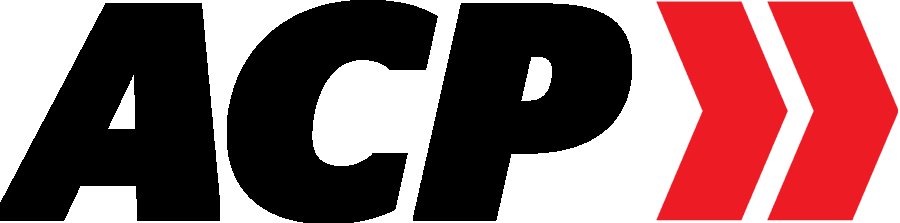



he venerable first-generation Chevrolet small-block has been out of production for decades now. Since then, multiple generations of engines from various manufacturers have come and gone, but the small-block is still everywhere you look. Of course, it remains incredibly popular in several forms of racing—everything from drag racing to oval track and beyond—and it remains a favorite with hot rodders in general. Its reputation as a reliable engine that makes great power without breaking the bank is well deserved.
Besides the ability to make big power pretty easily as well as its durability, one of the great advantages of the classic small-block is its versatility thanks to tons of aftermarket support. We’ve seen great small-block builds with carburetors on tunnel port intakes, giant roots blowers, twin turbos, you name it. And they’re all great. But one setup we don’t often see is individual runner intake setups like you often think of on old-school sports cars. That’s why we were excited when engine builder Keith Dorton of Automotive Specialists told us he was building a big-inch small-block complete with stack injection EFI from none other than Jim Inglese Eight Stack Systems and instantly decided to tag along for the build.
After spending decades concentrating on high-performance race engines, specifically for stock car racing, Automotive Specialists has broadened its scope and lately has been working with high-end car builders for unique engine builds. This project is one of those. That’s why it is still in primer in the final photos. The plan is for the car builder to take back the completed engine, strip off the intake, tape up the rest, and give it a high-end basecoat/clearcoat paintjob.
The baseline for the build is to maximize the cubic inches for the small-block with both a big bore and extra stroke. A Dart SHP cast-iron block with extra-thick bores help make this possible by allowing 4.125-inch-diameter cylinder bores combined with a 4.00-inch stroke to knock out 427 ci. Squeezing in the extra 1/2 inch of stroke did require a bit of clearancing work along the oil pan rails, but that can easily be done by hand with a die grinder.
There was also another step to be able to squeeze in the rotating assembly consisting of a Molnar Technologies forged stroker crank and connecting rods and the Mahle pistons. Dorton partnered with Jones Cam Designs to come up with a reduced base circle camshaft that still managed 250 degrees of duration for the intakes and 258 for the exhausts at 0.050 inch of tappet lift along with 0.410 lobe lift. The reduced base circle cam is necessary to create enough clearance so that the big end of the connecting rods can swing by without crashing into anything.
Big cubic-inch bottom ends require cylinder heads that can move a lot of air, so they’ve gone with a set of fully CNC-cut aluminum heads from Air Flow Research (AFR). These heads are designed to be as efficient as possible for traditional 23-degree Chevy heads with 195cc intake runners and 2.050/1.600 intake and exhaust valves with lightweight 8mm stems. At 0.550 valve lift the heads are rated for 280 cfm for the intake ports and 218 for the exhausts (which are raised 0.100 inch). The combustion chambers are sized at 65 cc, making the static compression ratio right at 10.5:1.
But the cherry on top of the cake for this build is definitely the polished aluminum individual runner intake system. Jim Inglese is famous for his Weber carb’d individual runner intakes. He sold his company, Inglese Induction Systems, years ago, but unfortunately, the new ownership didn’t treat the company with the same love and commitment, and it eventually went under. So, Inglese founded Jim Inglese Eight Stack Systems, building beautiful individual runner intake systems with both Weber-style carburetors and EFI.
Our unit is outfitted with a well-disguised electronic fuel-injection setup that will be controlled by a Holley Terminator ECU. The advantage of an individual runner intake system like this is without the large plenum between the throttle body and the intake valve, the throttle response becomes incredibly quick and responsive. Low-end torque is also maximized.
Plus, the top-end production isn’t too bad, either. On the engine dyno we saw peak torque of 571 lb-ft at 4,700 rpm and 566.5 lb-ft at 5,900. Now, those are both very healthy numbers, but the truth of the matter is Dorton says the 427 with the aggressive cam they are using would make over 600 hp if outfitted with a quality single-plane intake and a big double-pumper four-barrel carburetor—and he knows because he’s built that engine combo before.
Now, this is not an indictment on the Inglese EFI system. The customer provided the unit, and on the dyno it worked exactly as advertised. But there is an unavoidable design issue with the Chevrolet small-block that’s practically impossible to get around: the intake valve arrangement.
As you are probably aware, the valve arrangement on a small-block is E, I, I, E, E, I, I, E. That pairs the intake valves together. When arranging the 55mm throttle bodies and the even-wider airhorns, the width of the components are enough that both cannot be centered over their respective intake runners. So, they have to be spaced out and the intake runners curved inward on the intake manifold. Now you have the incoming air/fuel charge curving one direction in the intake manifold, slamming into the wall of the intake port once it enters the cylinder head and then having to turn another direction before it reaches the combustion chamber. This isn’t an issue on LS engines (or even Fords) because there are no paired intake runners. It is also not as big a deal on a big-block because even though it does have paired intake runners, the wider 4.84-inch bore spacing (compared to the small block’s 4.400) spaces the ports out enough to significantly help. Plus, on a hot 350 and not the aggressive 427 we’ve built, this combo would likely be just about perfect.
Dorton pointed out that even though the peak power is slightly down, in a car you probably would notice the low-end torque much more than the extra horsepower up top. For the typical hot street machine, it’d likely be more enjoyable. Plus, you just can’t deny those great looks. This is definitely going to be one fun street brawler!
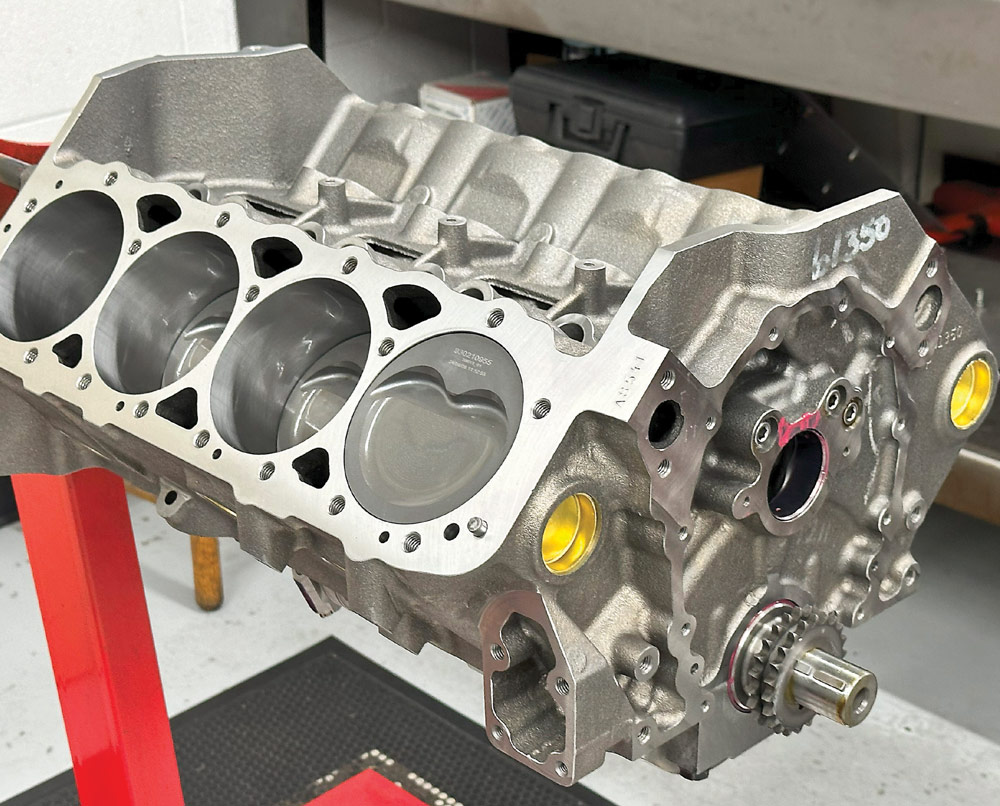
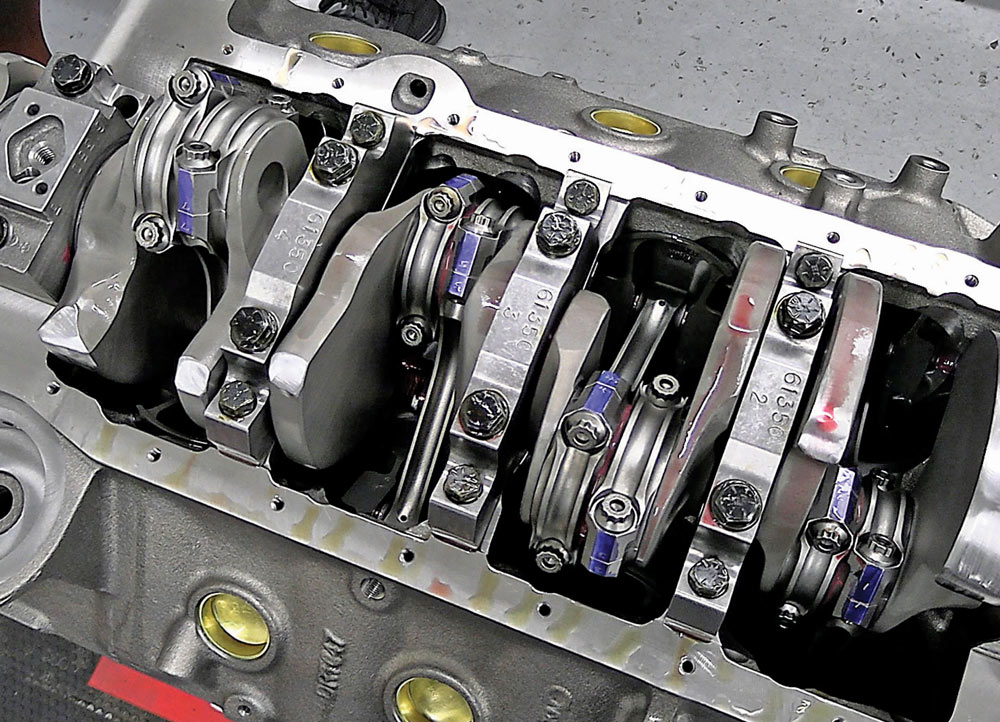
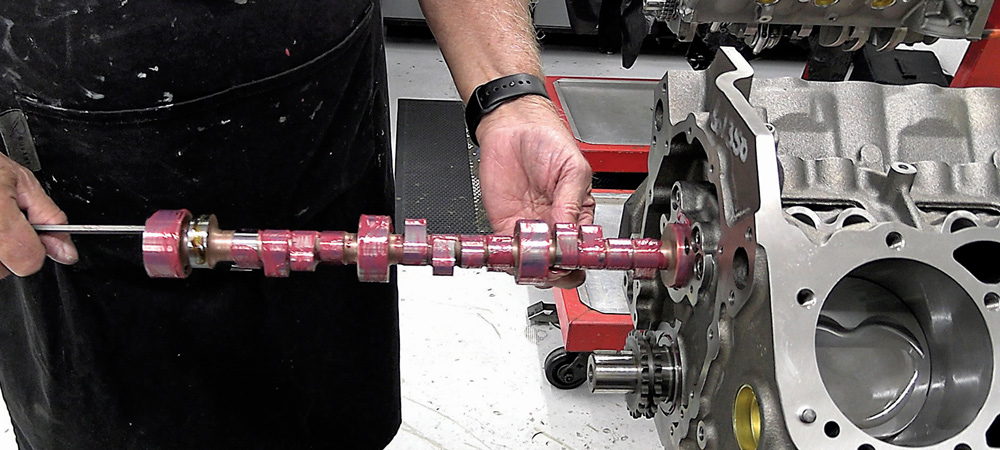
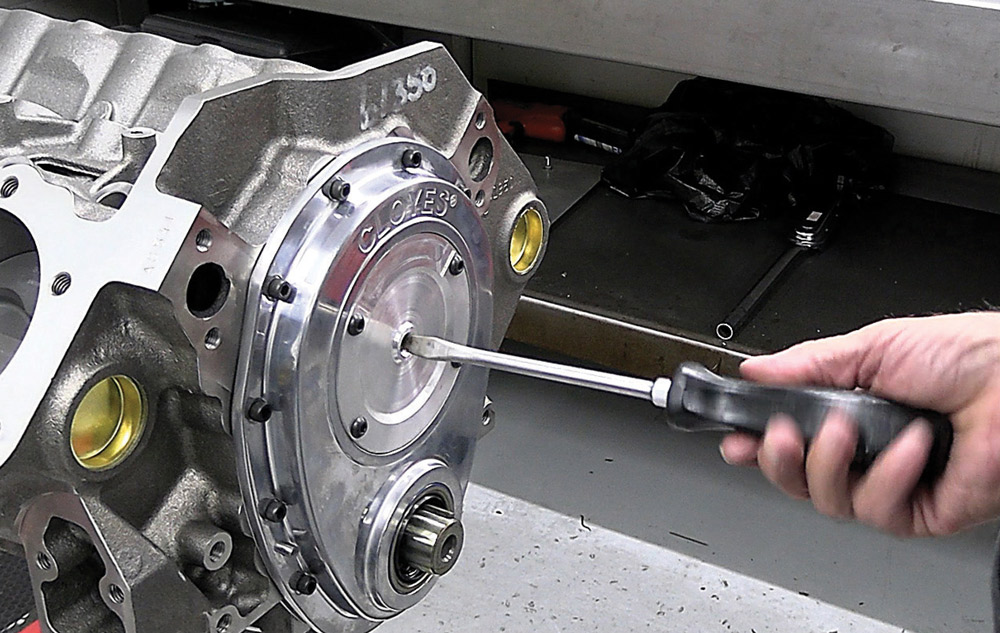
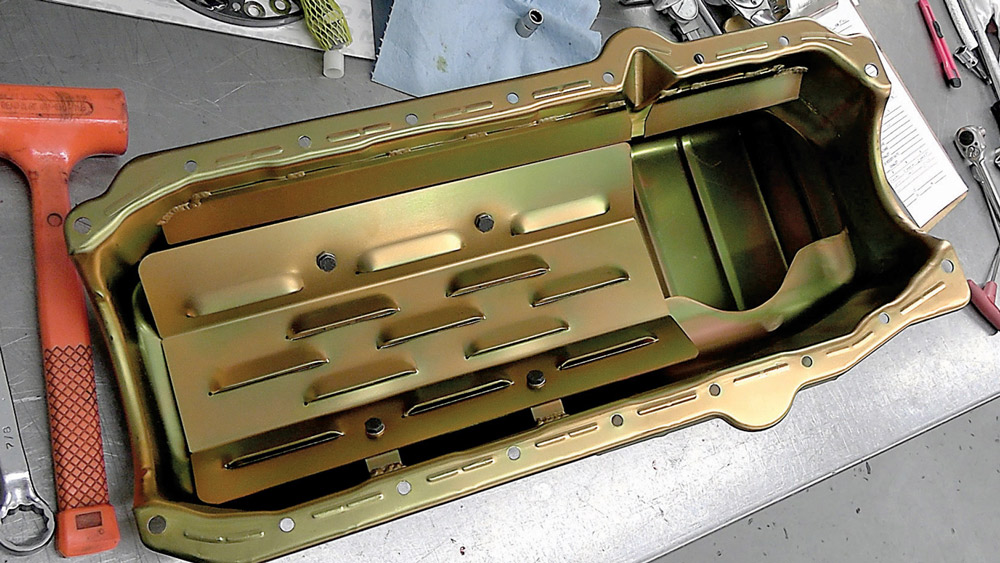
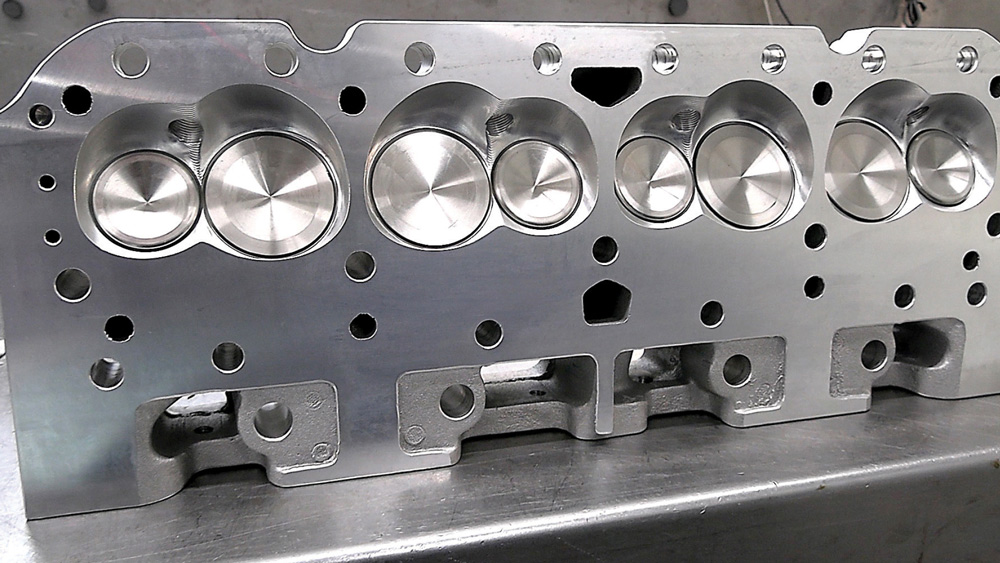
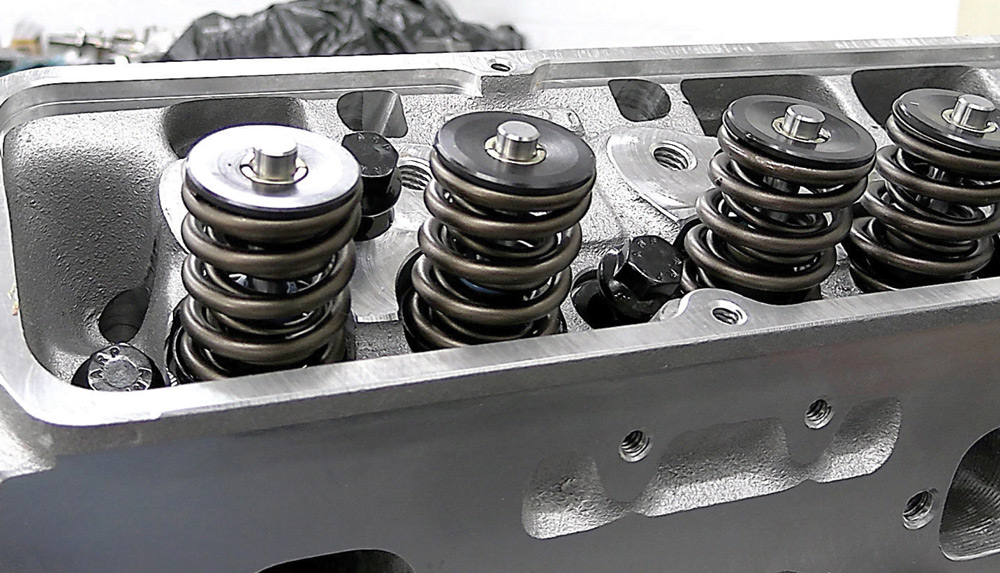
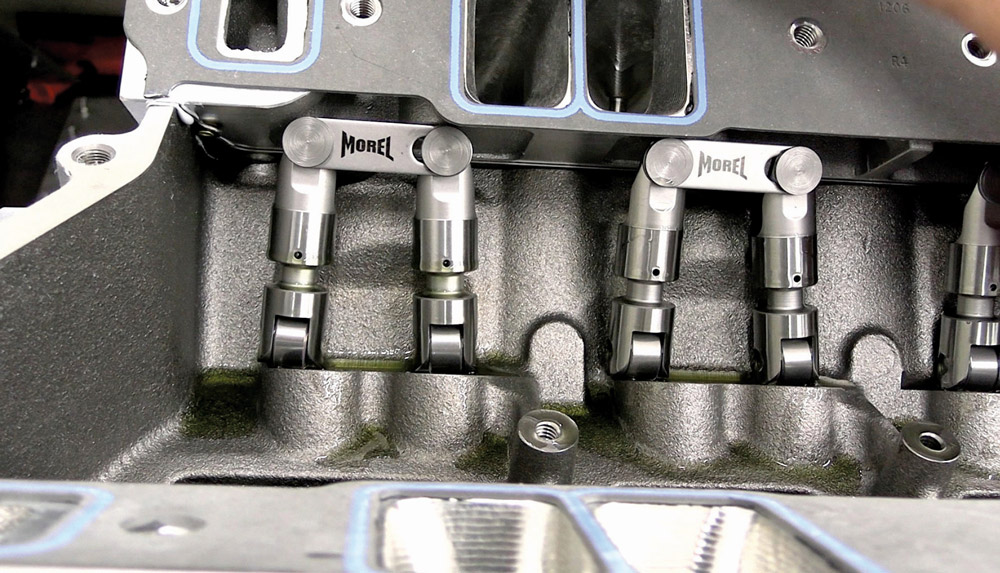
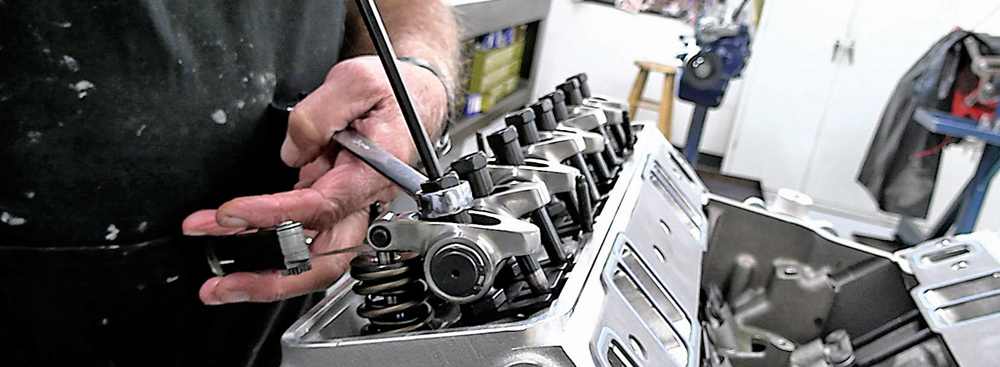
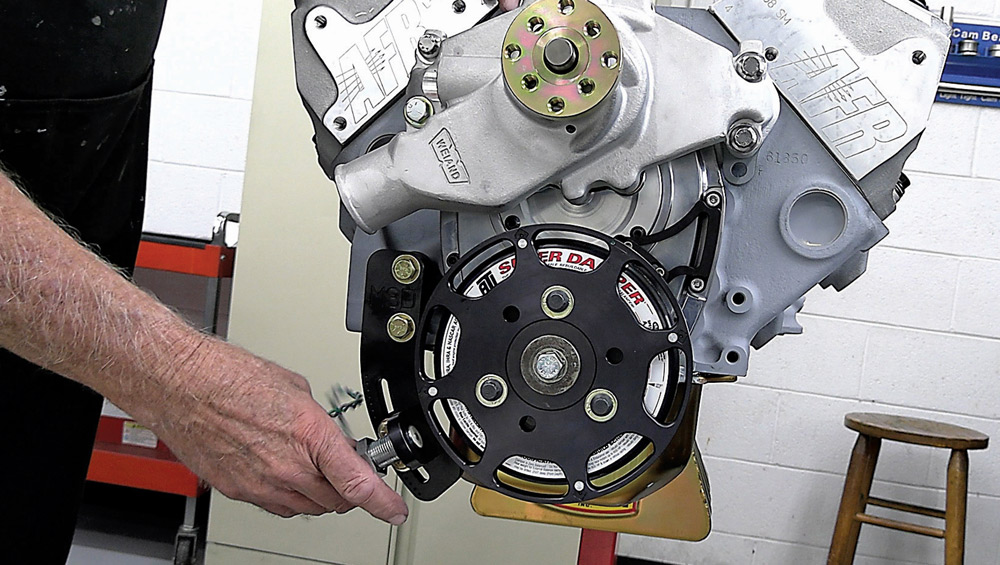
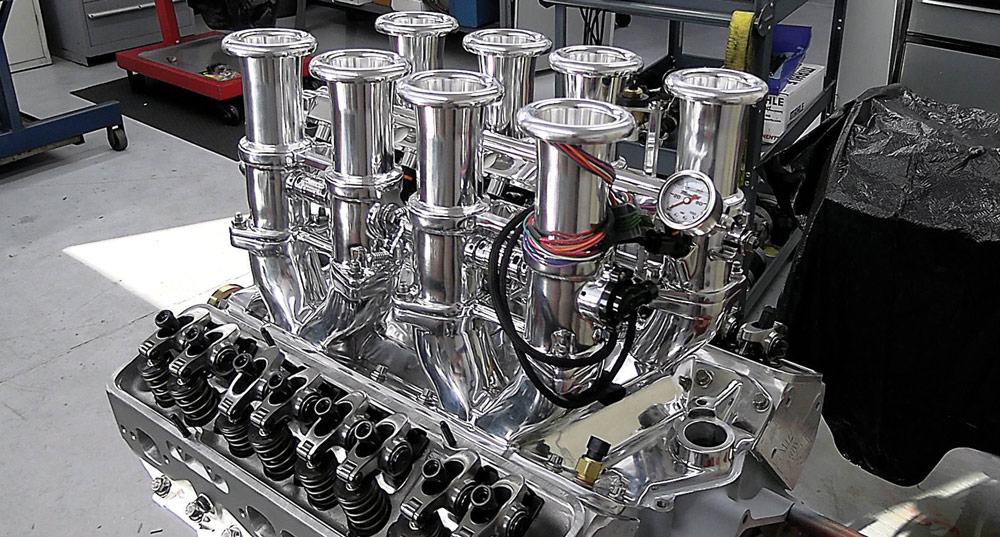
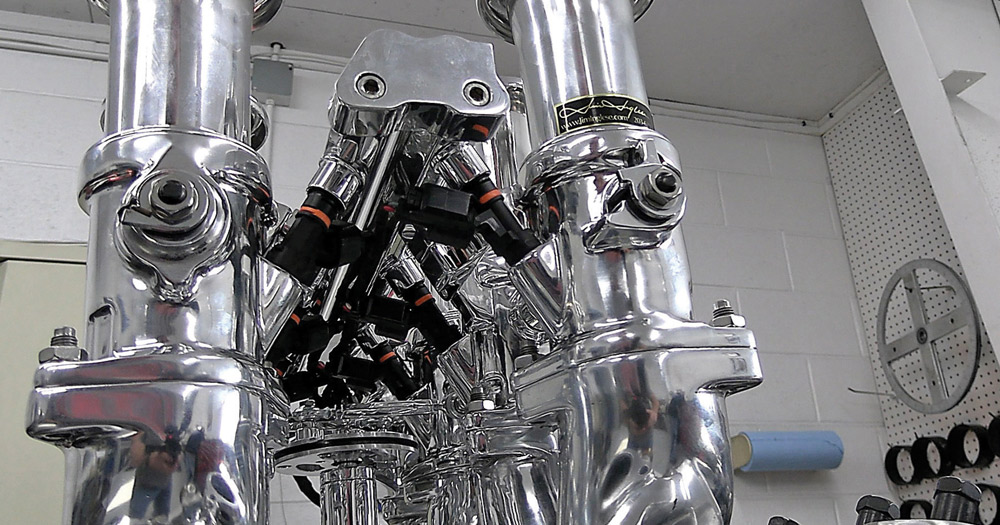
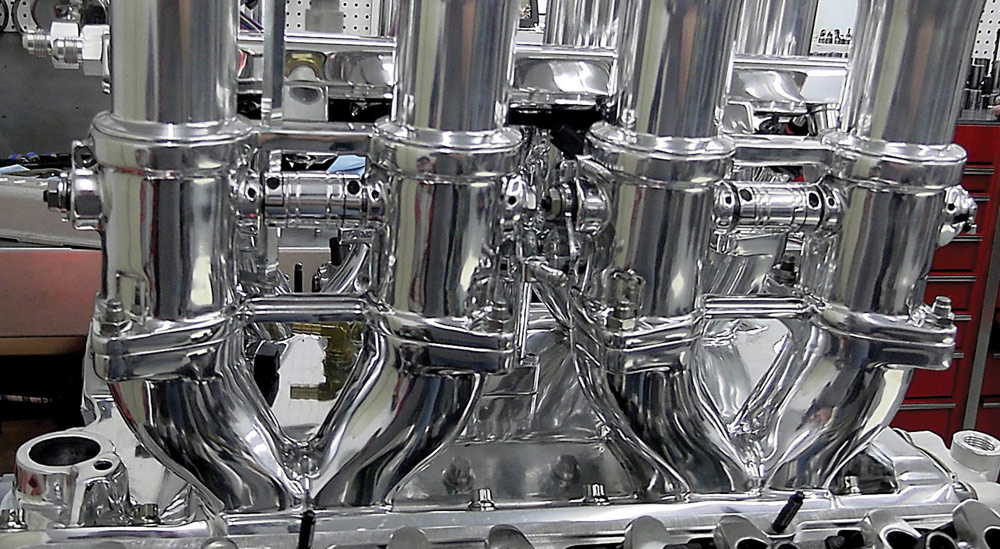
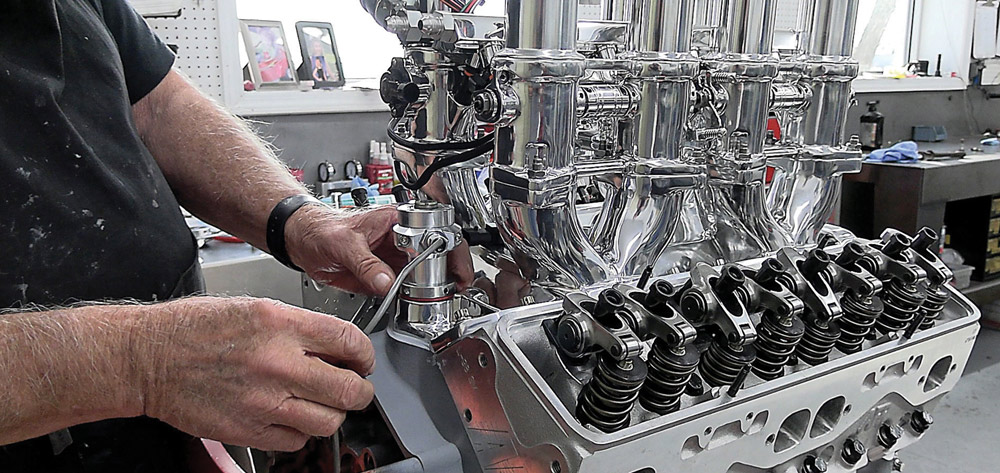
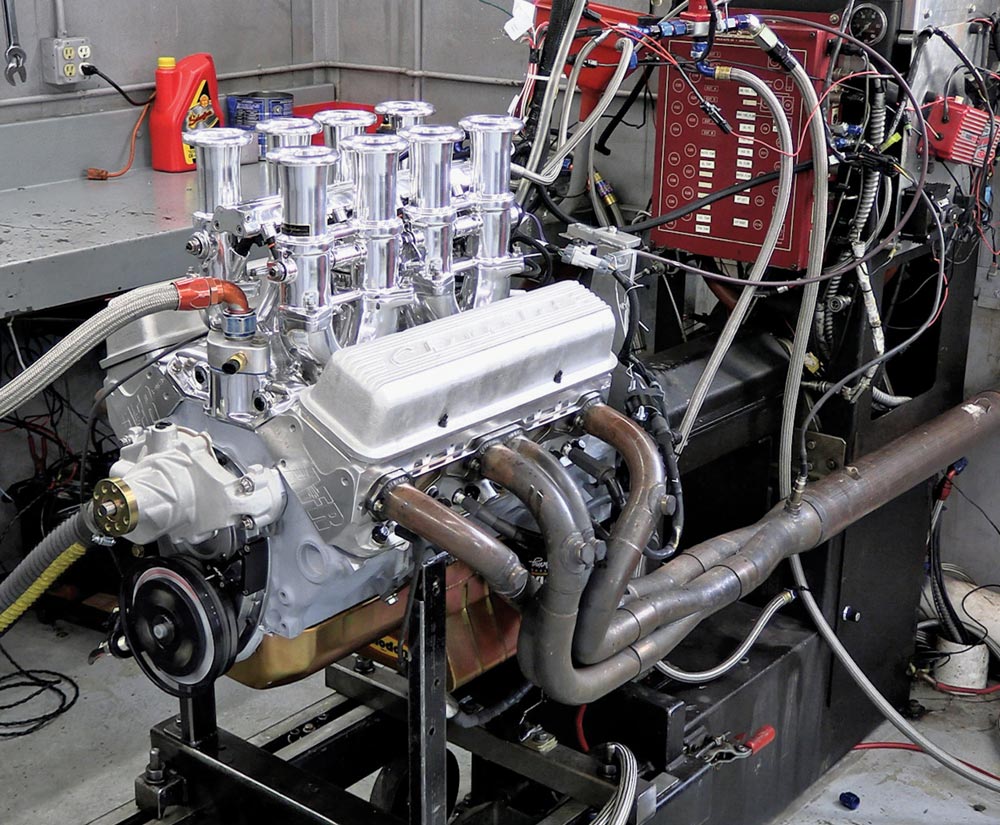
