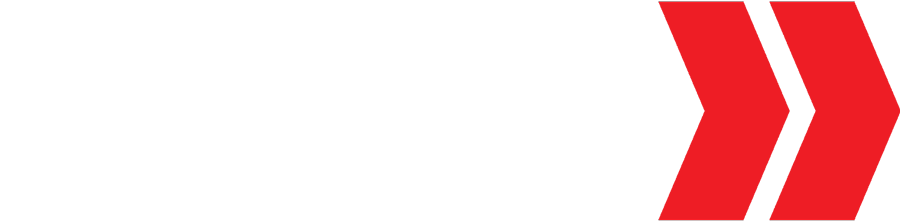
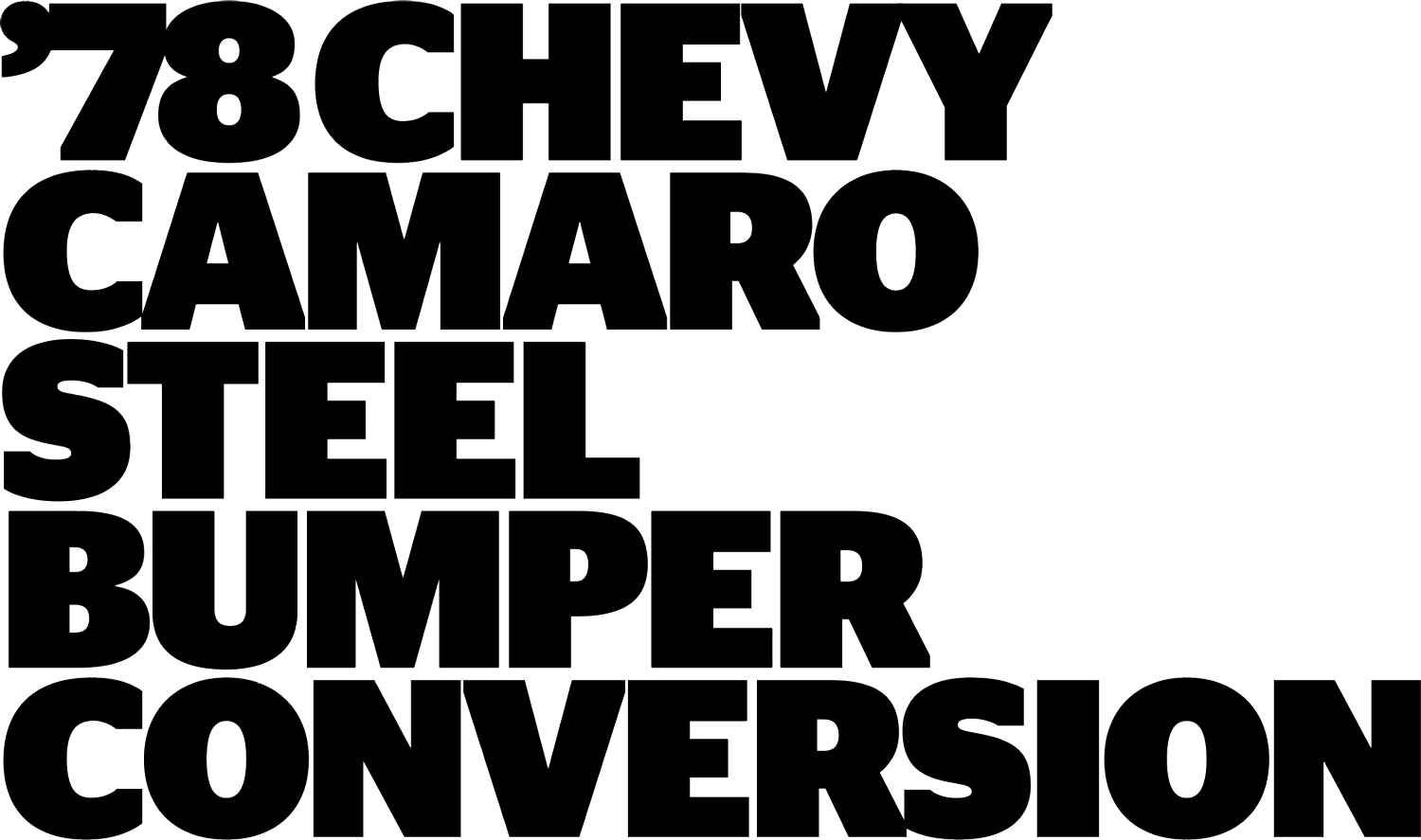

f you have been following along, we’ve covered the teardown of this rubber bumper to steel bumper Camaro conversion project. We removed the entire back end of the car, except for the roof, package tray, and framerails. With minimal modifications, this conversion can be done with a solid, general working knowledge of body panel replacement. This time around, we cover the modifications to the roof skin as well as welding up the body panels now that they are located properly.
Craig Hopkins of the Installation Center partnered with Auto Metal Direct to supply all the needed parts. He elected to reuse the roof skin, as it was in pretty good shape. The modifications to the roof are straight forward in order to turn this big back window into the smaller early design from GM. Hopkins gets us started on this modification and shows us how he aligns the AMD panels to make this conversion a breeze.
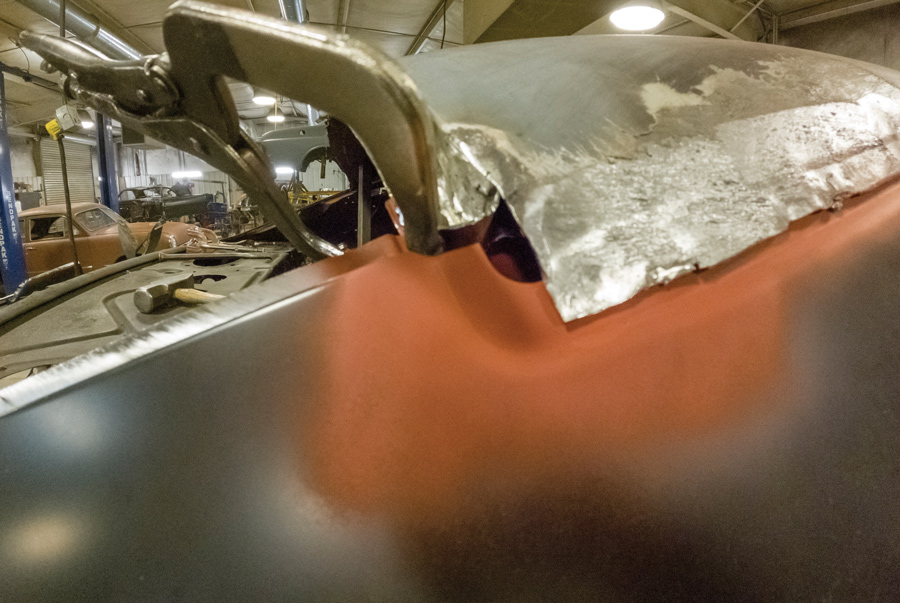
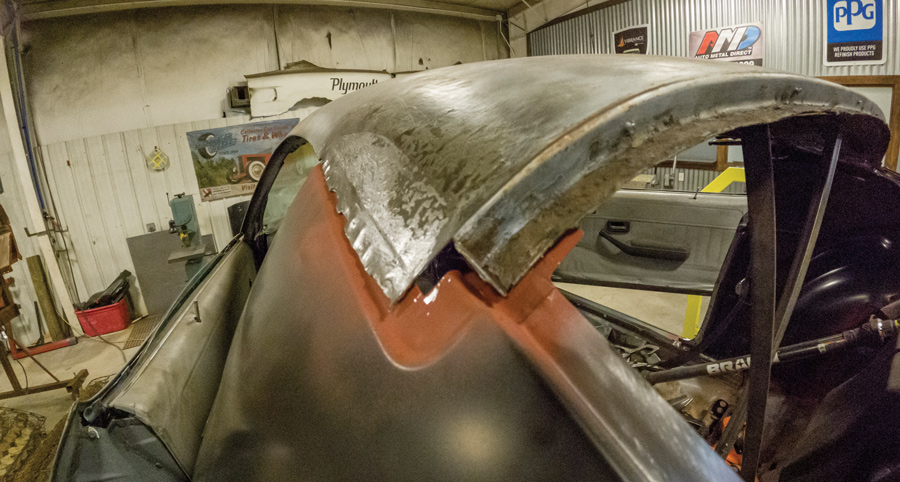
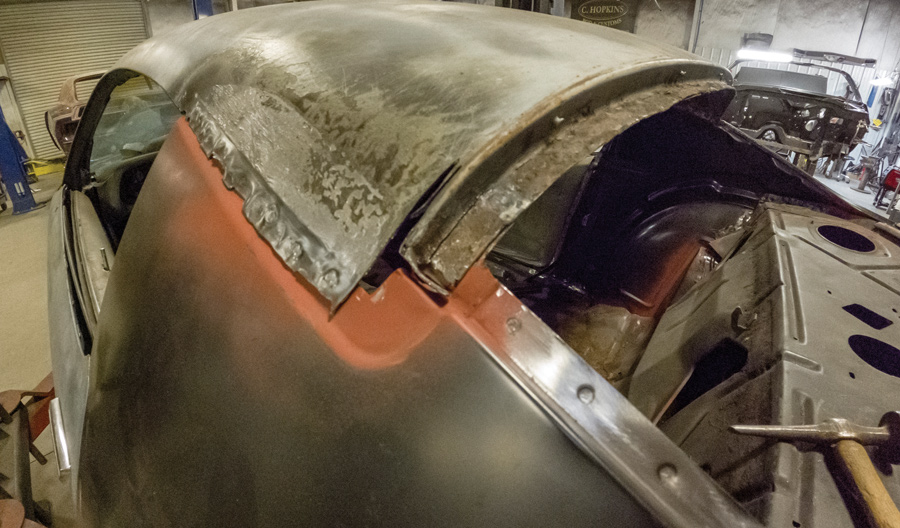
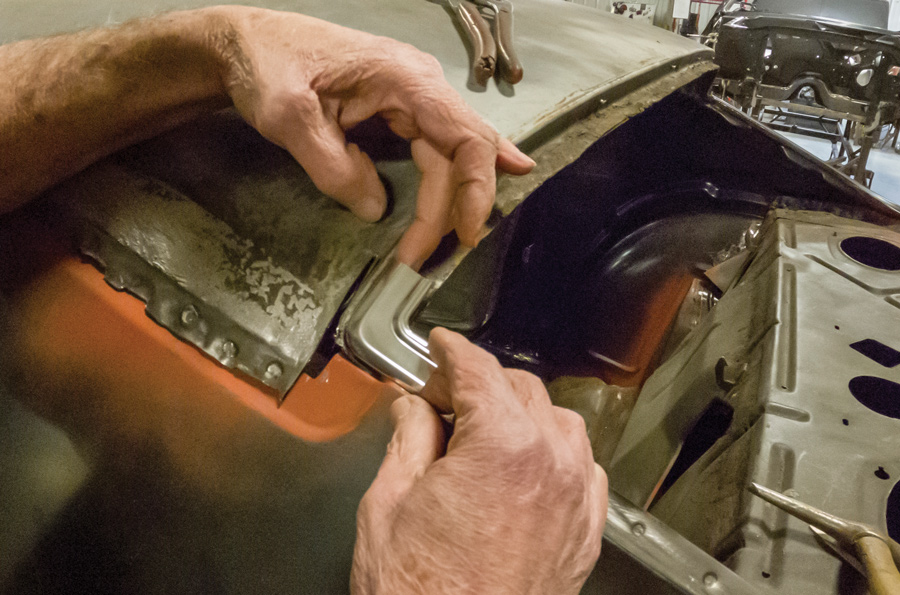
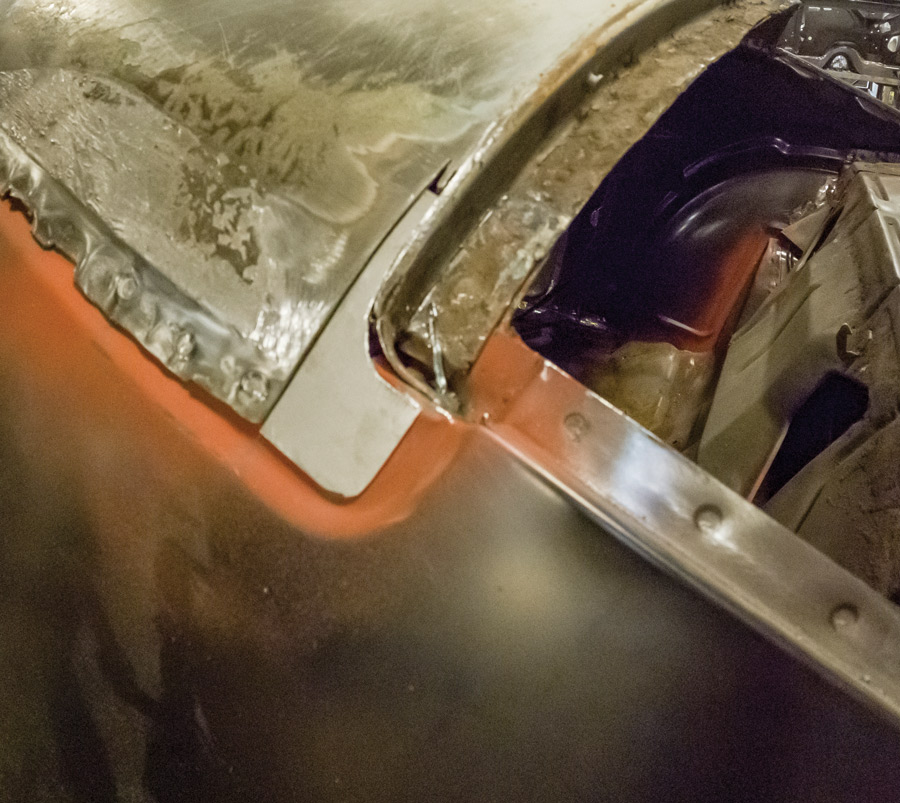
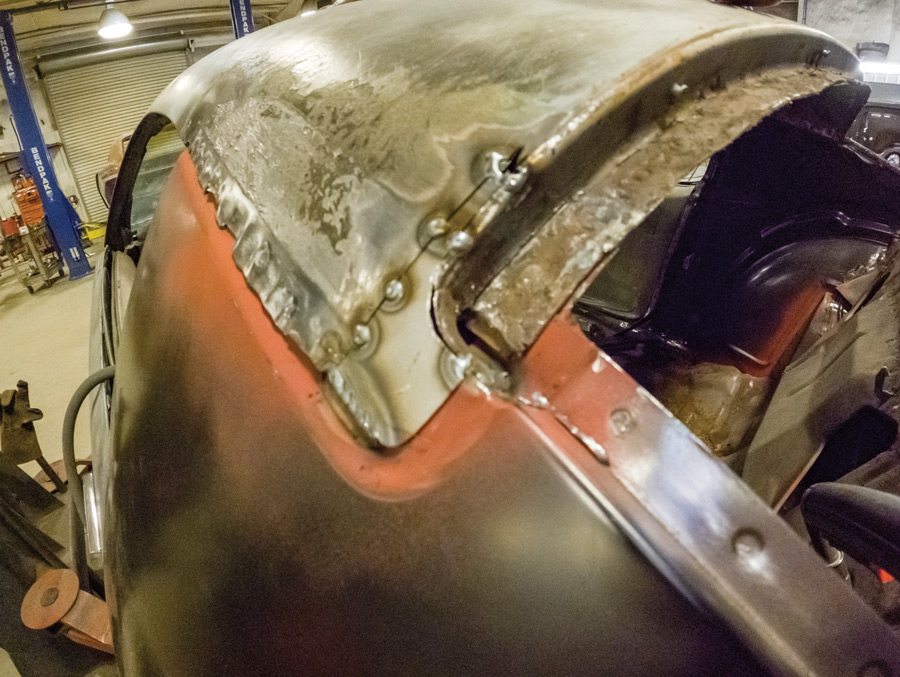
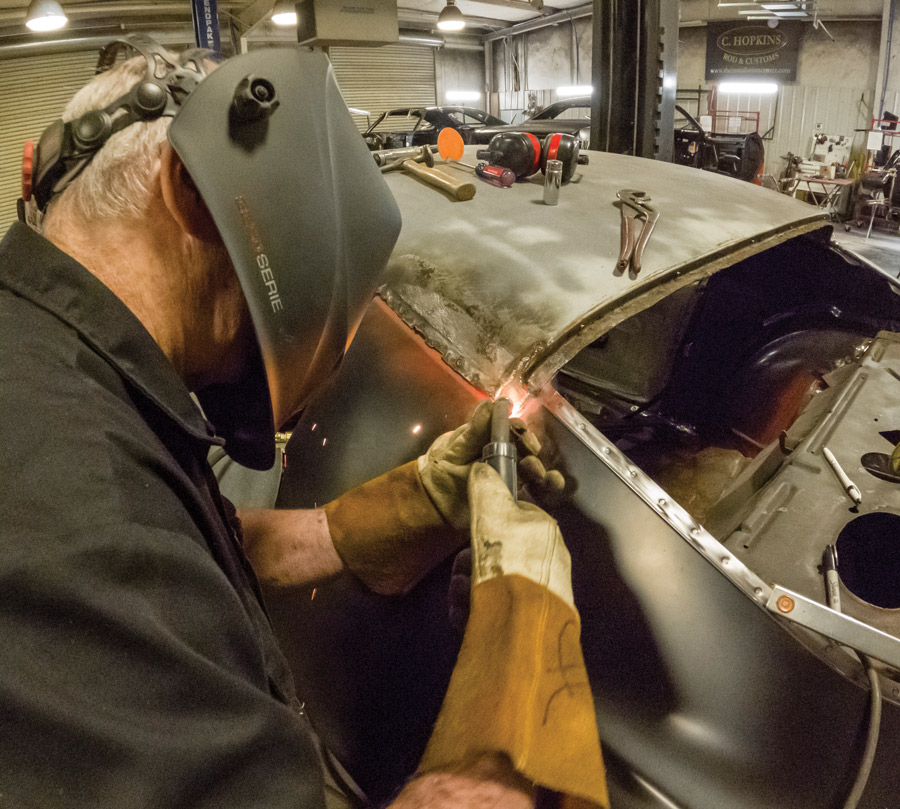
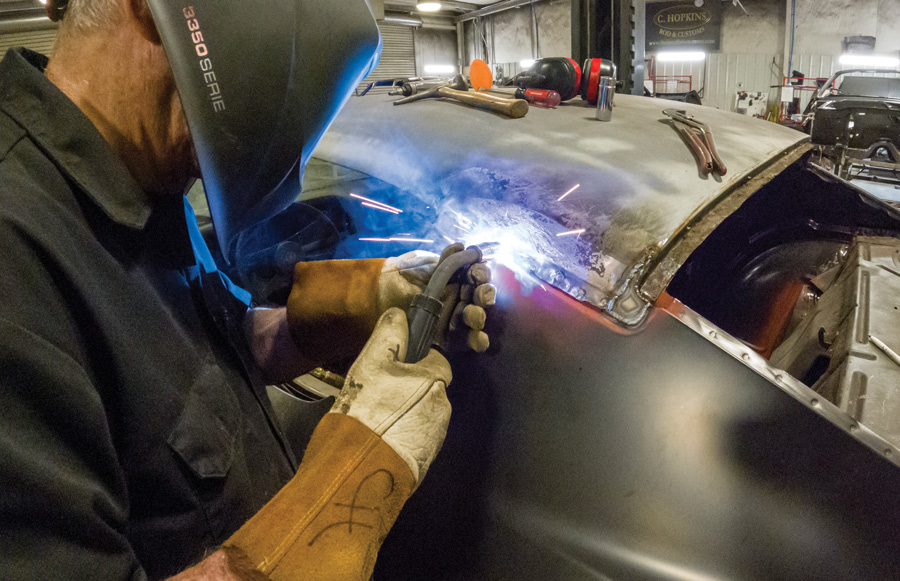
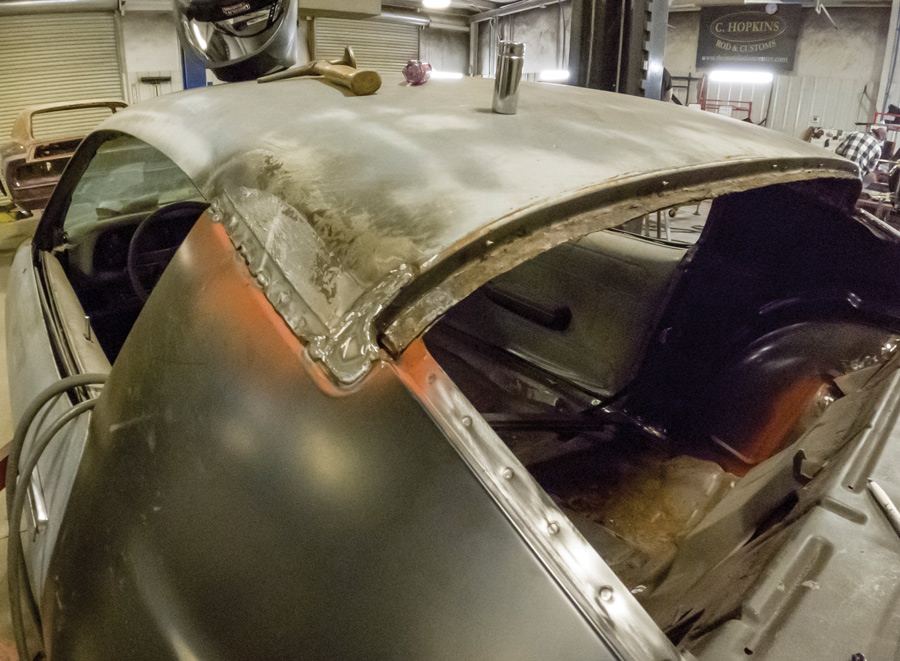
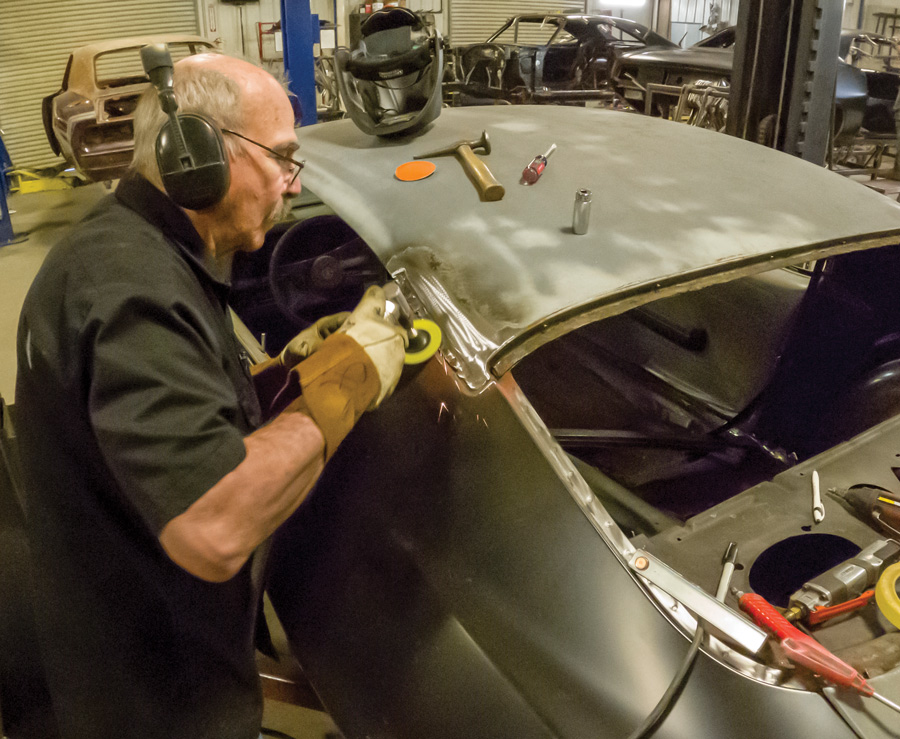
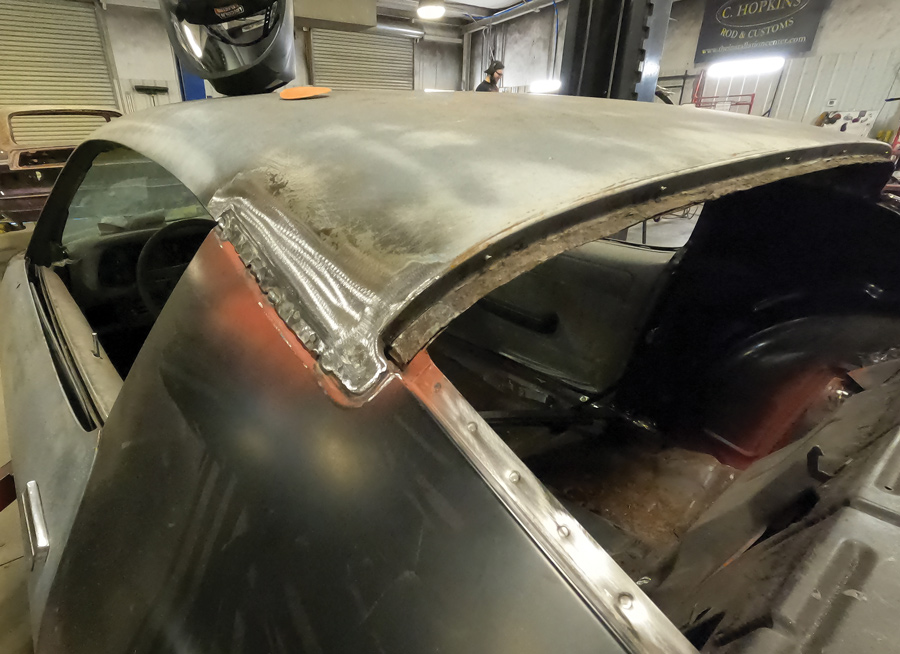
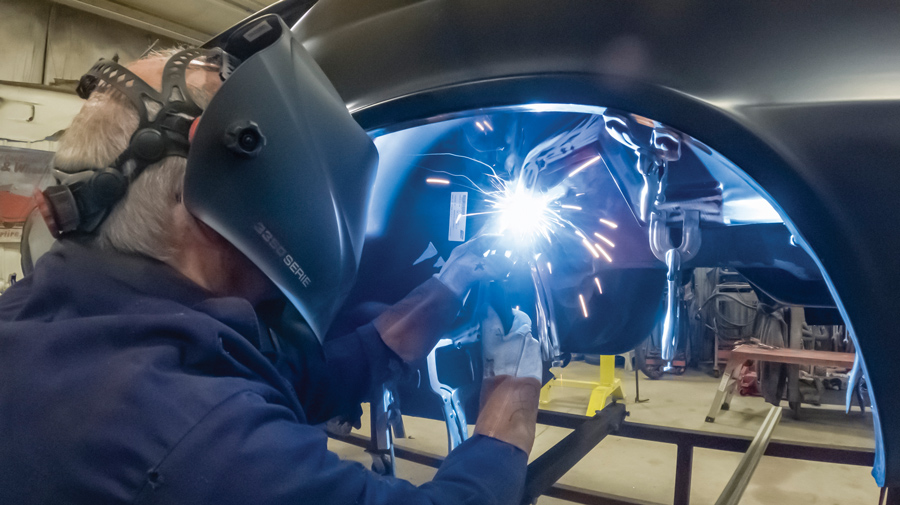
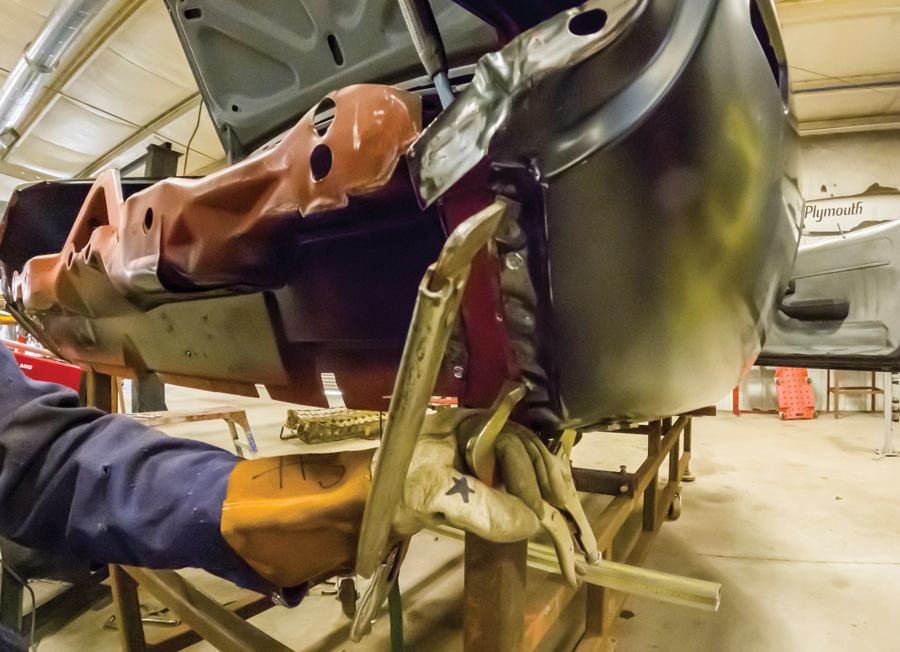
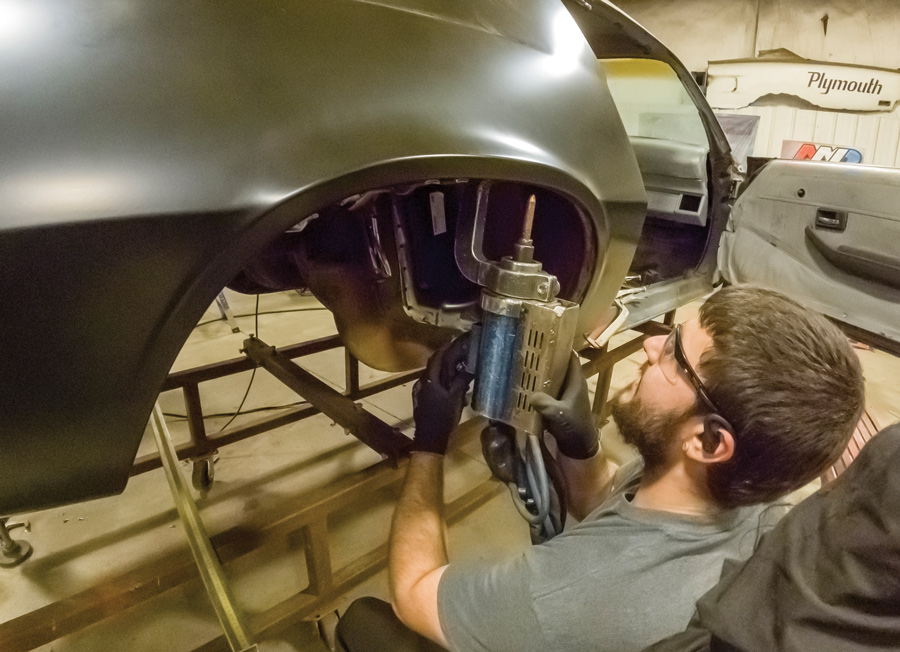
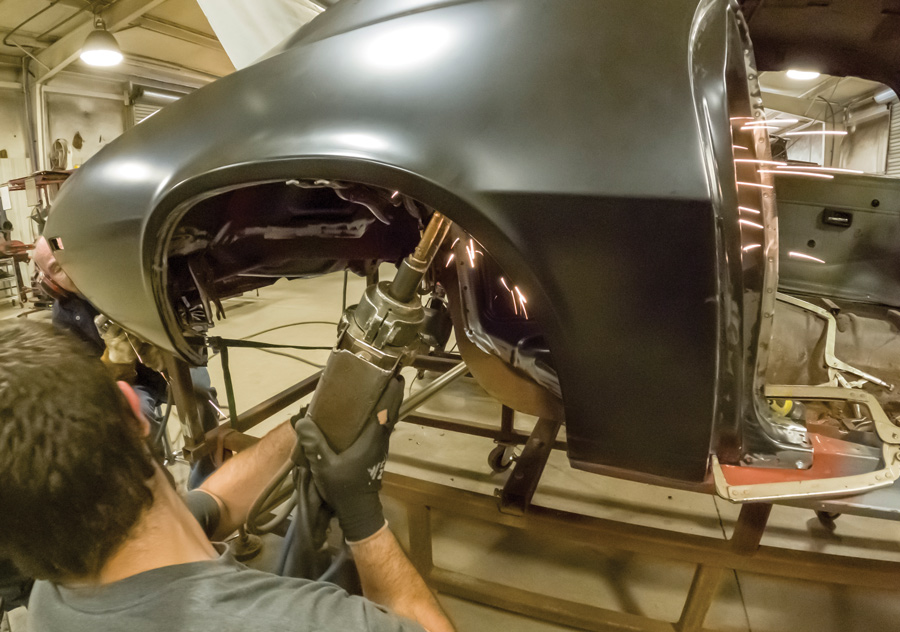
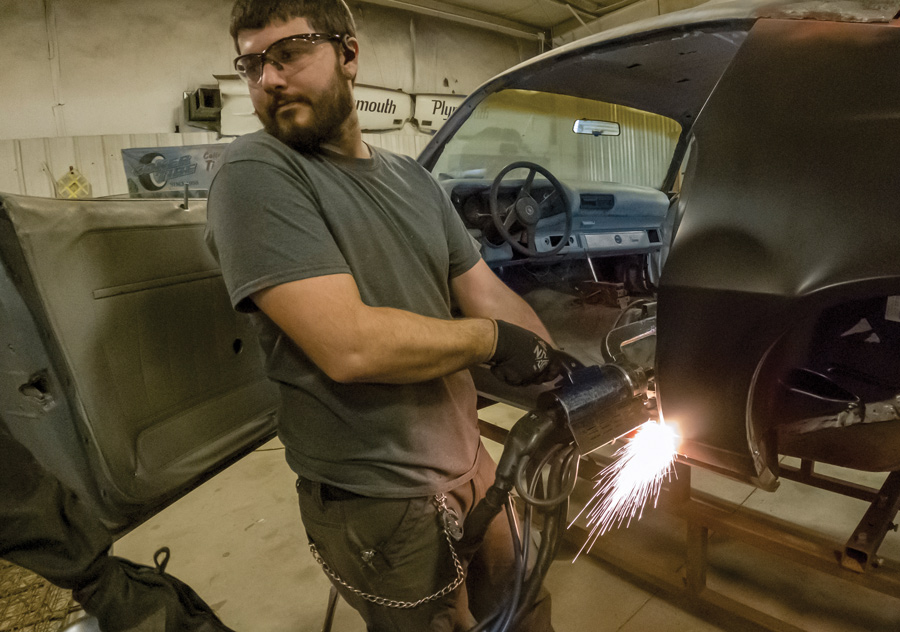
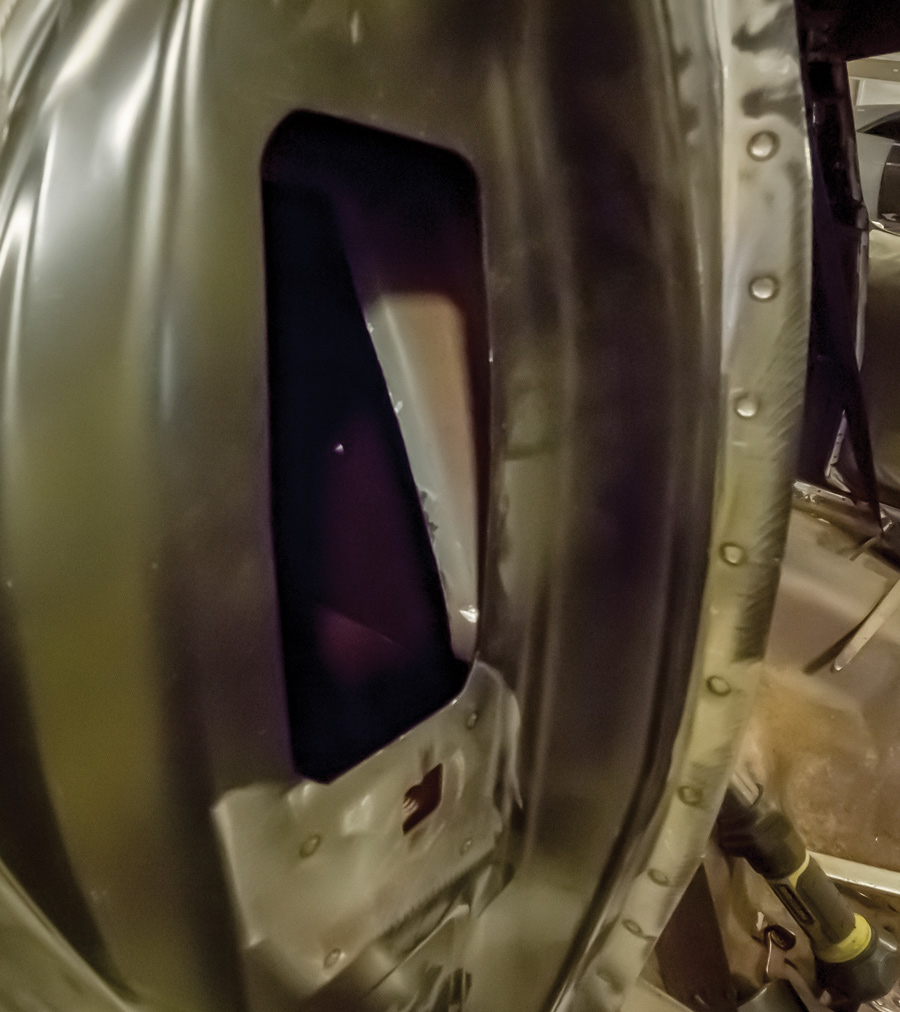
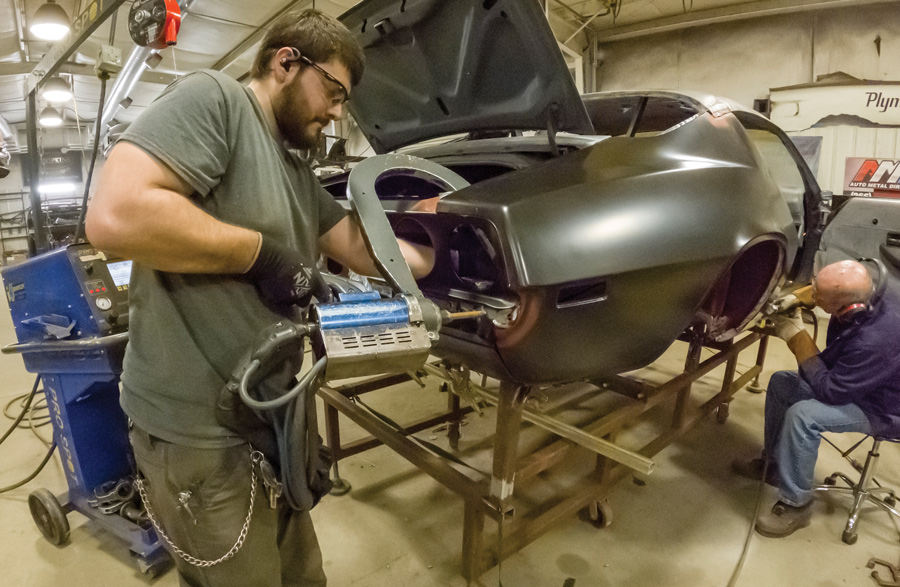
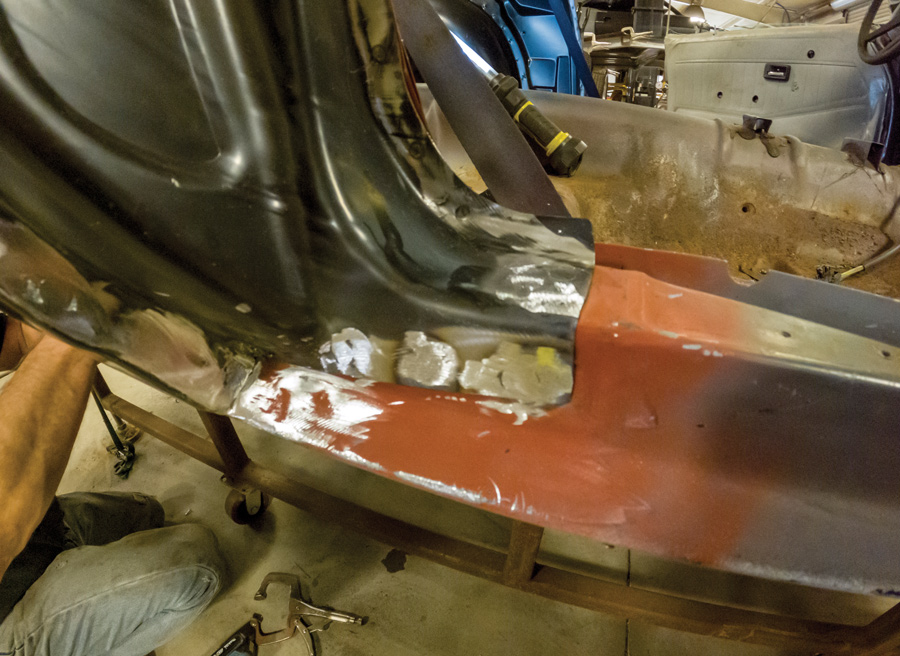
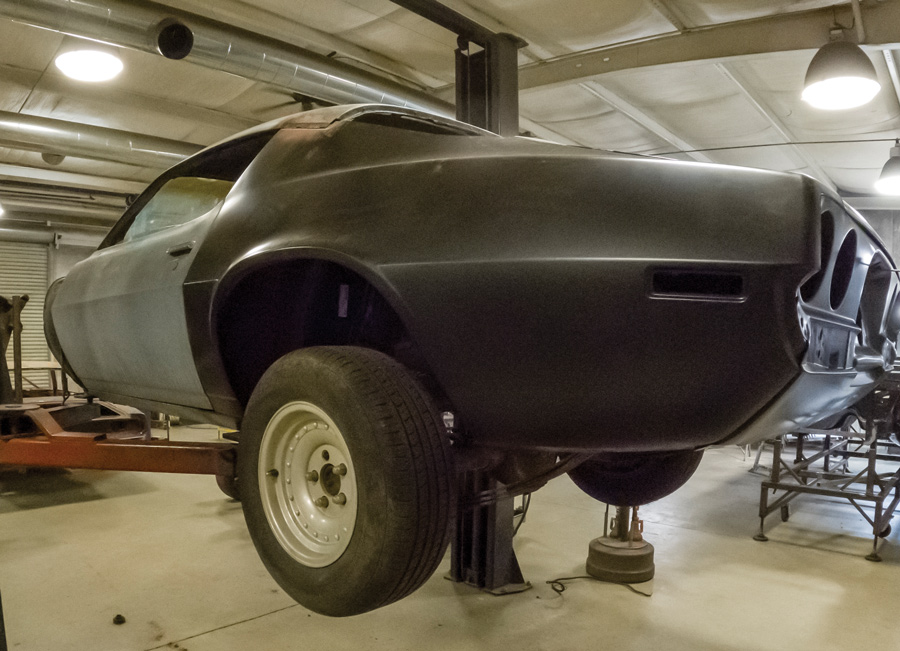
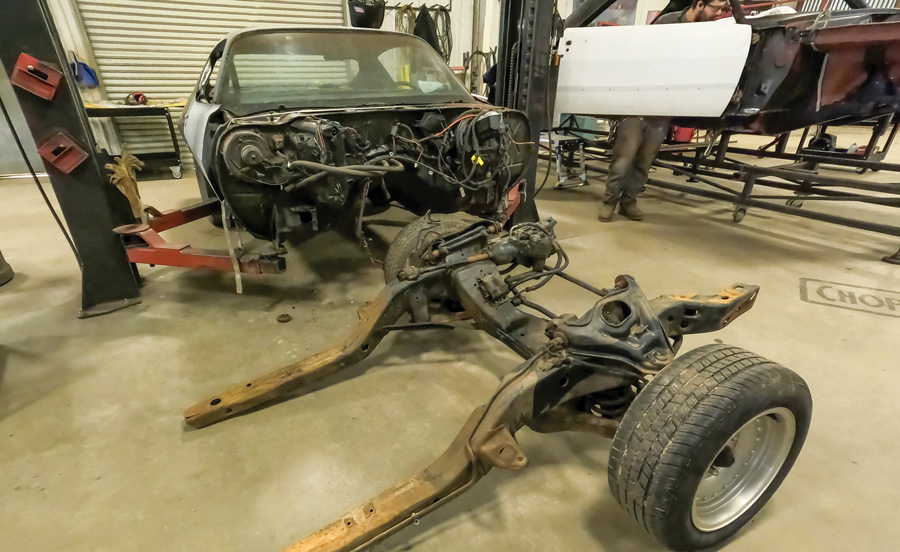
