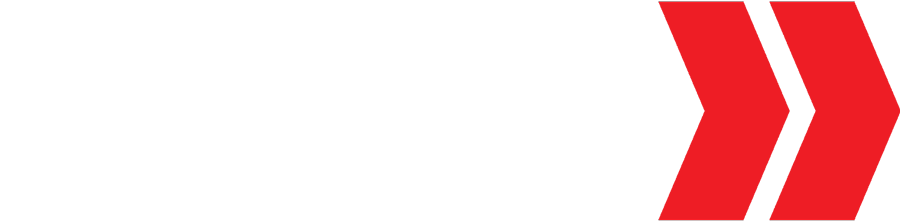
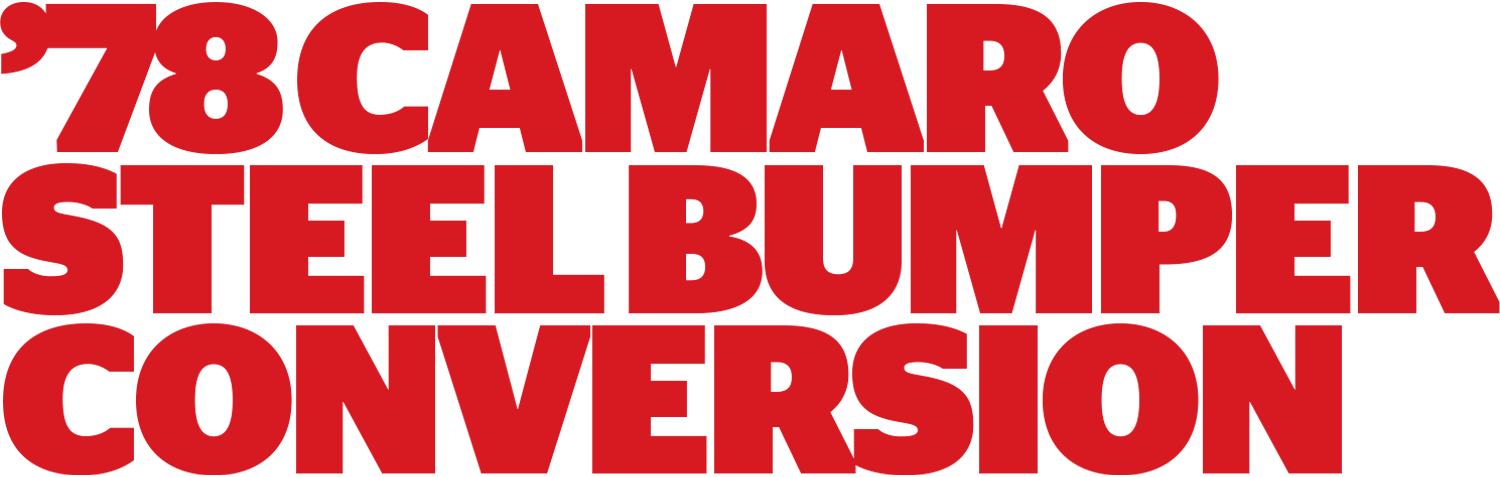
Part 2: Buildup and Framerail Mod

elcome back to our multi-part series on our second-gen Camaro conversion. Last time we covered this project we addressed the teardown of our ’78 Camaro that we are converting to a ’71-73 steel-bumper car. It is a pretty straightforward process where we removed the entire back end of the car with the exception of the roof, package tray, and framerails. You can catch that in the June ’22 issue of All Chevy Performance.
This time around, we cover the modifications that you will need to make both framerails, proper location of the trunk floor, prepping the panels for installation, and mocking them up properly to get those gaps nice and tight.
With this conversion there isn’t a ton of fabrication needed, making it a very approachable conversion. We are back with Auto Metal Direct and Craig Hopkins of The Installation Center. We’ll follow along to see how Hopkins tackles that framerail situation and how he aligns the AMD panels to make this conversion a breeze.
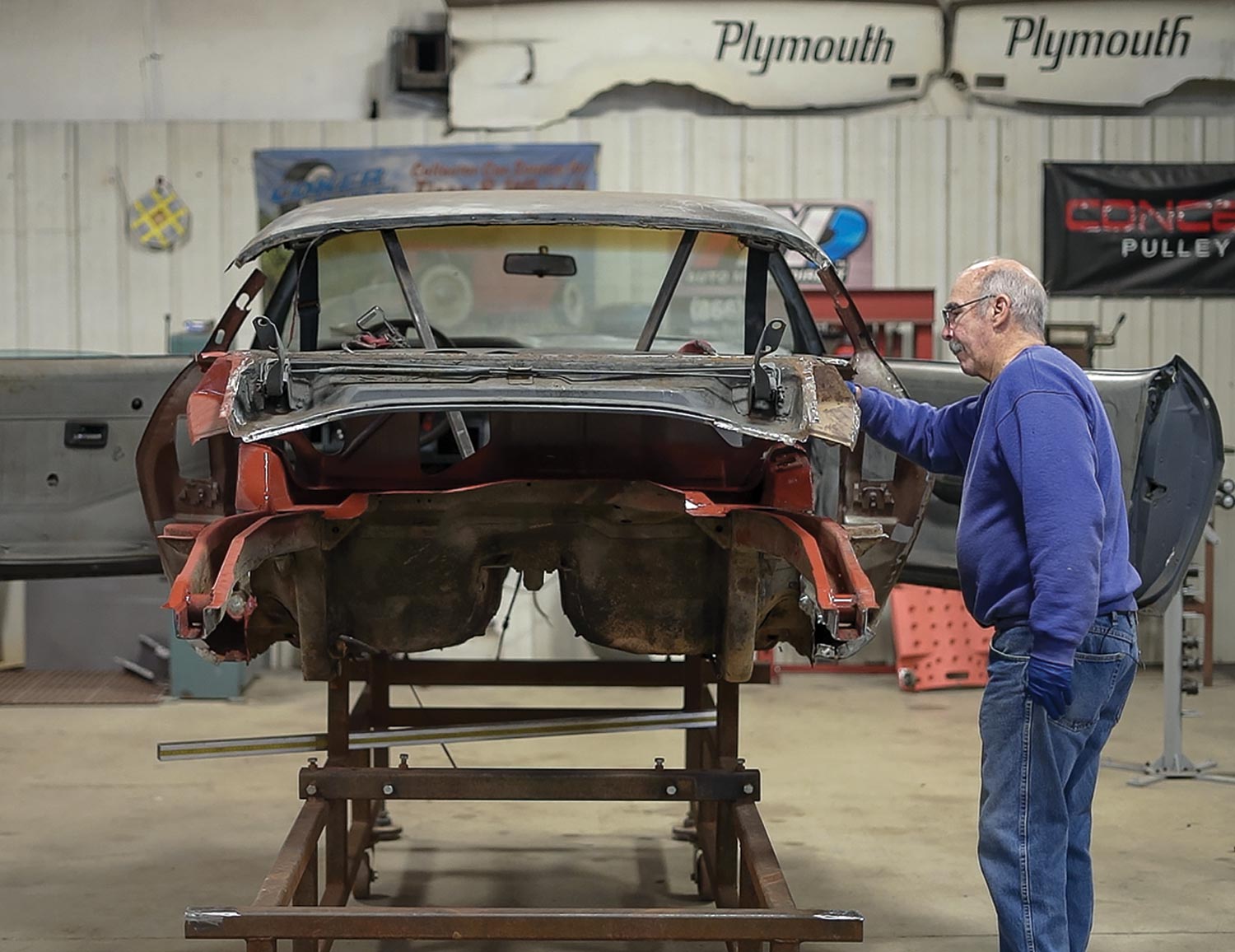
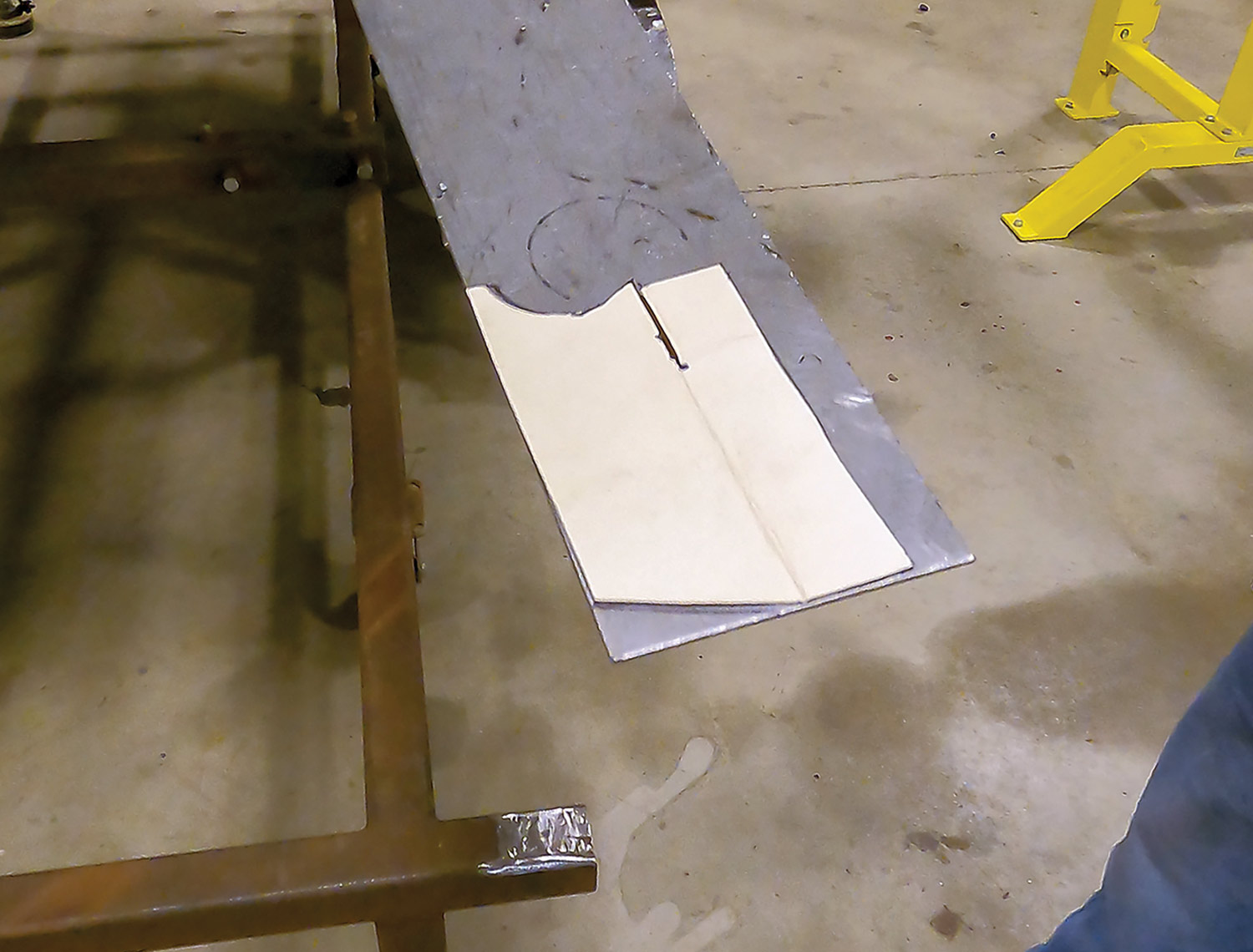
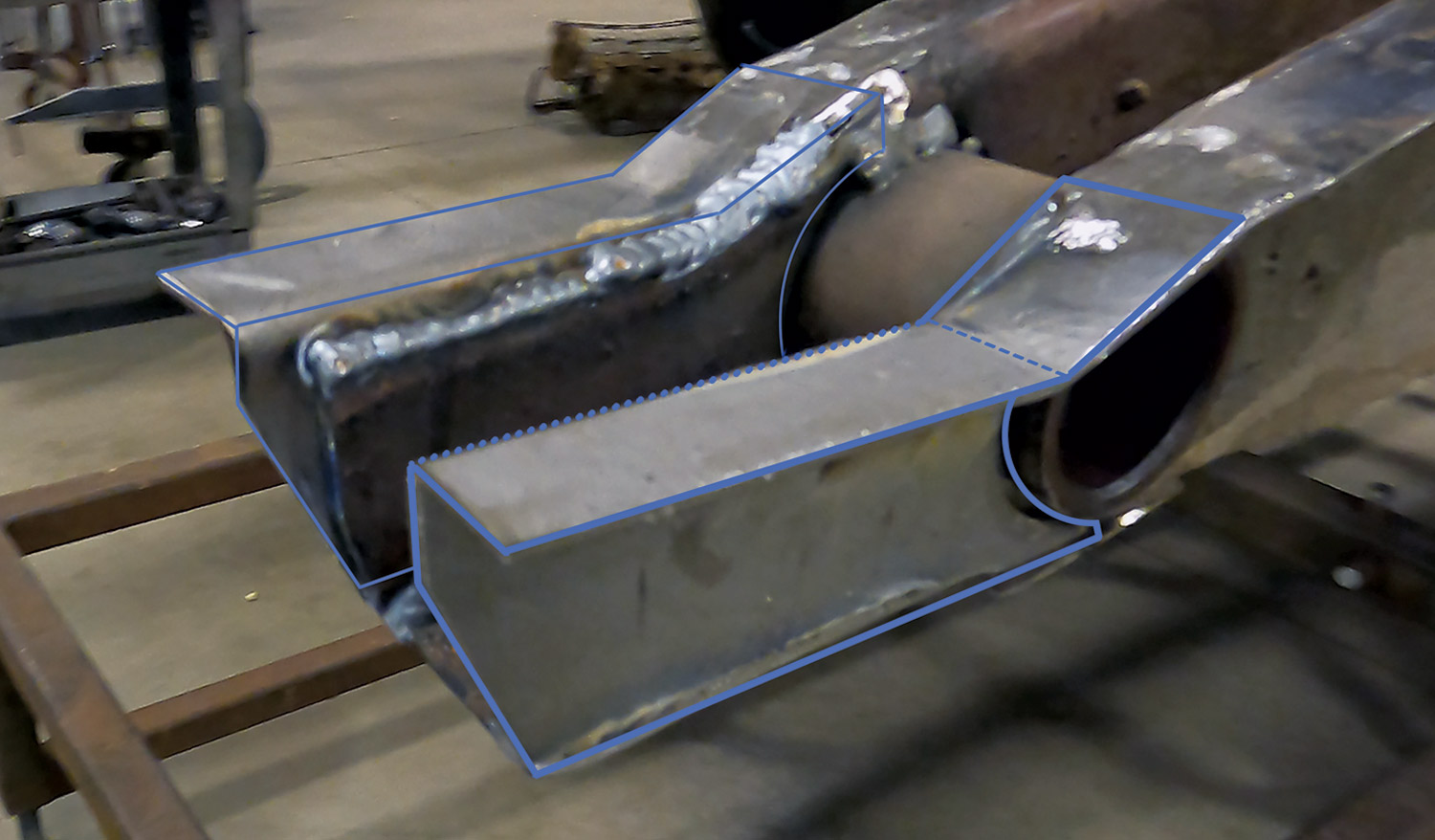
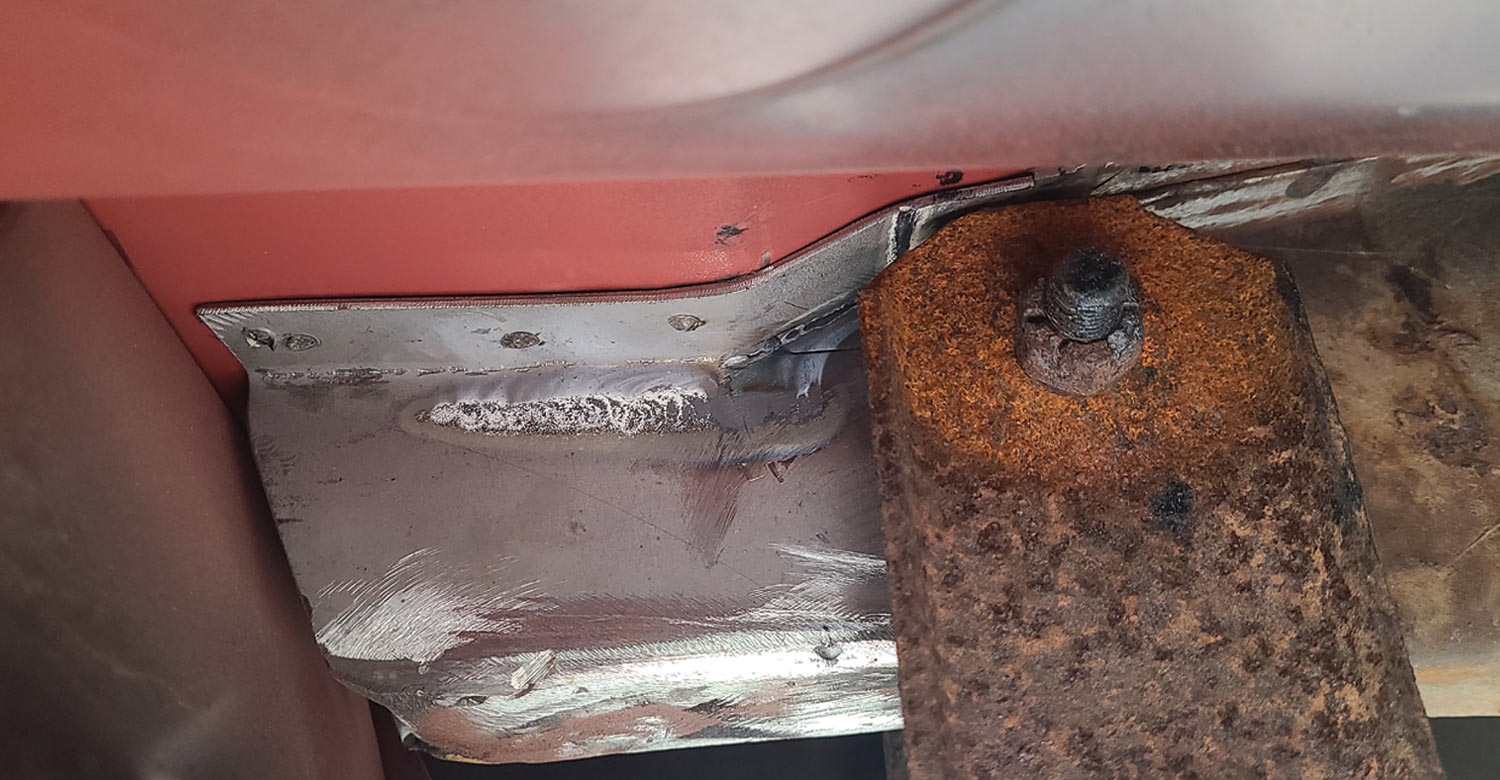
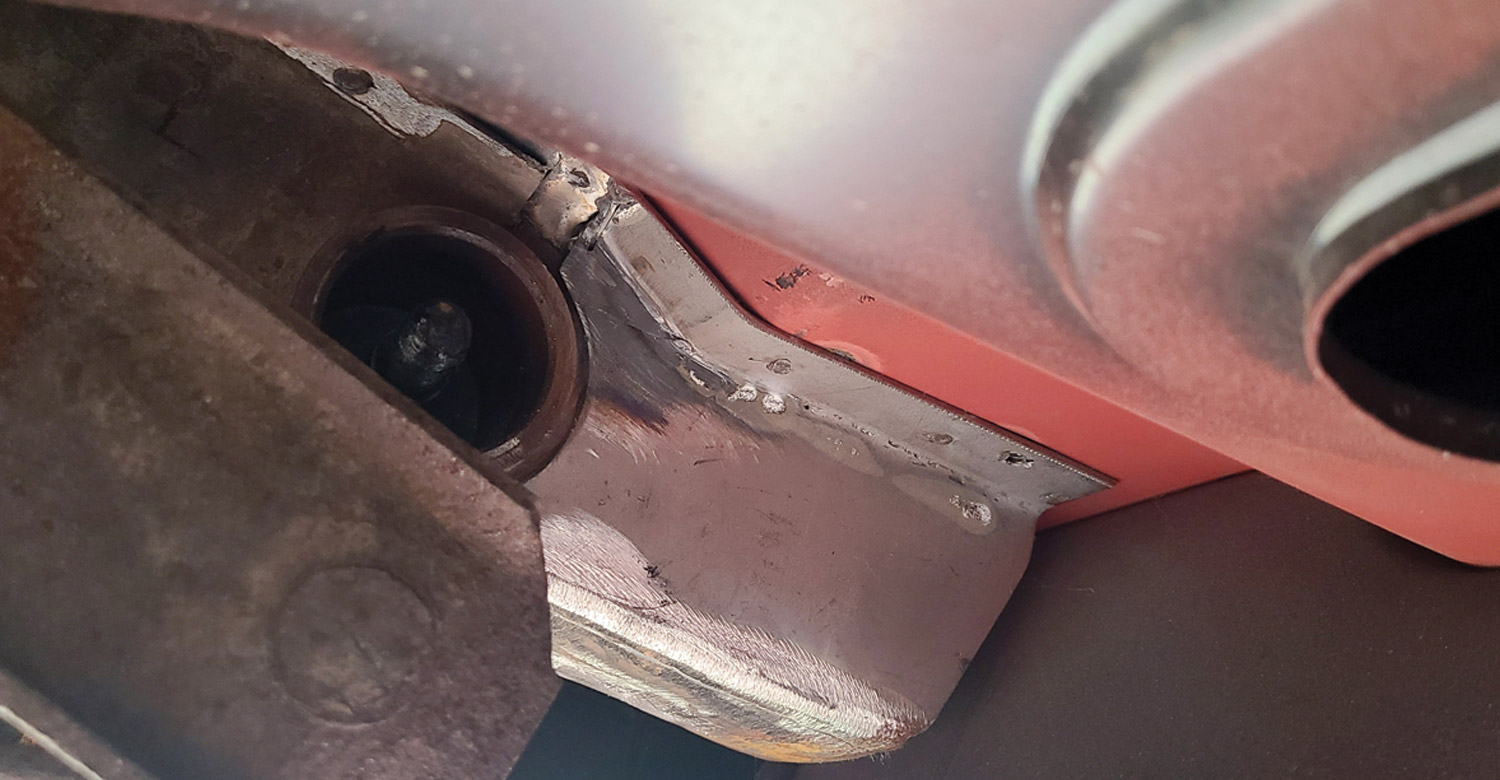
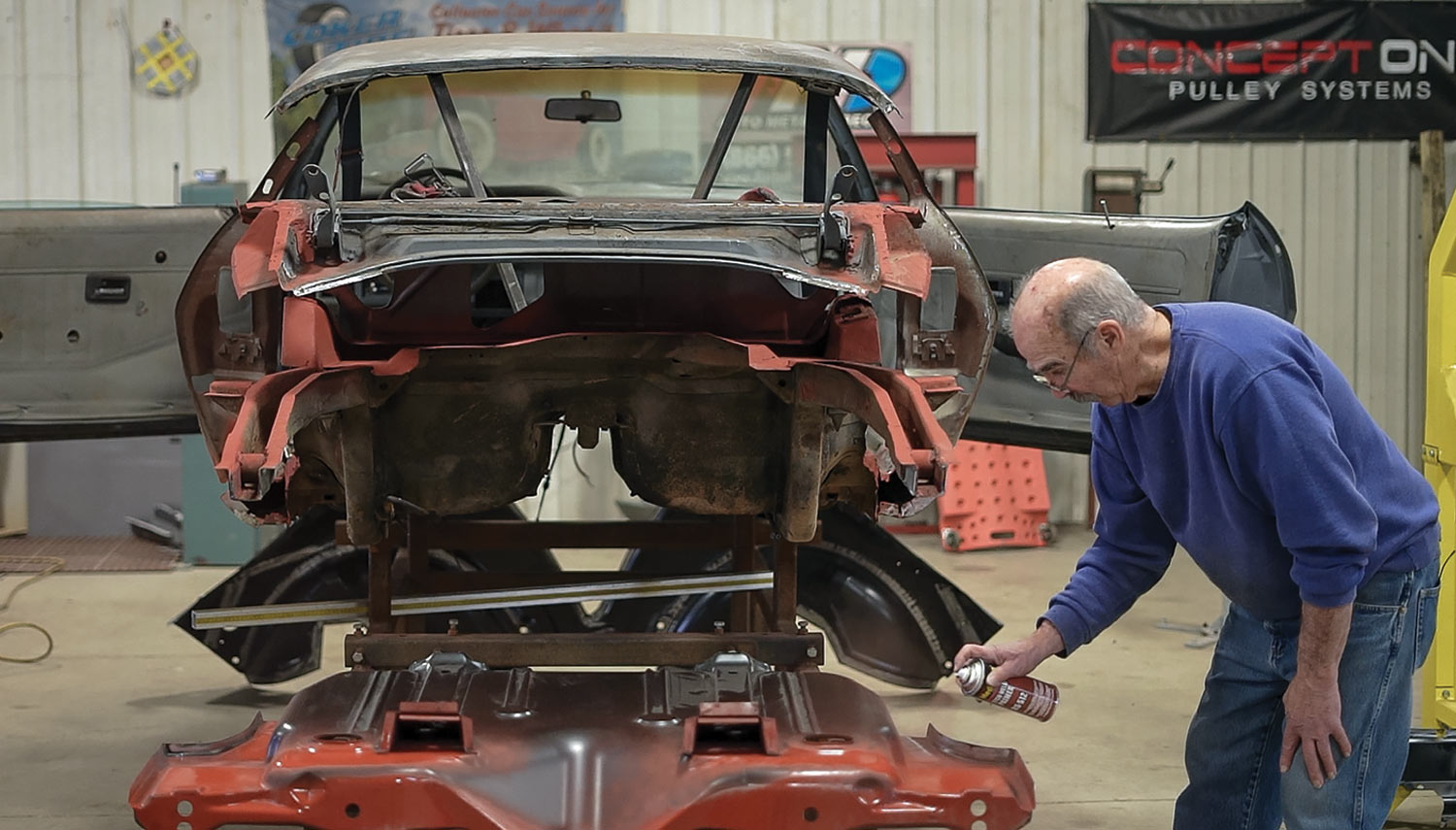
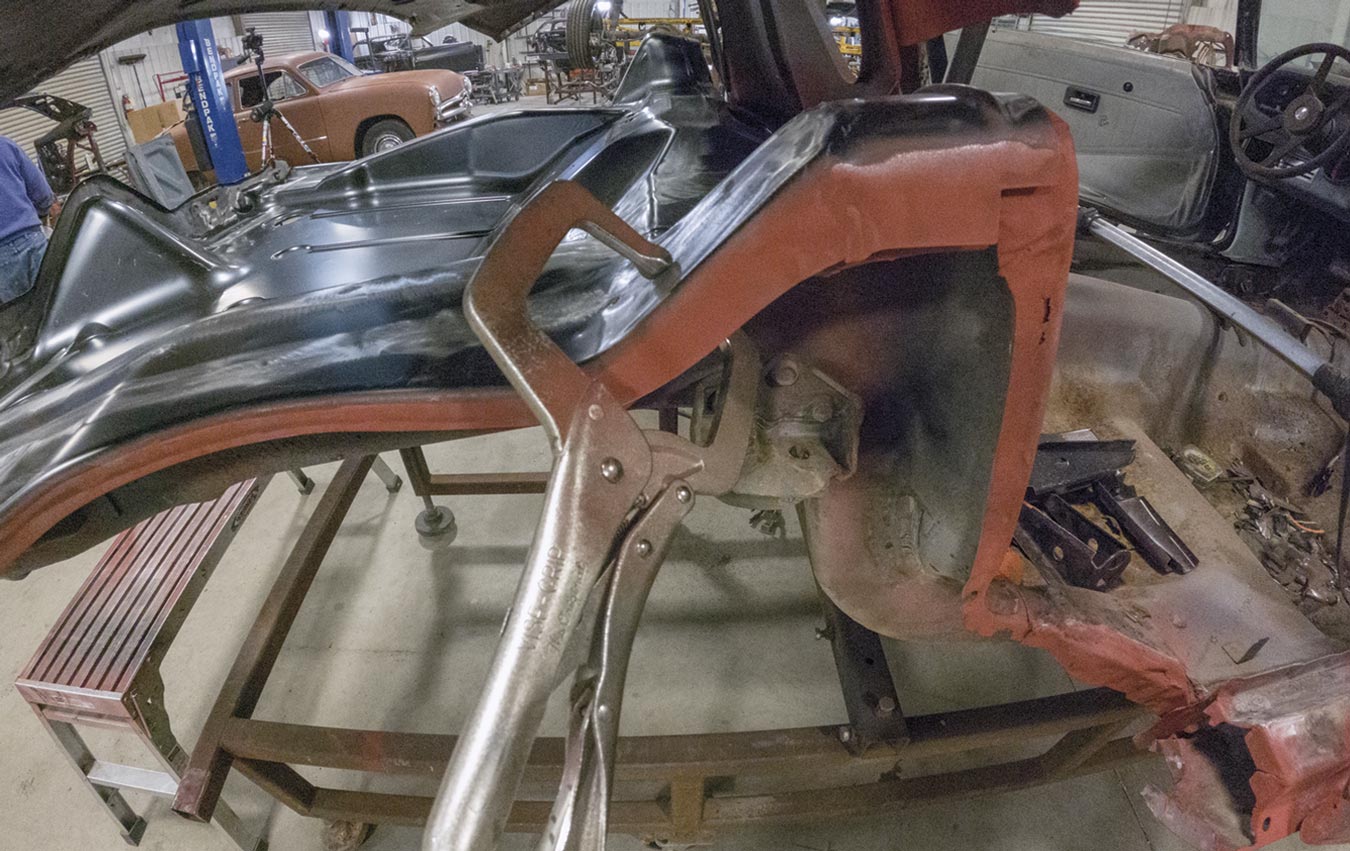
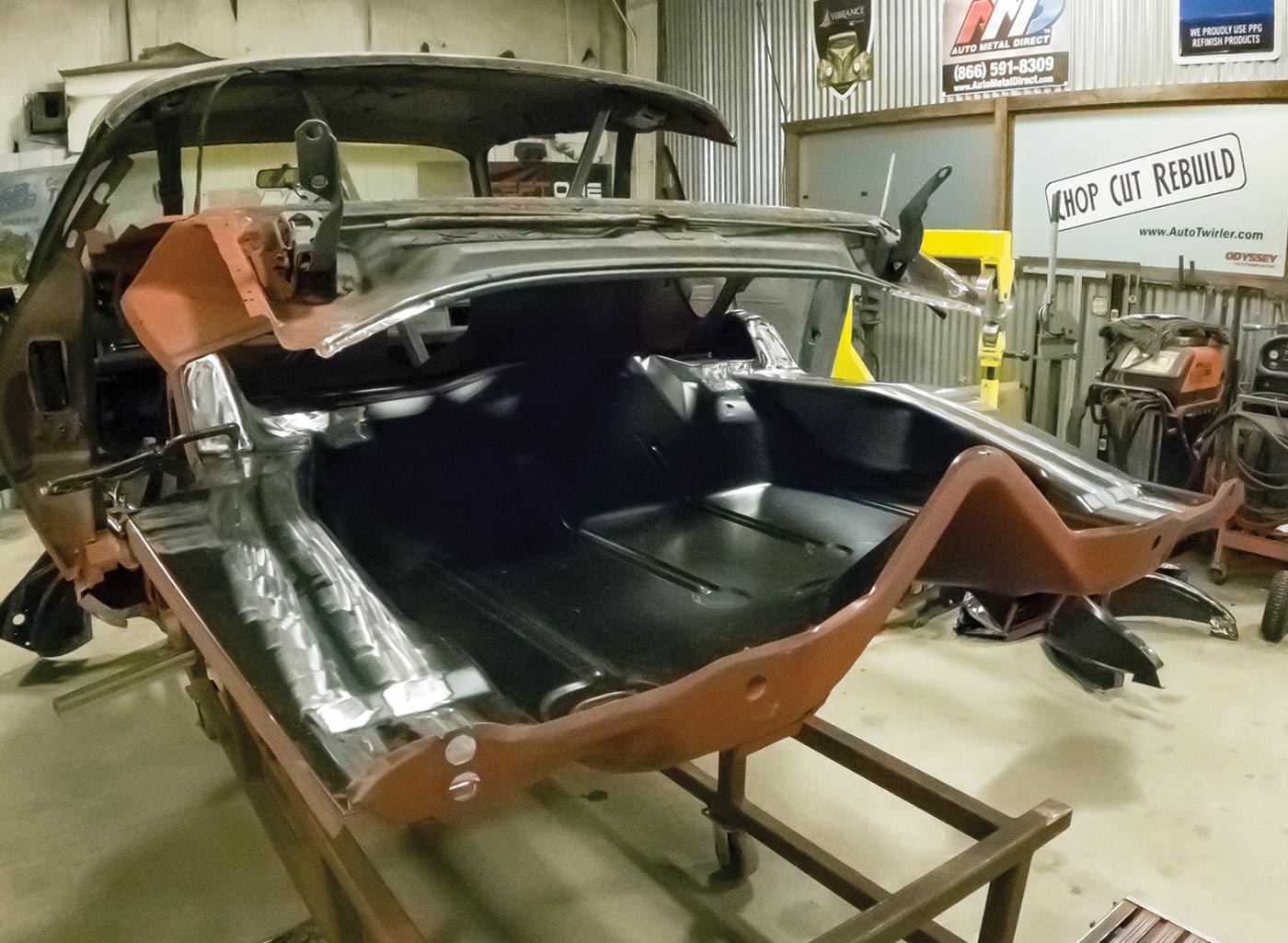
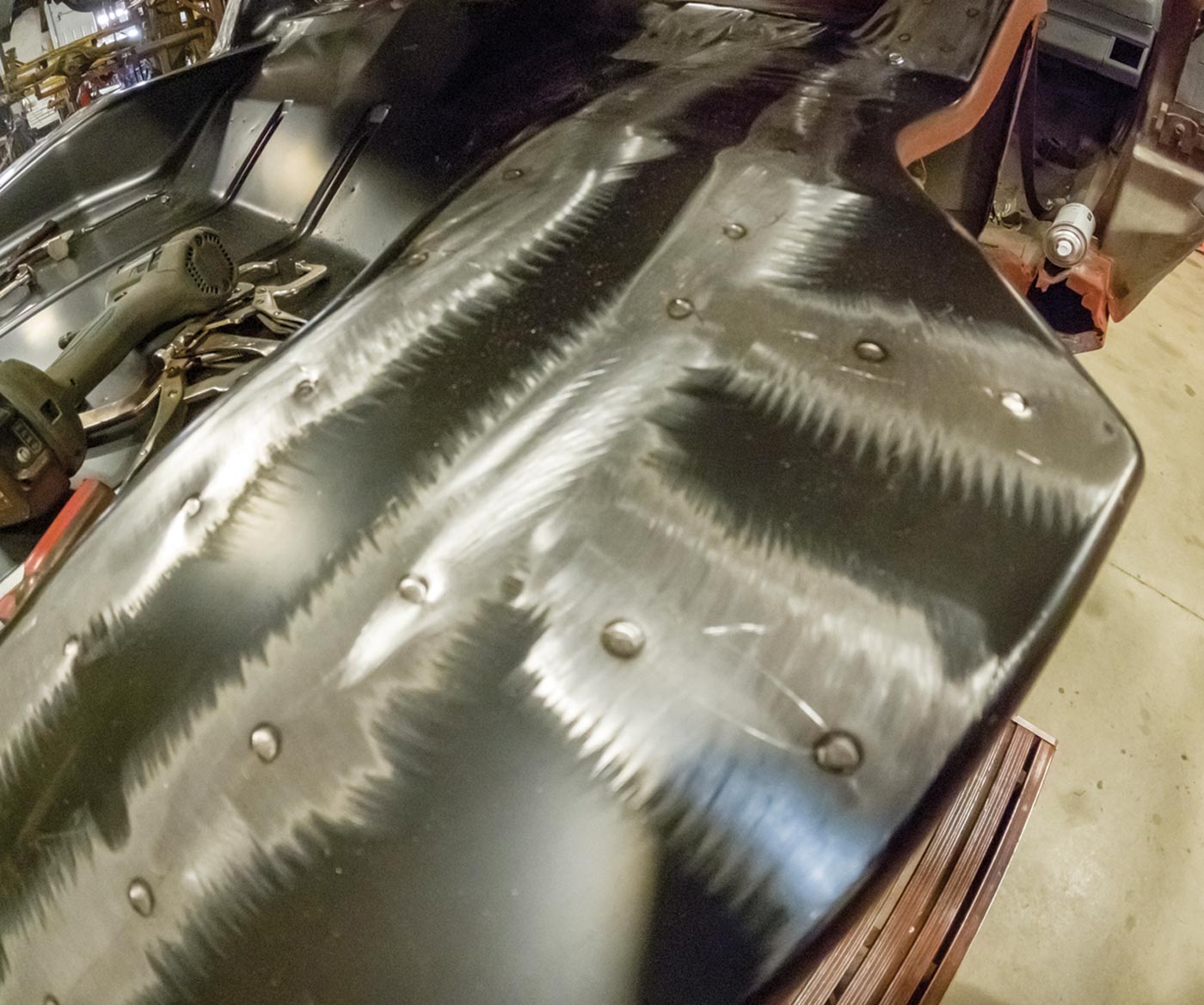
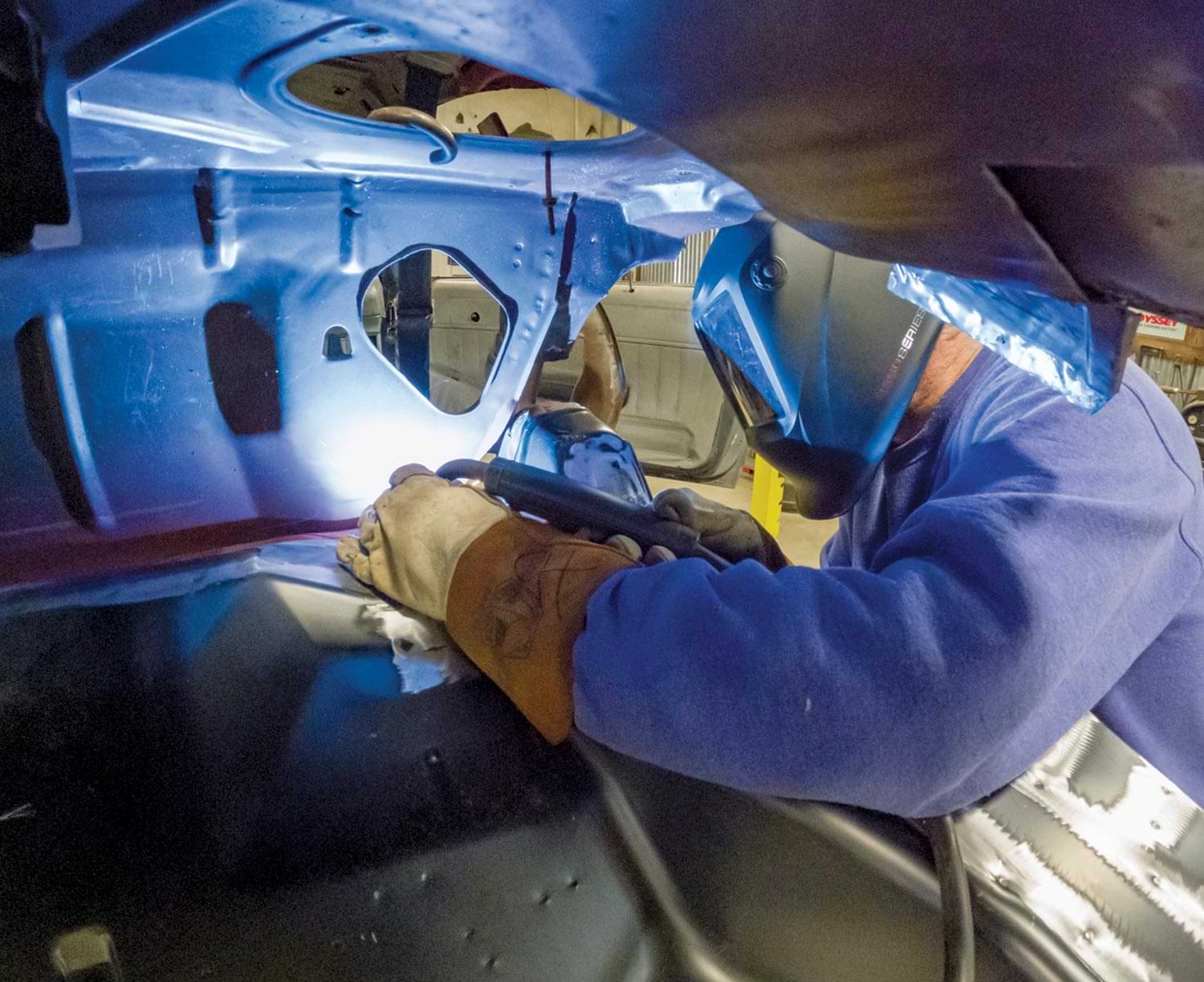
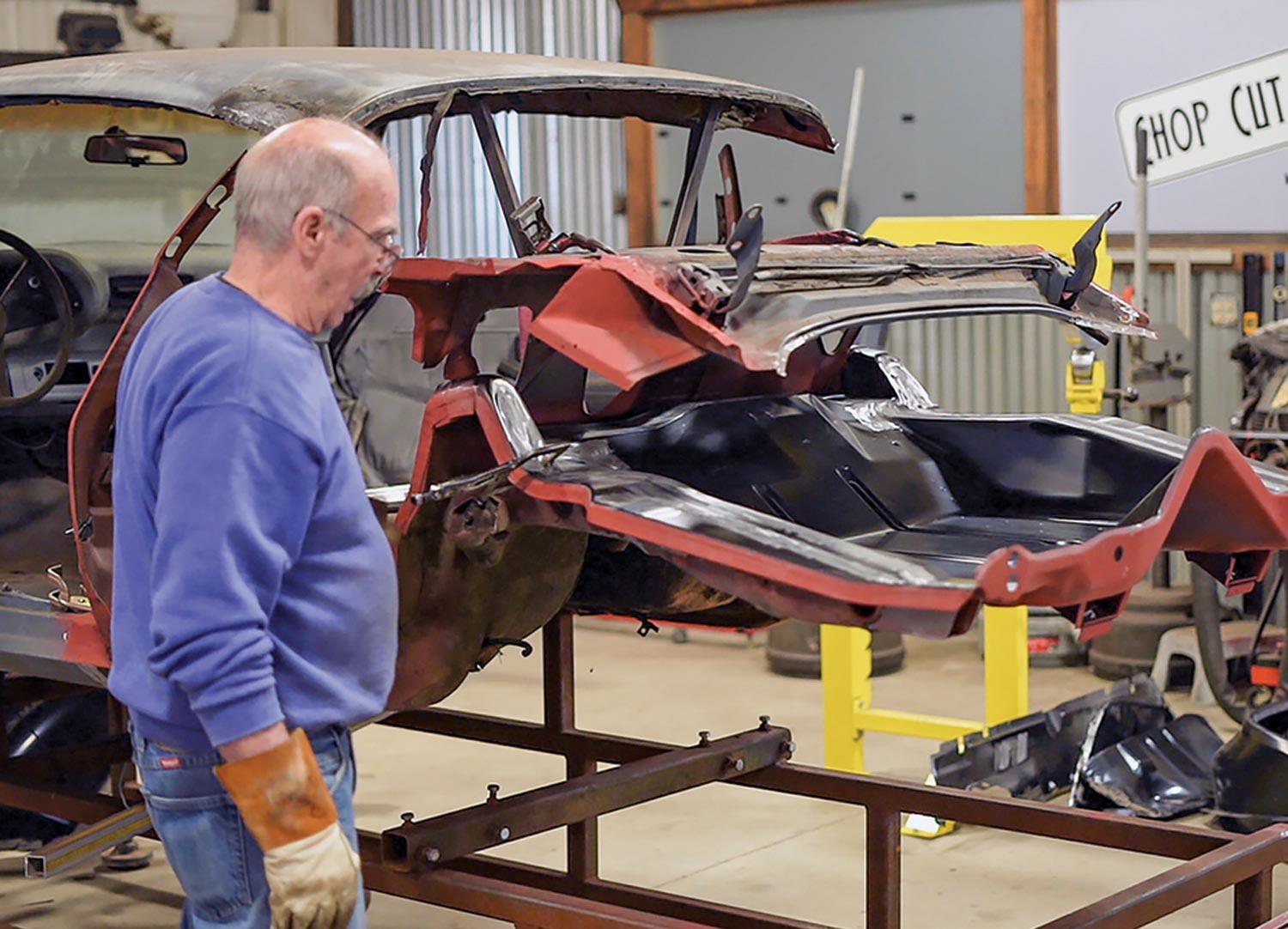
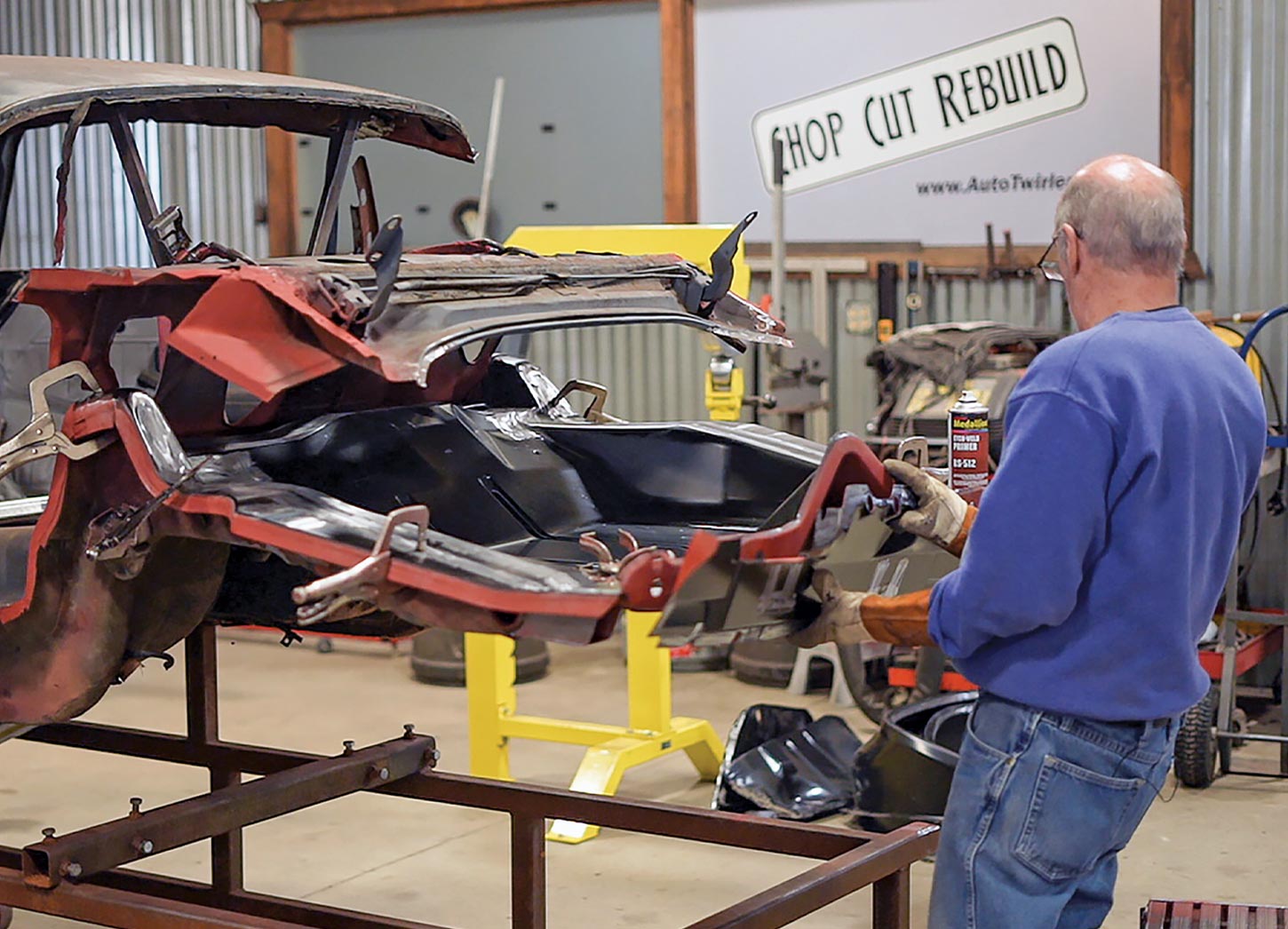

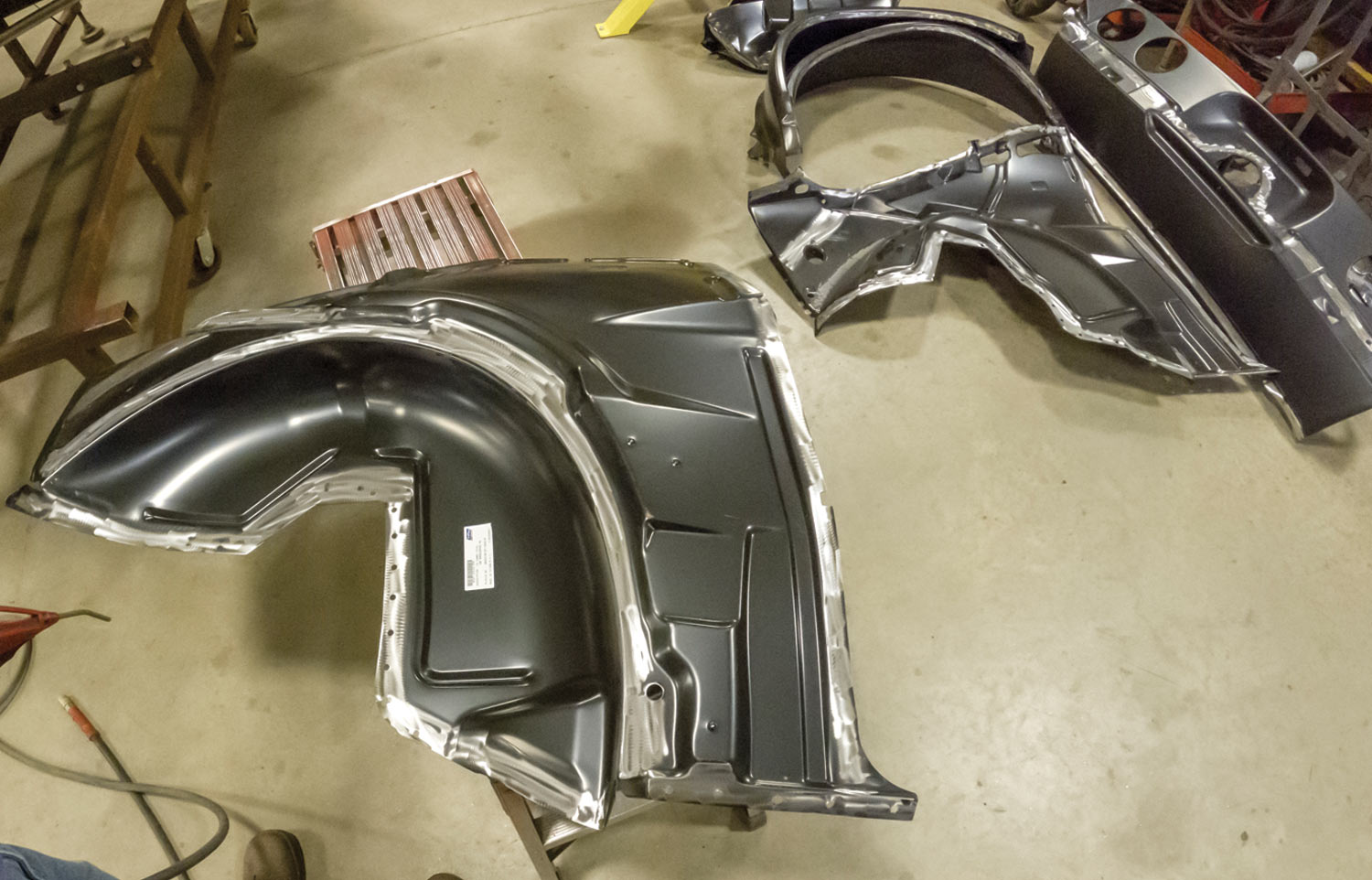
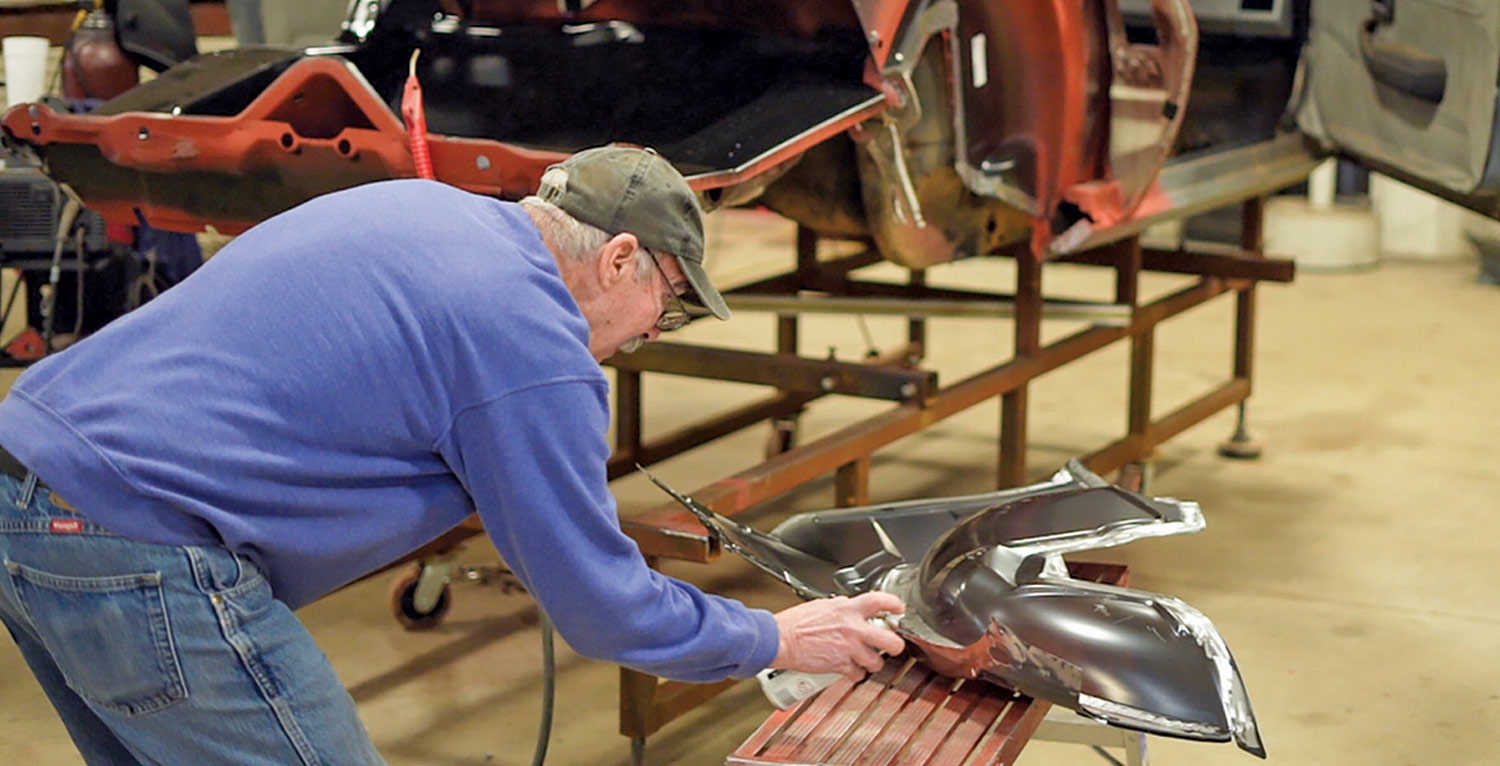
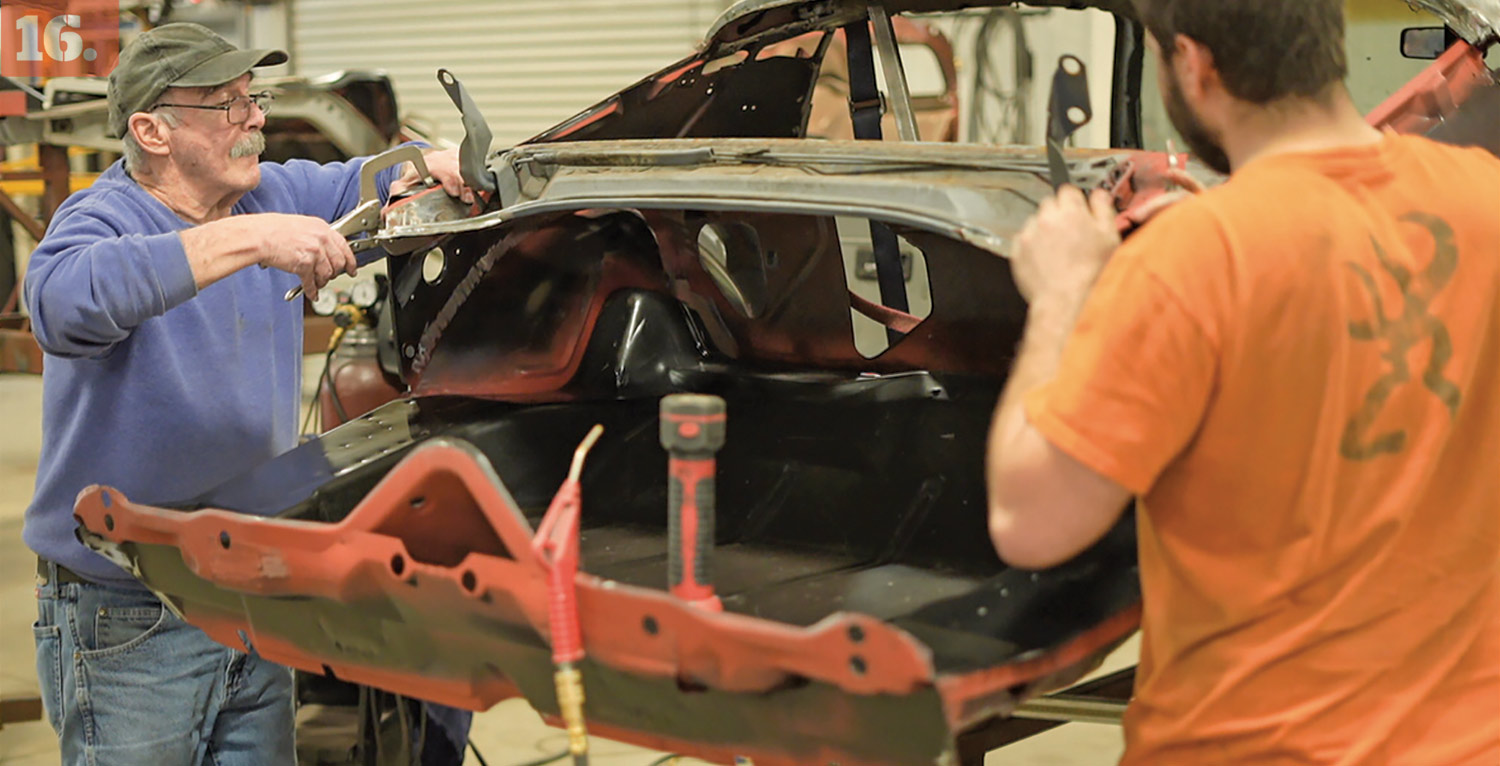
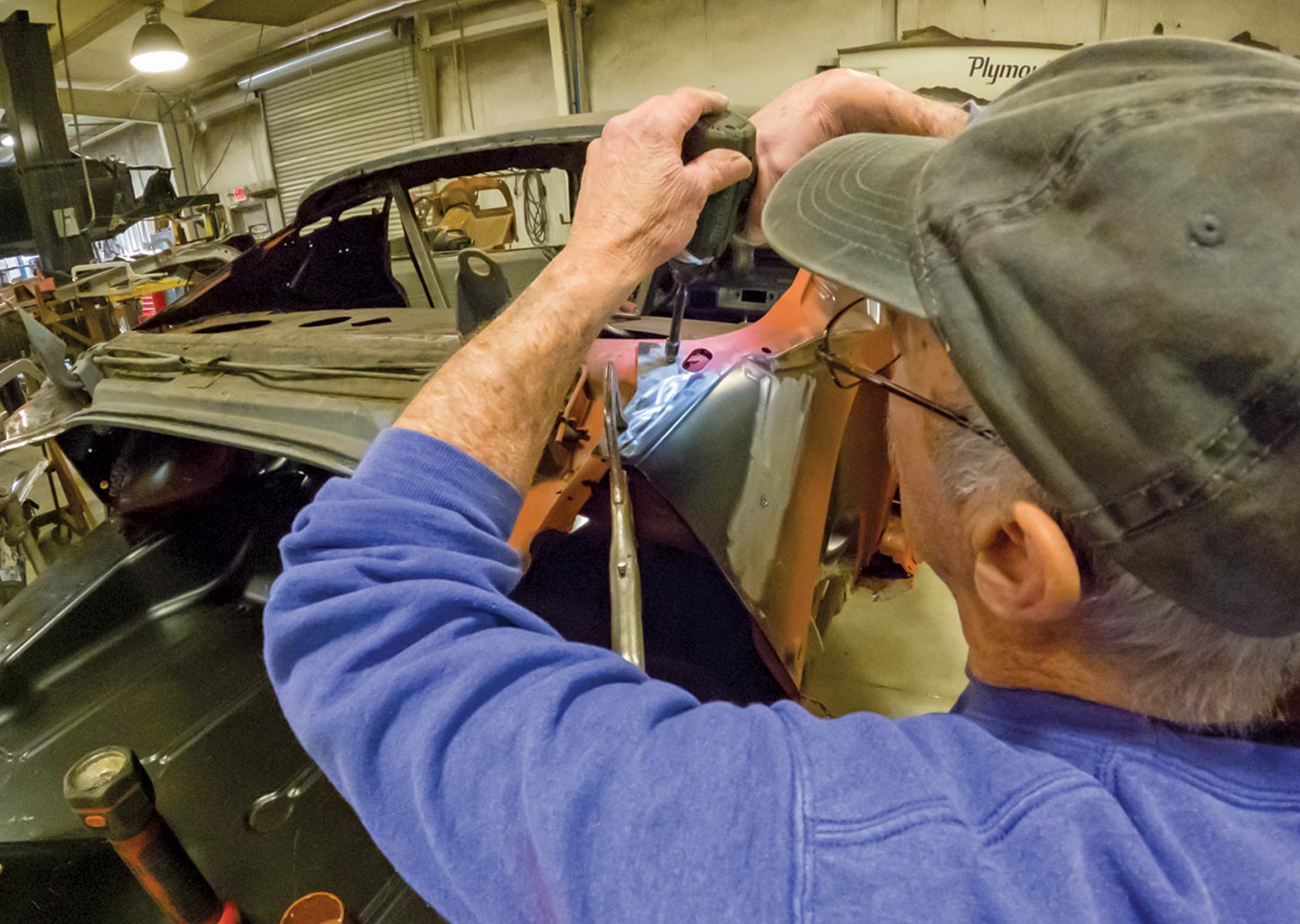
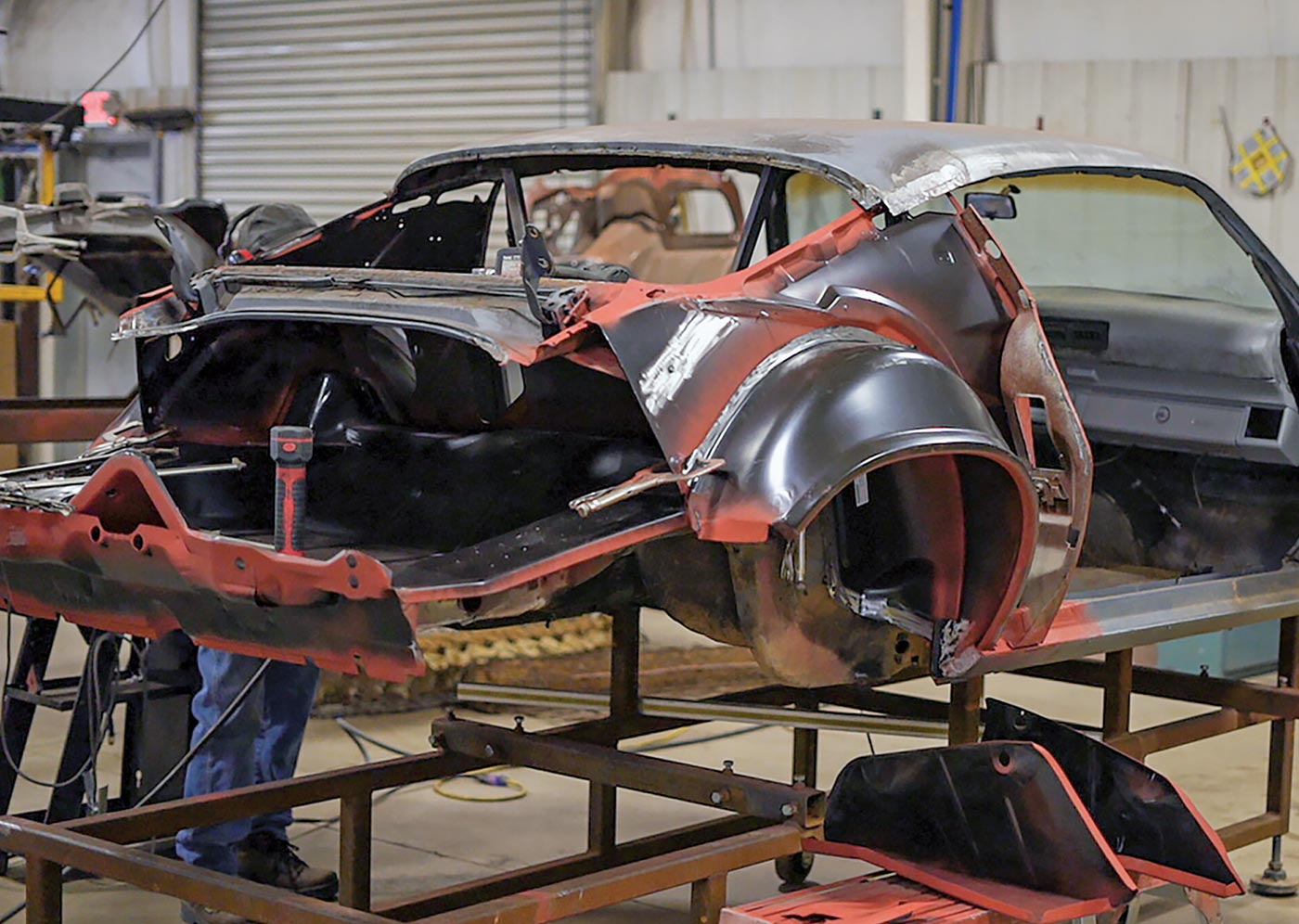
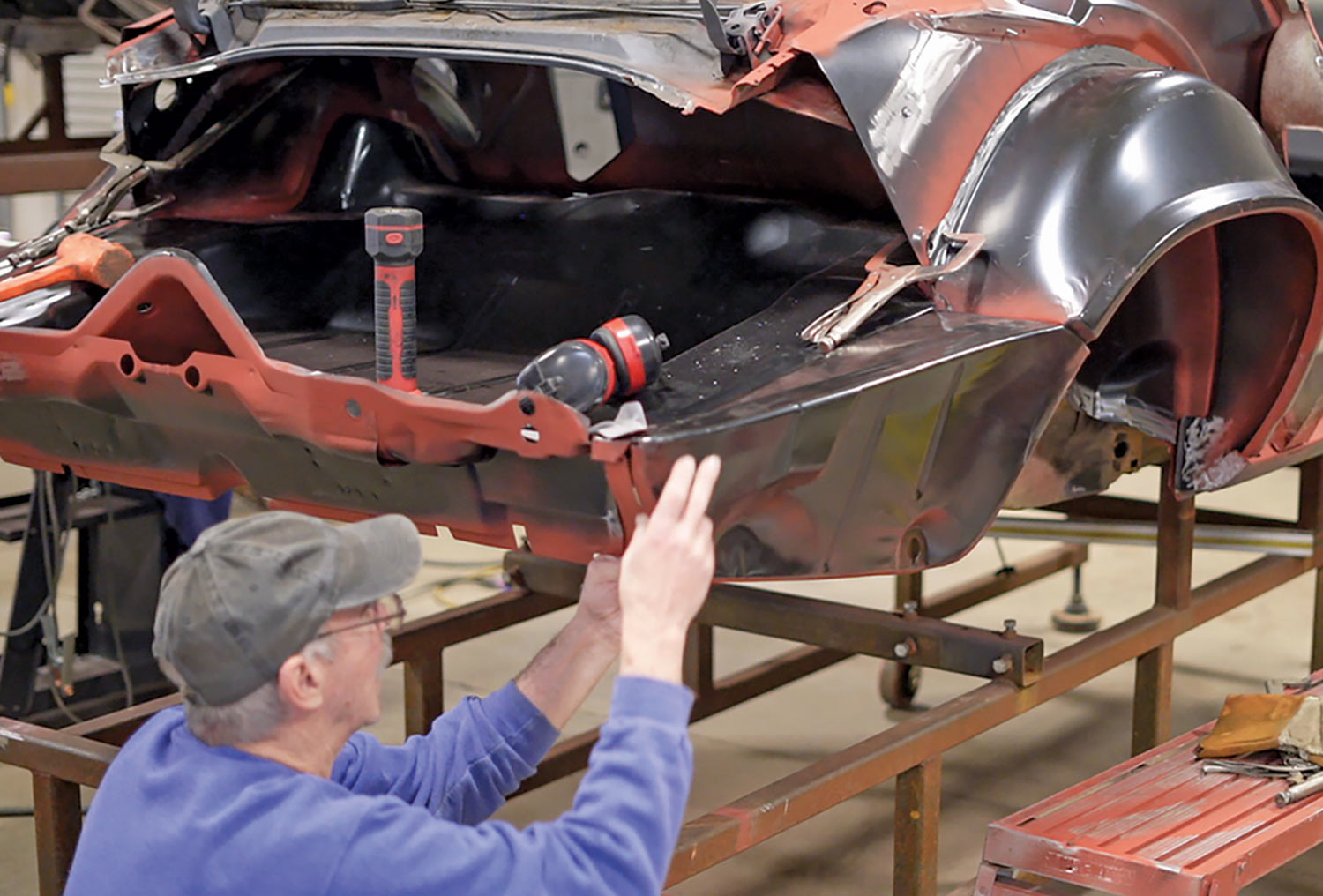
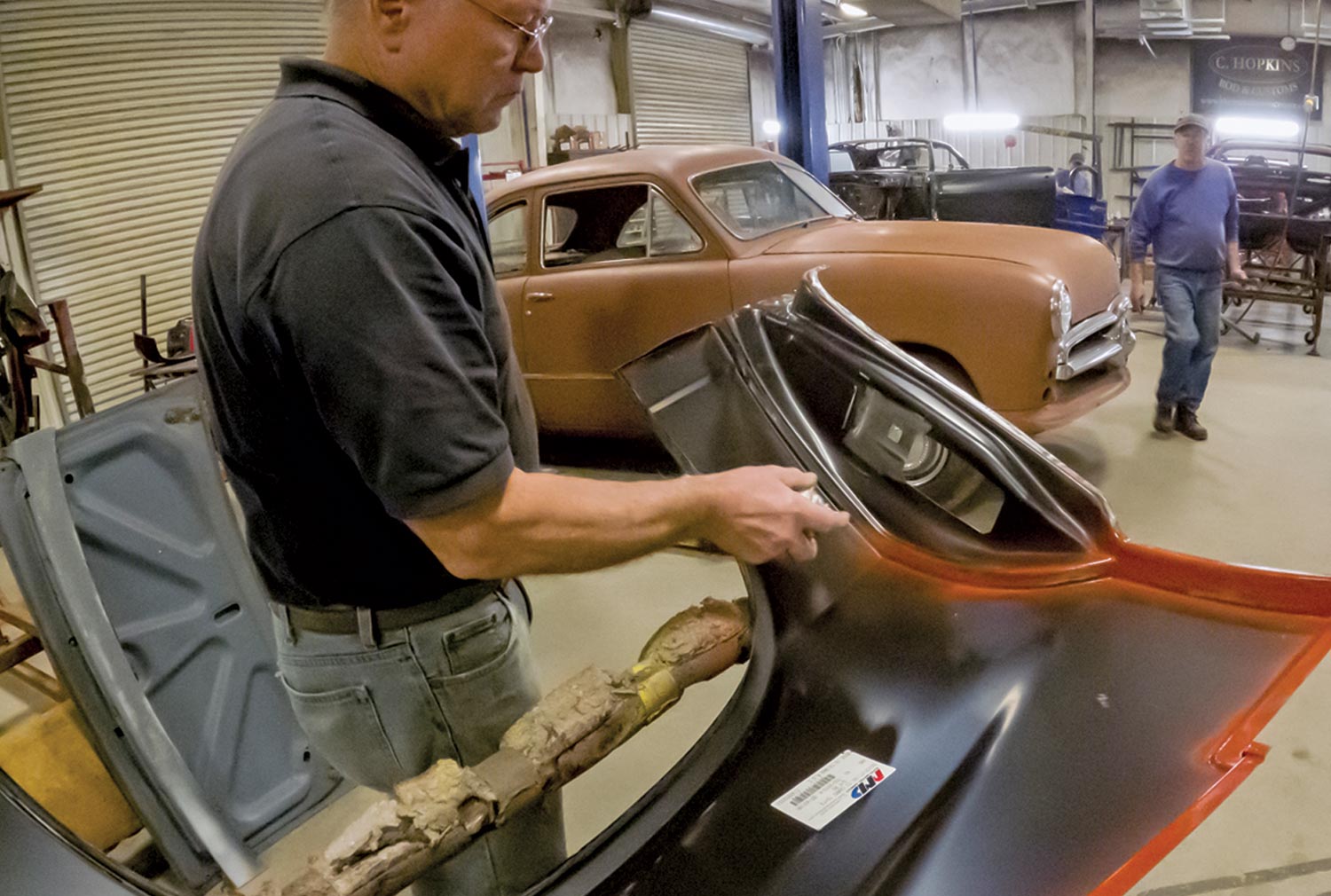
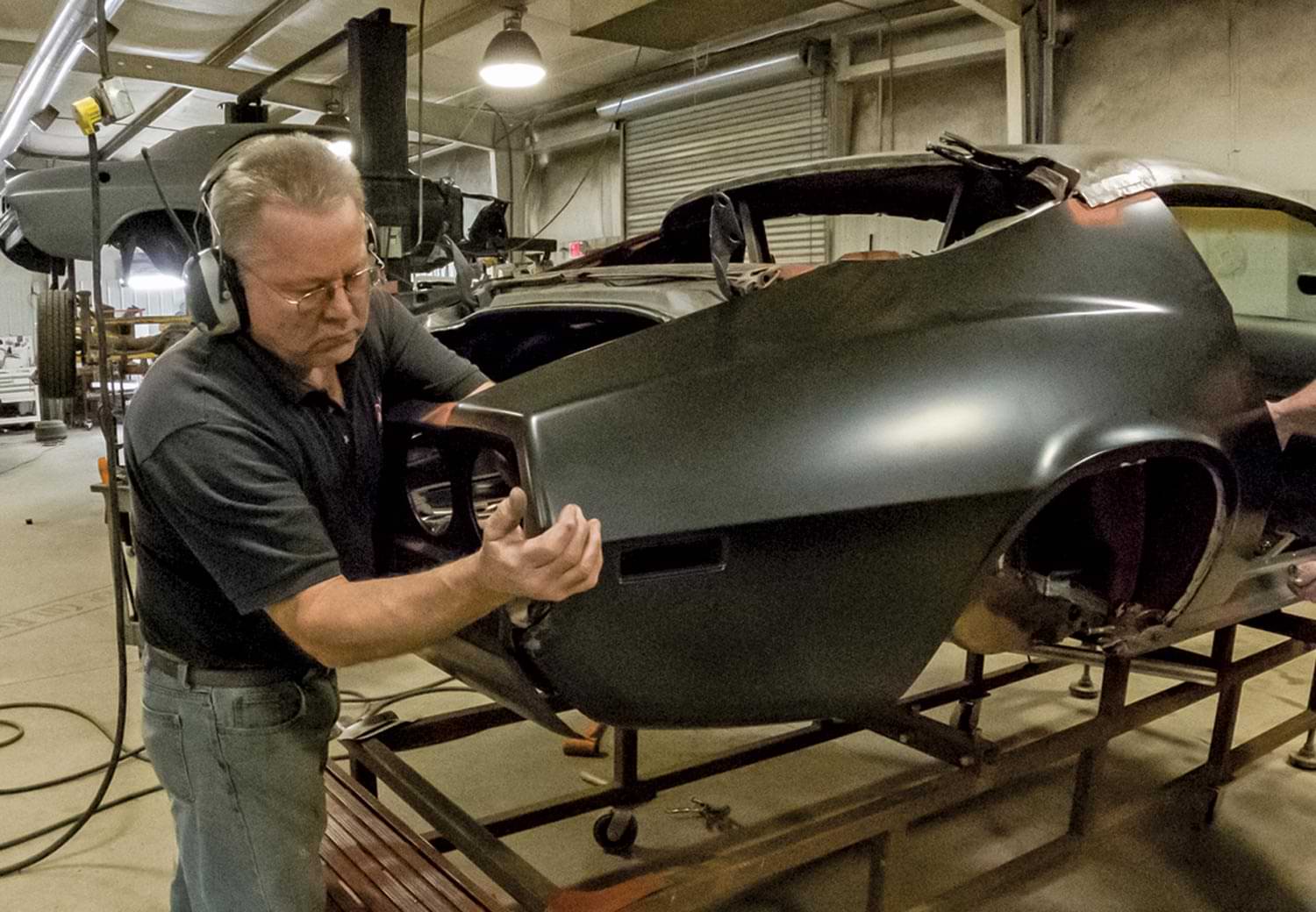
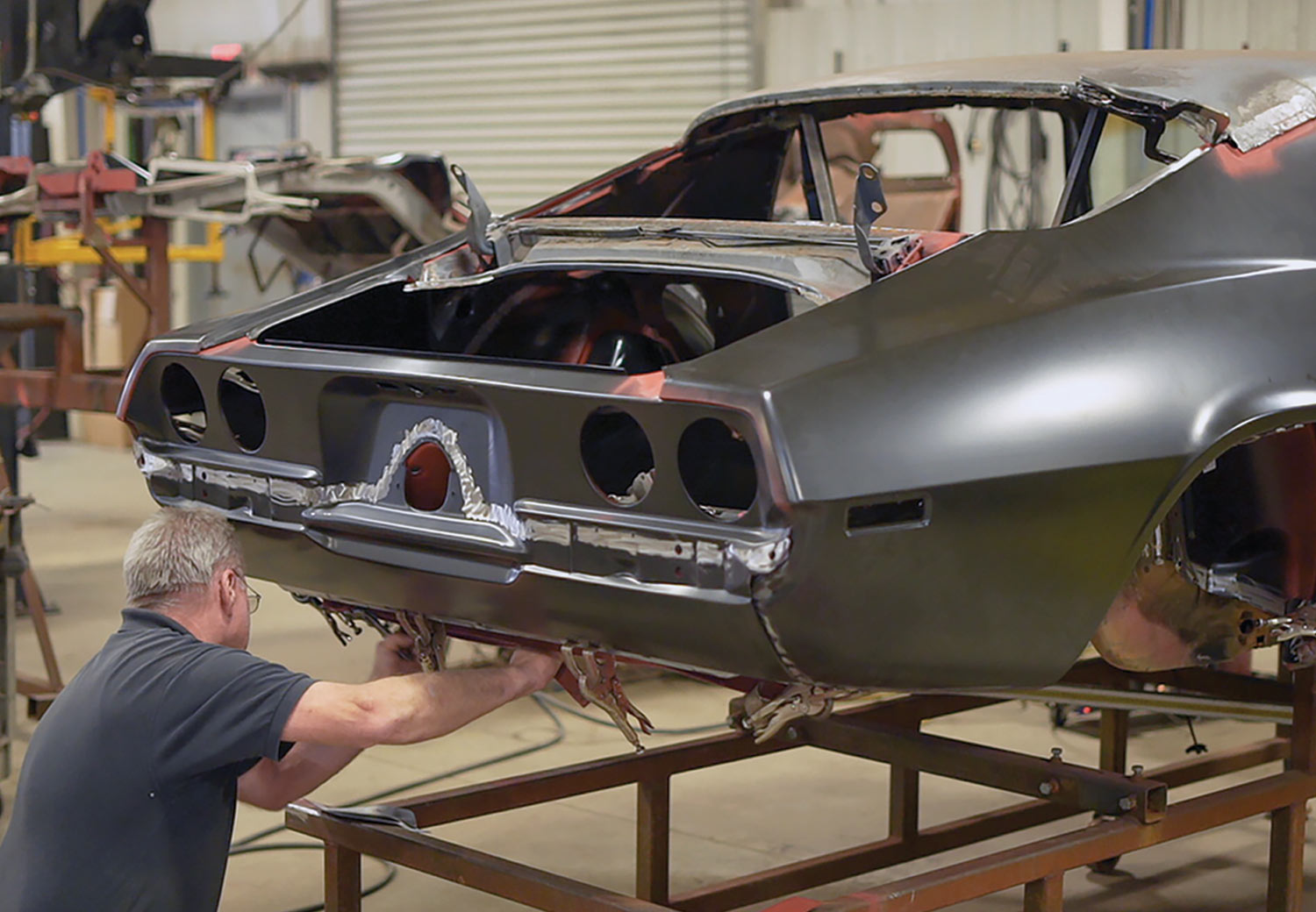
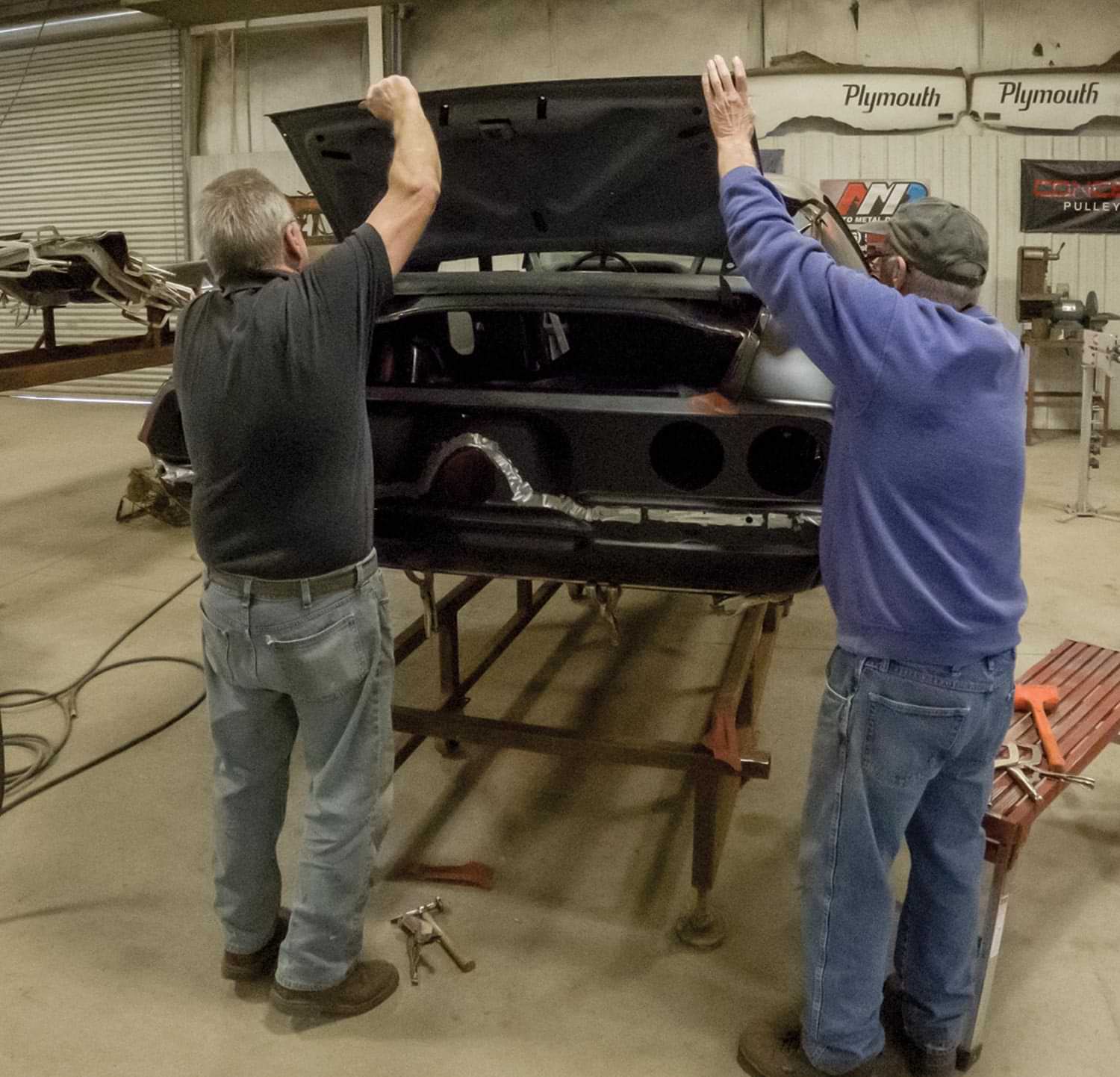
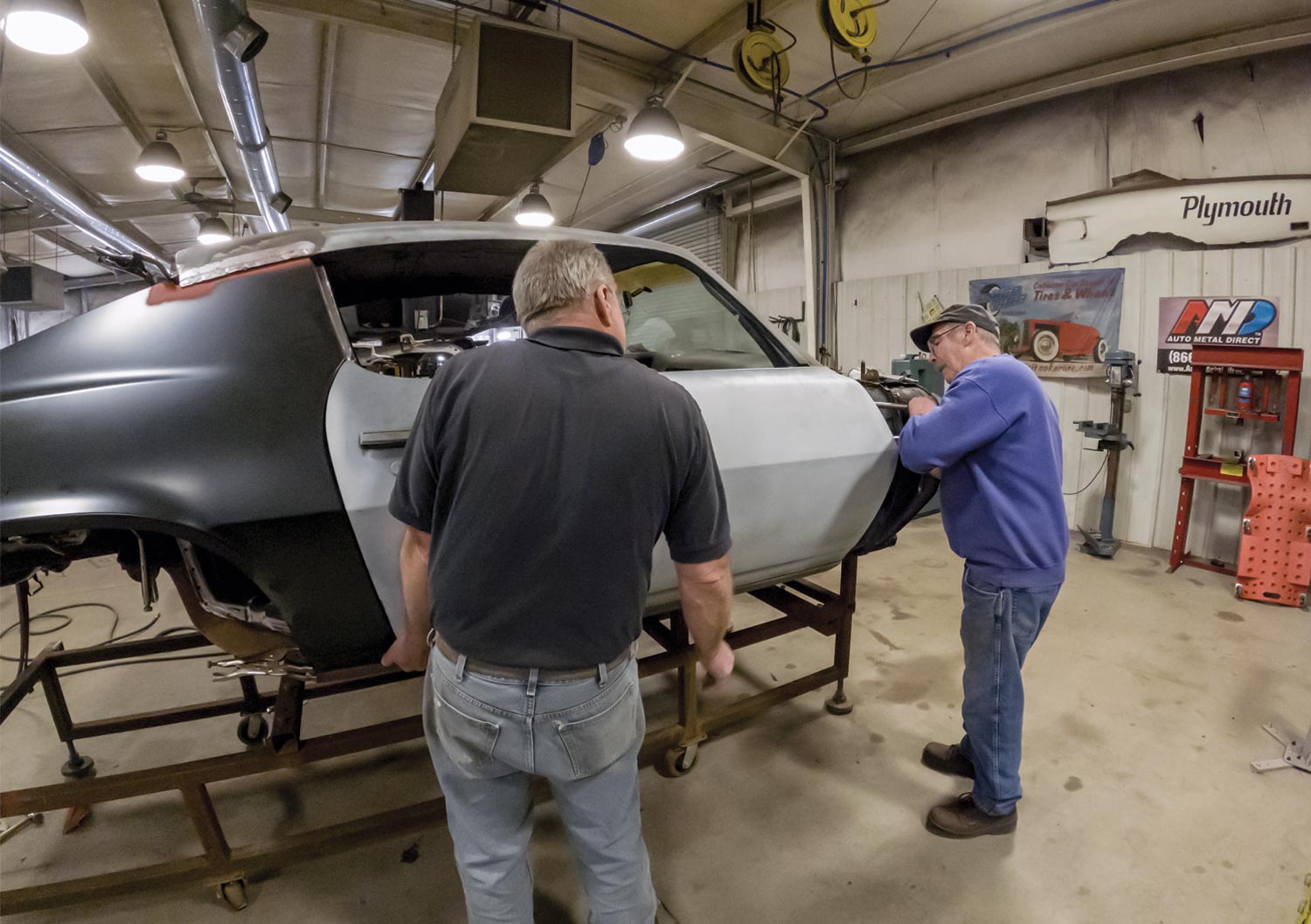
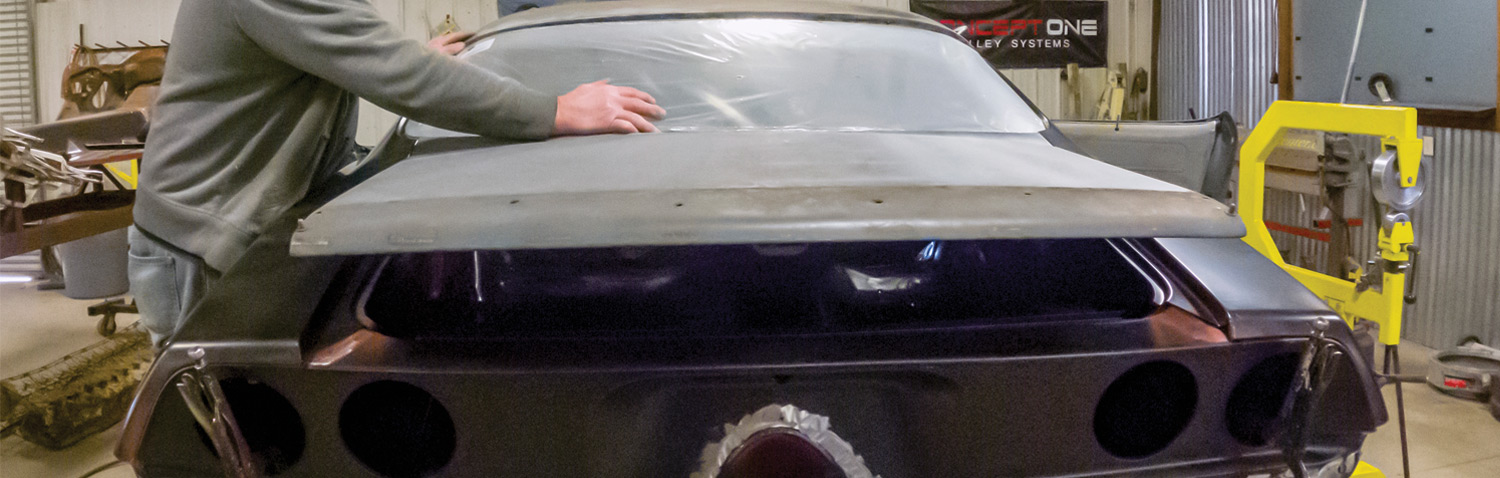
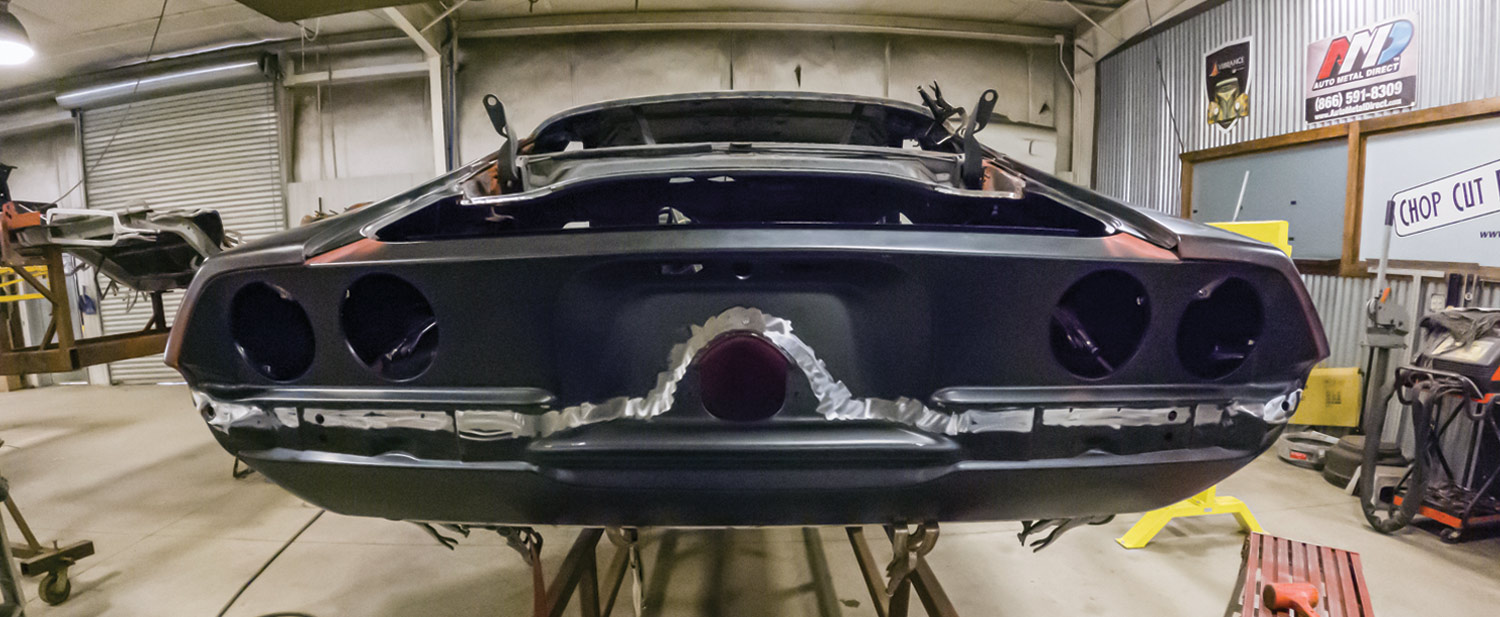
