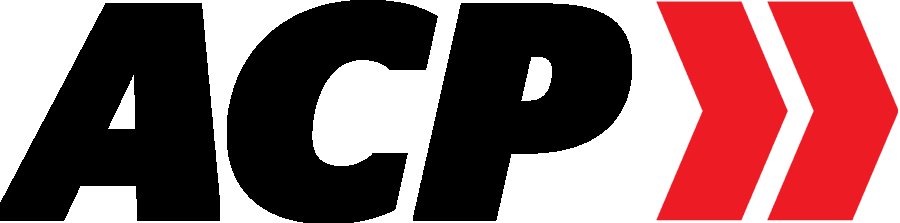
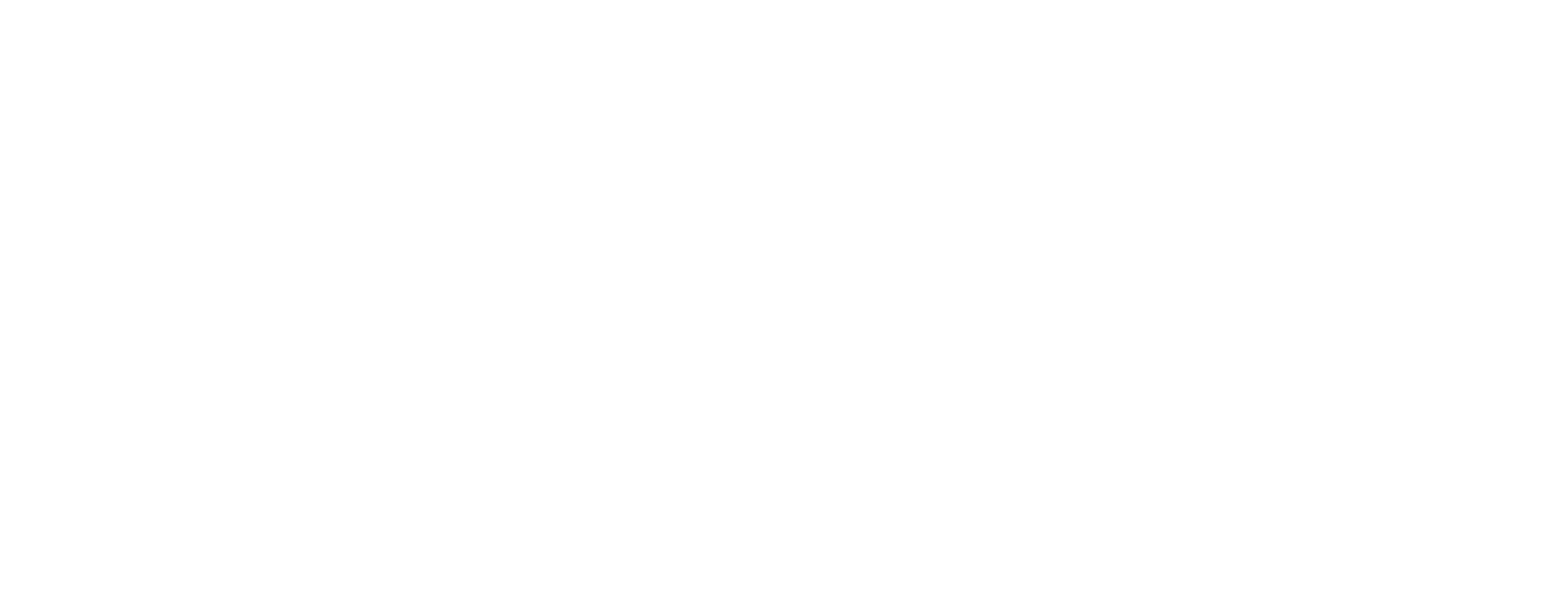
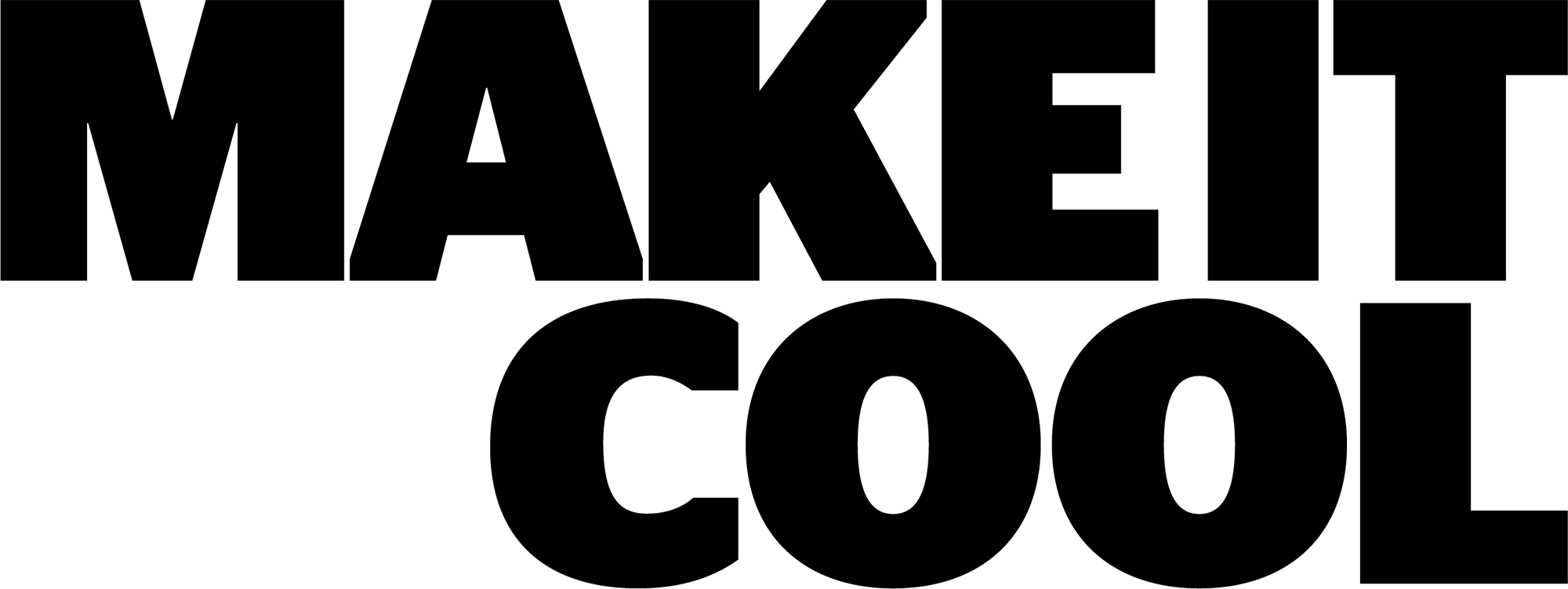

hen it comes to cooling a Tri-Five Chevy, the options are all over the map. Stock radiators typically need repairs, and they’re usually not efficient enough to cool most high-performance engines. For the past 20 years or so, it has been popular to swap the original copper and brass radiator for an aluminum unit. While aluminum radiators are physically lighter and do a good job of cooling, there is no replacement for a tried-and-true copper and brass radiator when it comes to durability and longevity.
Many years ago, Vernon Walker and the folks at Walker Radiator Works in Memphis, Tennessee, developed trick internal components that allowed brass and copper radiators to outperform most radiators on the market. Walker was known mostly for street rod radiators but later got into the ’50s and ’60s applications, including the Tri-Five Chevy. Shorter fins allow for more tubes to increase capacity, while louvers in each fin create air direction changes for much better cooling capability.
When Walker closed its doors, hot rod builder Alan Johnson bought the entire operation, including all the machinery, patterns, and notes that dated back for decades of design and production. The name wasn’t part of the purchase, so he renamed it Johnson’s Radiator Works and moved the machinery to a facility near his hot rod shop in Gadsden, Alabama.
Johnson and his staff take great pride in building radiators for a 70-year span of vehicles, from Model Ts to ’90s Chevy pickups and everything in between. We recently had the chance to watch the team build a Tri-Five radiator and it was eye-opening to see exactly how much work goes into each radiator. It is truly a handcrafted piece. Johnson’s Radiator Works builds every component, aside from the drain petcock, in-house. While there has been a learning curve on the intricacies of manufacturing radiators for so many different applications, each member of the staff knows every step of the process.
Follow along as we show you how Johnson’s Radiator Works builds a highly efficient radiator that will bolt directly into a Tri-Five Chevy and keep it cool with traditional copper and brass construction.


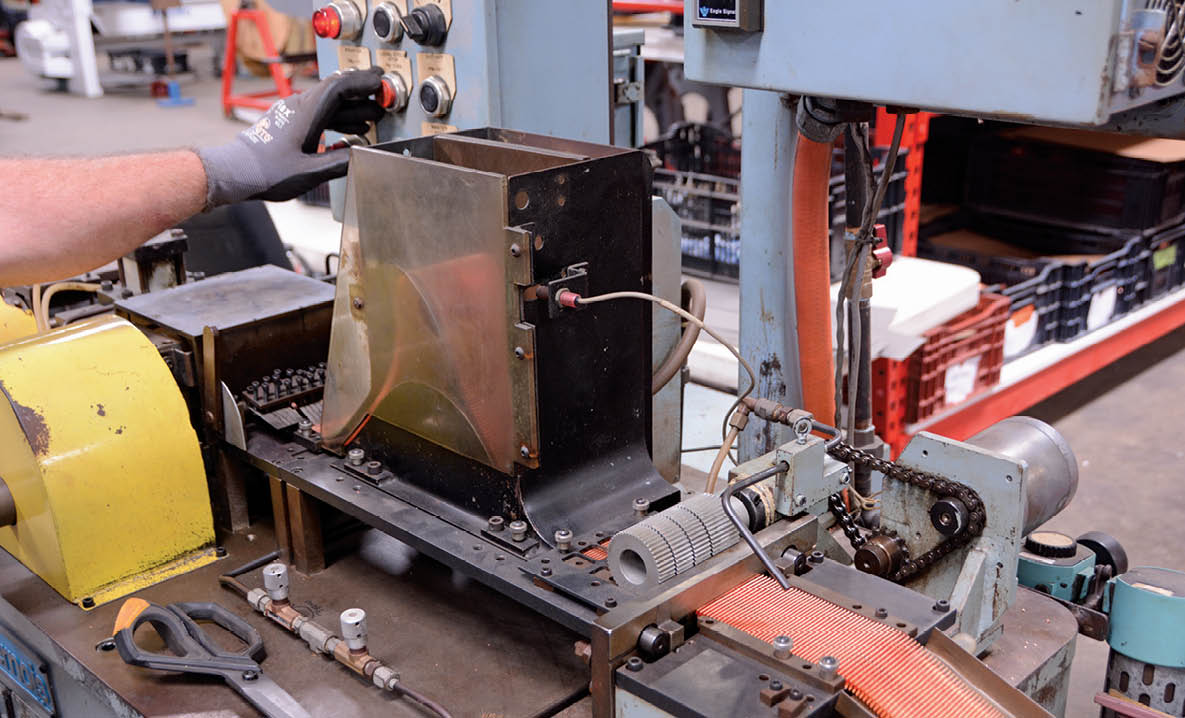

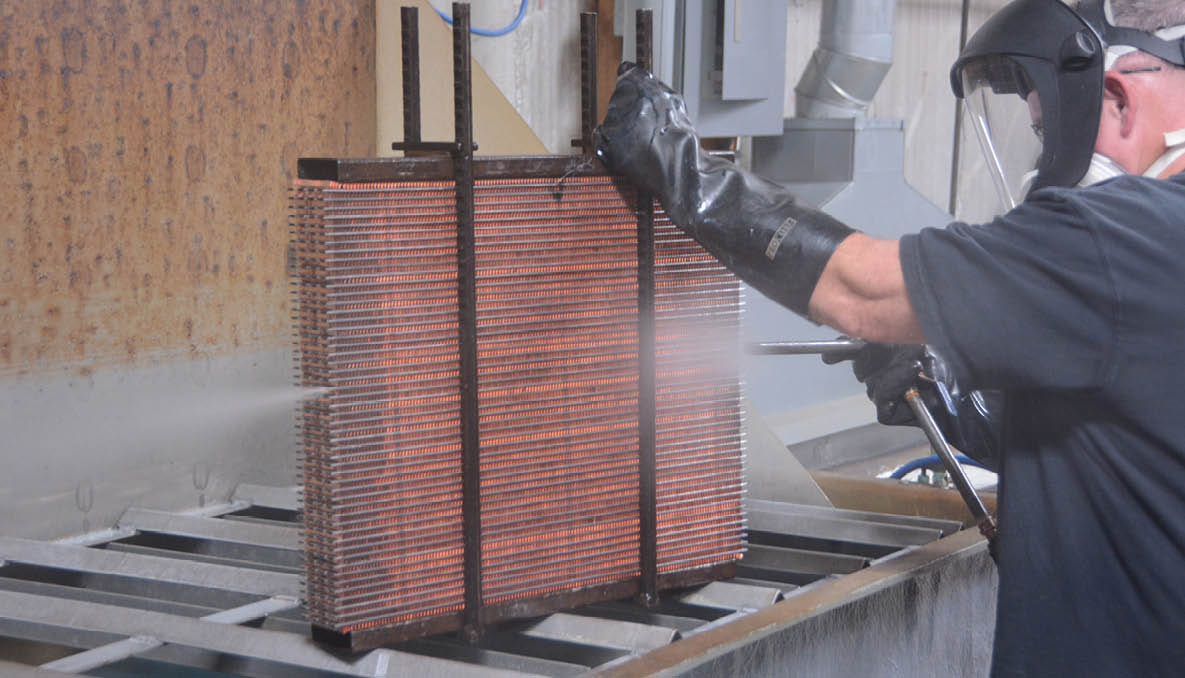

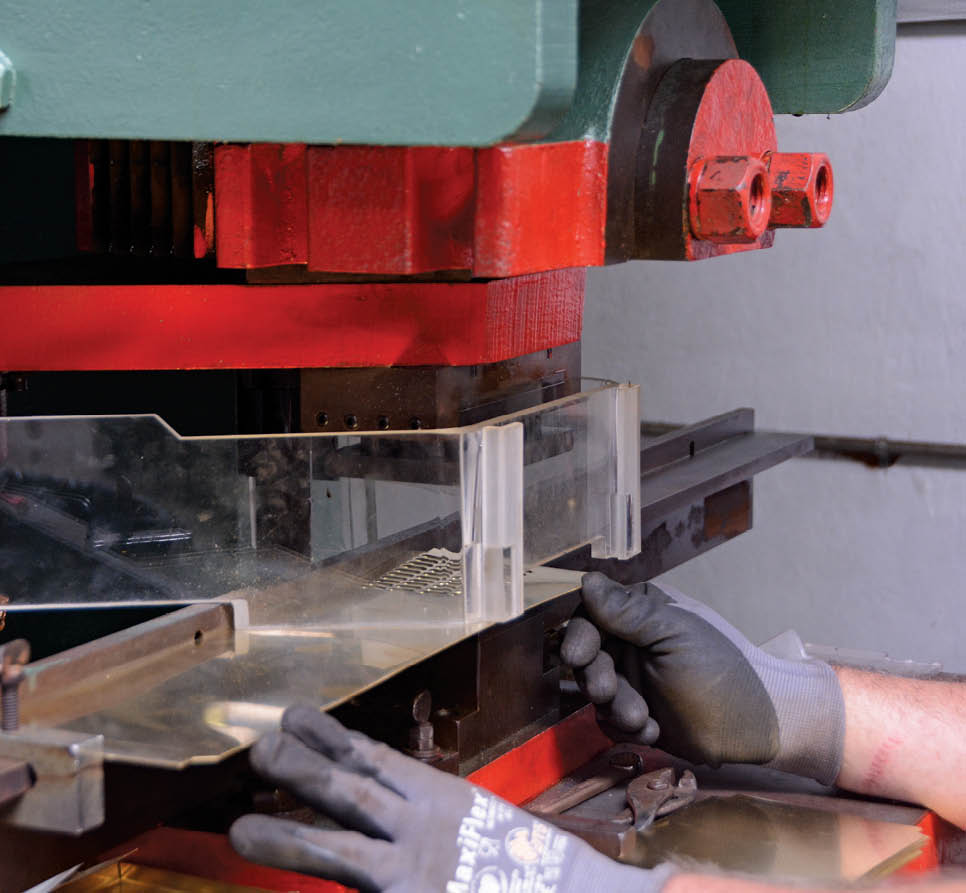


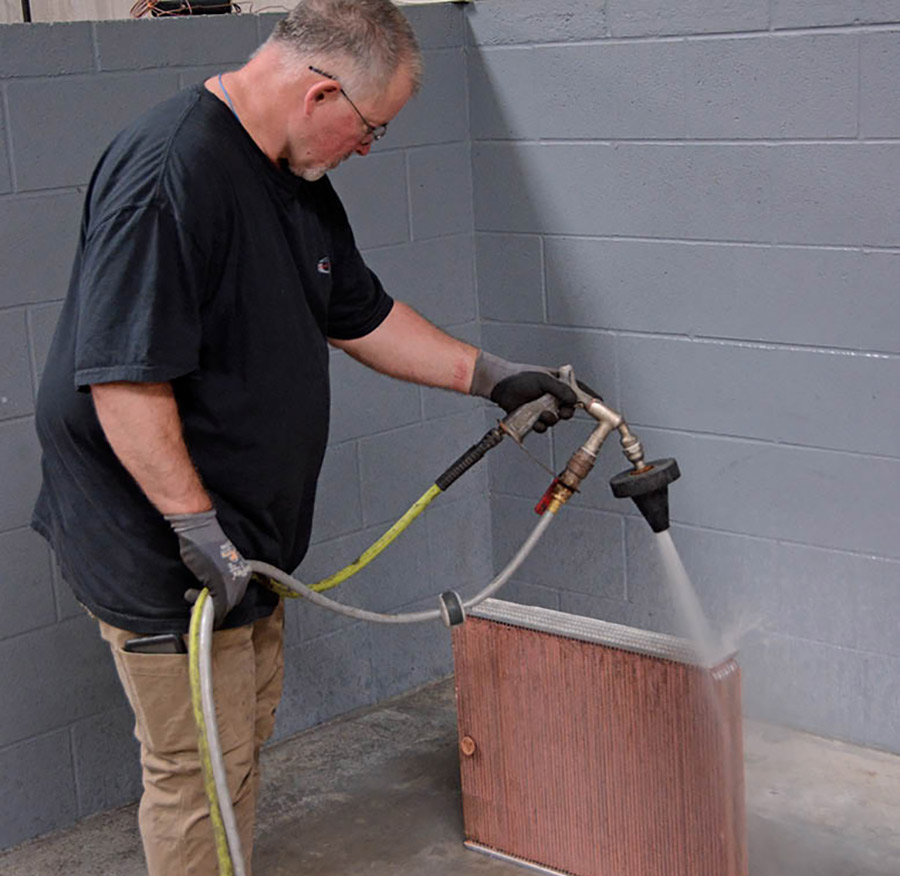
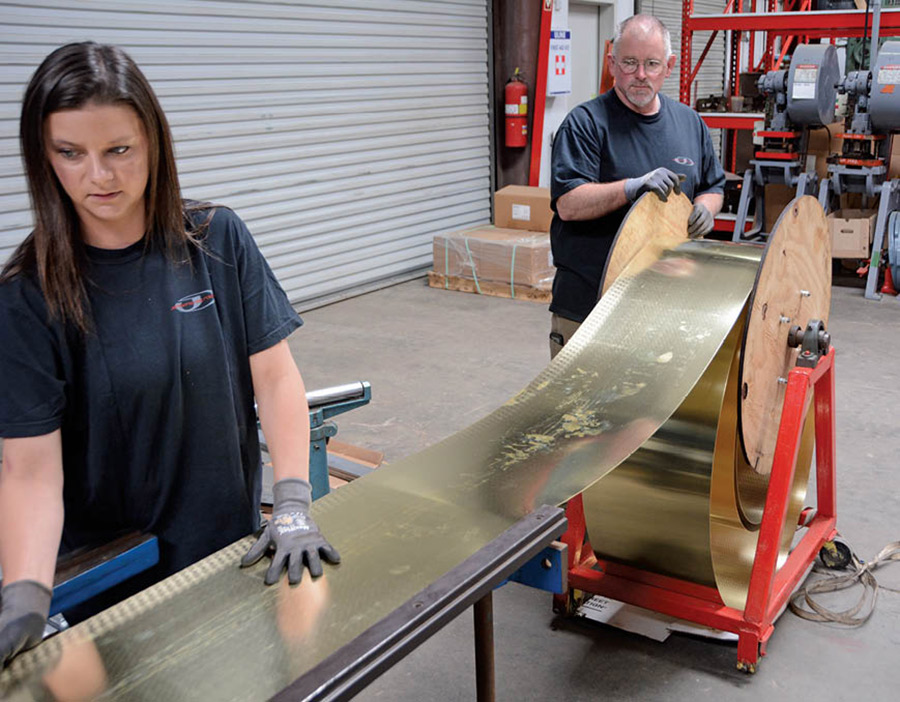

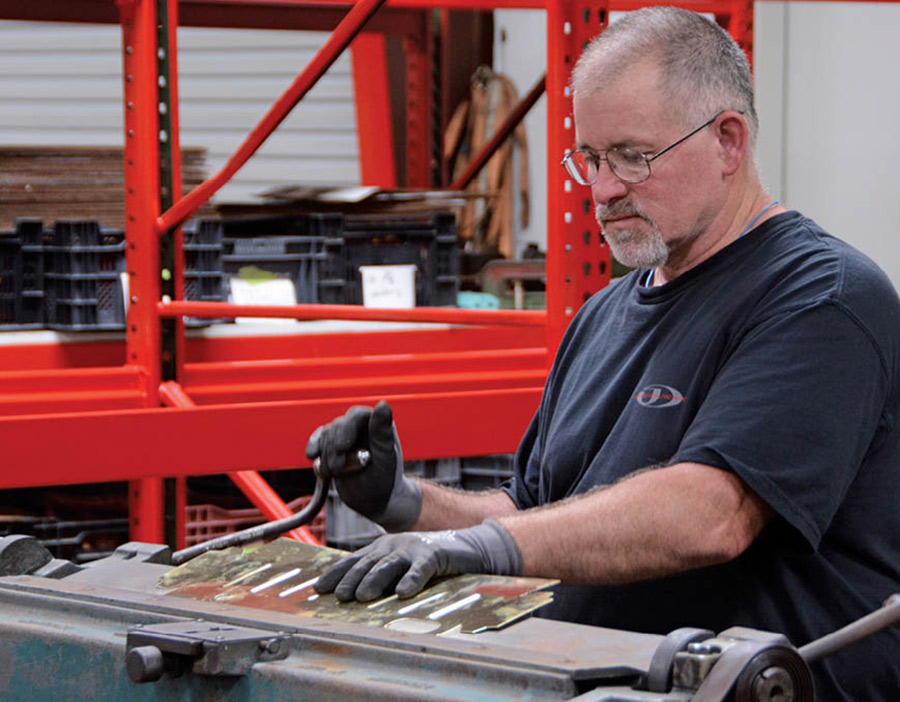

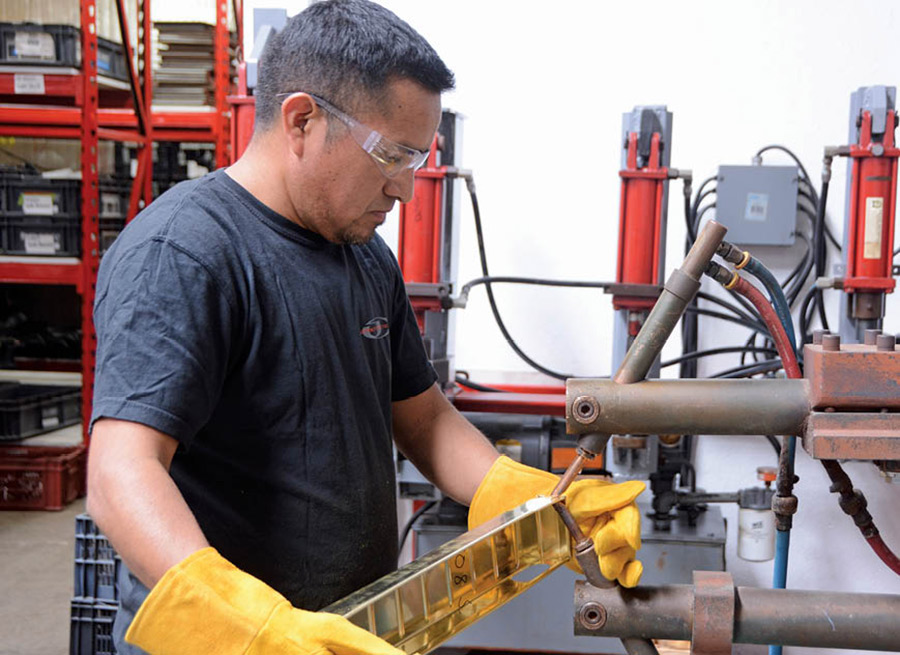
16. Jacob Gomez uses the spot welder to fasten the corners of the tank. The seams will be brazed on the inside and then filled with solder on the outside during the final assembly process.


18. The filler neck hole is punched with a special die that creates a tight fit with the neck, which is made in-house.


20. Alan Johnson brazes the inner tank seams, and then brazes the lower radiator hose outlet for a strong bond.
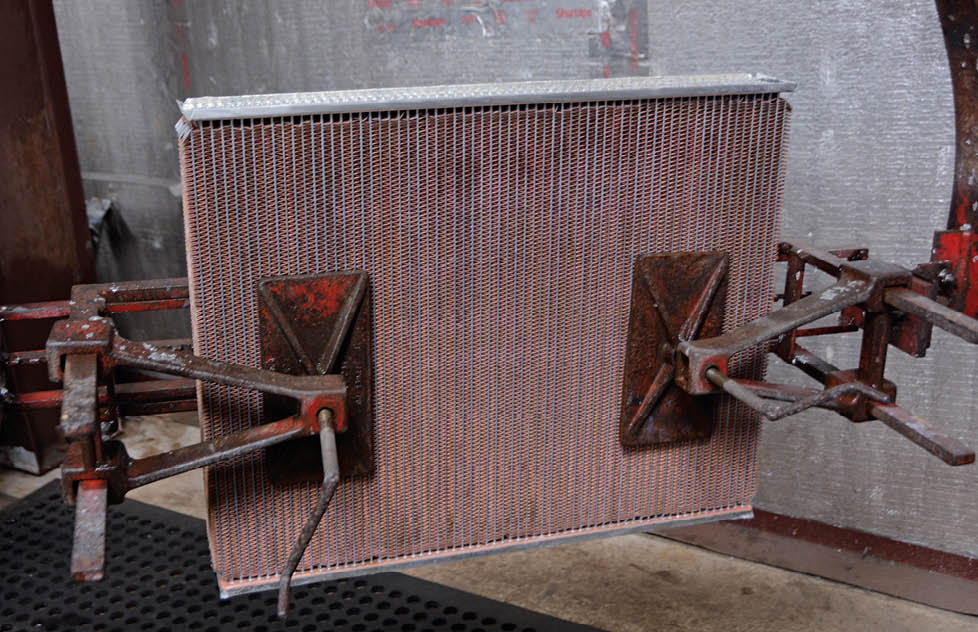

22. Johnson fits the lower tank into the header panel and then hammers the flanges down for a tight fit. Then, it’s time to fire up the torch and solder the joints.
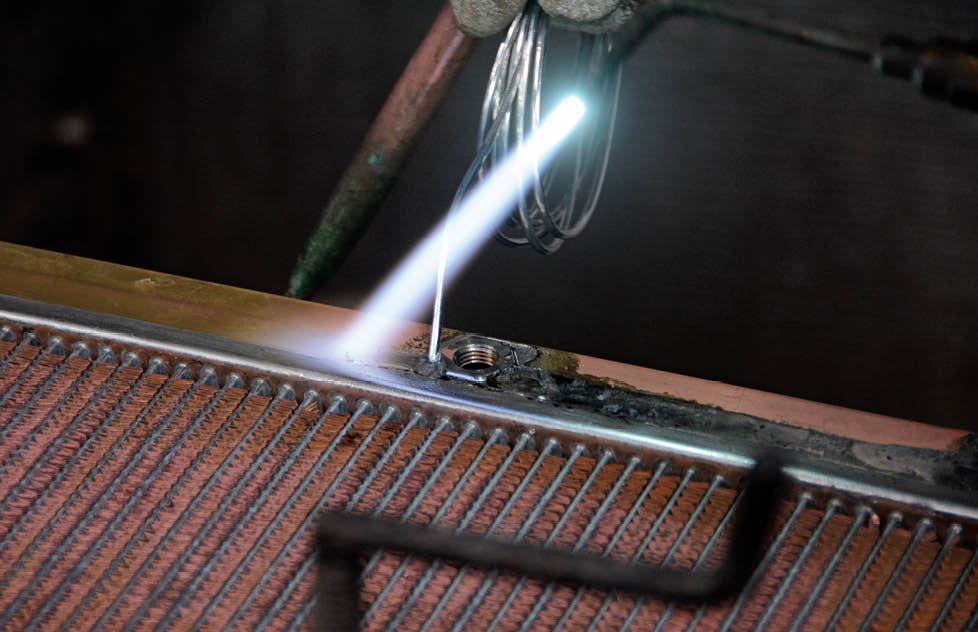

24. Johnson fits the stamped upper tank to the header panel and fine-tunes the fitment with a few soft blows of the hammer.


26. The upper radiator hose outlet fits tightly in the punched hole and then Johnson secures it with solder for a long-lasting bond.


28. Every radiator build is pressure-tested before it is painted and boxed for shipping. Johnson’s radiators are designed to operate with a 15- to 18-pound cap, so he applies 20-plus pounds during testing.

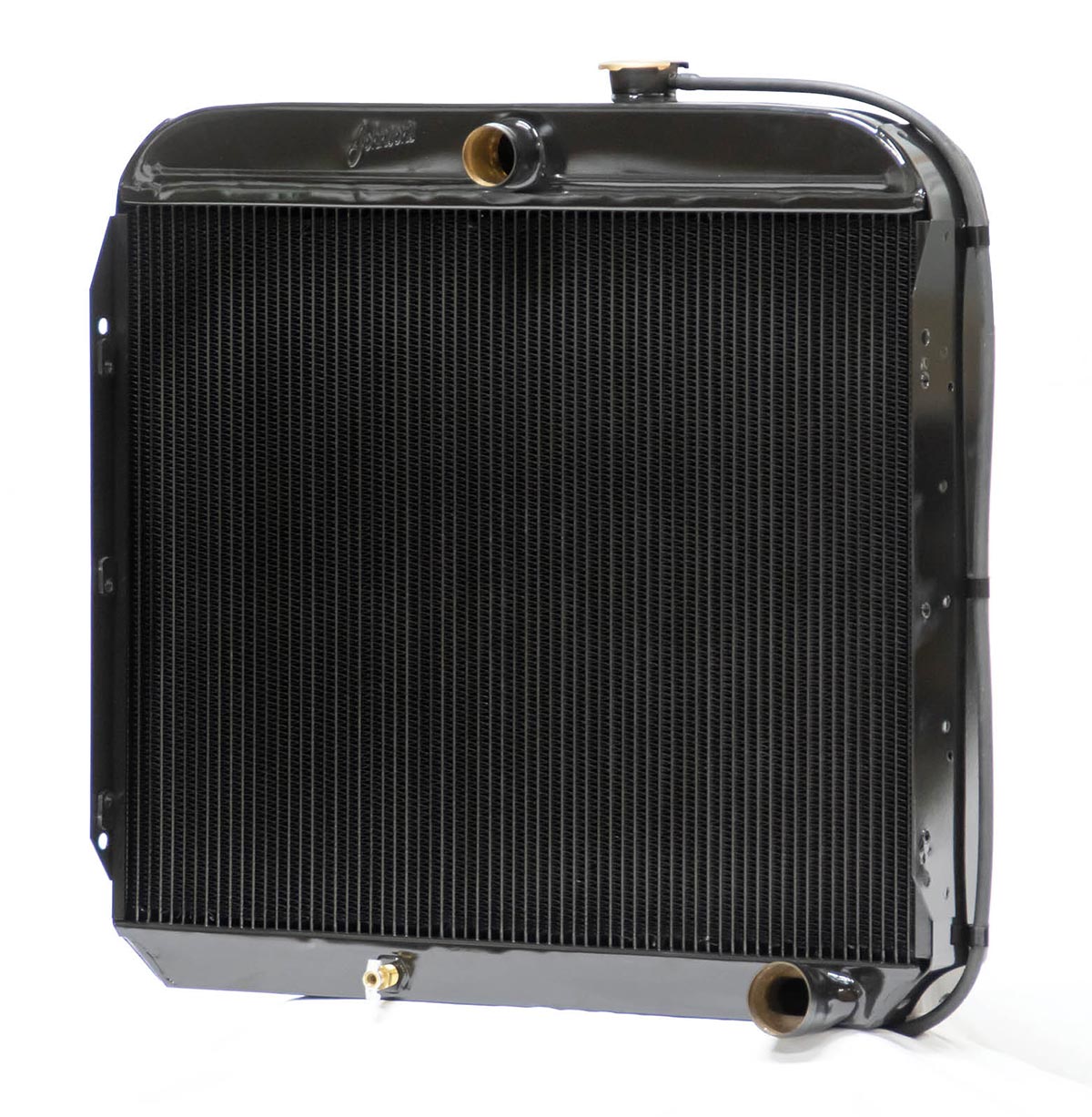
