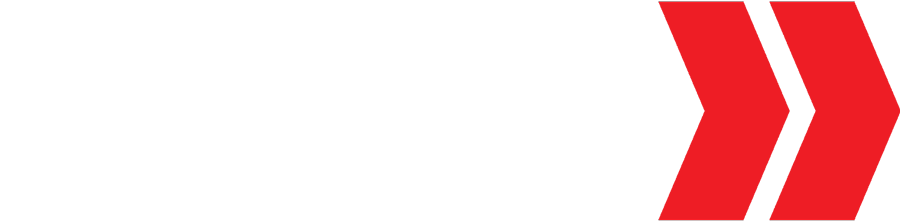

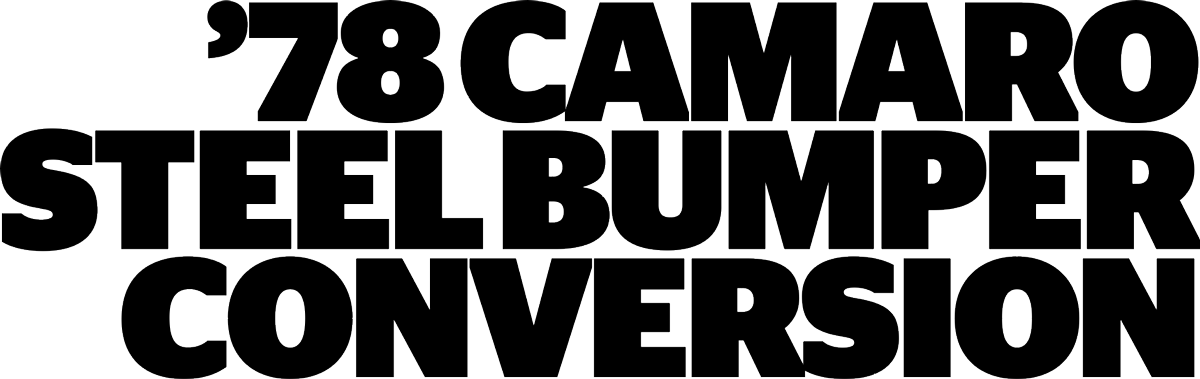
he collector car market continues to grow year after year, making a lot of the cars we know and love harder to obtain. While spit balling one night, The Installation Center owner Craig Hopkins and friend Bill Crabtree were hanging out after a long day’s work and started discussing this very topic. In the background sits a derelict ’78 Chevy Camaro. Hopkins looks at Crabtree and sees the wheels turning. Hopkins asks, “What’s the scheme?” This is where it gets good. Crabtree suggests, “Why can’t we take that old Camaro and turn it into a steel bumper car?” Hopkins, with his vast experience, immediately knew that this had to be done. Why not? The ’74-81 Camaro is vastly more available than that of the ’70-73 cars. Anyone who has restored an early second-gen Camaro knows that the entry point on one of these cars continues to climb. Crabtree continues, “If we can swap the front and rear and turn that car into an earlier version, that opens a whole realm of cars available at a considerable cost reduction.”
Hopkins then contacted us here at All Chevy Performance magazine to see if it was something our readers would want to see. Heck yeah! This is right up our alley. So, we are starting this multi-part process with some of the basics. This is going to be an involved project, but if you follow along in the next few issues we are confident that you too can do this at home, or at least bring the idea to your favorite hot rod shop to handle the process.
Let’s dive in and get started. We take you to The Installation Center in Cleveland, Georgia, where Hopkins will show us the ins and outs of how to make a later second-gen Camaro look like the more desirable early second-gen (’70-73) Camaro.
In this article, we are going to cover the basics of car prep and teardown. Here we go!
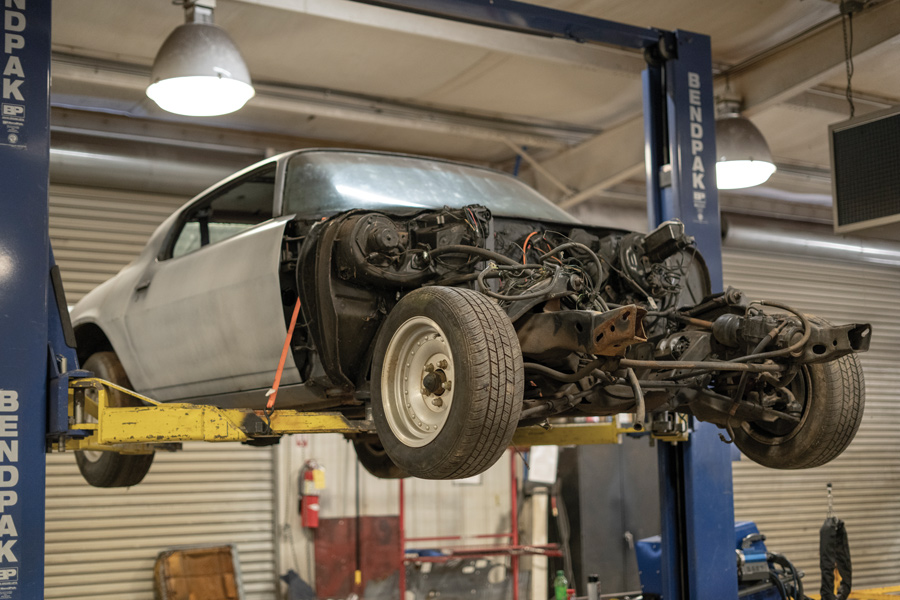
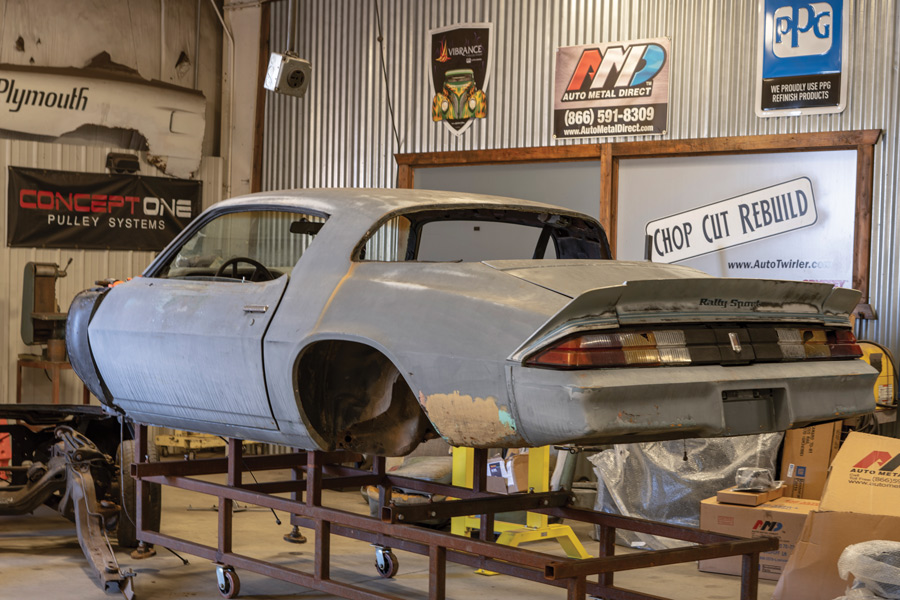
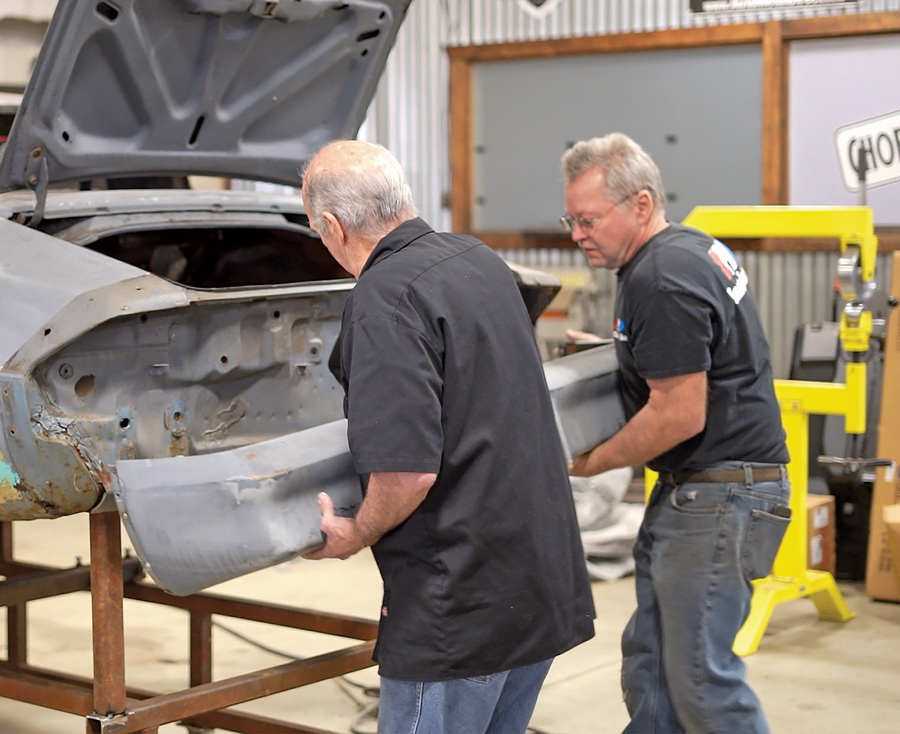
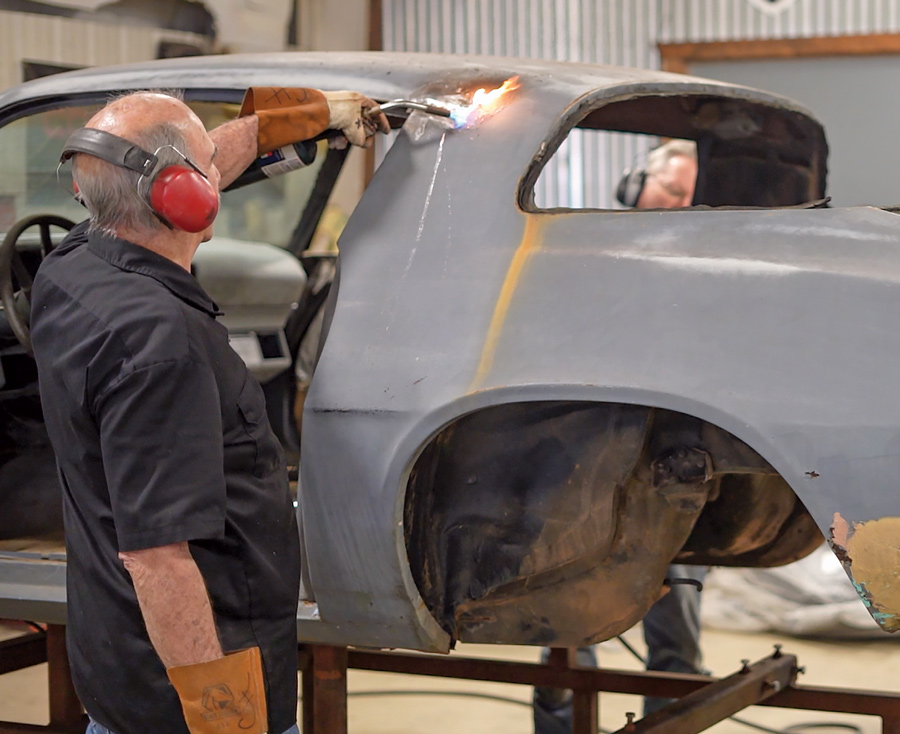
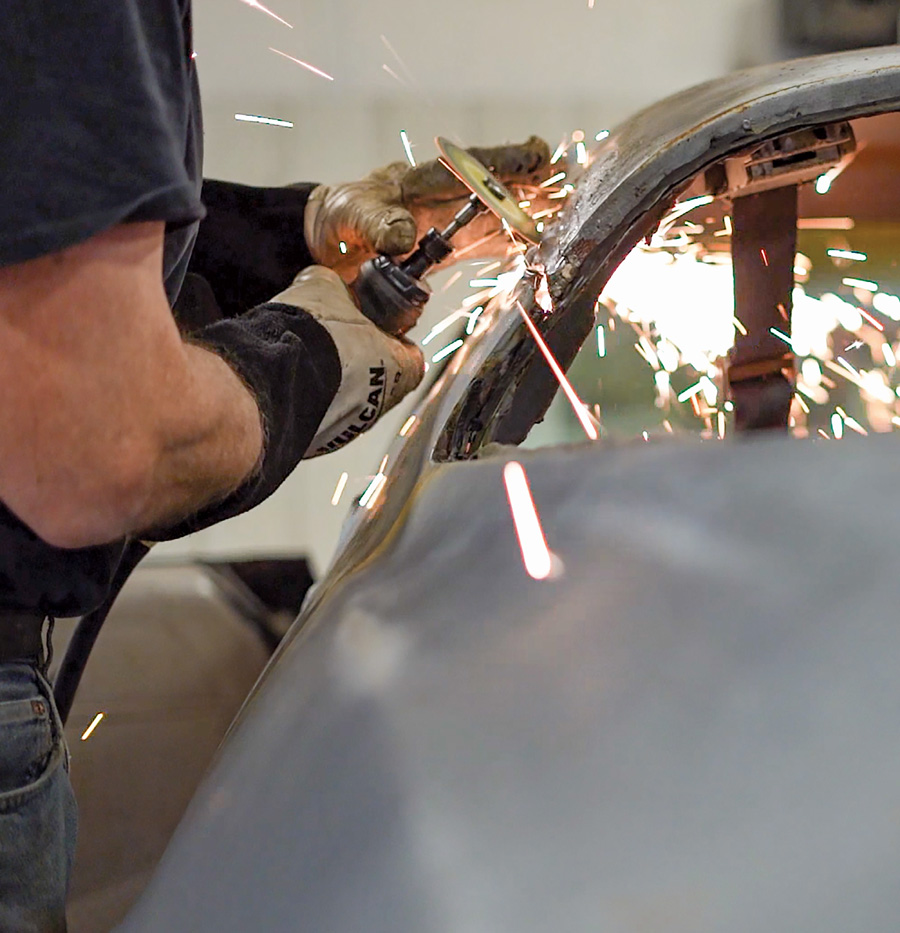
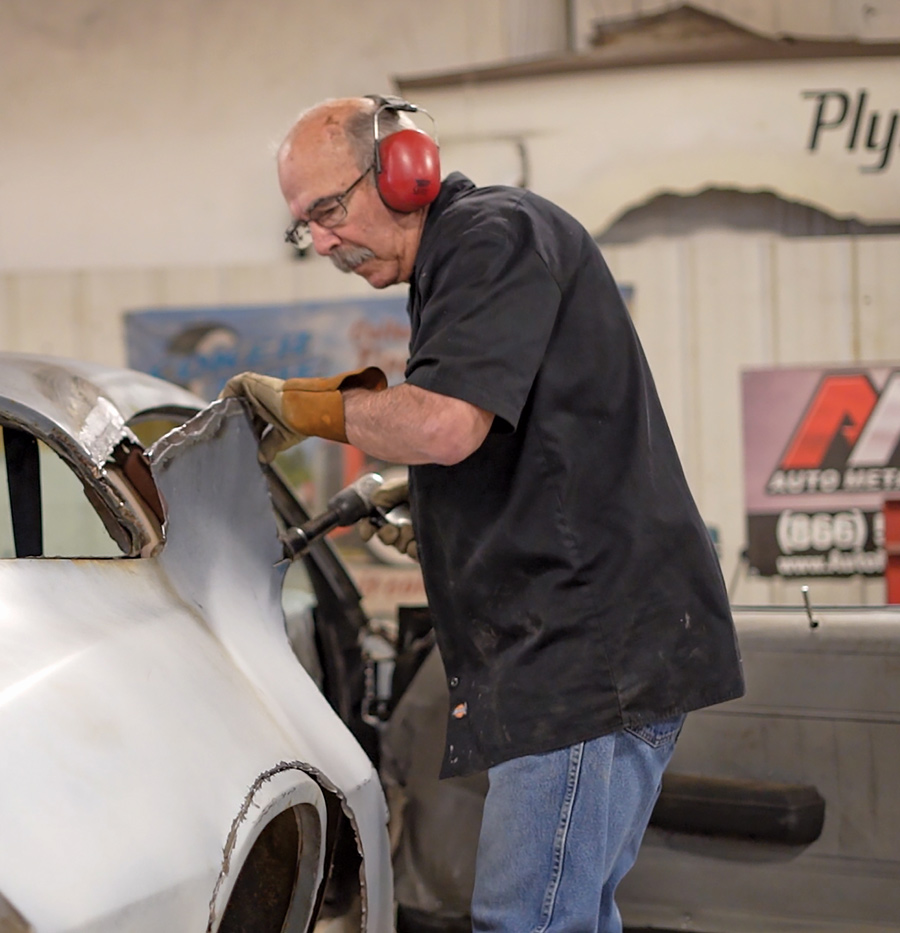
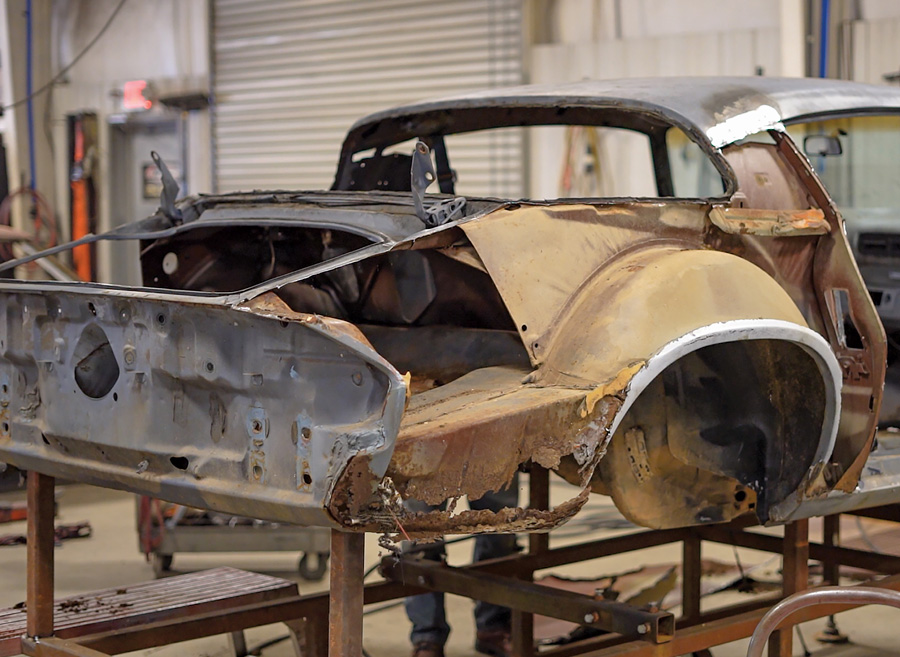
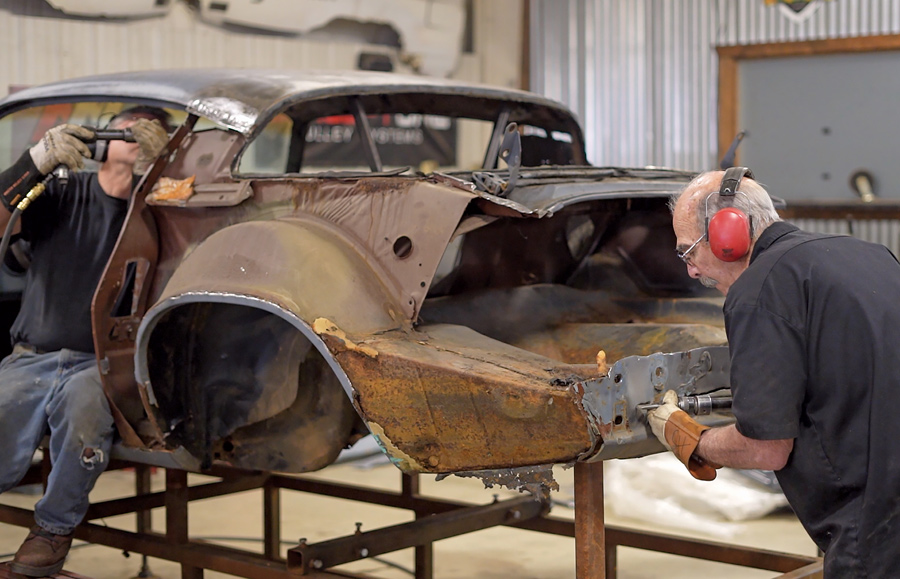
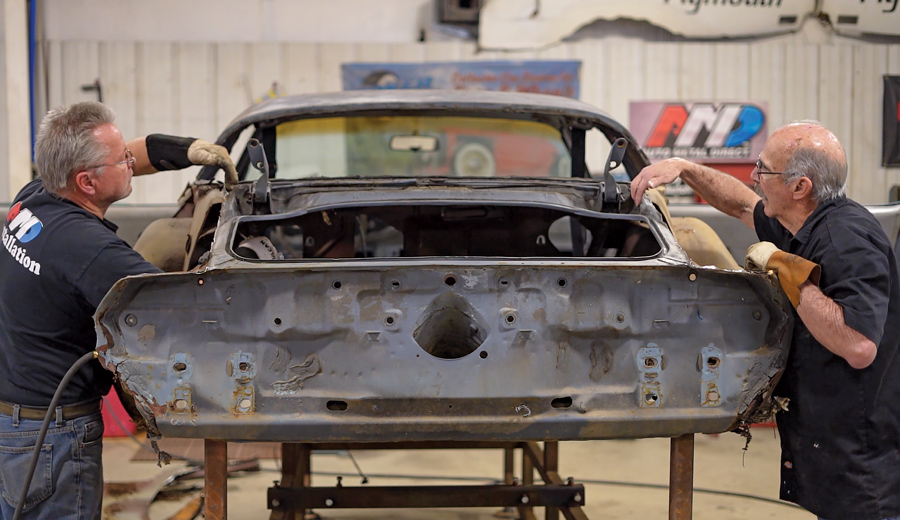
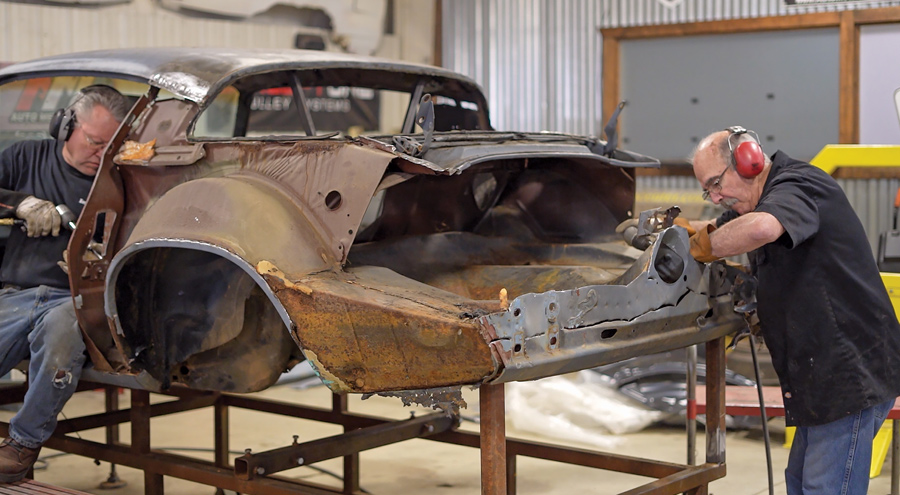
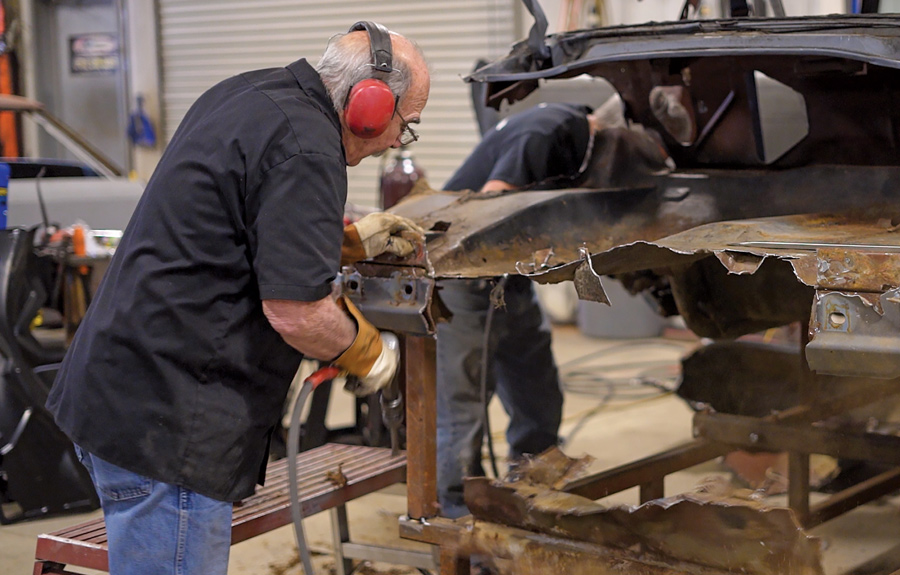
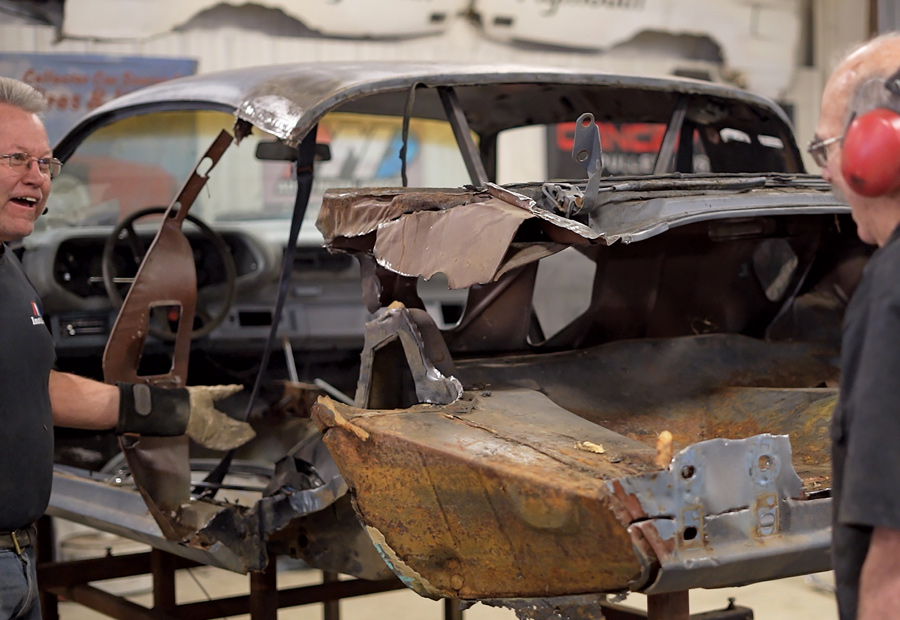
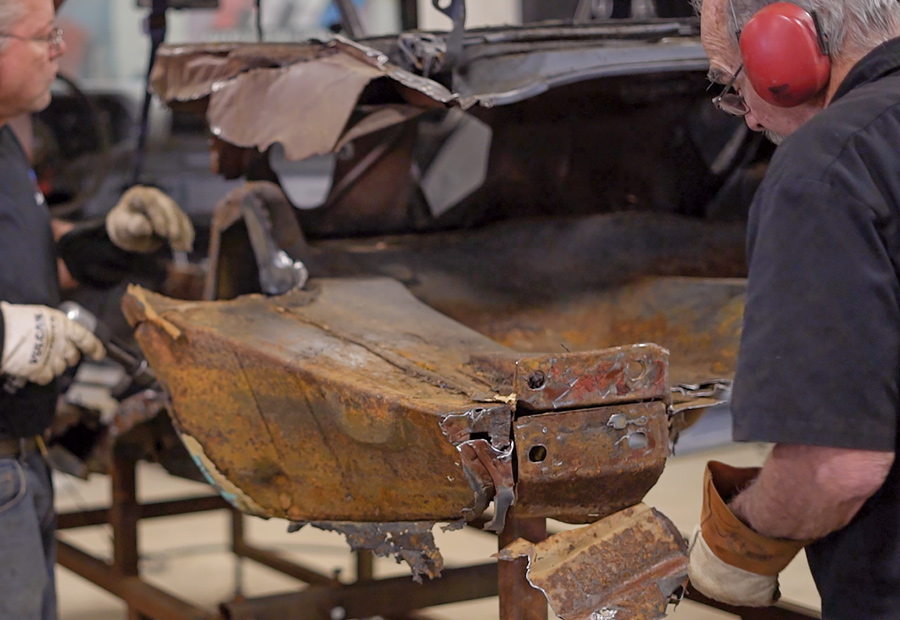
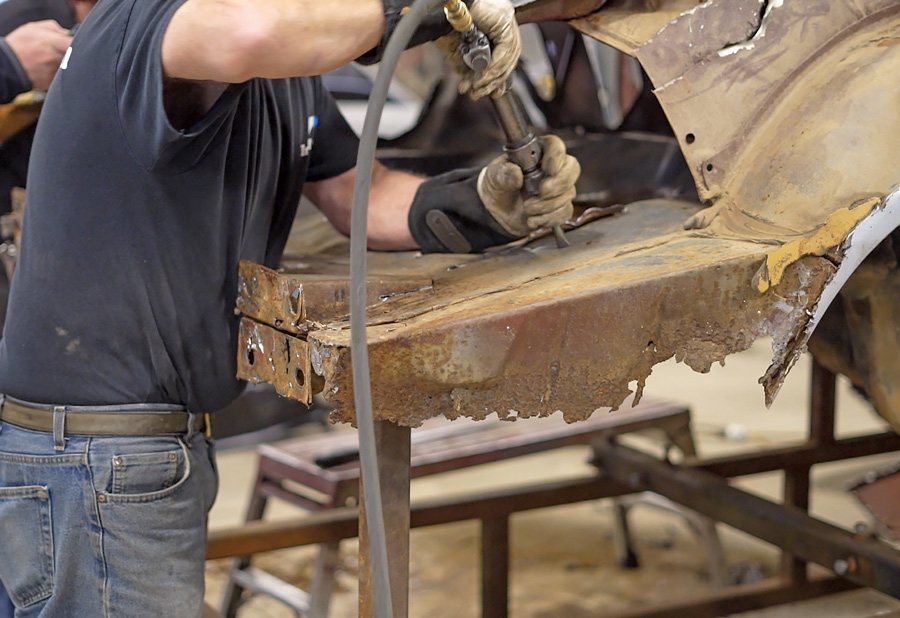
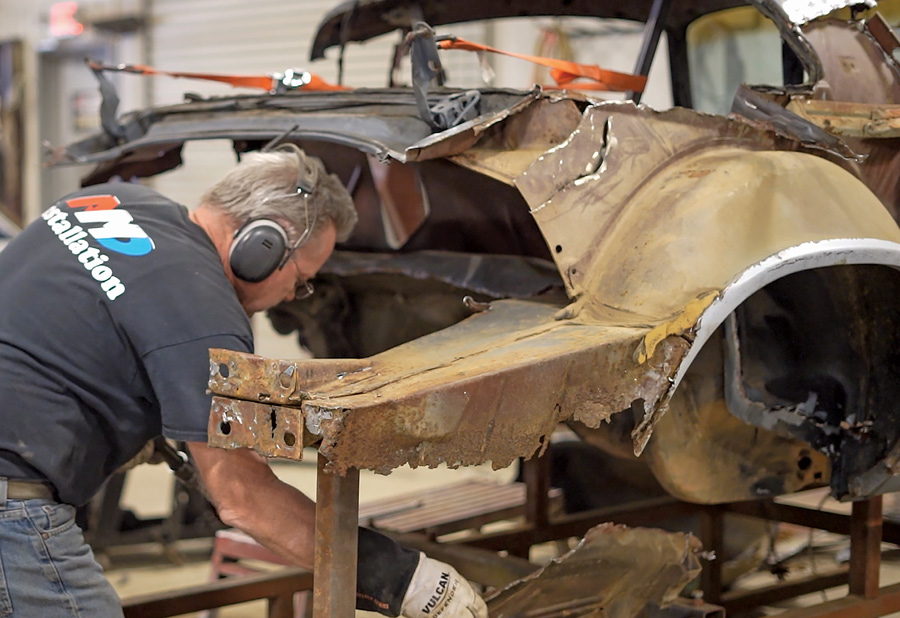
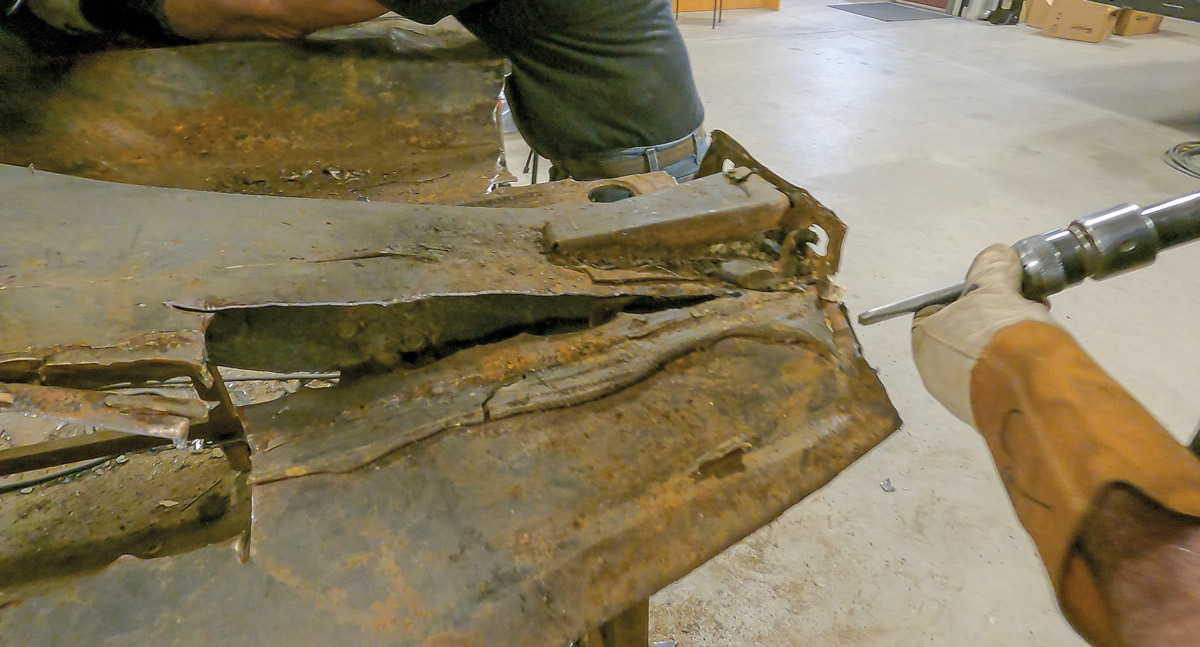
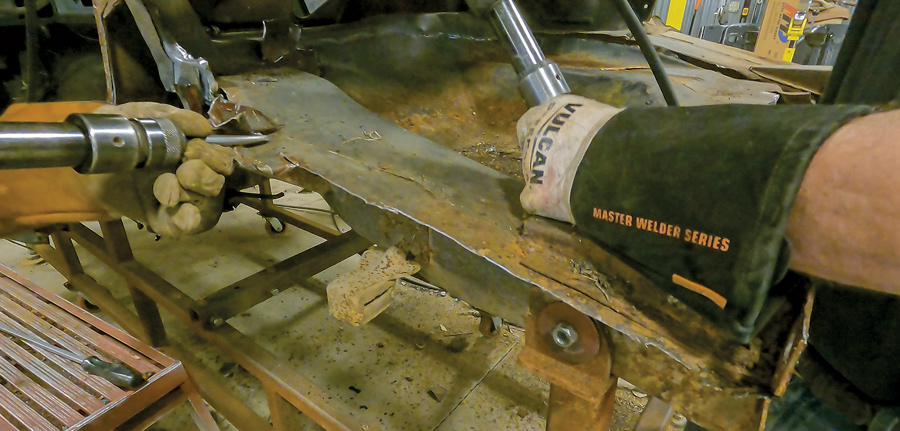

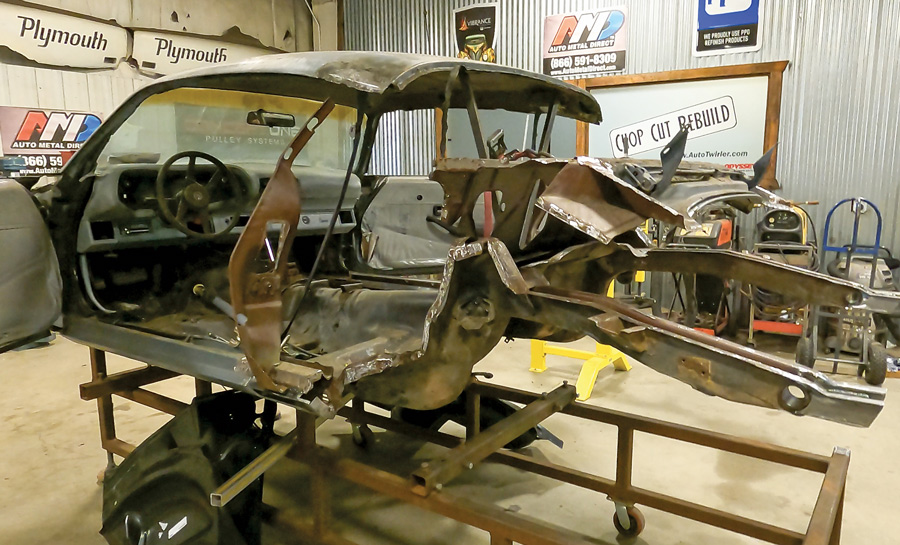
