TECH
InTheGarageMedia.com

BY Jeff Huneycutt Photography by The Author
n a perfect world, every car build starts out with a brand-new rolling chassis from Roadster Shop, Art Morrison, Scott’s Hotrods, or some other quality builders. But, in our world, that dream will just have to live in our heads a little bit longer.
Still, there are things you can do on a limited budget to help bring an old chassis back to life. That’s exactly what we were faced with when we dragged this ’80 Corvette home. The engine was shot, the transmission and most of the interior was missing, and, generally speaking, it was a basket case. But we got it for a good price, and the birdcage seemed to be in good shape—if you know anything about old Corvettes, that’s a big deal. So, it seemed worth saving.
This project, however, is experiencing severe mission creep. Chevrolet switched from fiberglass to steel floorpans in either 1976 or 1977, and the steel floors in our ’80 were severely rusted. In order to get the floors cut out and replaced properly, we decided the body needed to come off the chassis to create enough room to do it right.
That, in turn, freed up the chassis for a closer inspection. It definitely had a few areas where rust repairs were needed, and a solid coat of surface rust did nothing for its looks. Obviously, we had to go all the way by unbolting the suspension and stripping it down to bare metal before fixing those few rust spots, right?
See, mission creep.
So, while the rotten floorboards were totally ignored, we started yanking everything off the chassis for a complete refurb. The good news here is there is much that can be done to bring a chassis back to spec with minimal cost—as long as you are willing to put in some elbow grease. Plus, nothing we are discussing here is specific to the Corvette. It all applies to any Chevy product, from a Camaro to a C10. Of course, a unibody car like a Camaro means you can’t pull the body off the chassis, but you can still strip and coat the underside to protect it from rust for years to come, like we’ll do here.
Besides fixing rust, a major part of this chassis refurb will be coating the metal to protect it from oxidation and additional rust damage in the future. A fresh coat of paint is better than nothing, but it has to be constantly protected or it won’t last. Powdercoat is even better when it comes to protecting a car’s chassis and underbody, but it requires immaculate preparation of the steel—including complete rust removal—and it can get pretty expensive.
Our solution needed to check all the boxes. We didn’t want to deal with the wait of sending stuff out so it has to be something that can be done in the typical home shop. It has to be cost effective. And most of all, it has to be an absolutely excellent long-term protectant against rust, road grit, and a wide variety of chemicals.
So, we went with a kit from POR-15. The “POR” stands for “Paint Over Rust,” which you can literally do. That’s because even though it can be applied with either a brush or sprayed on, this stuff isn’t paint. Almost all paints dry by using a volatile organic compound or even water that evaporates out, causing the paint to harden. POR-15, however, actually cures by absorbing moisture out of the air, and the end result is a sort of shell around the metal that is quite hard and impervious to moisture. That also means that no moisture can get to the steel to cause additional oxidation.
How does a material become impervious to moisture by absorbing moisture? I don’t understand it myself. Black magic? All I know is it works, POR-15 uses its own in-house chemists and it’s made right here in the USA.
You can follow along with the process in the photos and captions that go with each, but we can tell you the results turned out excellent. We’ve heard others complain about the product, but the “failures” are almost always the result of one of two mistakes.
Probably the most common mistake is improper surface prep. Yes, the POR does stand for paint over rust, but it doesn’t mean you can also paint over dirt or grease. The metal to be coated must be properly cleaned so that the POR-15 can properly adhere to it. This also means that any loose rust must also be removed, either by sandblasting or wire brushing. That’s why we always recommend using one of POR-15’s kits that includes not only the POR-15 product itself, but also a cleaner/degreaser and a metal etch. This not only properly cleans the metal but also ensures that it has some texture so that the POR-15 can chemically bond with the surface and not flake off over time. You can put POR-15 directly on rusted metal, but the results will almost always be better if you use a degreaser and etching product to ensure you’ve got the best surface for it to adhere to.
Second, POR-15 can sometimes be blamed for failing when it isn’t properly protected. POR-15 is extremely resistant to moisture, scratching, and chipping, but it doesn’t handle the sun quite as well. If POR-15 is exposed to UV rays, it can break down or get “chalky” over time. Fortunately, the solution is simple: If whatever you apply POR-15 to is somewhere it can be exposed to the sun, just apply a topcoat to protect it. You can use regular paint, or POR-15 also sells several topcoat products depending on the application.
So, check out our chassis revival. The process of patching up the rust didn’t go perfectly, but we’re very happy with the results of applying the protective coating and confident the chassis is ready for many more years of service.
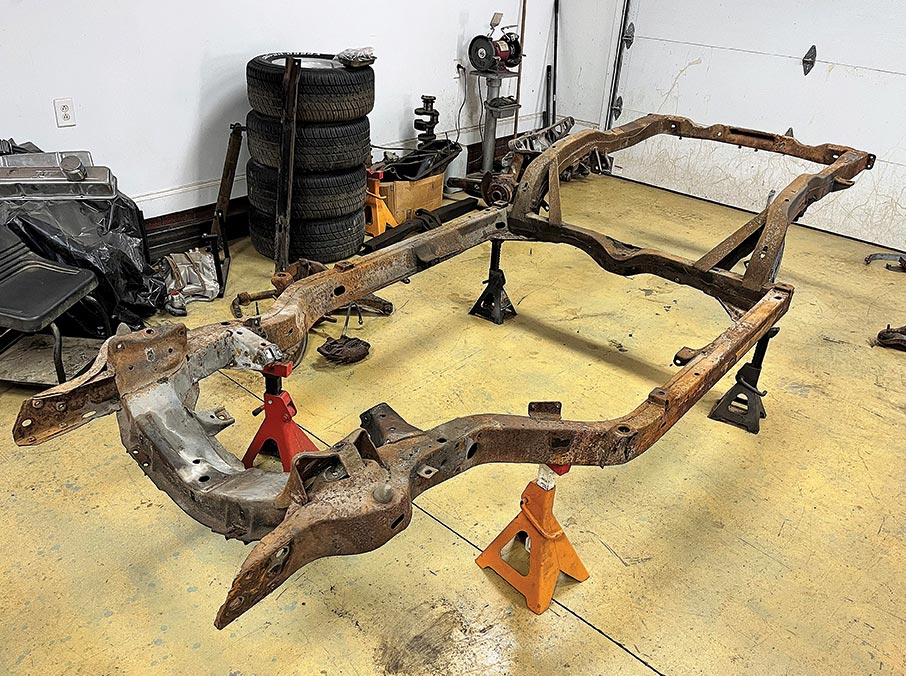
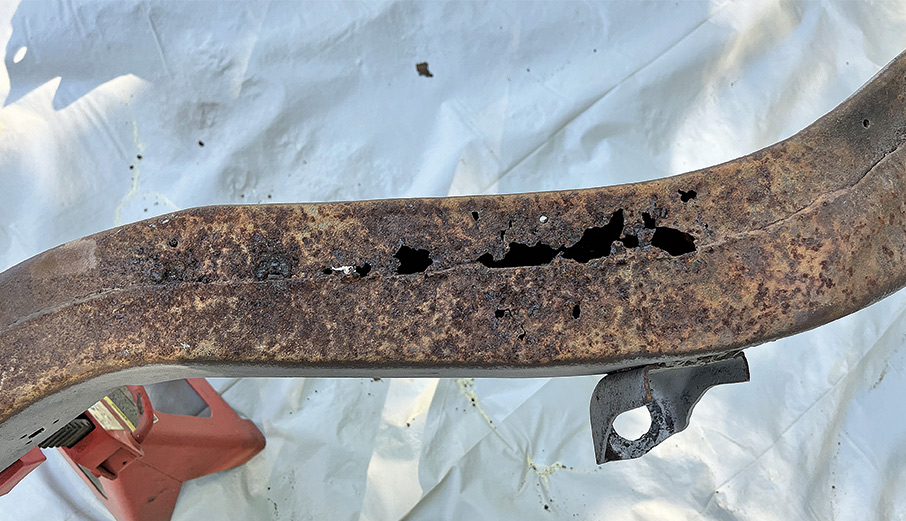
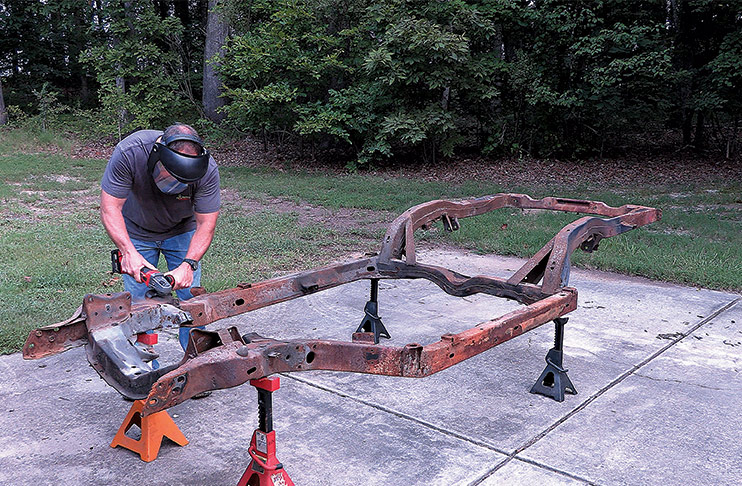
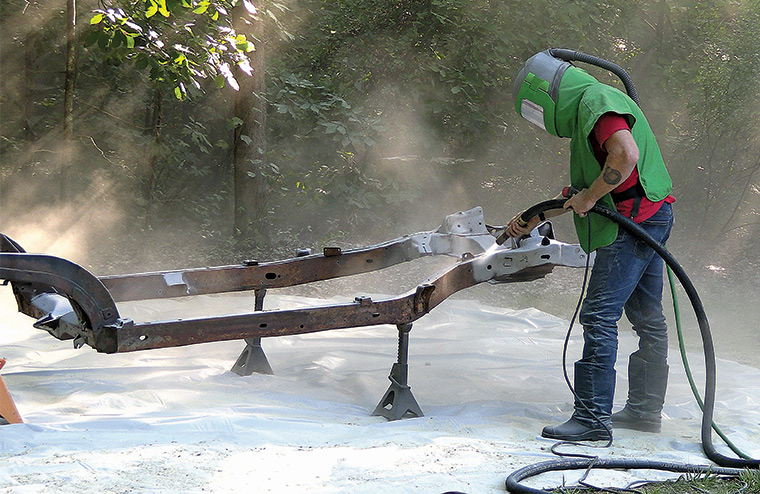
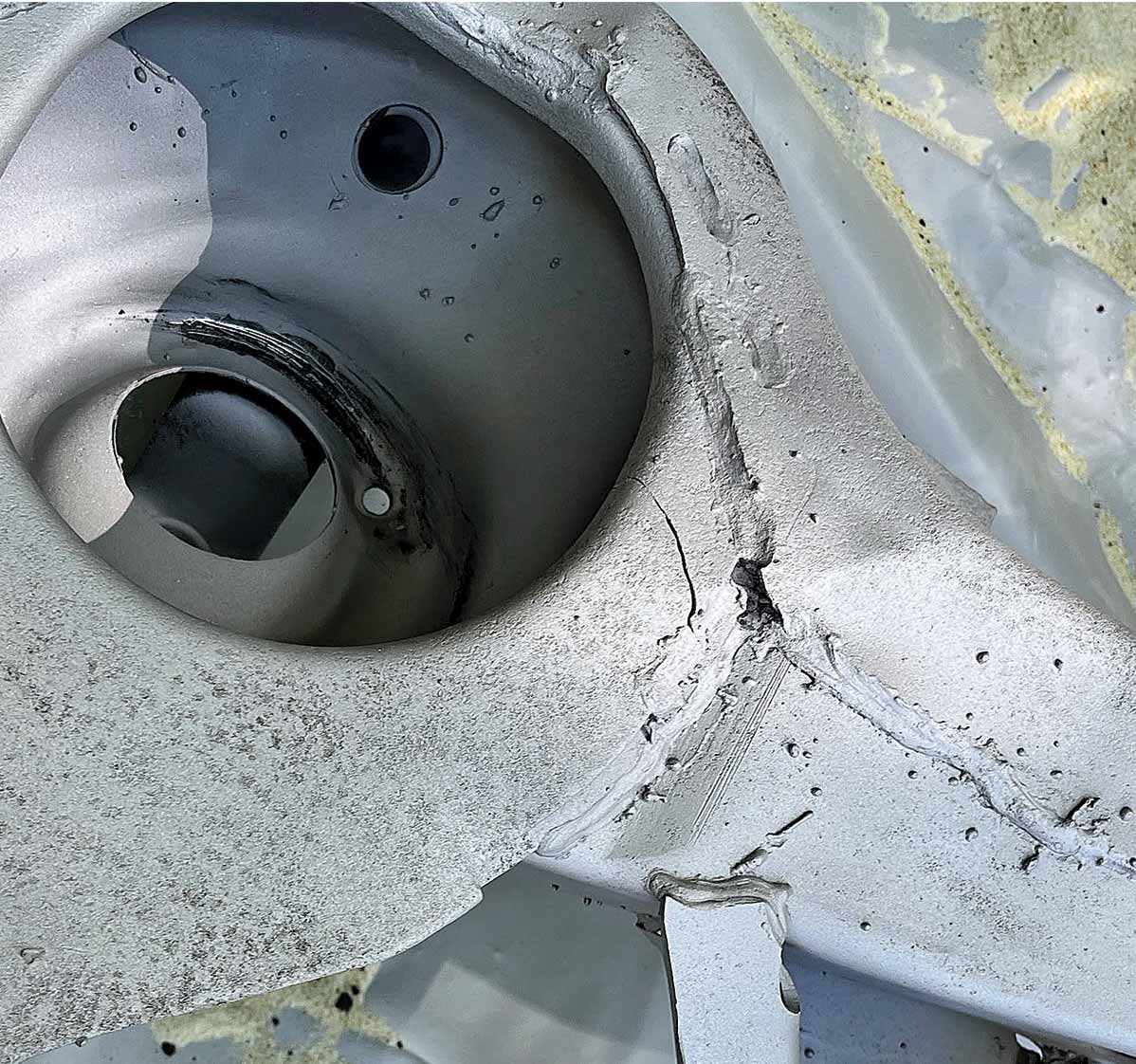
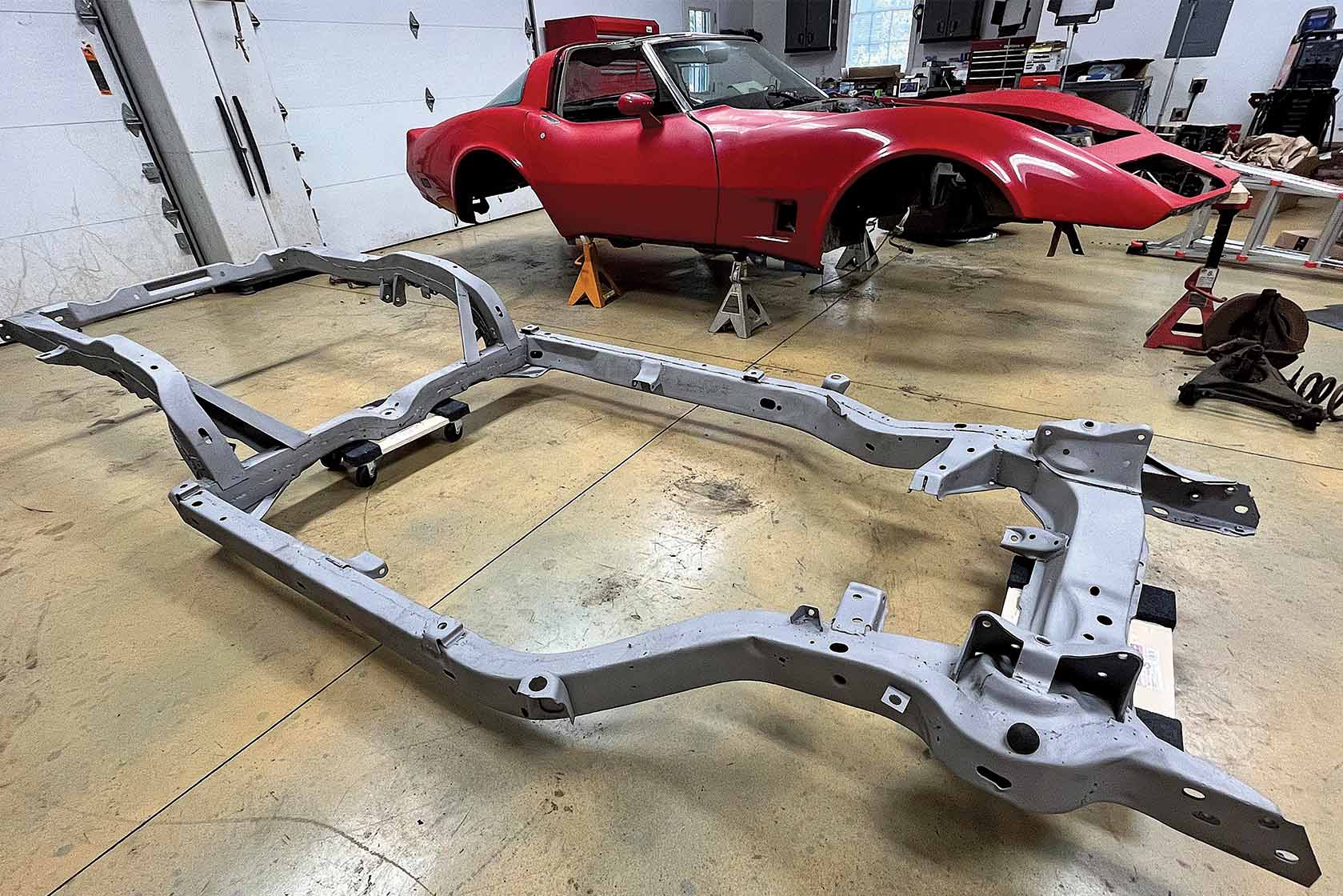
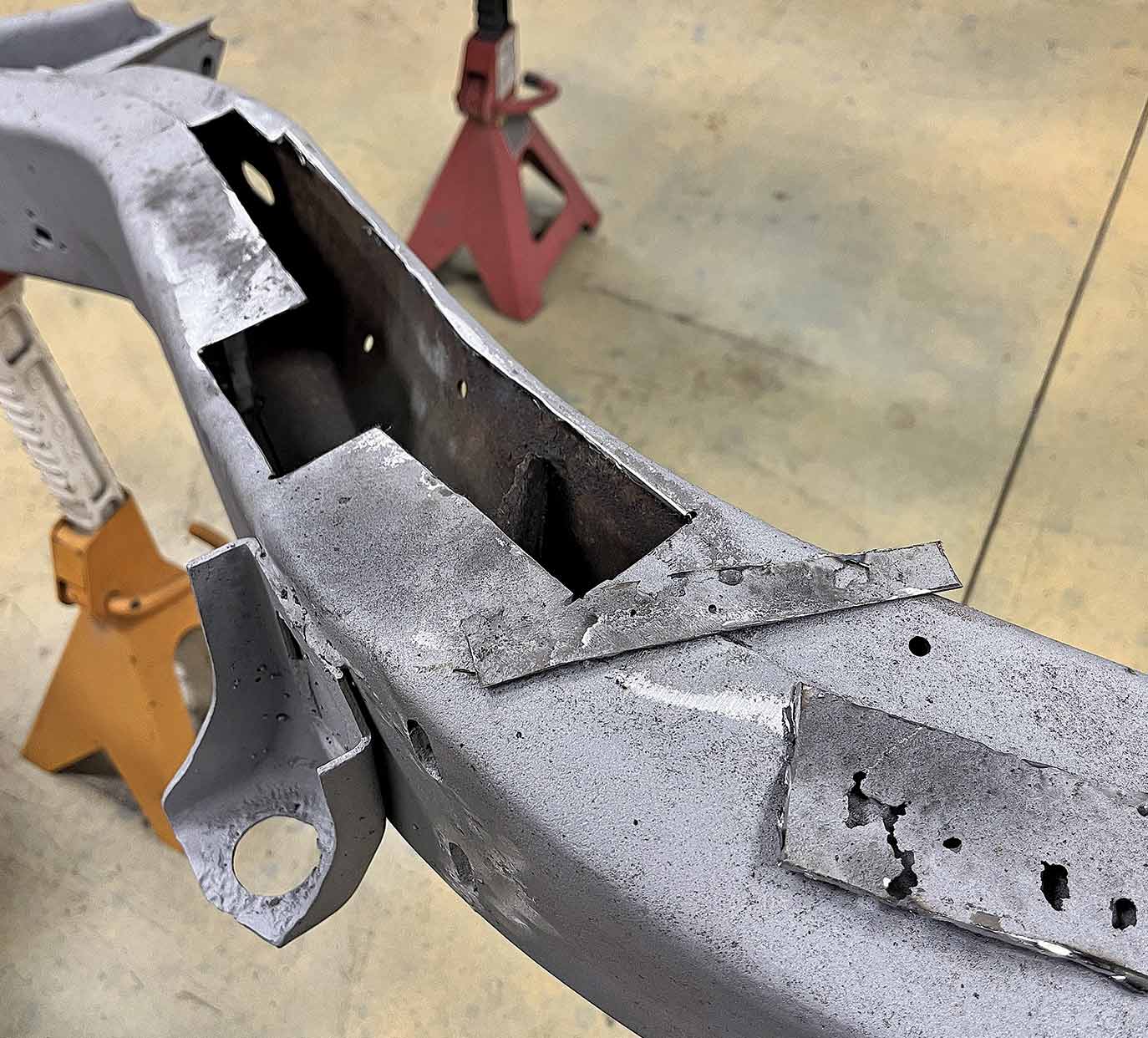
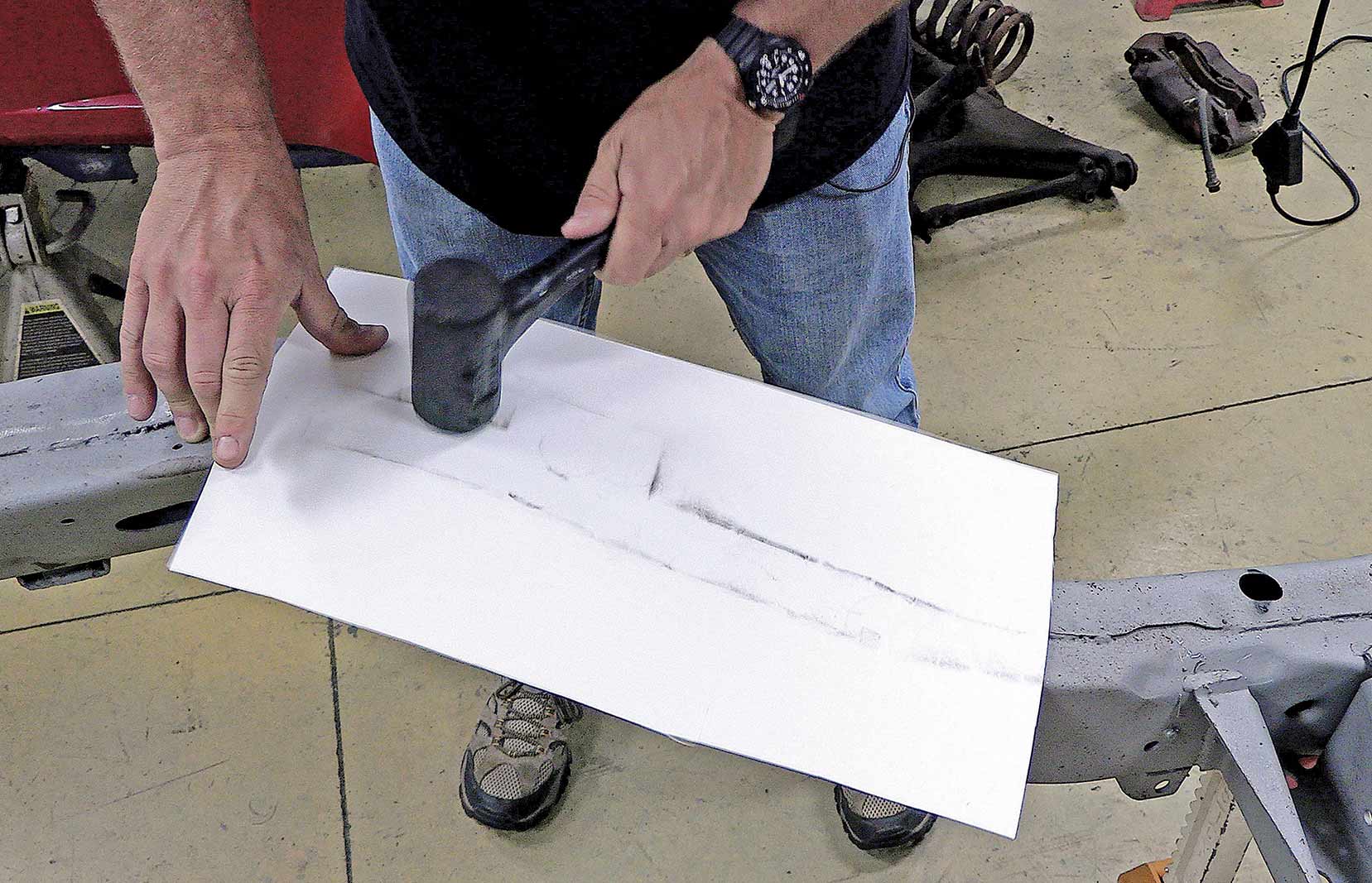

10. Here’s my pattern. There was one area where I cut away too much of the poster board, but that’s no big deal. I just taped another piece onto it and re-cut it to the correct dimension.
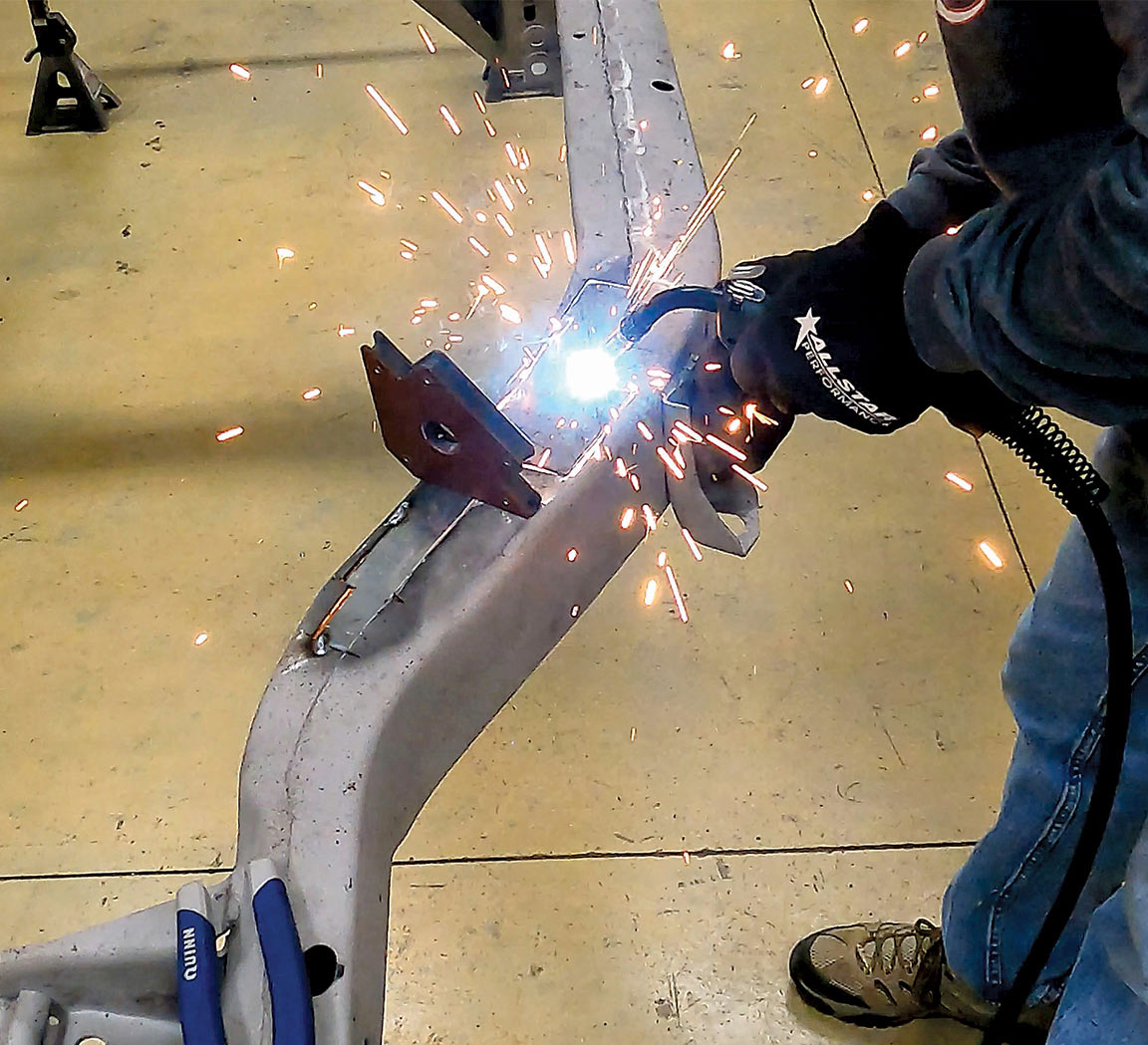
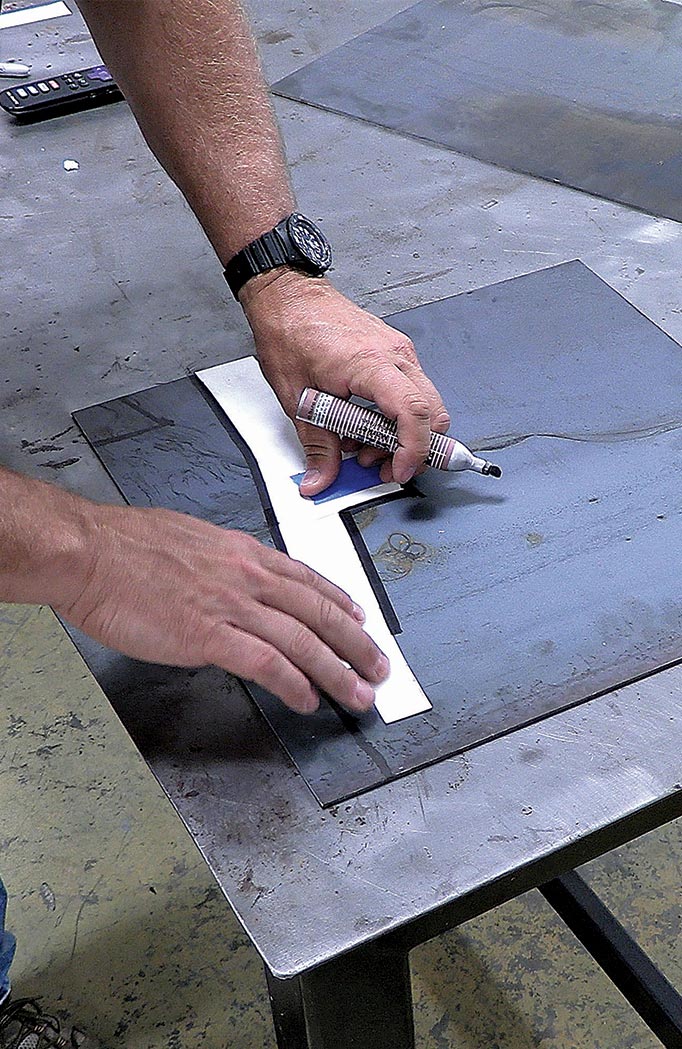

10. Here’s my pattern. There was one area where I cut away too much of the poster board, but that’s no big deal. I just taped another piece onto it and re-cut it to the correct dimension.
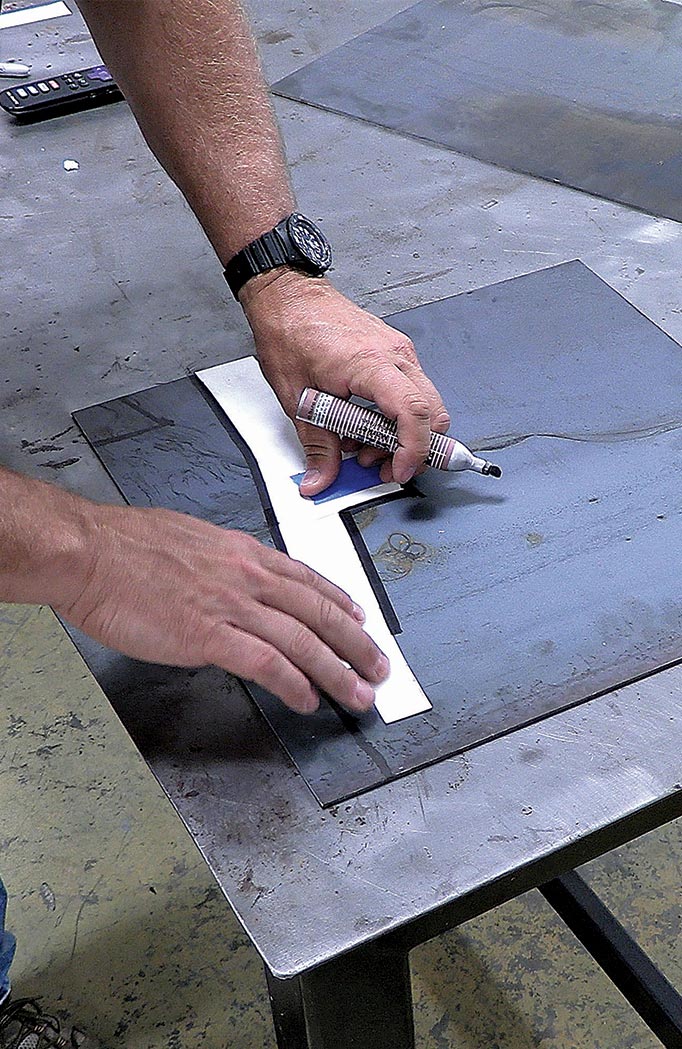
11. I picked up some 11-gauge steel from my local fab shop, which pretty closely matches the thickness of the steel used in the frame. Often, you can save some money by asking for “drops,” which are essentially the leftovers from a larger job. Metal shops will usually be happy to sell these at a discount, otherwise they’ll likely just be thrown into a scrap bin for recycling. Anyhow, these drops were more than large enough to transfer the pattern onto.
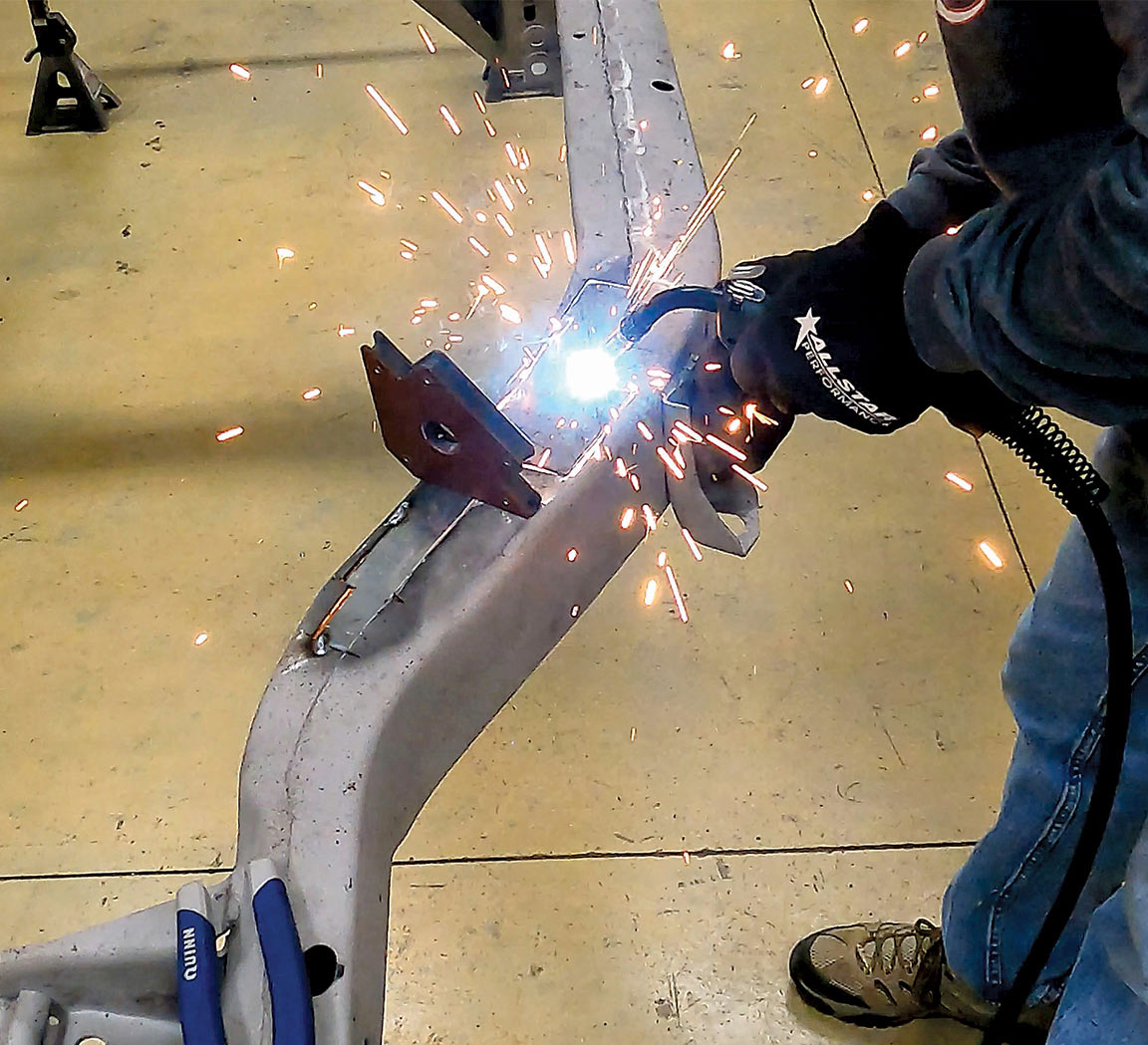
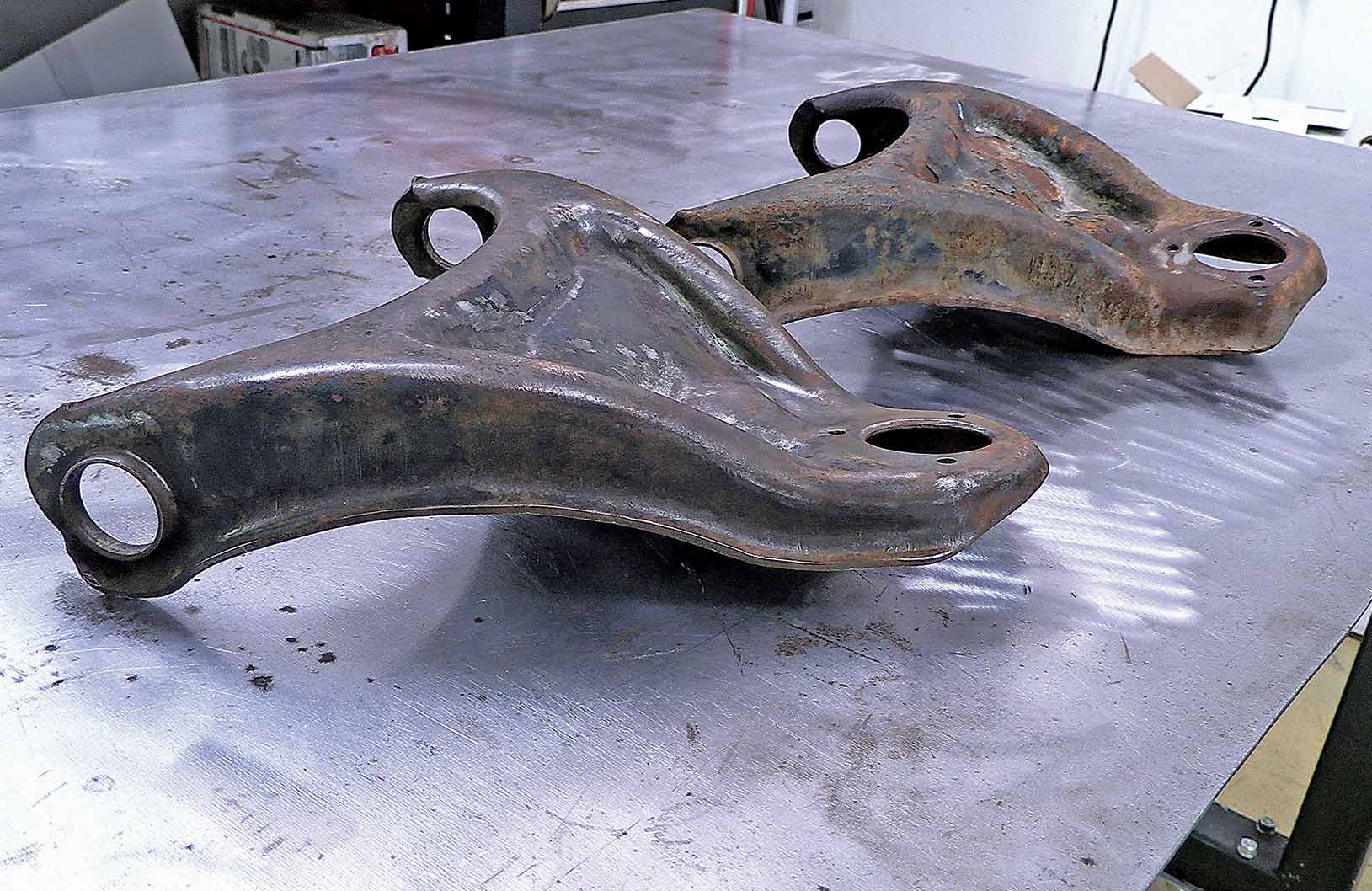
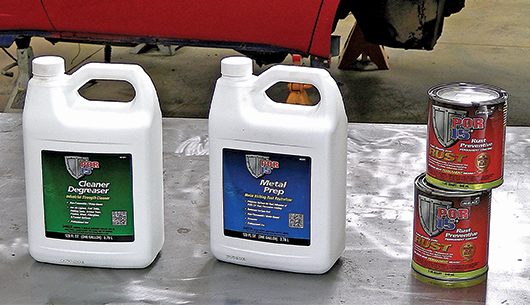
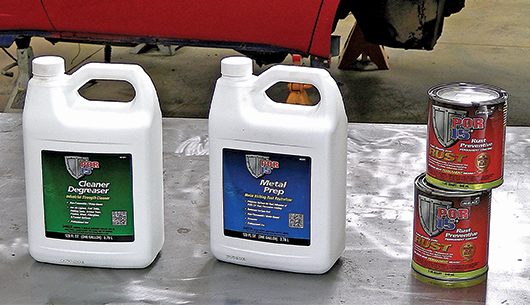
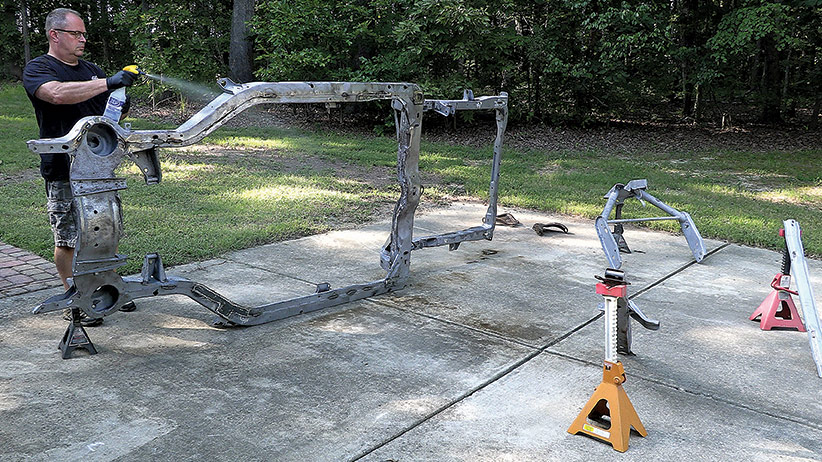
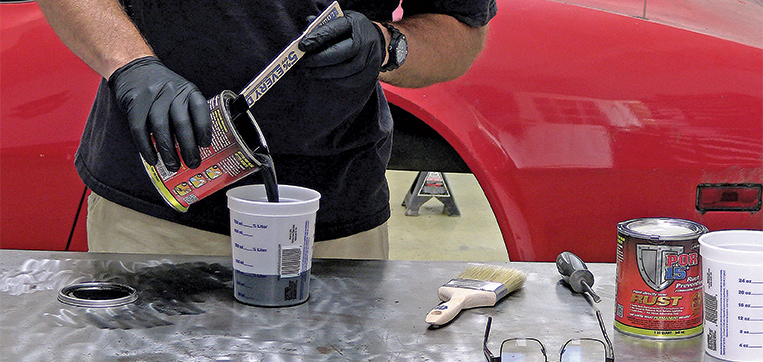
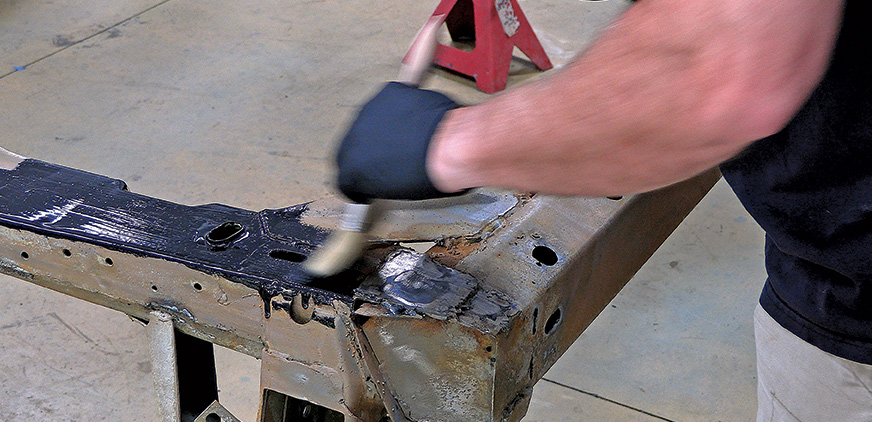
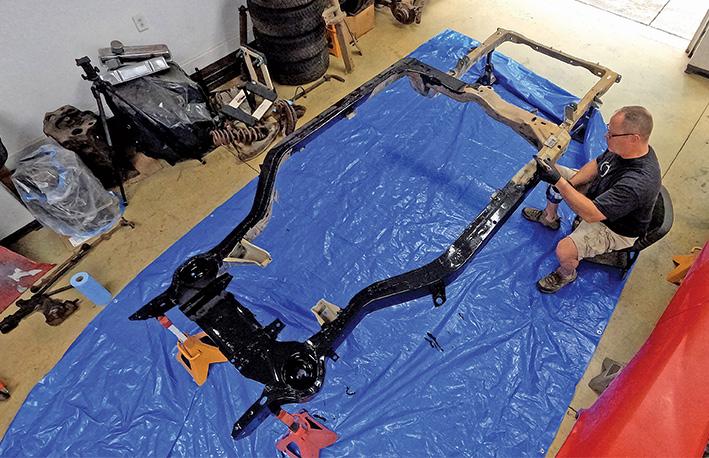
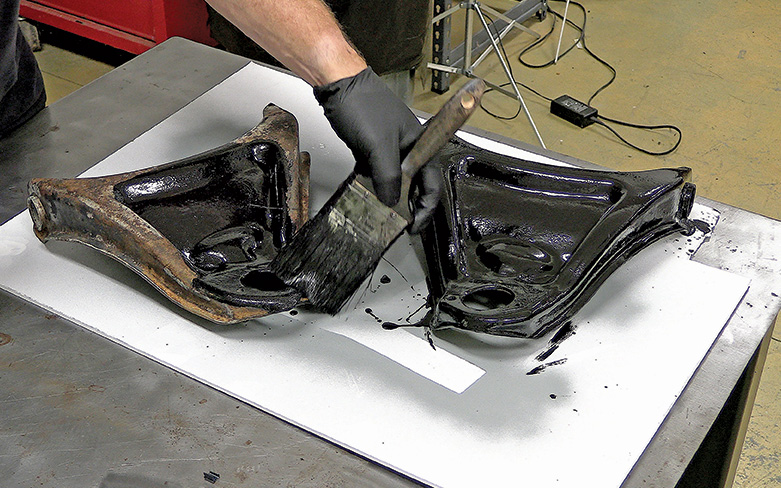
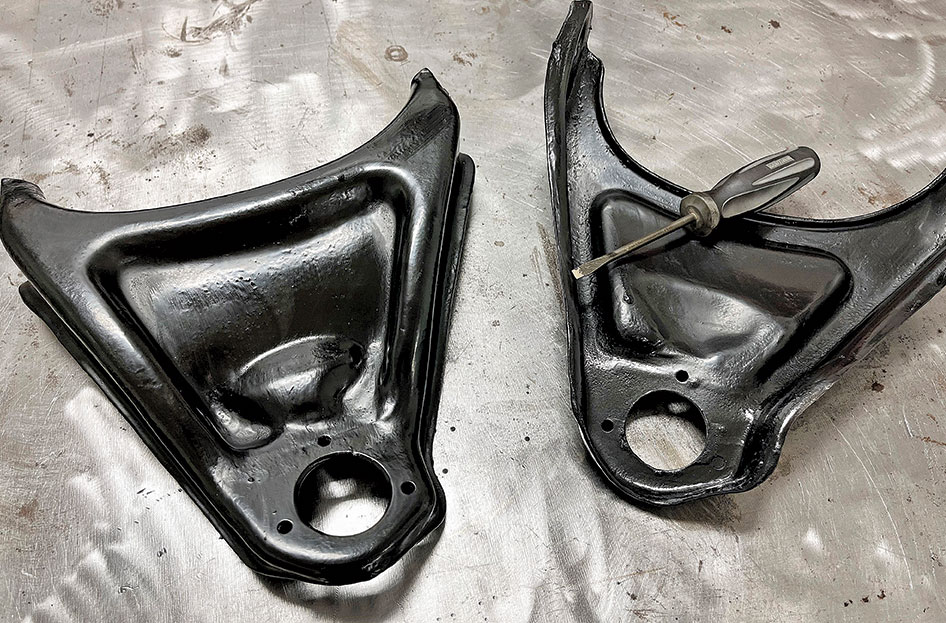
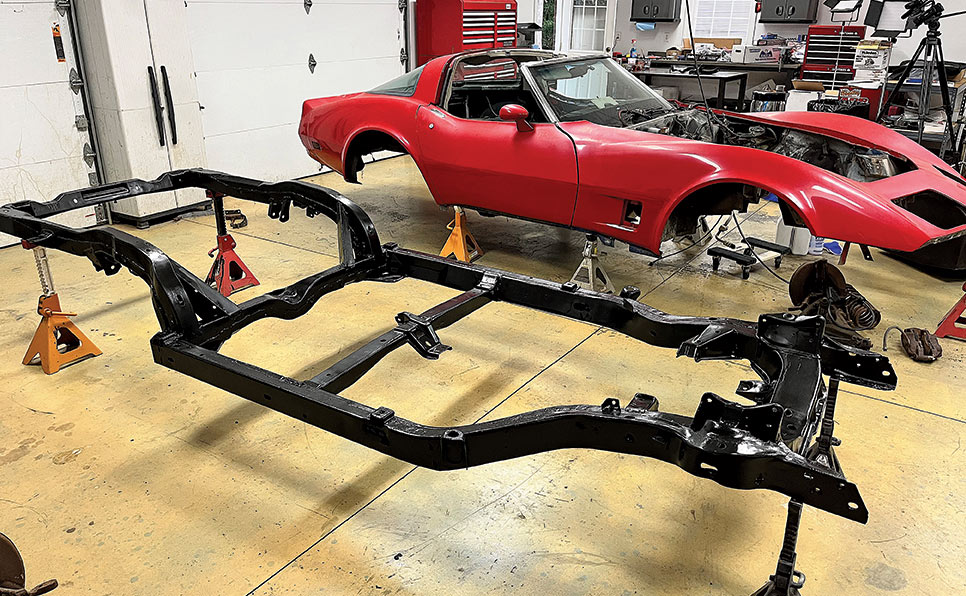
