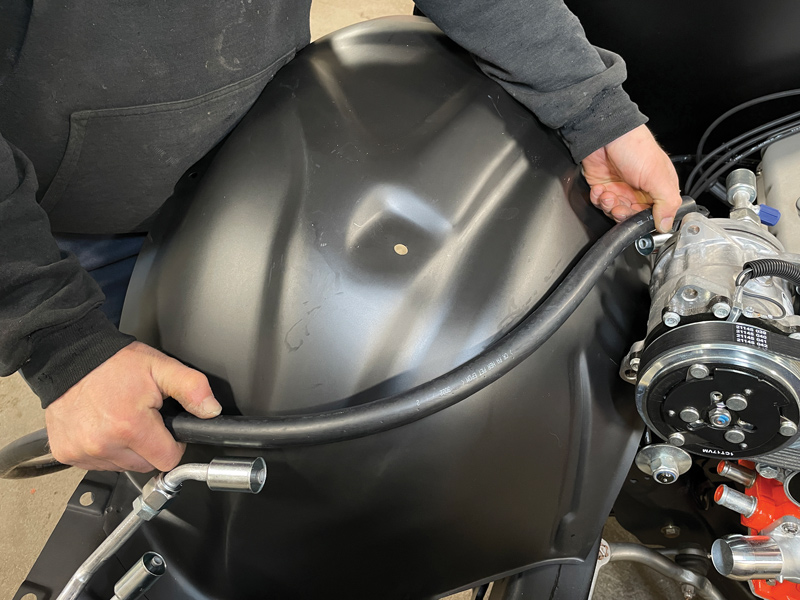
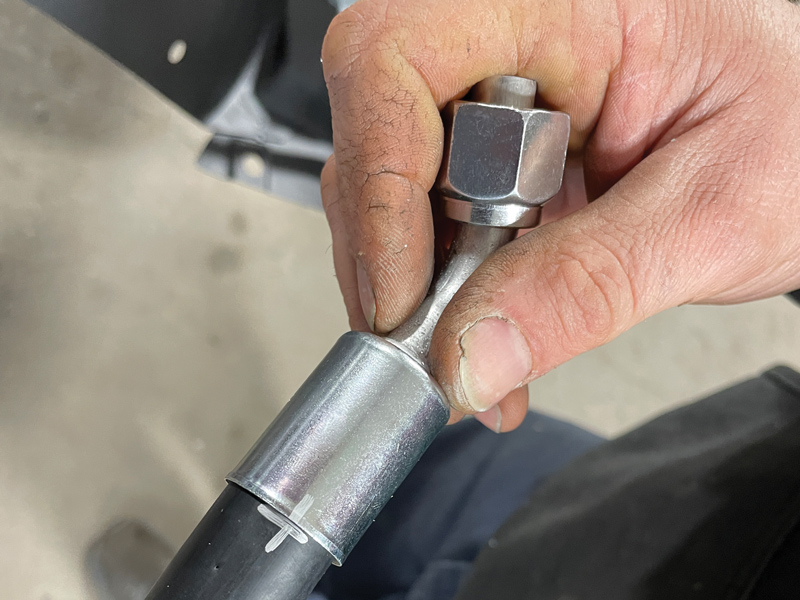
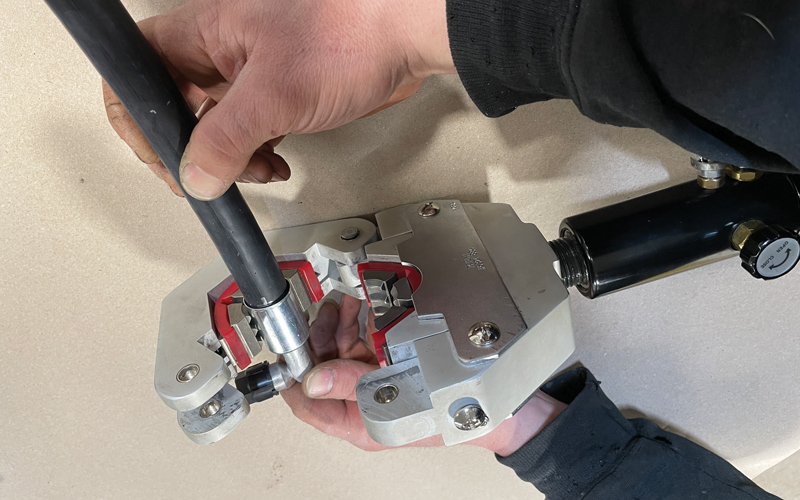
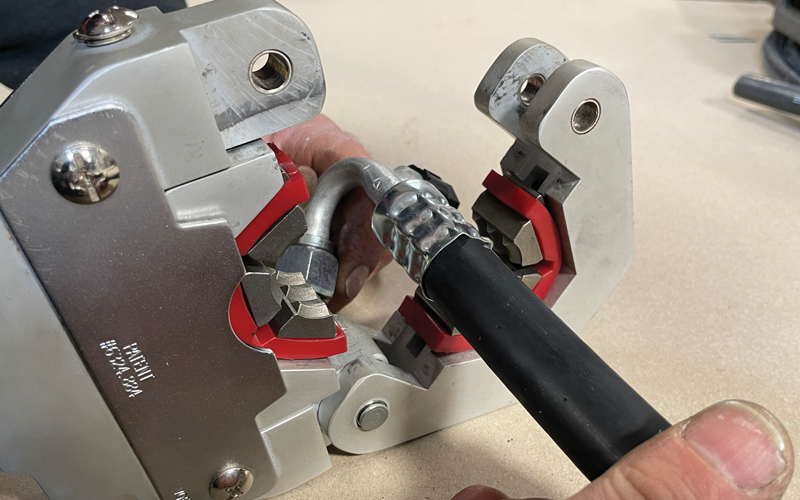
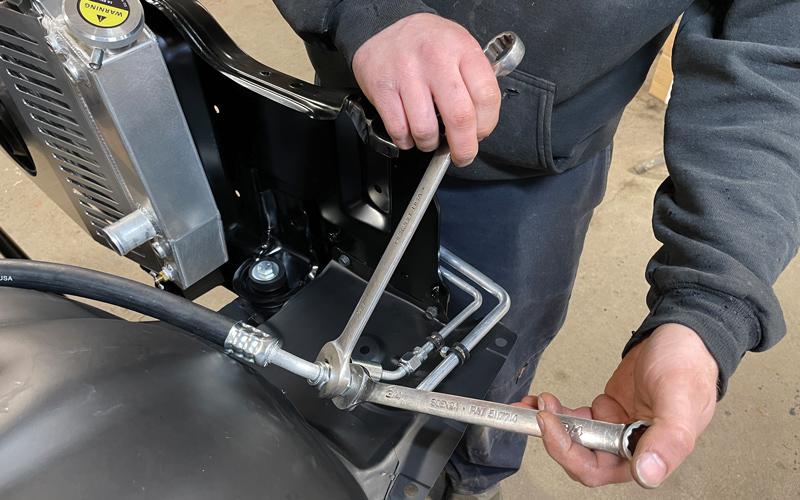
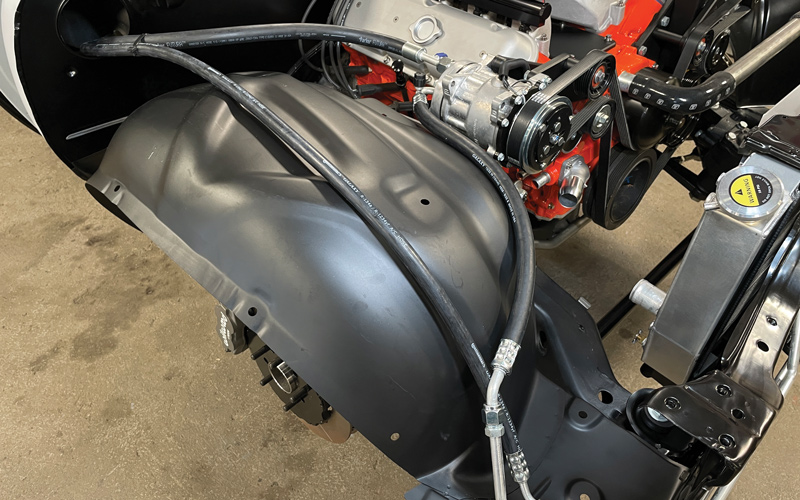
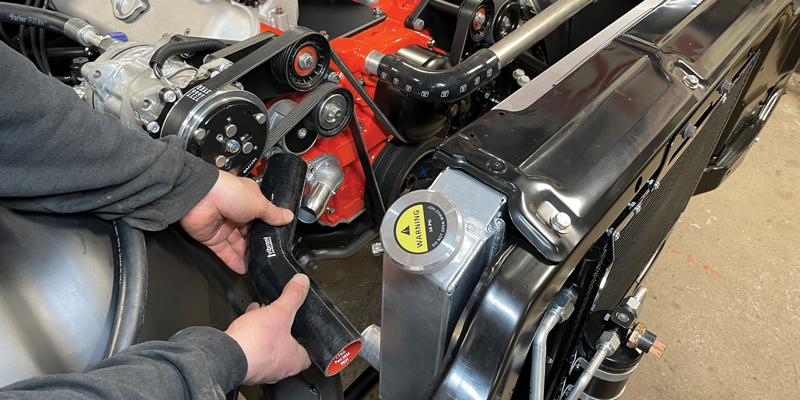
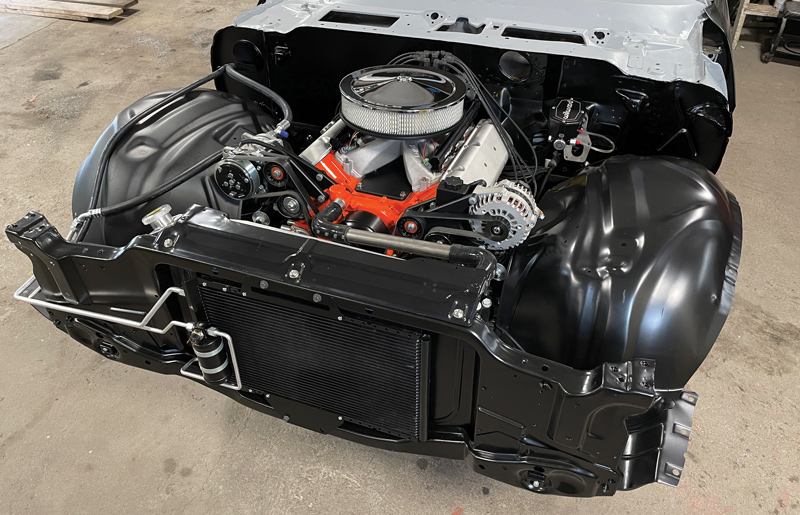
